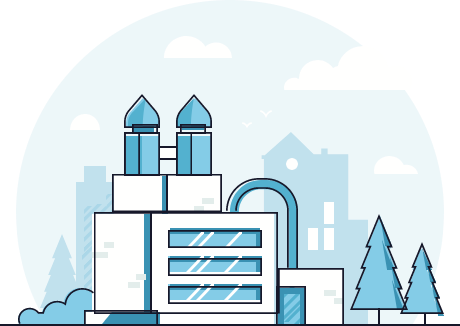
L2L
The Smart Factory
and What It Means for Manufacturers
Smart Manufacturing FAQs & Resources
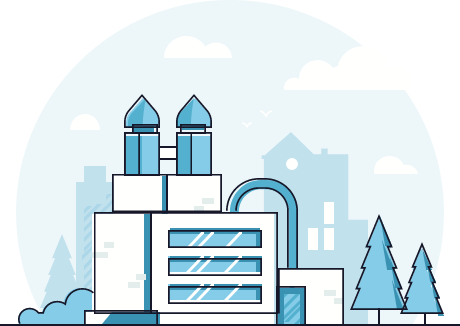
Ready to Get Started? Request a Free Consultation.
The term “smart factory” (a.k.a. "digital factory" or "intelligent factory") was initially coined at the Hanover Fair in 2011, although the ideas and practices known as smart manufacturing today have been developing for decades.
The same essential components that make up a traditional manufacturing plant apply to a smart factory as well. What makes a smart factory “smart” is its high level of digitalization when it comes to the control of machinery and production processes. It utilizes sensors, AI (artificial intelligence), ML (machine learning), cloud computing, and other Industrial Internet of Things (IIoT) technologies to enable real-time data gathering, transfer, and analysis.
When thinking of the smart factory, many picture a clean and highly efficient operation where all things work in unison, like clockwork — where downtime, defects, and other production disruptors are minimal. A manufacturing environment where plant and IT leadership plan and execute based on real-time data — where IT and OT are in perfect harmony.
The reality is that for most manufacturers, the experience is anything but perfect harmony. The questions then become: What’s possible? And what’s realistic?
Manufacturing leaders recognize that ignoring the smart factory opportunity (maintaining the status quo) will only leave them in the rearview mirrors of their competition. On the flip side, the attempt to transform the entire plant through one big technology push is where most forward-thinking manufacturers get off course.
The rise of the smart factory represents significant opportunities for gains in efficiency and productivity, but must be approached pragmatically. More on this below.
Smart manufacturing refers to factory operations where digital technologies are applied to connect machines, people, and processes together to ultimately produce product more efficiently. This combination of hardware, cloud computing, and big data should provide a clearer picture of where opportunities exist for improvement.
A smart factory, on the other hand, is simply a term describing a facility that enables smart manufacturing operations. It incorporates hardware and software elements into a cyber-physical system.
Smart factory and smart manufacturing fall under the umbrella of Industry 4.0 and are examples of digital transformation of the manufacturing environment.
The benefits that a particular manufacturer is looking to achieve should drive the decisions of whether to deploy, and where to deploy smart factory technologies. As Steven R. Covey taught, “begin with the end in mind.”
Broadly speaking, benefits for manufacturers include improvements in efficiency, quality, safety, and reduction of costs in a variety of ways. Ultimately, these benefits should lead to increased competitiveness and profitability in the marketplace.
Common benefits can be broken into four categories:
1. Asset efficiencyBy connecting assets such as machines and facilities through IIoT devices, data can be collected and analyzed to reveal asset performance issues that may or may not have previously been on the “radar” of plant leadership. As the most costly issues are identified and resolved, this translates into reduced machine downtime and optimization of production capacity.
It’s important to understand, however, that more data does not necessarily lead to more clarity about where to focus resources for the greatest improvements.
Data must be pulled into a smart manufacturing system, such as L2L’s digital reliability and production platform. The ability to view the data and drill down to understand what issues are costing the company the most and therefore merit the most attention is critical to realizing the desired efficiency gains.
2. QualityThere are a variety of causes that lead to poor quality including environmental, machine, or human error. The key is detecting these issues early and often so they can be resolved before they bloom into bigger problems. Catching and resolving issues early will typically lead to significant improvements in scrap rates, lead times, and yield. Better quality of products means fewer defects. In industries such as automotive, this can mean the avoidance of devastating product recalls and potential tragedies for customers.
3. Improved processesAs processes are optimized, the efficiency gains will impact the bottom line of the factory. Across L2L’s customer base, we have found that nearly 90% of processes or workflows are not machine related, but still represent the potential for production disruption when issues occur.
Technology offers visibility and issue prioritization. Plant workers can isolate and solve problems that have the highest negative impact on production. This clarity and focus provide the direction, and when coupled with responsive action, will translate into improvements and lower operational costs.
4. Higher level contribution from peopleThe smart factory unlocks the opportunity for the workforce to raise their level of contribution. As automation and artificial intelligence play a larger role on the plant floor, it reduces the need for humans to perform menial and repetitive tasks that fatigue and wear down the human body. It also creates additional need for higher level data analysis and decision making, even at the lowest levels.
As smart factory technology provides access to more, and better real-time data on the shop floor, it empowers the machine operators to identify, prioritize, and resolve issues that can disrupt production performance.
The path towards becoming a smart manufacturer is closely tied with a facility's capacity to collect and analyze data. The following levels can help you assess the progress of your facility towards becoming a smart factory.
Level 1: Integrated data
The most basic requirement of working smart is consolidating and integrating data into a central repository. This allows engineers, managers, and operators to monitor the facility in real-time, which facilitates quick and agile decision-making.
Level 2: Predictive analytics
The next level progresses to a more proactive approach. Instead of just reading data and reacting to whatever you find, you can get ahead of a “situation”. For example, at this stage the factory can use machine learning and artificial intelligence to combine historical data with real-time data, and make predictions about incoming asset failures.
Level 3: Prescriptive analytics
Data analytics can further improve, streamline, and automate the decisions that need to be made. With enough historical data, you can build and implement prescriptive analytics that go a step beyond predictive algorithms.
Prescriptive algorithms can help you optimize manufacturing resources by outlining “what-if scenarios”, and offering recommendations for managing equipment and processes.
Level 4: AI-driven automation
The futuristic goal of a smart factory is to execute any action instantaneously as soon as the system identifies the need. Having a fully-automated factory requires a very large amount of historical data and use cases, which the algorithms can then use to make the right decisions on their own.
There will always be inherent risks that come with highly automated systems, and some factories will still prefer having a person review and accept machine recommendations.
ADAC Automotive Smart Factory Initiative
ADAC Automotive is a supplier of engineered products to the automotive industry. Historically, their process recording mechanisms were painstakingly manual, relying on paper-based systems that wasted time and gave limited real-time visibility into their plant floor operations. They had a clearer picture of how their plant had been operating versus how their plant was operating at any given time. And when something broke, there was no connected way to notify, triage, and fix the issue.
“Machine downtime has a large impact on direct and indirect labor variance and lost production throughput, so it was essential ADAC make a shift to a Smart Factory concept to maximize machine availability.” - Brent Warren Director of Assembly Operations
ADAC selected L2L’s connected worker platform to unify their data, empower their workforce and increase efficiency. They started with small, highly measurable projects, and scaled up as they found success. Today, 287 assembly assets and 58 molding machines are fully integrated and automatically reporting descriptive machine downtime events into L2L, and ADAC has a standard real-time process for monitoring and responding to these issues quickly on over 200 production lines in their four Michigan-based facilities. This smart factory platform has enabled ADAC to embrace cycle-based preventative maintenance and increase machine utilization.
Results after 12 months:
- 26%
Reduction in number of preventative maintenance work orders - 367%
Improvement in on-time % preventative maintenance - 62%
Reduction in major downtime events
For more insights on where to get started on your digital transformation journey, you’ll find practical and powerful insights in this webcast recording with Smart Industry: How to Succeed With a Minimalist Approach to Digital Transformation.
Siemens Electronics Works Amberg (EWA)
The Electronics Works Amberg (EWA) is a Siemens facility that produces circuit boards, controllers, and other electrical devices. With 17 million components produced per year, the EWA utilizes an equally impressive level of technology.
For example, the facility's production equipment employs artificial intelligence in analyzing data picked up by sensors. This system uses an AI-based algorithm that automatically evaluates the quality of soldered portions of a circuit board.
Other applications of smart manufacturing are evident in the facility's warning systems. Anomalies in the operating conditions of particular machines can predict downtime and failure events. Through the cloud, this information is easily disseminated to relevant plant operators, allowing them to respond in a timely manner.
Cloud computing
Cloud computing leverages internet connections to access web-based software applications that are hosted on external servers. This allows manufacturers to deploy SaaS (Software as a Service) applications at a fraction of the cost of on-premise solutions that require servers and other hardware to deploy. Due to macro forces the adoption of cloud-based systems has been accelerated in recent years. According to Gartner, “the worldwide infrastructure as a service (IaaS) market grew by 40.7% in 2020.” This trend certainly holds true in the manufacturing sector and will continue to accelerate in the future.
A few benefits of cloud technology for manufacturers include:
• Dependability: Cloud-based systems are maintained by the provider, which means that their success is dependent on the customer’s ability to access and utilize it 24 hours per day, every day. As a result, reliability of cloud-based systems is higher than on-premise systems.
• Hardware cost savings: Since cloud-based systems do not require the manufacturer to host them on their own servers, this helps them avoid significant hardware costs.
• Access to information: Access to information becomes possible through cloud-based technologies from any location while still maintaining strict levels of security. This flexibility makes keeping a real-time pulse on plant operations much easier, and enables increased organizational agility as a result.
• Increased efficiency: IT departments no longer need to manage and update software applications since SaaS solutions are continually updated by the provider. This and other efficiencies add up to a competitive advantage for the manufacturer.
• Scalability of the solution: Cloud-based platforms can scale up or down depending on the needs of the manufacturer much easier than on-premise. This can also contribute to the manufacturers ability to adapt, manage costs, and be responsive to ever changing demands.
Sensors
Sensors are an important part of a smart factory because they allow for real-time monitoring of potential disruptors to production. These can include optical sensors that use image capture to detect abnormalities in machine or materials processes as well as vibration, pressure, proximity, contact, and other measurements that can indicate a deviation from normal operating conditions.
These IIoT sensor technologies are becoming more affordable and efficient to deploy every year, and can be a powerful tool when deployed pragmatically and purposefully (like tracking a specific failure mode).
Machine learning
Machine learning (ML) is a type of artificial intelligence (AI) intended to extract additional insights or patterns out of data that’s already being collected in the factory. With large volumes of data, patterns can be detected which can be used to train sophisticated algorithms to identify when these patterns are likely to be repeated.
For manufacturers, ML is often applied to achieve predictive maintenance where machine or other breakdowns can be predicted and prevented. How equipment is used in different factories will vary greatly, so getting to a point where maintenance is performed just when it’s needed, not at some time interval, can add up to huge cost savings. ML can also be applied to improve efficiency of power and other utilities consumption, predicting inventory levels and needs, and feeding other production consumption or quality data back to the factory to influence product improvements.
Additive manufacturing / 3D printing
Additive manufacturing, also known as 3D printing, refers to the technology that builds three-dimensional objects by applying superfine layer upon layer of melted or liquified material. This process of adding layers until the object is completed is done by computer-aided-design (CAD) software that guides a print head that can precisely apply the material needed for each layer. This level of precision allows for 3D printed objects to be dependably used for important industries such as automotive, aerospace, and medical device manufacturing. 3D printed products can be made from materials such as thermoplastics, ceramics, metals, and even biochemicals.
Augmented reality
Augmented reality can have several applications inside a smart factory. Wearable technologies such as Google Glass provide a “small, lightweight wearable computer with a transparent display for hands-free work.” These smart technologies allow the user to have an enhanced view of their surroundings that includes superimposed information or visuals related to completing their job. One powerful example is asset maintenance. For a maintenance technician, having this information in front of your eyes, while on-site at a machine breakdown, can improve the speed of the fix and reduce human errors, leading to improved efficiency and reduced costs.
Digital twins
In manufacturing, a digital twin is a virtual representation of a product, equipment, or process. As data is collected around products or processes, this data can be used to gain insights that will drive improvement for future iterations. As data is gathered from the original object or process, adjustments can be made to the digital twin to test different changes or improvements and their impacts before implementing them in real life.
Using IIoT in manufacturing
The Industrial Internet of Things (IIoT) refers to sensors, machines, instruments, and other devices that are interconnected or networked together and leveraged through cloud computing.
This connectivity facilitates the collection of data from each of these sources, which can be aggregated and visualized in software and dashboards. Analysis of this data can (or should) lead to clarity about plant floor operational performance, and it can help identify opportunities for improvements.
IoT is used for a variety of benefits on the plant floor including visibility to production performance, monitoring for quality issues, and triggering of material needs.
The most common example involves the deployment of connected devices such as sensors on the factory floor to monitor machine performance and health. This opens up the path for condition based maintenance (CbM), where issues are detected by sensors and addressed as they occur; and Predictive Maintenance (PdM), where sensor measurements are applied to formulas to determine when maintenance should be performed in the future, and schedule the activities to avoid the predicted issue.
How will Big Data impact factory operations?
Most manufacturers collect large amounts of data, and the quantity is accelerating. The industry is generally good at using this data for tracking purposes, but fails to tap it’s potential for driving operational improvements.
This can be a challenge because in order to gain reliable insights that can be used for decision making, different data sets typically must be merged and visualized in a way that humans can make sense of the data. Plant leadership and even the workforce need to know what the data means and what it’s telling them to do.
Instead, in many manufacturing plants, large amounts of data are collected and ultimately end up in the “data graveyard,” never to be seen again.
Having a system that can take various data sets and make them actionable, resulting in improved operations, is key to smart manufacturing success.
A Smart Manufacturing software solution is a platform that unlocks the value of smart manufacturing technologies for the factory. As mentioned above, if large amounts of data are collected from sensors and various systems (Big Data), but that data is never used to make better decisions and drive improvements, then the data is ultimately useless.
Therefore, a smart manufacturing platform is one that provides five key capabilities that are foundational for smart factory success:
1. Visibility at each level: Real-time visibility into plant floor operations (what issues are occurring, where, how often, etc) is the first requirement to understanding where to deploy smart technologies to solve specific problems.
2. Prioritization insight: Once you know what problems are occurring, where they’re occurring, and how often, then you can couple that with cost and impact data to quickly prioritize which problems are bleeding the company the most, therefore should be solved first. This might sound obvious, but focusing attention on solving the RIGHT problems is incredibly important.
3. Resolution structure: Once issues are identified and prioritized, manufacturers need a resolution structure that notifies the resources required to fix the issue, escalates unresolved issues when necessary, and provides transparency into how the issues were ultimately resolved and by whom. Then the solution to the problem can be turned into a best practice and shared with other lines and plants within the company.
4. Speed to value: This pragmatic approach to deploying smart factory technologies is key to success. To take a technology-led approach where sensors are implemented throughout the plant, without first understanding where they can generate the quickest ROI is a common pitfall. On the contrary, knowing where the biggest problems are and deploying technologies to solve them can generate both quick and significant ROI. Taking this approach creates the speed to value the manufacturers need to drive competitive advantage.
5. Employee empowerment: In the end, the above capabilities and the corresponding benefits cannot be achieved without human action. By connecting your workforce to actionable data, and empowering them to act on it, you unlock the greatest resource for improvement that you have - the human mind and desire to make a difference.
In the end, success is measured by return on investment (ROI) and how quickly it can be achieved. With these five capabilities, the factory now has the foundation for a successful smart factory initiative that will positively impact the bottom line.
To learn more about this pragmatic approach to the smart factory and the five key capabilities, we recommend the ebook: A Smarter Approach To The Smart Factory.
Also, check out this video: Five Essentials for A Smart Factory
What is Industry 5.0?
Industry 5.0 is the next industrial revolution taking place, characterized by people working alongside robots and smart technologies. Industry 5.0 recognizes that rather than seeking to eliminate humans from the equation, manufacturers will find new levels of efficiency and effectiveness by leveraging machines and AI to augment human capabilities.
What do workers in modern, automated factories do?
People think that the end goal of automating a factory is to achieve a “lights out” operation. By reducing the headcount, you reduce labor burden on the bottom line and reduce the potential for human error.
Elon Musk famously tweeted, “Yes, excessive automation at Tesla was a mistake. To be precise, my mistake. Humans are underrated.”
Instead seek to elevate the opportunity for the human to contribute. Arm them with the right data and the right times to make better decisions and allow them to actively solve problems. Empower them with intuitive smart manufacturing applications that make their job easier and more fulfilling. The menial tasks that machines can perform provide the opportunity for the workforce to access and analyze data to make smarter decisions and take smarter actions. The human is more critical than ever on the factory floor, but the role of the workforce is changing. Embracing this change is part of the equation for success in coming years.
The transition towards smart manufacturing can take years, not months. The plant has to go through several stages of development. Think of it as a process that starts with an initial push for modernization which evolves through continuous improvement.
Consider these high-level steps as you transition from a traditional facility to smart manufacturing:
1) Build a strategy: As with any significant undertaking, you need to lay down a clear plan that aligns with your organization. Start with a vision, identify clear objectives, and develop an execution plan. At a high level, there have to be discussions about the available budget and expected returns.
2) Establish connectivity: To enable smart manufacturing, a facility has to implement adequate hardware and software solutions. Network infrastructure, Industrial Internet of Things (IIoT) equipment, and a cybersecurity strategy are key areas to consider.
3) Integrate systems: This stage aims to combine the best of the virtual and physical worlds. Integrating information and operation technologies will allow the facility to gather relevant data about the condition of their equipment and the flow of their production processes.
4) Develop the necessary analytics: You can’t make data-driven decisions without proper data analytics and intelligence. Applying advanced analysis and learning algorithms makes way for predictive and prescriptive recommendations.
5) Scale, optimize, and refine: The roadmap to smart manufacturing does not stop at the proof of concept. The last stage refers to the importance of finding ways to expand current applications while optimizing resources.
In the blog post, Smart Factory - Where To Get Started, Eric Whitley touches on 5 keys to a successful Smart Factory start. Take a look to get practical insights on simplifying the scope, knowing the true goal, using your smartest device, and more!
Are you curious about your plant's return on investment by initiating a smart factory project? Try our free ROI Calculator.
Or need a simple but powerful digital maturity assessment so you can know where you are and where to invest next? Visit our Smart Manufacturing Scorecard to find out.
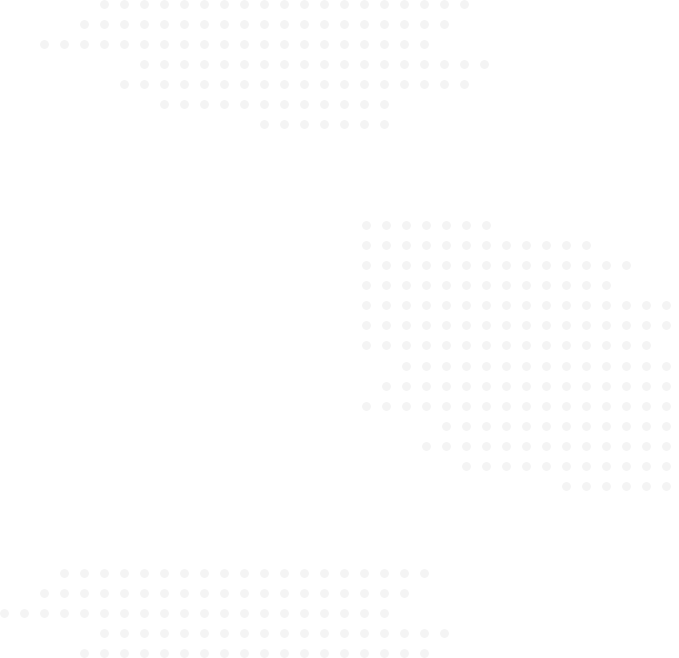
Change Your Shop Floor Culture
"The L2L data has helped Maintenance and Operations teams understand the importance of what they do. The culture is starting to change"
.png)