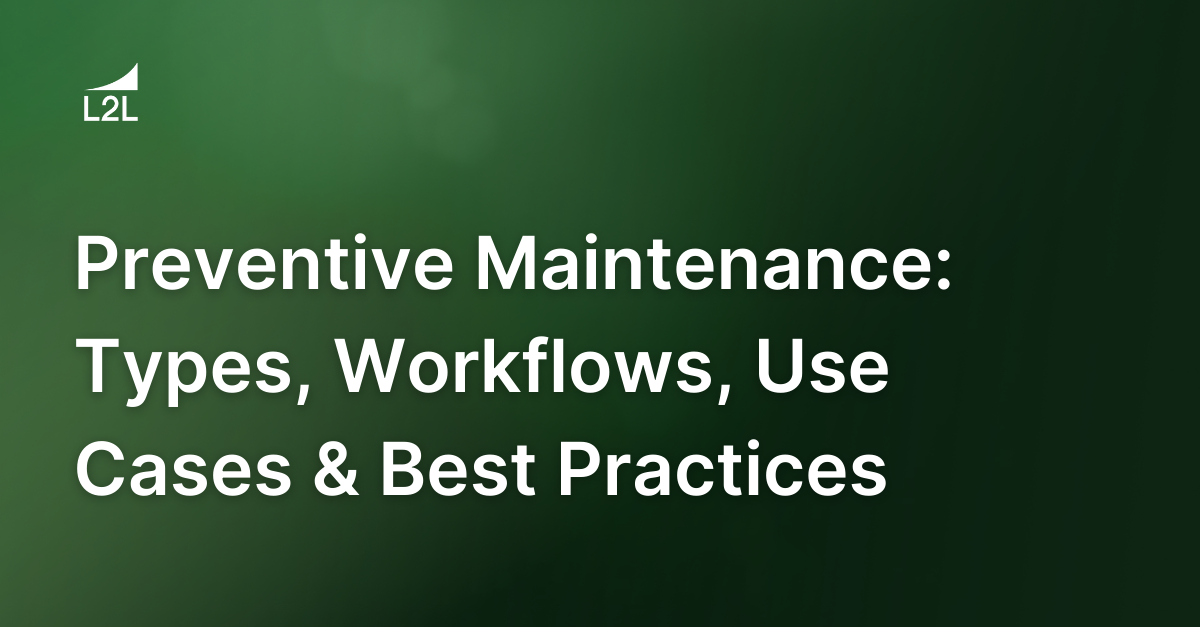
Decades ago, most manufacturers relied on reactive maintenance to address equipment issues. Maintenance teams would only fix a machine once it broke down or became too hazardous to operate, resulting in expensive repairs and excessive downtime.
This scenario is what preventive maintenance (PM) aims to, well, prevent. Relying on proactive measures to mitigate breakdowns, preventive maintenance systems are much more common today — although most facilities haven’t fully streamlined their PM.
In this article, we discuss the importance of preventive maintenance, the types most commonly used in manufacturing, and how plant leaders can successfully shift from reactive to preventive maintenance in their plants.
What is preventive maintenance?
Preventive maintenance is a maintenance strategy that relies on regular, scheduled maintenance activities to prevent equipment failures and unexpected downtime. Due to its low cost and ease of implementation, it has widespread use. But it's especially important in manufacturing and other industries that rely on complex, expensive machinery.
In practice, preventive maintenance involves a systematic schedule that includes tasks such as lubrication, adjustments, cleaning, and parts replacement based on a predetermined timeline or usage metrics. It requires careful planning and thorough documentation to track maintenance history and plan future work.
Common applications of preventive maintenance in manufacturing include:
-
Lubrication: Regularly applying lubricants to moving parts to reduce friction and wear.
-
Cleaning: Removing debris, dirt, and contaminants to ensure machinery operates efficiently.
-
Inspections: Conducting visual and instrumental checks to identify wear, damage, or abnormalities.
-
Adjustments: Fine-tuning equipment settings to optimal conditions for performance and efficiency.
-
Part replacements: Swapping out worn or near-end-of-life components before they fail.
-
Calibration: Ensuring measurement accuracy by adjusting instruments to standard settings.
-
Testing: Performing operational tests to verify functionality and detect potential failures.
-
Software updates: Updating control software to enhance functionality and security.
-
Electrical system checks: Inspecting wiring, connections, and power sources for signs of wear or damage.
-
Safety checks: Verifying that safety mechanisms and guards are in place and functional.
When properly implemented, preventive maintenance leads to a significant reduction in unplanned downtime, big cost savings, increased production efficiency, fewer production delays, and a safer working environment.
There are two main types of preventive maintenance
The two primary types of preventive maintenance are usage-based maintenance and time-based (a.k.a calendar-based) maintenance. Most manufacturers use a combination of the two on different assets in their facilities. The type of preventive maintenance used depends on the requirements of each asset type and the conditions in which it operates.
Usage-based maintenance
Usage-based maintenance focuses on servicing machines based on how much they’re used instead of relying on a set schedule. Maintenance is performed by tracking metrics like hours used or products made. This method prevents excessive wear and tear, reduces costs, and keeps production running efficiently.
By using data to decide when to service equipment, usage-based maintenance helps reduce excessive maintenance and optimize internal resource allocation.
Here are some examples of usage-based maintenance in a factory setting:
-
Assembly line robotics: Maintenance is scheduled after a robotic arm completes 80,000 cycles, preventing the arm from breaking down and stopping production.
-
CNC machinery: For a CNC machine, maintenance is prompted by the amount of material it’s processed. This ensures the machine is serviced after milling or cutting through a set volume of metal, preserving precision and extending its lifespan.
-
Packaging equipment: Packaging machines are checked for wear after sealing 50,000 boxes, keeping the operation efficient and avoiding shipping delays.
Time-based maintenance
Time-based maintenance schedules maintenance activities at specific intervals — daily, weekly, monthly, or yearly basis. The exact interval depends on the type of equipment in question, its frequency of use, and its operating conditions.
Examples of time-based maintenance scenarios include:
-
HVAC systems: Factory HVAC systems may require annual servicing before peak usage seasons to ensure optimal climate control and energy efficiency.
-
Safety equipment inspection: Fire extinguishers, emergency lights, and safety alarm systems are checked and tested every six months to comply with safety regulations.
-
Conveyor belts: Conveyor belts may undergo routine maintenance every quarter to inspect for wear and tear, adjust tension, and lubricate moving parts. This prevents breakdowns and ensures smooth operations.
-
Machine lubrication: To keep machines running smoothly and avoid excessive wear and tear, maintenance teams will perform routine mechanical lubrication every few weeks. However, the frequency depends on the type of machine.
-
Equipment cleaning: Manufacturers may schedule daily cleaning for machines and equipment, especially if issues like debris or excessive lubrication pose safety risks to shop floor workers.
When to use PM: Types of assets that should be on a preventive maintenance program
Implementing a preventive maintenance strategy is arguably the most effective way to reduce costs associated with maintenance and downtime. By proactively finding and addressing equipment issues, companies can save themselves hundreds of thousands of dollars annually.
Manufacturers looking to move from reactive to preventive maintenance should start this shift by identifying which assets will benefit most from a PM approach. Preventive maintenance is well-suited to industrial assets:
-
That are critical to operations: Focus on assets your factory can’t operate without. These can include conveyor belts, HVAC systems, and assets essential for product creation (e.g. extruders, rollers, mixers).
-
With high cost of failure: If production stops when an asset goes down or the asset is expensive to replace — put it on your PM list. CNC machines, compressors, extrusion machines, and power generation systems are prime examples of high-cost-of-failure assets.
-
That need preventive maintenance for regulatory compliance: Assets that need to meet certain regulatory standards or play a critical role in ensuring your facility’s compliance also need preventive maintenance. These can include safety equipment, boilers, environmental control systems, electrical systems, and more.
-
That have predictable wear and tear: If you can easily predict when an asset will need repair, it’s worth putting it on a preventive maintenance program. Machines like robotic arms, hydraulic presses, pumps, and compressors fall into this category.
While this isn’t an exhaustive list of machines you should add to a preventive maintenance program, it’s a good place to start if you’re just starting to implement PM strategies.
The differences between reactive, preventive, and predictive maintenance
The differences between reactive, preventive, and predictive maintenance strategies primarily revolve around how and when maintenance activities are performed in relation to equipment failure:
-
Reactive maintenance (Run-to-failure): Maintenance and repairs are performed only after the equipment has broken down. This strategy might be cost-effective for non-critical equipment. However, it often leads to higher repair costs and longer downtime.
-
Preventive maintenance: Maintenance activities are scheduled at predetermined intervals, regardless of the current condition of the equipment. The goal is to prevent failures before they occur. However, it might lead to over-maintenance of equipment, incurring unnecessary costs.
-
Predictive maintenance: Relies on real-time data collected from equipment through sensors and monitoring tools to schedule work at just the right time, minimizing downtime and maximizing performance. However, it requires significant investment in technology and skills to analyze data and predict failures accurately.
How to get the most out of preventive maintenance
Like any large-scale process implementation, this type of maintenance takes some planning, time, and incremental execution.
Here’s how you can ensure that you’re maximizing the benefits of preventive maintenance.
Prioritize assets based on production impact
Not all equipment in your facility carries the same weight in terms of production impact. It's crucial to identify and prioritize your assets based on their criticality to your operation. Focus on equipment that, if failed, would lead to significant operational disruptions or safety hazards.
This targeted approach ensures you allocate your resources more effectively.
Create a preventive maintenance plan
A generic plan won’t cut it. Your preventive maintenance plan needs to be as unique as your operation. Develop tailored schedules, procedures, and checklists for each prioritized asset, incorporating both the manufacturer's recommendations and your own operational insights.
This bespoke approach ensures that maintenance activities are perfectly aligned with the specific needs of each piece of equipment, optimizing performance and extending lifespan.
Implement preventive maintenance systems
Leveraging preventive maintenance software is a game-changer. It's not just about keeping track of what needs to be done; it's about strategic planning, scheduling, and execution.
These systems help ensure that maintenance tasks are performed on time and help analyze trends for better decision-making. The ability to plan, schedule, run, and track maintenance activities through a centralized system will keep your operations running smoothly and efficiently.
Standardize preventive maintenance work
Consistency is key in preventive maintenance. By developing and implementing standardized maintenance procedures, you ensure that every task is performed thoroughly and efficiently, regardless of who is performing it.
This standardization not only improves the quality and reliability of maintenance work but also enhances safety across your facility.
Help your maintenance team succeed
Your preventive maintenance strategy is only as good as the team executing it. Ensure that your maintenance personnel are not just adequately trained for the task you assign to them, but also equipped with the right tools and parts.
Connected workforce platforms like L2L ensure that maintenance tasks are completed on time and correctly by streamlining communication. For instance, machine dashboards centralize machine and equipment data so maintenance technicians have quick access to information, required tools, and operator notes.
Schedule Optimal Downtime
Finding the perfect time for maintenance can be challenging, but it’s essential for minimizing impact on production. Plan your maintenance activities during periods of low production when possible, ensuring that your technicians have what they need to complete their work efficiently.
Effective downtime scheduling is a balancing act that, when done correctly, can significantly reduce operational disruptions.
Maintain an up-to-date spare parts inventory
Keeping an up-to-date inventory ensures that critical spare parts are always available when needed, reducing mean time to repair (MTTR) and streamlining the maintenance process. Don’t let all of your planning go to waste because the technicians didn’t have the right parts to perform scheduled maintenance tasks.
Don’t overdo it
More isn’t always better. It’s important to monitor equipment performance and adjust your preventive maintenance frequency accordingly. Over-maintenance can be as detrimental as neglect, leading to unnecessary downtime and resource expenditure. By tracking failures and analyzing data, you can fine-tune your maintenance schedule to strike the perfect balance between upkeep and productivity.
By following this advice, you will maximize the value and effect of your preventive maintenance strategy.
Streamline preventive maintenance with the L2L Platform
Preventive maintenance is so much easier to run with the right software support. You need a solution that offers a complete, real-time view of asset data, automatically alerts technicians to mechanical problems, helps you easily schedule maintenance work, and allows workers to easily share insights on the shop floor.
L2L’s connected workforce platform offers manufacturers all of these benefits — plus seamless interoperability with major manufacturing software types (e.g. MES, ERP, inventory management), scheduling dashboards, and mobile-friendly interfaces.
Discover how our connected workforce platform simplifies maintenance for everyone in your plant, and see our product in action with our FREE Interactive Product Tour!
Revisions
Original version: 7 March 2024
Written by: Evelyn DuJack
Reviewed by: Daan Assen
Please read our editorial process for more information
Related Posts
Subscribe to Our Blog
We won't spam you, we promise. Only informative stuff about manufacturing, that's all.