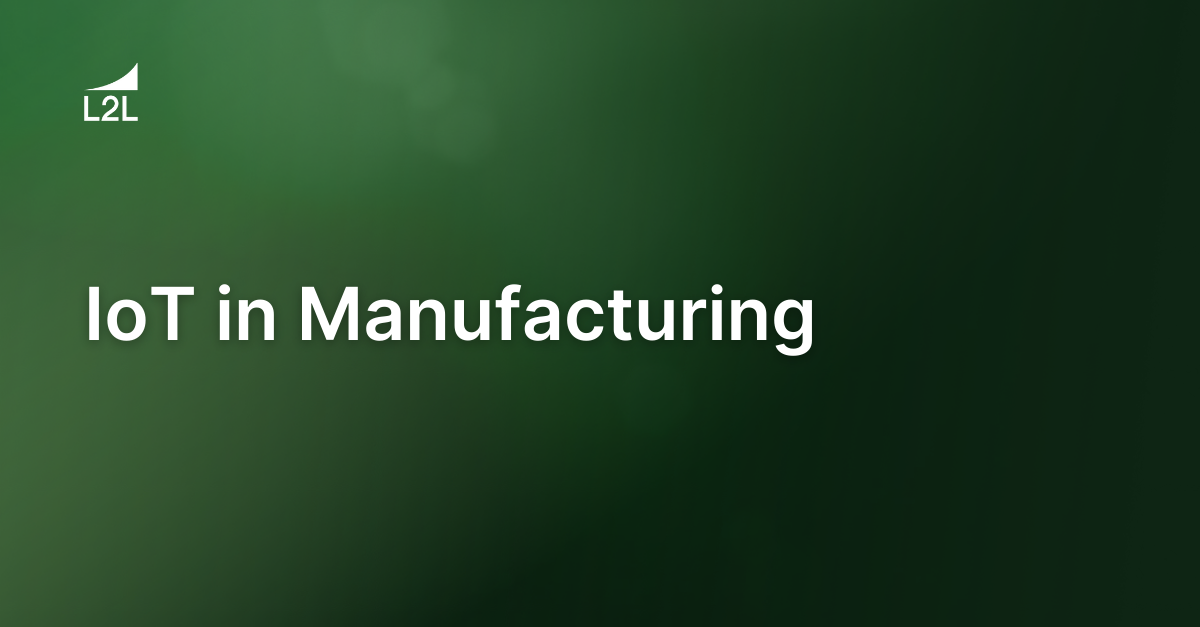
Over the past years, the term IoT has been making its way into our daily lives at a rapid pace. I remember the first time I heard it and how confusing it was. What? We're going to connect "things" to the internet and that's going to be a breakthrough? What "things" are we talking about anyway? I didn't get it.
The Insurgence of IoT
My first real introduction to this concept was when I was looking for an outlet timer for our holiday lighting. Mine stopped working and was a mechanical one that rotated and would connect or disconnect power based on some plastic tabs that you had to pull out or push in. I'm sure most of you remember these.
Well, at this time, my go-to shopping method was to research on Google and Amazon. That's when I learned about smart plugs or WiFi outlets. Not only could these things be programmed to turn off and on at certain times of the day, but they could also be controlled using and app on my smart phone or even by telling my Alexa to do it for me. Wow! This really was a breakthrough. No more manual tabs that I'd have to change with the daylight, or when the power went out.
This is what they were talking about when they mentioned "things." What other things could I connect to help make my life easier? To make a long story short. I now have IoT light switches, a garage door opener, sprinkler system, thermostat, doorbell, security cameras, motion sensors, home audio, etc. My house has gone from fully manual to fully automated in a very short time frame. And, the best thing is that it was easy to do at a relatively inexpensive price tag. I get it now!
IoT in Manufacturing
IoT in Manufacturing is also referred to as IIoT, or the Industrial Internet of things, and its primary focus is to not only connect things to the internet but to drive engagement. Why is this last part – "drive engagement" – so important? Well, because in a manufacturing environment these devices can be used to signal an abnormal condition that will require action to get things back in order.
IoT in Maintenance
So, coming from a manufacturing maintenance and engineering background, this concept of easily automating my home instantly got me thinking about how this could help with predictive maintenance in a manufacturing environment.
What if there were IoT devices that could monitor things like temperature, vibration, machine cycles, voltage, etc.? Well guess what: There are! And the good thing is that they're relatively inexpensive and easy to deploy.
Imagine if a maintenance technician could install an IoT temperature sensor on a machine and configure it to send a notification when the temperature is above or below a certain value. Also, imagine this can be done in minutes with no PLC programming or heavy IT support. That would revolutionize predictive maintenance in the manufacturing world. It would provide a new level of predictive maintenance tools. I call this Predictive Maintenance IoT.
IoT in Quality
Just like Predictive Maintenance IoT, quality could benefit by using IoT to easily monitor and signal process control failures. IoT enabled calibration and measuring devices could signal when calibration due or out of specification.
IoT and Lean Production
Lean manufacturing is all about making problems visible so they can be solved quickly. What better way to make problems more visible along with automated notifications than IoT? Also what better way to easily measure things like productivity or OEE than placing a few IoT sensors in the proper locations to monitor product and material flow.
IoT and Cloud Based Software
Unfortunately, there really aren't many apps or software solutions that are made for this type of application and/or are considered to be secure enough to get past the company's IT departments requirements. That was the one thing that I didn't mention about my home IoT journey. There are many applications and standards that made it extremely convenient for home use that aren't made for manufacturing. But, that is changing and changing quickly.
With the increase of cloud based manufacturing software solutions like L2L's LES solution, this is quickly becoming a reality. We have customers that can now easily connect "things" on their production floor to our solution to track conditions and notify them before there is a problem. Remember this is without having to go through the painful change management process of hard-wiring and rewriting PLC code.
The Future of IoT Manufacturing
This type of thinking has really made me start to realize that the days of difficult, expensive, heavy programming, consulting and hardware projects in manufacturing will be coming to an end very soon. Manufacturers have been slower than all other industries to adapt new technologies but this one is something that cannot be ignored.
I also believe that manufacturing IT departments can be the leaders in this new revolution. They just need to look at it as a good thing instead of a threat. Sure, there are concerns, but these concerns can and will be addressed just like they have been in other industries. The fact is that manufacturing is changing quickly and will require new ways of thinking, new talents and skills – which is a good thing for everyone in manufacturing. Just like Amazon has changed retail shopping, this will change manufacturing from this day forward. Don't be the next Blockbuster video store and ignore the inevitable. IoT and the cloud are here to stay!
"Neither RedBox nor Netflix are even on the radar screen in terms of competition," Blockbuster CEO Jim Keyes
If you'd like to learn more about how our LES integrates with IoT devices, visit our Integration page.
Revisions
Original version: 16 March 2020
Written by: Bob Argyle
Reviewed by: Daan Assen
Please read our editorial process for more information
Related Posts
Subscribe to Our Blog
We won't spam you, we promise. Only informative stuff about manufacturing, that's all.