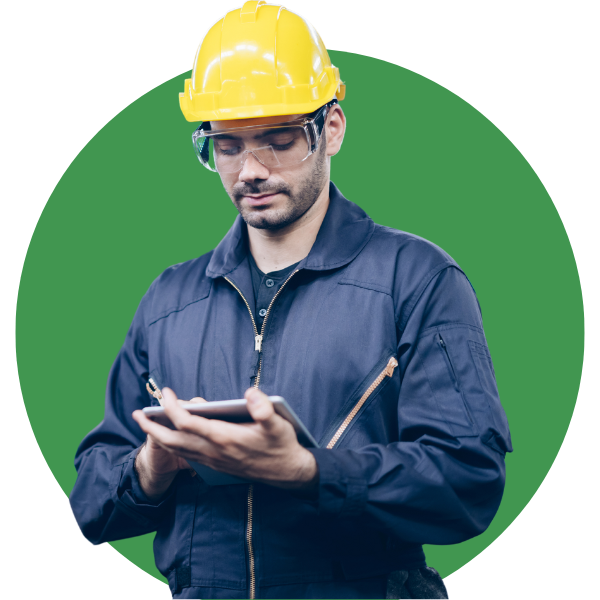
L2L
The Connected Worker Guide
Maximize production throughput by giving your workforce the tools it needs to drive continuous improvement.
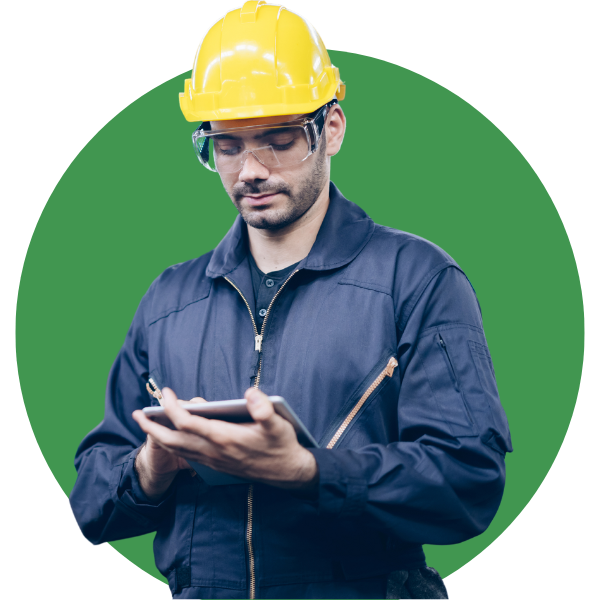
Ready to Get Started? Request a Free Consultation.
As a manager, you’re always dealing with problems at the manufacturing plant. For example, some of your new hires don’t seem to know what they’re doing. The complexities of the manufacturing process took you years to master, and now you have new apprentices who, while eager to learn, can’t work and study at the same time.
So how can you get your new employees up to speed in a way that doesn’t take years?
You need to show these people what to do without actually stopping to do it. Anything less means a lot of unplanned downtime and missed quotas.
In fact, Deloitte reports that an estimated 49% of factory workers lose 10 minutes of productivity per hour due to technological and process inefficiencies. If your training modules rely on insufficient or outdated technology, your workers are likely part of this statistic.
You need a centralized, universal source of information provided by your best associates that you can access instantly. Moreover, you need technology that can show new hires how a piece of equipment works in a way that’s practically self-explanatory.
And this technology is already here — it’s called the connected worker platform.
In this guide to connected workers and connected workforce technology, we’re going to dive deep into the concept of connected work: what it is, where it came from, what you can do with it, and how you can get started.
Simply put, a connected worker is a worker who uses digital technology to operate more efficiently — “sharing sideways” by constantly swapping information with other frontline workers — what the Japanese call yokoten.
The concept of the connected worker is especially prevalent in industries such as manufacturing, construction, and utilities, where real-time data and communication can significantly improve operations and outcomes.
A connected worker solution may look like this:
-
A task needs to be performed, such as maintenance on a complicated piece of equipment.
-
A new worker is assigned to the job.
-
Using standard work descriptions, checklists, digitized repair manuals, and integrated spare parts catalogs, they can see how to perform the maintenance in real time as if they were being given a step-by-step tutorial.
-
If they have a question, they can either look up the information straight from the computer they’re connected to on their device or ask someone else without ever needing to leave the spot they’re standing on.
Usually, the new worker would require hours of hands-on training to perform the maintenance task. With a connected worker solution, they can follow step-by-step guidance and self-serve whenever they get stuck.
The catalysts for the connected worker market were modernized asset performance management and cloud computing. Before the cloud, if operators needed information, they’d have to leave the production line and visit a physical terminal, where they’d sit at a computer until they found what they needed.
With cloud computing, there’s no need to move to a desktop computer. You don’t even have to leave the shop floor. This means you save a lot of time and drastically boost efficiency, worker safety, and productivity.
Younger, more tech-savvy generations of workers have also accelerated the adoption of connected workforce technologies. They know that solutions like smartphones and the internet exist, and they expect their workplaces to use those technologies. They also know that pen-and-paper methods are time-consuming and frustrating. Yes, this is the future of industrial work.
It’s easy to confuse the connected worker with the digital transformation of business. These two concepts are separate, but they’re also directly tied together.
Think of digital transformation as the integration of smart technologies into how corporations run their respective industries. Digital transformation creates an environment in which the connected worker can flourish. What separates connected workers from digital transformation is the garden and the flower: A connected worker is a natural product of digital transformation.
Here’s another way to think about it. In the big machine that is the manufacturing plant, the connected worker is a part of the digital transformation process. Companies implement a digital transformation strategy — essentially switching from pen and paper work to computerized work — and the connected worker is developed as a secondary part of that transformation.
The connected worker and the digital transformation aren’t the same things. They’re just two sides of the same coin.
What’s the Point of Connected Workers if the Old Systems Work Without Them?
No, you don’t have to have a connected workforce to function, as long as you’re okay with doing things the hard way — and losing profits due to inefficiencies. Manufacturing is changing, and investing in digital technology is critical to remaining competitive. Ultimately, the connected worker is how the new generation of workers can get up to speed with the professionals who used to perform manufacturing tasks by hand.
Instead of training new workers in a classroom setting — while a quota is in the back of your mind — you can train them on the job without stopping workflows.
Connected worker platforms give frontline workers the information they need to perform their jobs, whenever they need it. That data is always available, so workers don’t need to stop what they’re doing and visit a computer terminal to look it up.
Instant access to data takes efficiency to a whole new level. It’s just better when workers don’t need to leave their station if they’re not sure how to do something.
There are two layers to the connected worker approach, which can be summarized as underlying and overlying technology.
The underlying technology in the connected worker approach is the tools that enable workers to be connected to both each other and important data. This means smartphones and tablets, among other items — all the IoT devices that your employees need to work together.
But none of these devices would combine into anything meaningful without the overlying technology: A single, cloud-based software platform that keeps it all functioning.
In some aspects, connected worker solutions are current methods, modernized. Think of what’s familiar to the average worker: Social computing, how to read a timeline, how to access information about a particular job, or how to perform maintenance tasks. The connected worker can do all of this with greater efficiency.
Compared to traditional technologies used in manufacturing plants, this new type of digital technology is:
-
Less expensive
-
More intuitive
-
Easier to learn
-
More flexible
The connected worker space is all about technology that empowers employees, improves productivity, and ensures worker safety. Workers can learn new things, collaborate with their colleagues, and gain access to information that helps them perform jobs better.
The connected worker solution enables employees to manage various workflows and processes in a digital environment. Think whiteboards, radio, and printouts, but digitized.
What does a connected worker solution look like to all the stakeholders? Consider L2L’s approach, which offers real-time visibility into what’s happening on the floor and enables workers to take action faster.
For the plant manager, that enhanced visibility means something different than it does for a maintenance technician or line worker. They take different actions depending on the specific problem they’re dealing with. The solution won’t look the same to everyone using the same connected worker technology.
A good connected worker solution enables different perspectives for various jobs. It shows each worker what they need to see so they can take the appropriate action. This contrasts with traditional enterprise software, which only offers one interface for frontline workers to interact with. But this software is typically difficult to learn and cumbersome to use.
L2L consolidates all the information that has traditionally lived on separate systems into one platform that everyone in the manufacturing process can use simultaneously. Imagine if you had maintenance technicians using a computerized maintenance management system (CMMS) to manage their jobs, and those in operations are using an entirely different system. You can’t just fuse the two pieces of software together and turn them into one comprehensive solution. This leads to communication problems because everyone’s looking at different information on their own respective system.
By integrating existing software into a single platform, maintenance work schedules can be coordinated with production runs to minimize downtime. Additionally, improved visibility across departments helps leadership better support workers. An effective connected worker solution has one repository for all information that’s accessible to all authorized users, fostering smoother collaboration.
How Do You Get Started with a Connected Worker Solution?
You might think that with advanced technology like connected worker solutions, you’d need a sizable amount of resources and commitment. But you really don’t need much at all, and the process is very simple to get started with.
What’s really needed is the mindset to use the solution. Connected worker solutions come down to this: Someone with a problem on the floor needs help. Someone else responds and is able to say, “I see you have an issue, and this is how I’m going to help you.”
The software itself is inexpensive, flexible, and easy to learn. The true challenge of connected worker solutions is integrating them into what you already have on the floor. But with pre-built integrations available in L2L Connect, even that isn’t so hard.
There’s a famous scene in “I Love Lucy” in which Lucy and Ethel have a job boxing chocolates in a plant as line workers. At first, the workload is small enough that they have little trouble. But soon, so many chocolates start coming through that they can’t keep up. The result is a manufacturing disaster, and they’re both fired on the spot.
If the two women had connected worker solutions, they’d still have their jobs, and the manager wouldn’t have had any issues. Think about what the problem was for the two: It’s not that they were incompetent or made silly mistakes; it’s that they were given a job that they shouldn’t have been expected to perform in the first place. No one could have kept up with that many chocolates. What Lucy and Ethel needed to do was to ask for help, but they had no way of doing that.
A connected worker strategy prevents frontline employees from being exposed to too much work or unsafe working conditions. They keep workers from being isolated without assistance when they need it. If workers don’t know how to do something, they can immediately find out without even needing to look it up on a computer. In short, if they need help, they can get help right away.
That’s what connected workers do, and it’s what you can do with your own manufacturing plant. Download our connected worker eBook to learn more about what we offer.
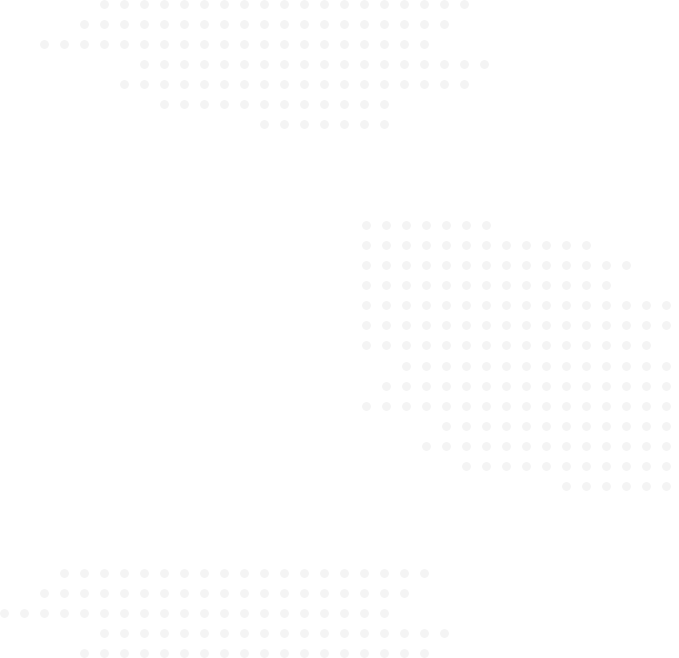
Why Manufacturers Trust L2L
"What makes L2L so unique is the fact that the product was developed by real manufacturing users. People that truly understand the day-to-day issues and concerns that drive the production floor."
