
L2L
What Is a Lean Manufacturing System and How Does the Tech Work?
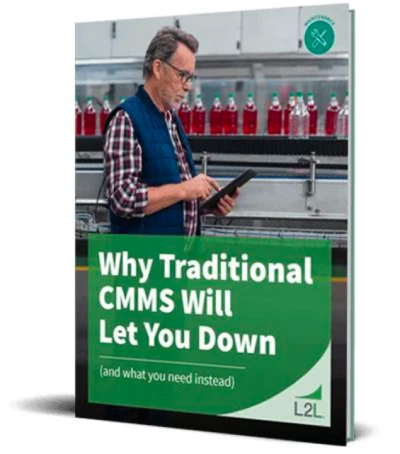
Ready to Get Started? Request a Free Consultation.
Most people involved in the manufacturing and production industries are at least somewhat familiar with the term lean manufacturing. Most of those people would agree that lean manufacturing is almost universally acknowledged as being born and raised in Japan. However, this is not entirely accurate.
“What is lean manufacturing?” is like a child asking why the sky is blue, over and over, followed closely by a series of, “But whys?”
When you are truly interested in a subject, you want to have a fuller and more complete understanding of all aspects of that subject. When you are passionate about it, your desire to keep learning never ends. In this case, the subject about which we’re passionate is lean manufacturing systems. We are going to go well beyond catchphrases and taglines throughout our exploration. There is no one absolute definition, no absolute singular approach, and no one absolute goal.
The only absolute about lean manufacturing is this: Accept that lean is a continuous process. Rome wasn’t built in a day and your factory won’t be transformed in a day. Your actions will return results, and hopefully some immediate changes and improvements are realized. Which is great! That’s just what you and your teams need to see happen to continue to fuel that fire. This is also the reason you take incremental steps as you start your lean journey.
Moving to lean manufacturing means openness to change and new ideas. It’s no secret that most people are change averse, if not change avoidant altogether. Laying out the big picture before the changes start is essential to ensure buy-in from every discipline in your organization. There can be no secrets or hidden agendas. Complete transparency and clear, effective communication must be incorporated as part of the process from the very beginning.
Lean Manufacturing Is About Eliminating Waste
So, beyond those basics, what is lean manufacturing? Far more than a series of buzzwords. When put into practice, lean manufacturing is a systematic approach to performing work with several primary points of focus. Two of the key principles of Lean Manufacturing are:
-
The identification of waste
-
The elimination of waste (called muda in Japanese). Elimination of waste (muda) can never be pursued or achieved at the sacrifice of productivity or quality.
So, why LEAN? It’s not an acronym for anything. It’s an easy enough word, but that’s not the reason people gravitated toward that particular word. Lean has been around in some form and to varying degrees for centuries.
Whether you have just recently been introduced to Lean, or you’ve been involved with it for years, you know the fundamental principle is the elimination of waste. Eliminating waste and streamlining processes are done to save time, money, space, and materials. Lean means those very things. When you eliminate waste and conserve precious resources, you literally lean things out.
Lean Manufacturing Is About Common Sense
Lean is a concept, a way of thinking and acting, and a collection of philosophies. It’s the kind of common sense you can’t always recognize or even perceive until someone flicks on that lightbulb. Like standing so close to your favorite tree that you can’t make out the forest all around you.
But lean is so much more than good ideas. It is behaviorism at its best. It is both the goal and the journey. The focus is the elimination of waste, in all its many forms and manifestations. Streamlining processes is but one component of a lean manufacturing system, but what an essential component it is. It’s like saying, “I love this 18-wheeler, and this here’s my favorite tire. The only one I really need.” Well, not so much. That truck might run, but you’re going to feel the effects down the road.
There are a number of theories about when and by whom the concepts of lean manufacturing were first conceived and put into practice. History tells us that the earliest iterations of lean began in the 1450s in Venice. By incorporating sequencing and standardizing processes, shipbuilders at the Venetian Arsenal were able to move ships through their entire production line in an hour! Think of that. Nearly 600 years ago, those shipbuilders could fabricate a ship from stem to stern in one hour! How could they have done that without computers and the technology we largely take for granted today? By standardizing their processes and the flow of their product, the shipbuilders discovered that they could maximize efficiency, quality, and safety. Three very important elements of any successful undertaking.
Although those Venetian shipbuilders are the first known users of standardized production processes, historians also cite the innovations and accomplishments of ancient civilizations like the Greeks, Aztecs, and Egyptians. The roots of lean may be deeper and more widespread than we will ever know.
Eli Whitney
Fast forward a bit to 1779. Eli Whitney, best known for inventing the cotton gin, is credited with inventing the concept of interchangeable parts. Well, inventing is generous and not entirely accurate. Let’s say he ‘borrowed’ the concept from a French arms maker in order to secure a government contract to build 10,000 muskets for the United States Army.
Ironically, he was awarded the contract as the U.S. prepared to go to war with France. C’est la vie, such is life. In fairness to Whiney, he revolutionized the way cotton was processed by greatly speeding up the separation and removal of seeds from cotton. This contribution to the economic well-being of the United States cannot be overstated. Utilizing the practice of interchangeable parts, we also have Whitney to thank for introducing and perfecting JIT - Just in Time Manufacturing, still a vital component of lean manufacturing today.
Frederick Taylor
Early in the 1890s, the father of scientific management, Frederick Taylor, closely investigated not only work methods but also the workers themselves, on the factory floor. After his studies, he propounded concepts like standardization of work, time studies, and motion studies, in order to achieve the greatest efficiency in the work methods, processes, and operations. However, he ignored the behavioral aspects of the work, workers, and work environment, which invited many criticisms against him.
To this day, management is guilty of perpetuating the Under-ism mentality. Under-ism is an umbrella term for all thinking and behavior that does not elevate, inspire, and motivate. Here are some of the most frequently seen examples. And no, sadly this is not limited to manufacturing but is prevalent in nearly every conceivable business without exception:
Under-isms: Always showing at a place of work near you.
-
Under appreciating attributes and qualities of their workforce.
-
Operating under the assumption that all shop floor associates check their brains at the door when they enter the building.
-
Underestimating the potential to want to learn and do more.
-
Assuming that employees, both blue and white collar, care only about exchanging their labor for a paycheck.
-
Undervaluing loyalty, intelligence, and integrity.
-
Setting the bar so low, it would be hard to disappoint. So their exceedingly low expectations are always met.
Enough of the negative. Notice that I cited "management" as the guilty party here. This is not to say that employees are without blame. It takes two to tango, and at least that many to keep the gears moving smoothly. Leaders do not perpetuate these behaviors. I guess that’s why we refer to Frederick Taylor as the Father of scientific management. He was clearly no one’s "Work Dad."
Henry Ford
No discussion about lean manufacturing would be complete without including Henry Ford. While Ford did not invent the automobile, he revolutionized the way they were manufactured. Ford is often given credit for conceiving the assembly line, and rightly so. Ford’s real genius and most significant contribution to lean manufacturing was transforming the flow of production. You could not have described any processes of manufacturing as flowing prior to Henry Ford. His gift to all future manufacturing generations was interchangeable parts and what we now think of as standardized work. He then introduced conveyance to the mix, and mass production was born.
Taiichi Ohno
It’s interesting to note that many of the well-known Japanese names we credit with advancing Lean Manufacturing (Eiji Toyoda, Taiichi Ohno, Kiichiro Toyoda), actually began their lean journeys by studying American manufacturing. Including visiting Ford plants in Michigan after the Second World War to learn about the production processes Ford instituted. They were also especially interested in the statistical quality control practices pioneered by William Edwards Deming, which were almost completely disregarded by American industry.
Taiichi Ohno is considered to be the father of the Toyota Production System. He combined and integrated "Just in Time’"Manufacturing, Kaizen (Continuous Improvement), Poka-yoke (Mistake Proofing), Eliminating Waste (seven distinct types of waste), and Kanban (level loading production volume).
Waste encompasses far more than scrap product alone. In lean production, waste can be found in at least these seven ways:
-
Inventory: Excess inventory that’s held in case of drastic increase in demand, quality issues, or inability to run production lines. This leads to costs in storage and often product spoilage or depreciation.
-
Waiting: If waiting is occurring at any point in the process, this is a form of waste. A machine breaks down, approval needs to be given, or material is needed in order to produce are all examples of waiting.
-
Defects: Wasted material in form of scrap, or wasted product due to quality or other defects are examples of defects. The resources needed to rework product is a form of waste resulting from defects.
-
Overproduction: Producing unnecessary product (product that a customer isn’t willing to pay for) leads to other forms of waste. Overproduction leads to transportation of those products, excess motion, waiting, and inventory, etc.
-
Over-processing: This comes in the form of doing work on products that doesn’t add value to the product. To add features or components to a product that nobody will likely pay for or use is over-processing.
-
Motion: Wasteful or inefficient movement by people or machinery. This leads to longer production times and wear and tear on your people. Making all movements minimal and efficient is the key to beating this form of waste.
-
Transportation: Unnecessary distance traveled by product or people, that is not value added to the product. There’s also a real cost to the equipment, time, and space used during transportation.
Common examples of waste are all of the following and more:
-
Unnecessary steps, whether they are part of a process or unnecessary physical steps.
-
Unnecessary movements; expending more energy, time, and resources than necessary to accomplish tasks.
-
Unused materials are waste; buying 10-foot lengths of material when what you really need are 8-foot lengths, resulting in 2 feet of unusable rem (remnant) material.
-
Asking people to perform work for which they have not received training is waste.
-
Constantly changing priorities is waste, especially if changing over between products is not efficient.
-
Paying expedited freight charges
Waste can even be asking people to perform three tasks at the same time. It's along the lines of no one being able to serve more than one master. Attempting to tackle three things simultaneously means all three things suffer and no one job gets the full attention it deserves. I could go on and on. (*Note how many of these examples of waste include ‘un’ somewhere.)
For Lean Manufacturing Production, Think Like Your Customers
Lean manufacturing is a much easier concept to grasp and embrace when we think as our customers think. Customers pay us for products and services. Period. They don’t pay us for any part of waste, whether that waste comes from the misuse of resources, time, or materials. Customers only pay for value. As manufacturers, we would be wise to follow that line of thinking. While we all seek value, we all pay for waste, whether we recognize it or not.
Lean Manufacturing and Kaizen
The intention of lean manufacturing is to continuously improve (a philosophy called kaizen in Japanese). Improve those factors that add value to products and reduce or remove (improve or eliminate) those factors that do not add value and waste precious resources.
The philosophy of improving, and continuously improving, is largely associated with the Toyota Production System, commonly referred to as TPS, and colloquially referred to as the Japanese Manufacturing System.
It is also widely believed that not all aspects of lean manufacturing came solely from the Japanese.
Dr. William Edward Deming is credited with much of the evolution of this way of thinking. W. Edward Deming, was born in Sioux City, Iowa, and educated at the University of Wyoming and later Yale University. Often called the "Father of Quality," Deming tried to share his philosophy with American manufacturers.
After receiving their, “Thanks, but no thanks,” Deming took his ideas to Japan. Deming was a highly successful business consultant and a leading pioneer in the field of quality. He was a statistician and leading management thinker whose philosophy and methods aided tremendously in Japan’s economic recovery following the Second World War and is still felt all these years later.
Back to Toyota and the Toyota Production System (TPS). Toyota has spent many years defining, implementing, and improving TPS. The steady growth of Toyota from a small regional company to the world’s largest automaker is a testament to the success of TPS. This phenomenal growth and success garnered worldwide attention for not only Toyota, but also for the vehicle through which this success was achieved (pun intended).
TPS focuses on the continuous identification, reduction, and elimination of the original Toyota seven wastes. TPS demands never being satisfied with the status quo, as there are always opportunities for improvement.
Toyota, and by extension, TPS, continues to improve and evolve. Not only is Toyota the world’s largest automaker, but it is also currently the most successful and profitable automaker in the world.
Let me share my personal introduction to lean manufacturing with you. I was a young worker happily toiling away in a big factory — the first I’d ever stepped foot into in my life.
Oh, sure, I was a bit intimidated at first. But before long, I was a lifer. A manufacturing junkie. I could not get enough. I loved it!
We worked really hard. We built a great product. We had a huge slice of the market. We had happy customers. We were happy and pleasantly plump.
Then one day, something changed. And pretty soon, everything had to change. Our business became increasingly competitive. Some other companies learned how to do what we did. Not as well, of course. But for less money. And they were pretty fast too.
“Lean manufacturing.”
I’m not going to try to kid you. It was a little scary. Lean manufacturing? Is that the same as forced reduction, like the kind of diet you don’t want to start?
It was unknown, unfamiliar, different. Where did we begin? Some of the people I worked with were really scared. Many of them had worked there for a long time and many of us thought of it as the best job we ever had or ever would have.
In hindsight, perhaps the transition was a little easier for us because we knew we had to get better and we had to do it in a hurry.
You know what happened? We did it! We learned. We got faster. We worked smarter. We got better. And no one lost their job. As we identified waste and eliminated non-value-added opportunities, some of us moved to new jobs. Some of us learned new skills. Some of us did things we didn’t think we were capable of doing previously. We weren’t scared of LEAN anymore.
Here are a few things we learned.
-
We eliminated waste, and suddenly, we found more waste.
-
As we eliminated waste, things got less frustrating; things we didn’t even realize were slowing us down and making our jobs harder.
-
Our quality improved, our production times improved, throughput improved, and we reduced costs.
-
We weren’t working seven days a week anymore. No one saw that coming.
If lean thinking teaches you anything, it teaches you that things change. Constantly. It teaches you to adapt. It teaches you to be lean manufacturing machines!
So if lean is about making things easier and more efficient then we can say lean production is about producing products more efficiently. So, how do we do this?
Well, once again it's not difficult; it's actually very easy. First, we must make problems and waste, or what we like to call "opportunities," seen by everyone. Once we can see the opportunities we then need to take action! Action is the key to lean manufacturing success and why people are so crucial to any lean manufacturing system. Once we take action we need to ensure that we sustain our improvements.
Lean Manufacturing Tools
Generally, lean tools are anything that can help us to see problems, take action, and sustain improvement. We call this Continuous Improvement. Continuous Improvement is a way of life and a culture of doing business. It's something that never ends because there will always be opportunities to improve.
If you look at the world today there are many examples of lean manufacturing tools that we use every day. Take, for example, road maps. Road maps used to be on paper, and to arrive at a location we'd never been before we had to map out our path before leaving, which took time.
Once we started our journey we had to pull over to make sure we were still on the right path or have somebody in the passenger seat to navigate.
It's now much easier with digital navigation systems. If you don't have one in your car, you've got one on your phone. It's totally changed the way we navigate today.
It's now very easy to navigate directly to a destination that before may have taken much longer (assuming we didn't get lost in the process).
What are some examples of lean manufacturing tools?
There are traditional lean principles and tools such as these 12 lean manufacturing tools :
-
Andon: A real-time system or process to visually notify of issues occurring on the plant floor so they can be resolved.
-
Heijunka (Level scheduling): Production scheduling based on similar processes
-
Jidoka: Automation of certain processes for efficiency, and to facilitate stop and fix activities when quality issues occur.
-
Just-In-Time (JIT): To pull parts or materials through production lines dependent on customer demand, not primarily based on projected demand.
-
Kaizen: Enabling the workforce to voice and act on ideas for operational improvement. When done consistently, this drives continuous improvement.
-
Kanban: A method of signaling when more goods, materials, or products are needed at a certain point in the production process.
-
Muda (Waste): The focus of lean manufacturing is waste reduction in all its forms.
-
Poka-Yoke: A method of error-proofing the production process through the detection and prevention of the causes of defects.
-
Root Cause Analysis: A process of digging down layer by layer into a problem until the root cause is found. Once the root cause is found, the underlying issue can be resolved. One common method is "Five Whys" (Asking “why” five times until you get to the root of the issue).
-
Standardized Work: Documenting a best practice and making it the standard method of performing a task or process.
-
Takt Time: Refers to the pace of production being aligned with demand for the product from customers.
-
5S: Is focused on organizing a work area for efficiency. It involves 1) Sort, 2) Set in order, 3) Shine, 4) Standardize, and 5) Sustain.
We’ve explored some of these already, and there are others, but if learning and implementing these tools feels a bit overwhelming, then you’re not alone. Let’s simplify things. The following are four benefits needed for lean success, which are achieved through lean manufacturing systems:
Visibility (Problems are SEEN)
As we said earlier we need to make problems or opportunities visible. The challenge is making sure they're seen.
We see a lot of manual examples that fall short for this reason. Because they're not real-time, and they're difficult to keep updated, you get an inaccurate view of yesterday's news. Thanks to the evolution of new technologies (i.e., lean manufacturing tools), making opportunities for improvement visible has never been easier. We can now notify and escalate problems to the right people at the right time. This helps ensure the issues are not only visible but are seen and action is taken.
Action
This brings us to our next point. Once problems are seen, we need tools to track and monitor activity. This can't be emphasized enough. If all you have is a system that flags or notifies you that there is a problem, but there is no tool to track the response, the corrective action, and the follow-up, then it's probably not going to give you the results you're looking for.
Once again thanks to technological advances, especially in cloud computing, we can quickly disperse information and track the actions taken.
Take for example the recent coronavirus outbreak. There's a website that uses a cloud-based method to track and show in detail how the virus is spreading in real time. Tools like this will help escalate action and minimize the problem.
Imagine if this was all done manually on paper. It couldn't be done! That's where lean manufacturing tools come in handy.
Problem-Solving
In our manufacturing facilities, we also need a lean manufacturing system to help track and drive problem-solving. This is critical because we don't want to just correct the problem this time, we need to make sure it never happens again in the future, whenever possible. Excel spreadsheets are a commonly used tool for this but the problem is that it's difficult to track and share solutions. Cloud-based solutions provide a quick and easy way to not only track your problem-solving but to also quickly share the solution with other sites all over the world.
Sustainability
Finally, we need tools that help us sustain not only our corrective actions but more importantly our culture of continuous improvement. This is the most difficult part of lean manufacturing and where most companies fail.
The solution however is quite simple and goes back to the beginning of this section. By making lean seem complex and difficult to understand, many companies end up surrounding their lean manufacturing system with complex tools that are hard to use and difficult to maintain.
It's also important to note that lean manufacturing tools must serve the people on the shop floor (make their jobs easier), not the reverse where people are serving the tool (cumbersome task). For these reasons, many lean manufacturing systems struggle to sustain themselves over the long term.
The Future of Lean Manufacturing Is Here
We live in a time where lean manufacturing doesn't need to be overly complex and confusing (only understood by a select few). Today, we have technology and tools that can help facilitate a common sense lean manufacturing system that everyone understands and can contribute to.
While the lean principles of the past are still very much relevant, the methods of the past need to stay in the past, just like paper maps for navigation. They served their purpose but it's a new day, a new time, and a different way of doing things. Lean manufacturing should be easy and fun!
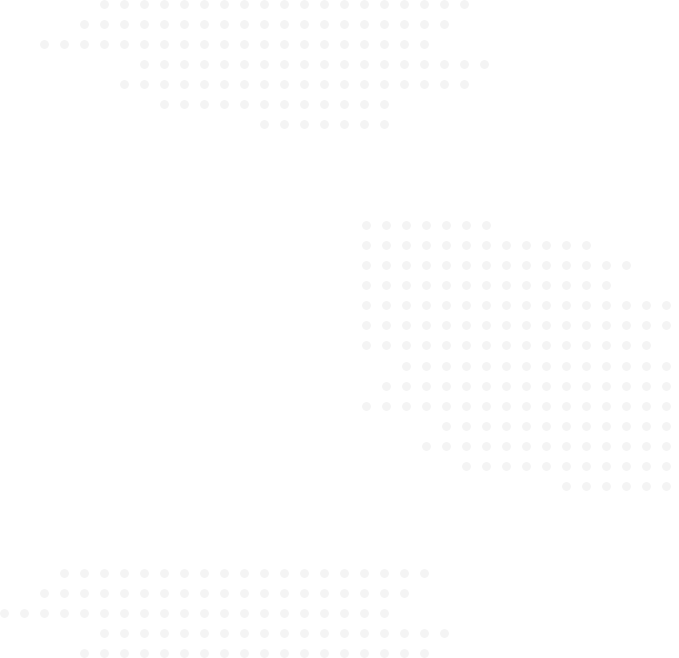
Explore why 225,000+ users trust L2L
"What makes L2L so unique is the fact that the product was developed by real manufacturing users. People that truly understand the day-to-day issues and concerns that drive the production floor."
