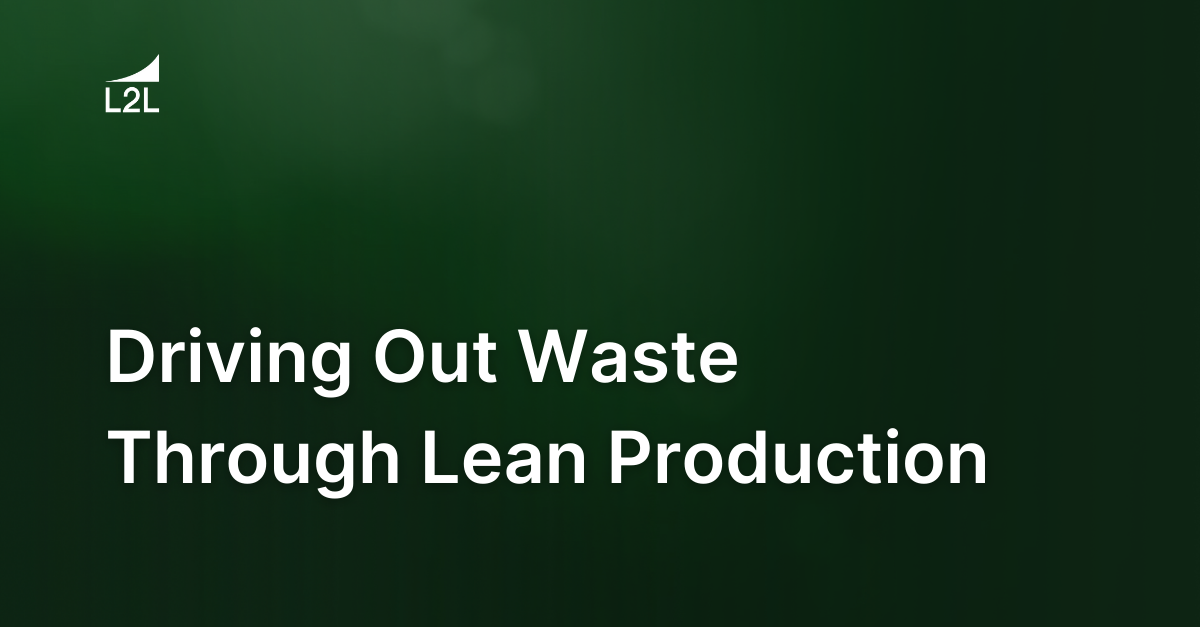
A discussion on lean production first requires the definition of waste. Students of Toyota’s lean production methodologies may be better acquainted with the Japanese term muda, though both muda and waste refer to activities that add cost but do not add value to the end product or service.
Lean production, by extension, is doing more with less through the elimination of waste and the improvement of the remaining workflows.
The Match Up: Lean Production vs. Waste
While the Toyota Production System, one of the original lean production methodologies, defined seven wastes, many recent processes have expanded to incorporate eight. A common acronym used to remember the forms is DOWNTIME:
Defects |
Errors or incomplete products, services, or information requiring replacement or correction |
Overproduction |
Wasting resources creating product/services that are not needed or, for downstream processes, are not ready to receive them |
Waiting |
Idle time due to lack of available materials, machines, personnel, or information |
Non-Utilized Talent |
Failure to fully leverage the skills and talents of the human resources available |
Transportation |
Movement of products, materials, or equipment |
Inventory |
Materials and products exceeding customer demand which consumes resources to manage and may require rework |
Motion |
Unnecessary movement of personnel |
Extra Processing |
Additional processing that creates a product exceeding the customer requirements |
Some companies also include another waste category, injury/incidents. This form of waste encompasses the lost employee time and productivity due to injury.
Lean Production Approach
With waste in all its forms now defined, it must be eradicated. Lean production is the vehicle to achieve this: Identify and eliminate waste to do more with less and better serve the customer. Lean production is classically broken into five principles, as defined by Womack and Jones,
(1) Define Value
The first and most critical principle to implementing lean production at a company is to first define what value is. Without understanding value, a business cannot successfully identify waste - the non value-added work customers are will not pay for.
The business must therefore engage in intensive customer communication to understand for each customer relative to specific products and product capabilities, what they value and will pay for.
(2) Identify the Value Stream
Armed with a thorough understanding of what is valuable to customers, the next lean production principle is mapping the product value streams: The sequence of activities performed to design, create, and deliver a product to the customer, including both physical and information-centric processes.
Each step in the value stream is then analyzed and classified as value-added, non value-added, or business value-added.
Value-Added Activity |
Work that directly changes the product, nature or quality, and which customers are willing to pay for. i.e., Processing crude oil to produce petroleum. |
Non Value-Added Activity |
Activities that consume resources but do not create value according to the customer and that the customer is unwilling to pay for: Waste. i.e., Searching the warehouse for a pallet of packaging components to deliver to the packaging line. |
Business Value-Added Activity |
Work which does not directly create customer value but is required; also called necessary non value-added or needed activities. These activities often relate to legal, regulatory, or customer mandates. i.e., Completing internal audits required to maintain ISO 9001 Quality Management System (QMS) compliance. |
Those steps which create no value are then eliminated, streamlining the value stream in to apply the next principle.
(3) Create Flow
Once non value-added work has been removed from the value stream, the remaining steps must be sequenced in a way that ensures the product is continually being worked on. This activity often proves a challenge for firms, given tendencies for industry to think in terms of departments and therefore cluster work by type.
The failure of such batch processing, even at high speeds, is that it generates waste: Inventory, waiting, and transportation. As such, this lean production principle must be applied with only a mind to continual product flow and the recognition that process steps, as well as functional departments, may require redefinition to support flow.
(4) Establish Pull
With the creation of flow and the transformation of the support infrastructure toward this aim, product throughput times drop drastically and production means will become infinitely more flexible.
The result is a value stream that supports just-in-time production and can accommodate variation in customer demand: A system based on the lean production principle pull, where actual demand dictates the production schedule opposed to traditional forecasting. Once established, pull systems become self-perpetuating: The company's ability to consistently supply customers drives down variability in customer demand.
(5) Perfect
Lean production, like so many other improvement practices, is a journey and not a destination. The success of the previous four factors (defining value, mapping the value stream, creating flow, and establishing pull) is that they are interconnected. A change in demand, a refinement in the value definition, faster flow -- each will force hidden forms of waste to the surface so improvement becomes cyclical.
Having a continuous improvement system in place that is visible, engaging, and to which all employees are accountable will ensure that new forms of waste are addressed by encouraging and empowering them to call out process breakdowns and share opportunities.
The Power of Lean Production
Lean production is a powerful means to refocus and reinvigorate businesses across industries by applying its five principles to eradicate waste. However, these benefits are lost without incorporation of these ideals into company culture and the means to support that adoption.
A Lean Execution System (LES) can facilitate employee engagement by sharing performance throughout the organization, linking each workflow to the company goals, and providing employees a platform to identify waste and share improvement opportunities. See how Leading2Lean's LES helps customers achieve lean production across their organizations today.
Revisions
Original version: 28 February 2020
Written by: Amy Mele
Reviewed by: Daan Assen
Please read our editorial process for more information
Related Posts
Subscribe to Our Blog
We won't spam you, we promise. Only informative stuff about manufacturing, that's all.