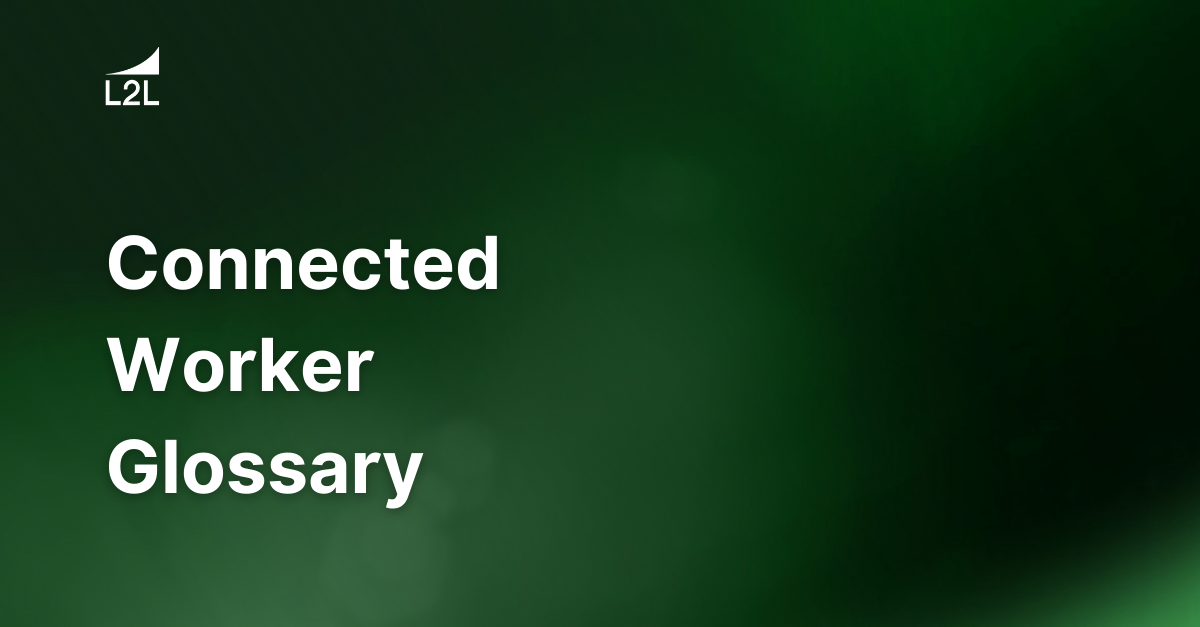
New to the concept of connected workers? Here's a list of important terms and definitions related to connected work and smart manufacturing.
A
-
Application Programming Interface (API): An application programming interface (API) is a set of rules and protocols that allows different software applications to communicate and interact with each other, enabling them to exchange data and functionality seamlessly.
-
Artificial Intelligence (AI): Artificial Intelligence (AI) is a field of computer science that focuses on the development of systems and algorithms capable of performing tasks that typically rely on human intelligence. These tasks include problem-solving, synthesizing information, understanding natural language, and recognizing patterns. Predictive maintenance is an example of AI’s application in manufacturing.
-
Augmented Reality (AR): Augmented reality (AR) refers to the real-time integration of digital information with a physical environment. AR devices like smart glasses can be used to enhance shop floor training experiences by overlaying computerized guidance over real-world scenarios.
-
Automation: Automation refers to the use of machinery, technology, and computer-controlled systems to perform tasks, processes, and operations to perform repetitive tasks and coordinate production. The primary goals of automation in manufacturing are to improve efficiency, increase productivity, reduce errors, enhance product quality, and lower production costs.
B
-
Bill of Materials (BOM): A manufacturing Bill of Materials (BOM) is a comprehensive list specifying all components and materials required to produce a finished product, providing essential guidance for production processes.
C
-
Centerlining: Centerlining refers to the process of optimizing and stabilizing production by identifying and maintaining the ideal or "centered" operating conditions for machinery and processes. This involves setting and monitoring key parameters to ensure consistent quality and efficiency.
-
Changeover: A changeover is the process of switching from producing one product to another. It involves adjusting machinery, tools, and processes to accommodate the new product, which may include changing settings, materials, and configurations.
-
Computerized Maintenance Management System (CMMS): A Computerized Maintenance Management System (CMMS) is software that helps manufacturers manage and streamline all maintenance activities. This software tracks maintenance tasks, schedules, and equipment history to improve maintenance efficiency and reduce downtime.
-
Connected Worker: A connected worker is an employee who uses digital tools, such as mobile devices and wearable technology, to access real-time information, collaborate, and enhance productivity while working on the shop floor. This connectivity improves communication and enables better decision-making.
-
Connected Worker Platform: A connected worker platform is a digital solution that enhances human workers' efficiency and productivity by integrating them into their work environment through technologies like data analytics, AI, AR/VR, IoT devices, cloud computing, and similar tools.
-
Continuous Improvement (Kaizen): Derived from the Japanese word kaizen, continuous improvement is a term used in lean manufacturing to describe an ongoing effort to enhance processes, products, and operations. This systematic approach involves identifying inefficiencies, reducing waste, and making incremental changes to optimize quality, efficiency, and overall performance.
D
-
Digital Factory: A digital factory is a manufacturing facility where advanced digital technologies such as IoT, automation, AI, and data analytics are extensively employed to streamline and optimize production processes. These technologies offer benefits such as increased efficiency, reduced downtime, and improved product quality, ultimately enhancing competitiveness in the market.
-
Digital Lean: Digital lean is an approach to lean manufacturing that uses Industry 4.0 principles and digital tools for precise, real-time operational insights. It enhances lean principles, amplifies core tools like kanban, and unlocks advanced analytics, driven by abundant high-frequency data and increased processing power, revolutionizing manufacturing efficiency and decision-making.
-
Digitalization: Digitalization refers to the process of converting analog information, processes, and systems into digital formats. It involves using digital technologies to streamline operations, enhance data accessibility, and leverage data-driven insights, ultimately increasing efficiency, productivity, and innovation in various domains such as business, manufacturing, and communication.
-
Digital Performance Excellence: Digital Performance Excellence (DPX) is an integrated approach that combines traditional management systems with intelligent risk management to enhance operational agility, flexibility, and resiliency. It helps manufacturers navigate risks across the value chain, providing a comprehensive view for proactive decision-making to improve and secure service operations.
-
Digital Maturity: Digital maturity is the measure of an organization’s readiness, capability, and effectiveness in adopting and using digital technologies and strategies to achieve its goals. Digitally mature companies tend to be more resilient, adaptable, and productive.
-
Digital Standard Work: Digital standard work is an approach that uses digital technologies to standardize work processes on the shop floor. It involves creating digital work instructions, checklists, and visual aids accessible to shop floor workers through computers, tablets, or other devices.
-
Digital Transformation: Digital transformation refers to the long-term process of using data and digital technology to improve how organizations operate and deliver value. It involves adopting digital tools, processes, and a digital-first mindset to enhance efficiency, productivity, and quality while staying competitive in a rapidly evolving digital landscape.
-
Digital Twin: A digital twin is a virtual replica or simulation of a physical product, process, or system that represents the behavior and characteristics of their real-world counterparts. Manufacturers use digital twins for analysis, optimization, and monitoring, allowing for better decision-making, performance improvement, and predictive maintenance.
-
Digital Transformation: Discrete manufacturing refers to the production of individual finished products. Unlike process manufacturing, discrete manufacturing involves taking materials, assemblies, and components through multiple production steps that result in distinct and quantifiable parts. Automobiles, windows, canned food, and cardboard boxes are examples of discrete manufacturing products.
E
-
Enterprise Asset Management (EAM): Enterprise Asset Management (EAM) is a solution that uses software, services, and systems to keep an organization’s assets running at peak performance throughout their lifecycle. Manufacturers use EAM systems to monitor asset performance and manage the quality and reliability of their machines and equipment.
-
Enterprise Resource Planning (ERP): Enterprise Resource Planning (ERP) is a software system that integrates an organization’s business processes and functions. It centralizes and automates tasks, streamlines operations, and improves efficiency, resource management, and decision-making.
F
-
Future of Industrial Work (FoIW): The Future of Industrial Work (FoIW) is a comprehensive, forward-thinking, and lifecycle-based approach to building a future-proof frontline workforce. FoIW initiatives focus on improving worker retention by deploying human-centric technologies to improve the industrial work environment.
I
-
Industrial Internet of Things (IIoT): Simply put, the Industrial Internet of Things (IIoT) is the Internet of Things (IoT) functioning in an industrial setting. IIoT involves a network of interconnected industrial devices, equipment, and sensors collecting and exchanging data within a manufacturing facility.
-
Industry 4.0: Also known as the Fourth Industrial Revolution, Industry 4.0 refers to the stage of technological evolution that represents the integration of digital technologies like IoT, AI, cloud computing, and automation into industrial processes. It aims to create smart, interconnected, and highly efficient factories and supply chains.
-
Just-in-Time (JIT) Manufacturing: Just-in-Time (JIT) manufacturing is a production strategy focused on producing items precisely when they're needed, avoiding excess or premature production. This approach is embraced by organizations to enhance efficiency, cut expenses, and accelerate product delivery to customers.
L
-
Lean Manufacturing: Lean manufacturing is a production philosophy that aims to optimize productivity by minimizing wasteful activities in manufacturing operations. Waste, in this context, is defined as any activity that doesn't contribute value that customers are willing to pay for. This approach leads to advantages such as shorter lead times, lower operating costs, and enhanced product quality.
M
-
Machine Monitoring: Machine monitoring refers to the process of using advanced technologies to collect data about mechanical performance, status, and utilization in real time. This helps manufacturers optimize production efficiency, prevent downtime, and enhance overall equipment effectiveness through data-driven insights and automatic alerts.
-
Machine Status: Machine status gives a current picture of a machine’s condition, availability, and operational state. It indicates whether the machine is running, idle, undergoing maintenance, or experiencing any issues.
-
Manufacturing Work Instructions: Manufacturing work instructions are detailed guidelines or procedures that enable teams to efficiently assemble, package, label, and ship products that meet specified standards. Whether in mass production or product transitions, creating easy-to-understand work instructions is critical for success.
-
Manufacturing Execution System (MES): A Manufacturing Execution System (MES) is a computerized system designed to track and document the process of turning materials into finished products. An MES solution offers manufacturers product traceability, recipe management, machine process control, and more.
O
-
Overall Equipment Effectiveness (OEE): Overall equipment effectiveness (OEE) is a key performance metric in manufacturing that measures the efficiency and productivity of a production process or piece of equipment. It quantifies the percentage of time that equipment is operating effectively, taking into account factors like downtime, speed loss, and quality defects.
-
Operational Excellence: Operational excellence is a workplace philosophy that focuses on continuously improving operations and processes to achieve the highest levels of efficiency, quality, and customer satisfaction. It involves optimizing production, reducing waste, enhancing resource utilization, and fostering a culture of continuous improvement and innovation throughout the organization.
-
Operator: An operator in a manufacturing facility is an employee responsible for operating machinery, equipment, and tools as part of the production process. Their primary role is to ensure the smooth and efficient operation of these assets, follow established procedures, monitor quality, and perform basic maintenance tasks.
P
-
Poka-Yoke: Poka-yoke is a Japanese term used to refer to error-proofing or mistake-proofing manufacturing techniques. Poka-yoke methods can include the use of specialized tools, visual cues, or automation to detect errors or defects throughout the manufacturing process.
-
Predictive Maintenance: Predictive maintenance is a type of condition-based monitoring that proactively anticipates maintenance requirements, mitigating unplanned downtime expenses. It involves configuring machines and equipment with monitoring devices and analyzing their data to detect possible issues or failures before they occur.
-
Preventive Maintenance: Preventive maintenance is a strategy that involves systematic actions to ensure a machine operates smoothly without setbacks or breakdowns that could lead to significant production failures in the future. These actions are executed within a time-based model or a condition-based model.
-
Proactive Maintenance: Proactive maintenance is a strategy for preventing mechanical failures and minimizing unplanned downtime through planned, preemptive actions. It involves systematically identifying and addressing potential issues before they lead to breakdowns with the goal of increasing overall operational efficiency and reducing maintenance costs.
Q
-
Quality Management System (QMS): A Quality Management System (QMS) is a collection of business processes and procedures aimed at boosting productivity, efficiency, and customer satisfaction. A QMS helps an organization achieve its goals for quality by ensuring regulatory compliance and adherence to efficient practices.
R
-
Rework: Rework entails the process of repairing and reprocessing materials, components, or subpar products to transform them into items that align with the required quality standards and specifications. In plastics manufacturing, rework is often referred to as “regrind.”
-
Return on Investment (ROI): Return on investment (ROI) is a financial metric used to evaluate the overall profitability of a business endeavor. The typical formula used to calculate ROI is:
ROI (%) = [(Net Gain or Profit from Investment) / (Initial Investment Cost)] x 100
S
-
Scrap: Scrap refers to defective or unusable materials, components, or products that do not meet a manufacturer’s quality standards and must be discarded or recycled. It represents wasted resources and can impact production efficiency and profitability if not minimized and managed effectively.
-
Smart Factory: A smart factory is a manufacturing facility that uses advanced digital technology and digital-first strategies to enhance efficiency, productivity, safety, and agility. Smart factories accomplish this by integrating intelligent technologies like AI, cloud computing, IIoT, and AR/VR into traditional manufacturing processes.
-
Smart Manufacturing: Smart manufacturing is an approach that leverages advanced technologies such as data analytics, IIoT, automation, and cloud computing to enhance the efficiency of core manufacturing processes. A smart factory is an embodiment of this concept. Unlike traditional manufacturing, smart manufacturing embraces more flexible, data-driven, and automated systems.
-
Standard Operating Procedure (SOP): A Standard Operating Procedure (SOP) in manufacturing is a detailed, written set of instructions that outlines step-by-step processes for tasks, production, or equipment operation. SOPs ensure consistency, quality, and safety by guiding workers on how to perform specific tasks or jobs in a standardized and efficient manner.
T
-
Technician: A technician is a skilled worker responsible for operating and maintaining machinery, equipment, and production systems. They perform tasks such as equipment setup, troubleshooting, routine maintenance, and quality control checks to ensure smooth production processes and product quality.
-
Throughput: Throughput refers to the rate at which a production system or facility can manufacture products within a specific time frame. It measures the volume of goods produced or processed, which indicates the system's efficiency and capacity to meet production demands.
-
Total Productive Maintenance (TPM): Total Productive Maintenance (TPM) is a manufacturing strategy focused on improving the reliability and efficiency of every piece of machinery and equipment involved in production. This holistic approach to improving plant performance involves every level of the manufacturing organization.
V
-
Virtual Reality (VR): Virtual reality (VR) is a technology that creates immersive, computer-generated environments or simulations, typically experienced through a headset or smart glasses. It can be used to simulate production processes, train workers in a safe virtual environment, visualize complex products, and aid in prototyping.
W
-
Waste: Waste refers to any resource, material, time, or effort that is not effectively utilized in the production process. It includes activities, defects, excess inventory, waiting times, and other inefficiencies that reduce productivity and increase costs without adding value to the final product.
Y
-
Yokoten: Yokoten is a Japanese term that means “sharing sideways,” or dispersing knowledge across an organization. This methodology helps manufacturers communicate best practices and democratize important information throughout their facilities.
Revisions
Original version: 16 October 2023
Written by: Evelyn DuJack
Reviewed by: Daan Assen
Please read our editorial process for more information
Related Posts
Subscribe to Our Blog
We won't spam you, we promise. Only informative stuff about manufacturing, that's all.