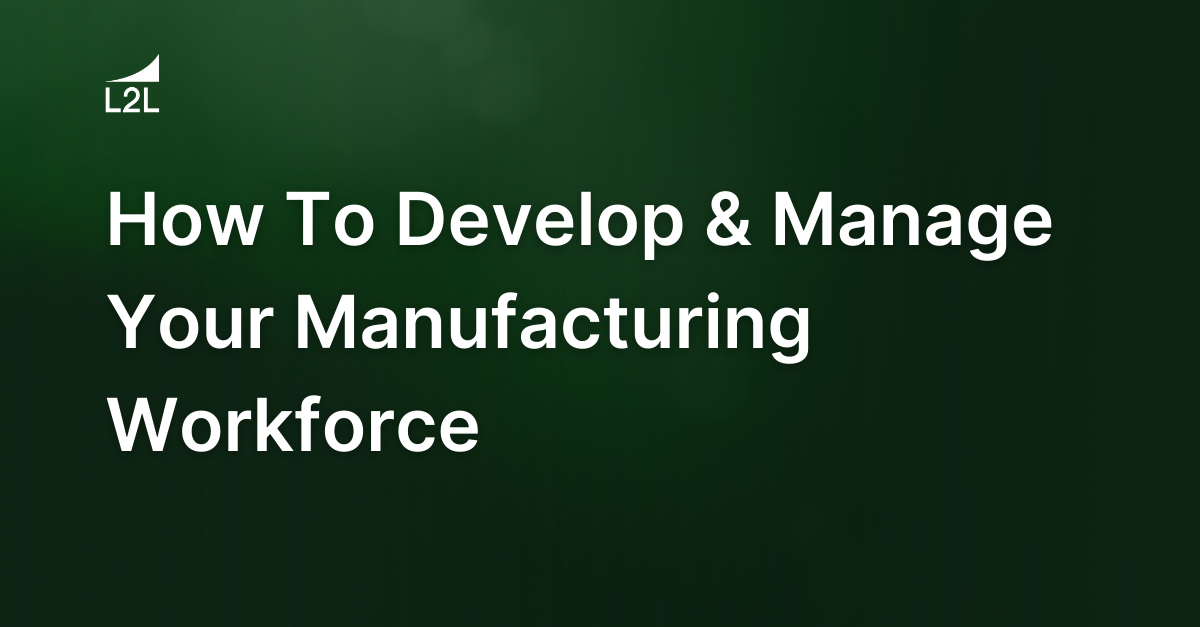
Manufacturing is facing a talent emergency that's only getting bigger. By 2033, our industry will need 3.8 million workers—but half of those positions risk sitting empty because manufacturers can't find people with the right skills.
The pace of change isn't helping. According to a recent EY survey, 65% of manufacturing leaders see skills requirements evolving faster than their workforce can adapt. And what makes this challenge even more pressing is the fact that 87.2% of manufacturers expect to increase their use of technology in the coming years.
With the median age of manufacturing workers sitting around 44, there’s also a race against time to transfer knowledge from experienced workers to the next generation.
What’s the solution? Make workforce development a core part of your business strategy. When you do, you'll develop the skills your operation needs to stay competitive—faster and more effectively than ever before.
In this article, we’ll dive deeper into the role of workforce management and introduce the framework for building a future-ready manufacturing workforce.
The role of workforce management in manufacturing
Modern manufacturing success depends on more than just having enough people on the plant floor. You need to build teams that can handle both hands-on work and complex technology and do it well.
Workforce management gives you the tools to match your workforce precisely to your production needs through accurate demand forecasting. This will help you boost productivity, cut operational costs, increase employee satisfaction, and create an operation that adapts quickly to changing market demands.
With automation, IoT, and AI reshaping the factory floor, the skills your team needed yesterday aren't the same ones they'll need tomorrow. Insights from one Deloitte and The Manufacturing Institute study show what you need to give attention to:
-
Manufacturing roles increasingly require cybersecurity and network security competencies, as production systems become more connected and digitally vulnerable.
-
Knowledge about cross-functional systems integrations has become essential, as Industry 4.0 breaks down traditional silos between production, maintenance, and quality control.
-
As AI and ML become integral to manufacturing processes, workers must develop critical evaluation skills to assess AI outputs and maintain quality control.
Manufacturers can't afford to sit back and watch these changes unfold—it’s time to take action. You need to invest in continuous training and use data to spot skills gaps before they become problems. To succeed, you’ll want to build flexible teams through cross-training while measuring success in ways that go beyond basic productivity metrics.
Manufacturing workforce management framework
Effective workforce management involves four critical areas:
-
Workforce planning to maintain optimal staffing levels
-
Recruitment strategies to build reliable talent pipelines
-
Development and training programs to build critical skills
-
Engagement initiatives to retain your valuable team members
Let’s discuss each in more detail.
1) Workforce planning
Workforce planning is all about having the right people, with the right skills, at exactly the right time. Too few workers? Your production line slows down. Too many? You're wasting money and resources. And if you're missing critical skills, both your product quality and equipment effectiveness take a hit.
Getting workforce planning right delivers immediate benefits across your operation, from lower expenses and downtimes to simply having an easier time managing production processes.
To get your staffing levels just right, try these strategies:
-
Analyze workforce data: Track past production levels, employee performance, and other internal KPIs to spot patterns that reveal exactly how many workers you need. This lets you match your headcount to production targets without burning out your team or racking up excessive overtime costs.
-
Manage seasonal or cyclical demand fluctuations: Use flexible staffing arrangements like part-time workers and rotating shifts to quickly scale your workforce up or down. Cross-train your employees in multiple roles so you can easily shift them where they're needed most during peak times or slowdowns.
-
Implement contingent labor strategies: Stay ahead of peak seasons by bringing in temporary workers early and training them before the rush hits. Partner with staffing agencies that understand both your technical needs and company culture—they can pre-screen candidates and train them on your procedures before they step onto your floor.
These strategies will hopefully give you some of the control and flexibility you need to maintain optimal staffing levels throughout the year.
2) Workforce recruitment and hiring
When you make a bad hire, you're not only wasting time and training resources—you're risking quality issues, equipment damage, and even safety incidents that can shut down entire production lines.
Today's manufacturing talent needs to handle both physical operations and digital systems. Workers need to be tech-savvy to work with automated systems, skilled to maintain quality standards, and adaptable to learn new processes quickly.
Finding such manufacturing talent isn't getting any easier. Still, here are some ideas for building reliable talent pipelines:
-
Build partnerships with vocational schools and universities: Create real partnerships with technical schools and universities—shape curriculum, provide modern equipment for training, and help students get hands-on experience in your facilities. The best part? Deloitte suggests that 73% of manufacturers are already doing so
-
Leverage apprenticeships and internships: Combine hands-on training with classroom learning and allow interns to earn while they learn. If possible, expose apprentices to both traditional skills and new technology like robotics and digital systems.
-
Attract a younger workforce: Many young job seekers have outdated views of manufacturing as dull or labor-intensive. Highlight advanced technologies, innovative practices, career growth opportunities, and employee stories in your recruitment materials.
-
Use employee referral programs: Your best technical workers know other skilled people. Offer rewards for referrals who stay and perform well, use quick application processes, keep referring employees updated, and offer bigger bonuses for those hard-to-fill technical roles.
-
Become an employer of choice: JELD-WEN's plant in Louisiana shows how digital transformation can be a game-changer for recruitment. After implementing modern systems like iPads, digital scoreboards, and real-time monitoring, the company went from struggling to fill positions to maintaining a waiting list of qualified maintenance workers. Despite its rural location, JELD-WEN's advanced technology has become a key selling point for attracting skilled talent.
These recruitment strategies can help you build a reliable pipeline of skilled workers. However, the key is to start implementing them before you desperately need to fill positions.
3) Manufacturing workforce development and training
As processes and machines become more complex, effective training programs are essential for equipping employees with the necessary skills and knowledge.
Today's operators need to manage complex systems, read data displays, troubleshoot modern equipment, and make smart decisions on the fly. You need a training program that both upskills and reskills workers as traditional roles become automated.
Here’s how to develop your manufacturing workforce efficiently:
-
Conduct a skills gap analysis to assess current workforce capabilities: Document each worker's current capabilities, then compare these against your immediate operational needs and future tech requirements.
-
Create personalized training and career development plans: Design individual plans that match each worker's abilities and career goals with your facility's needs. Mix technical training, leadership development, and cross-functional exposure based on their potential.
-
Use blended learning strategies: Combine hands-on machine time, digital learning tools, and structured mentorship to accelerate skill development. Employ e-learning for theory, supervised equipment time for practical skills, and experienced operator shadowing for more nuanced knowledge transfer.
-
Cross-train to increase workforce flexibility: Build flexibility into your workforce by training operators across multiple equipment types or production areas. Start with your critical backup needs, then systematically rotate workers through different roles under experienced operators.
-
Use simulation and augmented reality (AR) for training: Let workers practice complex or dangerous operations safely using simulation and augmented reality tools. These technologies provide risk-free training environments and can overlay guidance during actual task performance. Perfect for new equipment training or complex procedures where mistakes could be costly.
-
Leverage software to track employee training: Track everything in one place. Modern connected worker and LMS platforms can help manage training schedules, deliver digital content, track certifications, and monitor progress.
These workforce development strategies help you build the skills your team needs today while preparing them for tomorrow's challenges.
4) Workforce engagement and retention
When a skilled operator walks out your door, they take more than their technical skills with them. You lose years of process knowledge, equipment expertise, and mentoring capability that can't be replaced overnight. As the fifth greatest workforce challenge in the manufacturing sector, companies know this all too well.
Keeping your best talent isn't only about fancy perks or huge paychecks. Create an environment where skilled workers see real value in their work and invest in their development.
Strategies to consider:
-
Offer clear career pathways and opportunities for advancement: Create clear skill-based progression paths that show exactly what workers need to master to move up. Whether it's promotions, lateral moves to different departments, or skill development opportunities, make the path crystal clear.
-
Employee recognition and reward programs: Build a program that rewards real contributions to quality, safety, and operational excellence. Besides usual performance bonuses, employee of the month awards, and milestone celebrations, offer personalized rewards like gift cards or extra time off—and allow employees to choose which reward they want.
-
Cultivate a positive company culture and work-life balance: High standards don't mean high stress. Find ways to offer flexibility through shift preferences or compressed schedules. Make break areas comfortable, provide the right tools for the job, and build team spirit without disrupting operations.
-
Role of leadership in fostering engagement: Your best engagement tools are leaders who actually lead. Get your management team out of their offices and onto the production floor. Have them ask for input, clear obstacles, and show workers how their daily work drives company success.
-
Encourage transparency and open communication between management and employees: Skip the corporate speak. Hold regular shift meetings that actually matter. Share performance metrics where everyone can see them. Create clear channels for workers to raise concerns and suggest improvements. And when workers speak up, take action. Nothing kills engagement faster than ideas that disappear into a black hole.
With the high turnover rate, manufacturing leaders need to prioritize employee engagement. ScreenCloud’s research discovered that it has additional benefits—besides retention, high employee engagement increases workplace safety and productivity.
Image source: ScreenCloud
Empower your workforce with L2L
Streamline your workforce management with L2L's connected workforce platform. Our digital solutions put critical workforce data and tools at your fingertips, helping you build, train, and retain high-performing teams.
Manufacturing teams can use L2L's workforce capabilities to:
-
Accelerate onboarding with standardized training programs and digital certification tracking that gets new hires productive faster.
-
Enhance performance through step-by-step digital work instructions that help every worker perform like a veteran.
-
Improve knowledge retention by making critical information instantly accessible when and where workers need it.
-
Standardize operations with digital standard work that ensures consistency and makes updating procedures simple.
-
Optimize workforce planning using real-time skills tracking and certification management to deploy the right people to the right tasks.
Request a personalized demo today and discover why manufacturers trust L2L to drive workforce excellence.
Revisions
Original version: 7 November 2024
Written by: Evelyn DuJack
Reviewed by: Daan Assen
Please read our editorial process for more information
Related Posts
Subscribe to Our Blog
We won't spam you, we promise. Only informative stuff about manufacturing, that's all.