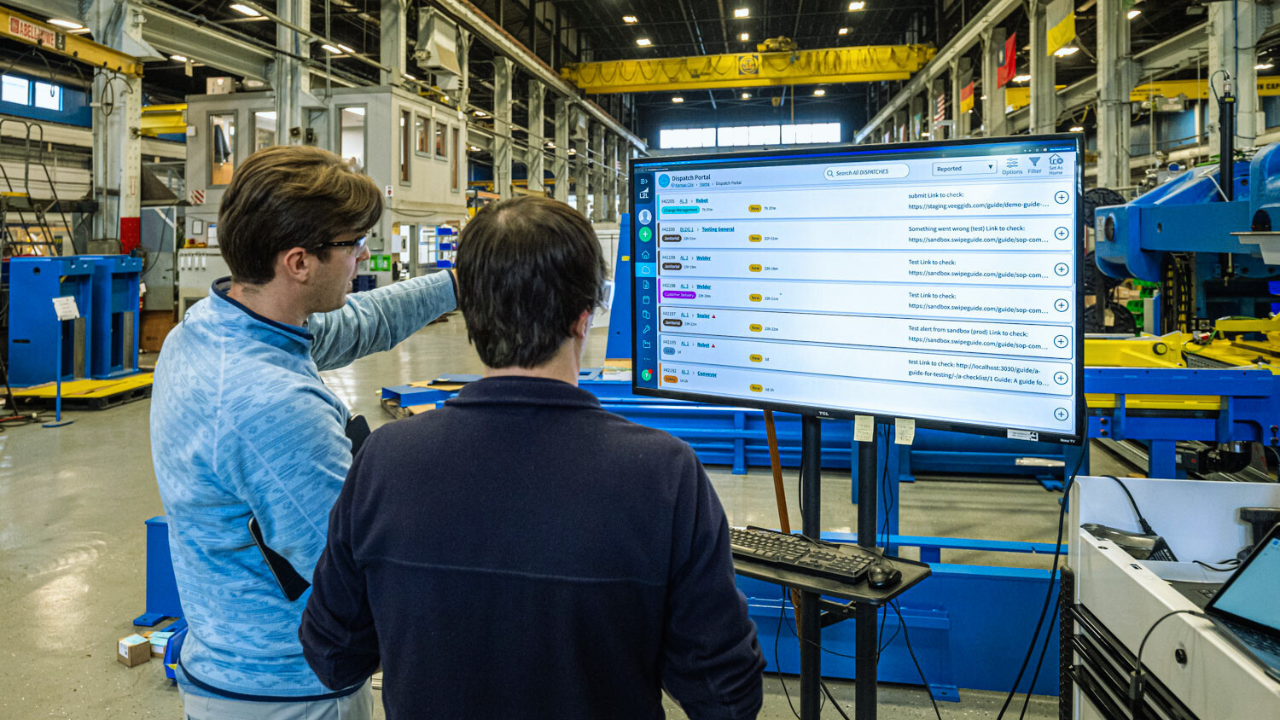
“MES” and “ERP” are some of the most common acronyms you’ll hear in the manufacturing industry.
MES stands for Manufacturing Execution System, a computerized system that monitors and documents the transformation of raw materials into finished products. ERP stands for Enterprise Resource Planning. This system has a much broader scope than MES; it functions as an integrated, typically software-based management system for an organization’s integral business processes.
In this article, we'll break down the differences and similarities between ERP and MES, their unique roles in a manufacturing facility, and what you need to know about MES and ERP integration.
MES vs ERP: The big picture
Although MES and ERP are essential to keeping plants running smoothly, they’re little more than acronyms to many. But the truth is that each system plays a unique role in maintaining a functioning manufacturing facility. Understanding the difference between the two is crucial for maximizing their value in your plant.
MES and ERP are complementary systems whose functions can slightly overlap. However, an MES is specifically designed to manage production and inventory processes. An ERP system manages enterprise data across multiple departments, but it lacks the manufacturing-specific capabilities of an MES.
Differences and similarities between MES and ERP.
Before we dive into their differences, let’s briefly define what each system is and what it does.
What is an ERP system?
ERP is somewhat like the brain of your factory. It ties together many of the other business processes within the plant and enables the flow of information between them. It's the financial engine for the facility and includes:
-
Accounts payable, receivables, payments, and collections
-
Purchasing of raw components to build the product, including the consumption of the components for the reordering of those parts, and tracking the delivery of the product
-
Supply chain management, inventory management, warehousing, and storage locations
-
Managing sales of product orders, including when to build and ship those orders
-
Production planning and Bill of Materials (BOMs) for production builds
-
Managing human resources for payroll, benefits, and hiring
ERP software is very good at purchasing, planning, and managing resources within the plant — and paying the bills that keep the lights on. It also stores data and enables reporting on key financial KPIs so management can make decisions on where to improve.
While these are the primary functions of an ERP system, you can typically add on other modules, depending on what your ERP provider offers. For example, some organizations choose to add Customer Relationship Management (CRM) functionalities to their ERP systems to further enable end-to-end enterprise integration. Other common modules include enterprise performance management, risk management, and ERP analytics.
In short, the available modules vary by ERP system. However, ERP integrates with many other manufacturing systems, including MES and connected workforce platforms.
Bonus Guide! What makes a connected workforce, well, "connected"? Grab your FREE eBook to find out:
What is an MES?
MES is used to extract data from shop floor production processes and machines, and it sends the data to other systems and servers for storage.
Many companies like to custom-build their MES systems so they can track production processes in greater detail. The main points you need to know about the function and benefits of an MES are:
-
Part traceability and the genealogy of the components that go into making the product. Depending on the type of product you make, you may not need this level of detail. For industries that do require it and will pay for it, traceability and genealogy are essential parts of an MES.
-
Recipe management functionality that sets up the machine controls needed to run the product. An example of this is going to your microwave and pushing the popcorn button. The microwave has been pre-programmed for the amount of time and heat needed to make a perfect bag of popcorn.
-
Machine process controls to monitor any change in the process and store the values for reporting. Changes can be captured using the pressures, flows, torque values, and many other variables to help maintain the quality of the product.
The main differences between MES and ERP
MES and ERP are distinct systems with unique purposes, but there is some overlap.
Now that we’ve defined the primary functions of ERP vs MES, let’s take a closer look at the critical differences between the two — and the unique advantages they offer manufacturers:
-
Focus areas: Whereas MES focuses on the optimization of manufacturing processes and operations on the shop floor, ERP focuses on broader business processes beyond manufacturing, including finance, HR, procurement, and sales.
-
Strategic vs. tactical: MES is tactical, focusing on day-to-day operations and immediate improvements in manufacturing processes. ERP is strategic, aimed at long-term business planning, resource management, and organizational growth.
-
Integration with other systems: MES is designed to integrate closely with shop floor equipment and processes, enhancing operational efficiency and product quality. ERP integrates with a wide range of business processes and systems across the organization, facilitating information flow between departments.
-
Data management and analysis capabilities: MES handles real-time data collection and analysis from the production floor for immediate decision-making and process adjustments. ERP manages data from across the organization to provide comprehensive insights, financial reports, and strategic planning tools.
-
Implementation complexities and time frames: MES implementation focuses on operational technology and may require customization to fit specific manufacturing processes. ERP implementation is a major enterprise-wide project that often requires significant time and resources to align with organizational processes.
-
User interface and accessibility: MES typically provides interfaces designed for shop floor employees, emphasizing usability and access to real-time operational data. ERP interfaces are designed for a wide range of users across the organization, with features supporting diverse business functions.
-
Operational impact: MES directly impacts production efficiency, product quality, and compliance by providing detailed control and monitoring capabilities. ERP impacts organizational efficiency by optimizing resource allocation, improving financial management, and enhancing customer satisfaction.
Should you integrate your ERP and MES?
These two manufacturing systems share many similarities in how they track the flow of the product through the plant. Most companies need a blend of the two to maximize plant efficiency. They need to be able to talk to each other, collect data, and present information to decision-makers.
What your MES and ERP systems should include
When selecting an MES for your plant, it’s important to prioritize factors that maximize production efficiency and quality. Key considerations include:
- The system's ability to integrate with existing hardware and software
- Real-time data tracking and analysis capabilities,
- Scalability and flexibility
- The ability to support industry-specific regulations and standards
For an ERP system, essential considerations include its support for all business processes, seamless integration with operational technologies, customization options, and scalability. Your ERP selection should also factor in the provider's reliability, support services, and the system's user-friendliness to ensure effective implementation and usage.
Do you need both?
Most plants rely on both MES and ERP to keep production running smoothly. But due to these systems’ overlapping functionalities, you may be questioning whether you need both to run a successful manufacturing operation.
It’s true that some manufacturers can use either system exclusively, particularly ERP. However, today’s production challenges increasingly require the capabilities of an MES to solve.
MES can, for instance, analyze shop floor data at a level of granularity that most ERP systems can’t. MES systems can integrate with shop floor applications, such as Internet of Things (IoT) devices and sensors, whereas ERP primarily integrates with other software systems.
In summary, not every manufacturer needs an MES. However, most find that having integrated MES and ERP systems is important for sustained growth and profitability.
Closing thoughts on the ERP vs MES debate
If you're thinking about making a change or even going in a new direction with these systems, make sure you know what you need first. Start small and always use an evolutionary approach. It's always better to start simple than to use the disruptive rip-and-replace strategy, which will usually fail.
Not every plant requires a full MES, which can be costly to purchase and deploy. In fact, many manufacturers can use a connected workforce platform like L2L as an MES alternative. Not only is L2L less expensive and faster to deploy, but it also offers benefits that MES systems lack, such as real-time abnormality detection and greater flexibility. Additionally, it integrates seamlessly with most ERP systems.
L2L can also coexist with MES solutions. Manufacturers that need an MES—like an auto parts plant requiring advanced track-and-trace functionality—can use L2L to extend the value of their MES and ERP.
See for yourself how a connected workforce platform interacts with major manufacturing software. Take L2L’s FREE Interactive Product Tour today!
Revisions
Original version: 14 February 2024
Written by: Evelyn DuJack
Reviewed by: Daan Assen
Please read our editorial process for more information
Related Posts
Subscribe to Our Blog
We won't spam you, we promise. Only informative stuff about manufacturing, that's all.