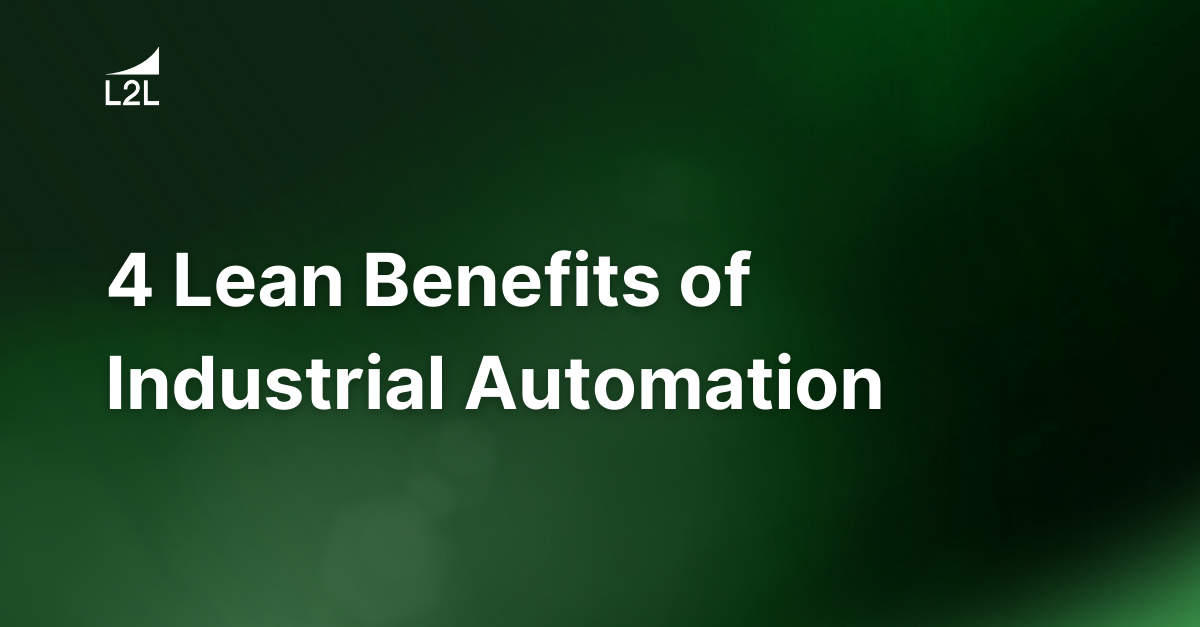
Over the years, and throughout my career, I have seen many different approaches and methods to incorporate Industrial Automation in modern manufacturing. I have worked and been part of exceptionally large, completely automated manufacturing lines. On the other side of the wall, I was also part of the design and layout of manufacturing cells that are manual, and have little, if any, automation.
Year after year, the challenges and goals were to configure and better define the perfect combination of the people with the modern Industrial Automation of products, processes, and information. Being part of and working closely with these manufacturing methods, both automated and manual, I believe the best combination and ideal layout lies somewhere in the middle.
Implementing Industrial Automation in a process or a site does not automatically categorize the manufacturing process as “Lean Manufacturing”. Utilizing lean manufacturing philosophies and principles, along with measuring key performance indicators to achieve the vision and mission of a site, will help prioritize and clarify opportunities for Industrial Automation in four ways.
Safety
Safety is naturally one of the highest priority opportunities when considering Industrial Automation. Is your process susceptible to safety events? Can you show data over time, quantify, and identify event specific details? In order to capture this data and event details, you will want to make sure you are utilizing a modern digital LES (Lean Execution System) like Leading2lean (L2L). Use the objective data to identify areas of concern and to measure results. Many of the Industrial Automation projects I was part of were initiated as a direct result of safety event data captured in L2L. My team used this data to identify and prioritize key areas to begin executing Industrial Automation.
Quality
Let's face it, humans are pretty good at identifying poor quality and defects. Our production teams do a great job with the jidoka process. They stop the process and notify supervision when defects are found. However, the reality is, we as humans cannot visually identify all defects. We know some percentage of defects are very subjective and cannot be identified consistently by our production teams. Poor quality instances are prime candidates for Industrial Automation. With today's technology, even the most subjective visual defects can be identified with Industrial Automation. Use your L2L quality data, such as scrap, jidoka, and first time quality results, to PFMEA (Process Failure Mode Effects Analysis) your process. Use your data, identify high severity and high occurrence rates.
Delivery
We can say delivery is not as critical as other elements in manufacturing for adding Industrial Automation. However, let's acknowledge the reality when it comes right down to it. In terms of satisfying the customer, delivery is just as important as other areas of improvement. Delivery is probably one of the most common variables considered when implementing Industrial Automation.
Employee Morale
At times, it may seem like addressing employee morale ranks incredibly low on the likelihood scale for incorporating Industrial Automation. However, in my experience, it has been high on the priority list. At the risk of sounding cliche, happy employees make happy customers.
Consequently, we need engaged, committed, productive crews. People want a challenge; they want to add value and feel they are making a difference. I have found some of these very monotonous or repetitive tasks that are not desirable to the average associate can be prime candidates for implementing Industrial Automation. These conditions have many objective measurable indicators, such as high attrition and absenteeism. These circumstances and the resulting behavior can also manifest themselves as instances of poor execution (PEFF), poor OEE, and poor quality.
Of course, not all instances of poor production performance are candidates for Industrial Automation. However, it's our responsibility to understand what our data is telling us. If you're not reviewing your LES System data, from L2L or elsewhere, you can't fully grasp the current condition, making it much harder to identify anomalies and abnormal findings. You may be missing opportunities to improve employee morale and focus on potential instances where Industrial Automation would make a huge impact.
Impact of Industrial Automation + Lean
Industrial Automation, when approached from and used in conjunction with, lean philosophy and practices, can have tremendous benefits that play a huge role in all missions of the worksite. When applying lean concepts together with Industrial Automation, consider total cost and impact on the following:
- Purchase Price of Industrial Automation tools
- Maintenance costs
- Operating costs
- Number of Operators required plus cost of training
- Expense of ensuring flexibility - moving systems and tools where needed
- Expense of modifying existing equipment and processes
- Costs (temporary) of changes to output and throughput
- Costs to increase flexibility and changes to products and production
- Operator Skill Level
- Maintenance Skill Level
- Purchasing price and inventory of increased spare parts
- Advance lead times and set up times
- Changeover times
- Real estate
- Design skill
- Quantity and speed, which may initially be reduced
- Reliability
- Ease of retrofit
- Cost of quality
When considering modernizing your manufacturing processes and equipment through Industrial Automation, the ability to utilize your LES system opens the door to not only automating your equipment, but also to ensuring your manufacturing process is autonomous.
With Industrial Automation, automated and autonomous manufacturing allow for a seamlessly integrated hardware and software system like L2L's LES. Utilizing your LES system with modern Industrial Automation can greatly enhance the flexibility and efficiency of your digital factory.
See how L2L's LES can provide the insights you need for smart industrial automation.
Revisions
Original version: 1 July 2020
Written by: Jon Richardson
Reviewed by: Daan Assen
Please read our editorial process for more information
Related Posts
Subscribe to Our Blog
We won't spam you, we promise. Only informative stuff about manufacturing, that's all.