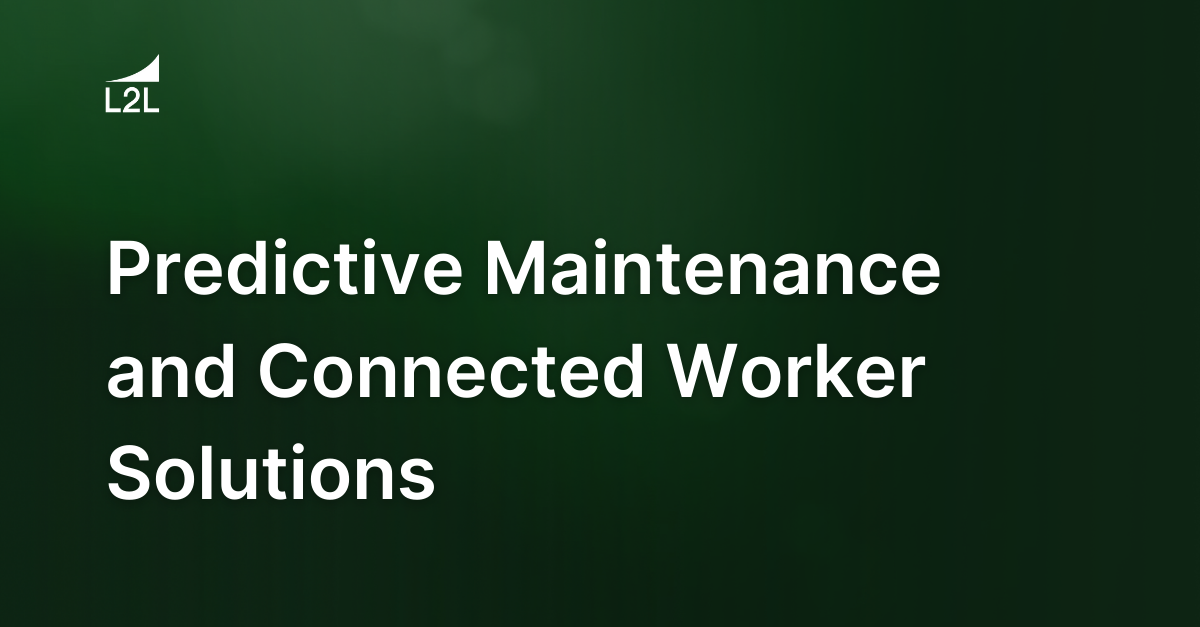
Predictive maintenance is the endlessly innovative, spry entrepreneurial cousin of reactive and preventive maintenance. Reactive maintenance means waiting for your equipment to break, leading to longer unplanned downtime and costlier asset upkeep. Preventive maintenance means scheduled plans for work even if the equipment doesn’t show any overt signs of wear. Then you’ve got predictive maintenance services, which answers the question, “What if we had a smart, artificial intelligence-based way to tell when equipment needed repairs?”
A refresher on predictive maintenance
Predictive maintenance is what the T-1000 should have had in Terminator 2: Judgment Day. In the film, the T-1000 can repair any part of its body after it breaks — this is an example of reactive maintenance. But it takes some time for the machine to repair itself and this slows it down a lot, even by James Cameron standards. This unplanned downtime means the cybernetic organism can’t meet its quota of eliminating one John Connor.
If Skynet were a truly intelligent AI, it could have equipped the T-1000 with predictive maintenance. This would allow it to predict when a part of itself was breaking down through condition monitoring and machine learning, notifying the system when it needed repairs before it actually stopped functioning.
Granted, this would have made the T-1000 way too strong and the movie would have ended too soon with the bad guys winning and I would have asked for my money back. But from a manufacturing standpoint, predictive maintenance could have given the T-1000 a chance — the same chance it could give to your manufacturing plant.
When I look out the window, I don’t see any Terminators, so Skynet hasn’t taken over yet. That’s probably because it wasn’t smart enough to implement predictive maintenance on an extremely high-value machine. Don’t make the same mistake Skynet did.
Let’s break it down into simpler terms: You have equipment. Equipment requires maintenance costs to stay in working condition. You could wait for it to stop working with total equipment failure and then fix it with reactive maintenance. But this means unplanned downtime and higher maintenance costs, and that leads to missed quotas during your manufacturing cycles.
If you had predictive maintenance software, on the other hand, you would have an idea of when your equipment needed upkeep before it breaks down. That means you can avoid downtime and reduce overall maintenance costs while at the same time boosting your productivity.
How preventive maintenance differs from predictive maintenance
The simplest way to put it is that preventative maintenance works on a schedule, whereas predictive maintenance works through artificial intelligence and smart software that can detect when upkeep is required.
There are two kinds of preventative maintenance:
- Usage-based preventative maintenance determines its maintenance cycles by how many production cycles the asset has gone through. After a certain number of cycles, the equipment undergoes upkeep.
- Time-based preventative maintenance is dictated by the number of hours an asset has been in use. Repairs begin once a certain period of time has passed.
Sounds simple on paper, right? To an extent, it is. But to quote the beginning of every infomercial ever, there must be a better way. That’s where predictive maintenance comes in.
A predictive maintenance program isn’t something that can be done with just a pen and paper. In fact, predictive maintenance aims to do away with the pen and paper completely in favor of a software and machine learning approach.
Implementing predictive maintenance means for AI to monitor the individual parts of your equipment for wear and tear and notify you when upkeep is warranted. With this method, you’re not using a schedule, nor are you simply waiting for it to break as you would with reactive maintenance.
Instead, you will know precisely when repairs are needed because your solution is constantly staring at every core part of your equipment, meticulously looking for signs of trouble, and notifying you at the first trace.
In practice, this can significantly reduce the need for unplanned maintenance, as you’ll always know when parts need to be repaired or replaced. Ultimately, this means fewer worries about meeting your production numbers as a consequence of key equipment in your manufacturing process breaking down. It’s the definition of peace of mind for the corporate employee overseeing the production system.
Predictive maintenance challenges
Sure, a predictive maintenance program sounds like something everyone should have, even a Terminator. But there are some challenges involved in integrating such a solution, such as:
- Costly upfront price. To have predictive maintenance, you need sophisticated artificial intelligence equipped with predictive analytics installed into your equipment. This can take time, not to mention training and a significant amount of money to get running.
- Expertise. You’ll need people monitoring the software that’s overseeing your equipment. The software they’ll be using requires a special kind of savvy. Expect there to be an education process for your employees.
- Cost-inefficient for low-value assets. Using a predictive maintenance solution on equipment that doesn’t cost much to replace is probably not going to be worth the effort, time, or money it would take to implement it.
To get the most from predictive maintenance software, it’s better to install it in critical, high-value assets that have the most to lose from unplanned downtime and equipment failure. In addition, you won’t get much out of it if the item it’s installed on isn’t suitable. This might be the case if you’re trying to monitor a large fan like the kind you’d find in curing units, for example, which would probably be better off with a preventative maintenance program — because the comparably higher cost of predictive maintenance wouldn’t be practical given the relatively low cost of the item.
If you’re going to have downtime, the only kind you should be happy about is planned downtime. To make the most of it, you can use predictive maintenance to identify which of your equipment and assets could use repairs to minimize the amount of unplanned downtime your manufacturing process needs to undergo through condition based maintenance.
The final product is an optimized production run
Production runs are when your manufacturing process gets to come together. All the individual parts are in place, everything’s functioning at full capacity and everyone’s happy. No one’s worrying about unplanned downtime — instead, they’re looking forward to the weekend. That’s why predictive maintenance can also help you better schedule production runs: You’ll plan them for times when all the different assets involved in the manufacturing process are in tip-top shape and the least likely to require maintenance before the operation’s complete.
How connected worker solutions make predictive maintenance better
Let’s talk about connected worker solutions and how they integrate with predictive maintenance. We’ve gone over the fact that predictive maintenance requires a lot of training and sophisticated artificial intelligence, but that just leads to more skilled employees who know what they’re doing.
Consider what connected worker solutions typically consist of: Augmented reality, headsets and employees that can perform complicated maintenance tasks without necessarily needing years of experience to do it. With predictive maintenance, all of that comes together so your workers are able to understand the condition monitoring and predictive analytics that make up the solution. This means that you don’t necessarily need a team of expensive specialists to maintain your predictive maintenance software — instead, your workers are trained to handle it themselves.
How to get started with worker/machine connectivity solutions
It takes some planning to achieve optimum worker/machine connectivity, so here are a few steps you should follow:
- Develop a strategy. A connected worker solution needs to be a part of a larger operation that brings together technology and some sort of manufacturing platform.
- Get your tools together. All projects like these require, at the very least, mobile devices and cloud connectivity. But you might also want enterprise resource planning and manufacturing execution systems as part of the big picture — or, better yet, one platform that brings them all together. This ensures an efficient, premium connectivity solution that demonstrates you have plans for the future.
- Develop a timetable. Traditional enterprise software can take months to years to set up, but spending the time and resources on a worker/machine connectivity project means you can develop a solution within weeks.
- Speak to your stakeholders. Frontline workers and corporate employees can both benefit from a worker/machine connectivity solution. Explain the ROI particulars to your stakeholders so they understand what this shiny new piece of technology can do for your operation.
Predictive maintenance makes it so you might never have to worry about unplanned downtime, ever again
Hopefully, all of this has demonstrated precisely what predictive maintenance is, how it differs from other types of maintenance, the key benefits of predictive maintenance, the challenges involved in implementing it and how it ties into connected worker solutions. With this, you should be prepared to implement a predictive maintenance solution in your own manufacturing process, all with the goal of avoiding failure and meeting your production goals.
That doesn’t mean predictive maintenance is appropriate for every asset you have, but that’s okay, because it doesn’t have to be. In fact, it should be combined with other types of maintenance depending on the value of the asset in your manufacturing process. Predictive maintenance is a smart process, and for you to smartly integrate it, you need to know which of your assets is worth utilizing the software. It might take a bit of planning and training, but the ROI can be very well worth it — and your production process could be more advanced than Skynet.
Want to see how it all comes together? Contact us today to watch our platform make predictive maintenance a breeze.
Revisions
Original version: 1 November 2022
Written by: Eric Whitley
Reviewed by: Daan Assen
Please read our editorial process for more information
Related Posts
Subscribe to Our Blog
We won't spam you, we promise. Only informative stuff about manufacturing, that's all.