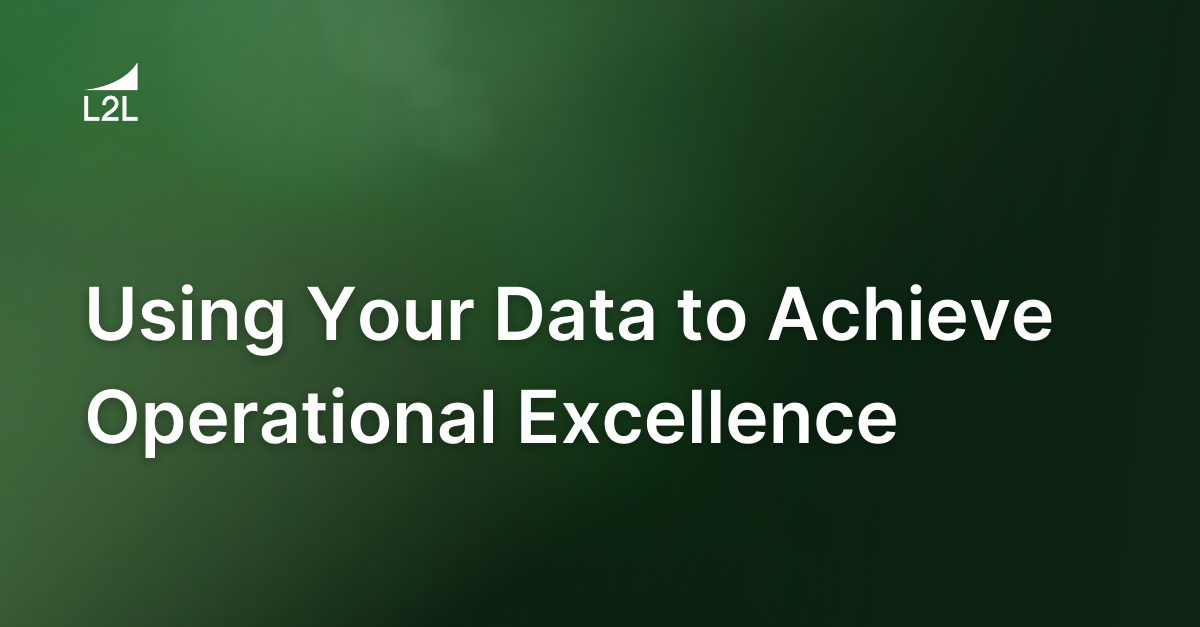
"Operational excellence" is an industry buzzword that gets tossed into the mix with other words like "lean" and "continuous improvement." But while many people recognize operational excellence as a good thing, its definition — along with its value to an organization — remains unclear. But with businesses experiencing dramatic upheaval in demand and resourcing, executing with operational excellence is more important for company survival than ever. However, most businesses already have a roadmap to achieve operational excellence: their data.
What Is Operational Excellence?
Contrary to popular belief, operational excellence isn't a process or practice like continuous improvement. In scholastic terms, operational excellence is a workplace philosophy that emphasizes customer needs and empowers employees to act in the interest of those needs to continuously improve the organization. More simply, operational excellence is a state where each employee understands how value flows to the customer and engages in correcting that flow when it fails or falls short.
The implication of operational excellence is enormous. The business’s processes now self-correct as frontline personnel observe issues and address them in real time. Management, freed from firefighting, is now able to turn its attention toward innovation and enhancing the business.
How Does Data Help Achieve Operational Excellence?
Data generation, particularly in the past few years, has been increasing exponentially. While people remain the primary sources, industry trends toward digital transformations and IoT are vastly expanding the information businesses have at their disposal. Data on its own does not add value, but as the basis for decision-making and process visualization, it can be amazingly powerful. Early adopters have already begun to recognize and realize this competitive edge.
In the world of operational excellence, data is an invaluable tool to foster employee ownership of processes. Data output from lines and processes combine into holistic representations of plant systems, providing feedback on events as they occur. When individuals across the organization see the effects of their workflows and output on their organization’s goals, they readily engage in problem-solving. As a result, frontline workers feel a sense of ownership over their roles, where they leverage data to identify roadblocks, remove obstacles, and suggest and design improvements.
What to Look for in Data to Drive Operational Excellence
Achieving operational excellence with data requires determining which data points provide process insights that align with business strategies. As the saying goes, "What gets measured gets managed and improves." The growth in digital systems throughout business departments like Finance, Purchasing, and Operations provides a wealth of information that can inform administrative calls.
While this volume of data allows the process interconnections and dependencies within a firm to be more accurately depicted, it can also inhibit decision-making if the site does not distinguish its KPIs from the rest of its numbers and measurables. Defining KPIs not only helps a business fulfill customers’ needs, but it also highlights which of their site metrics are levers to improvement.
The data that drives operational excellence, depicted by KPIs, should encourage a shift from a reactive response to a proactive approach to issue resolution. Leading indicators are analytics that look ahead in the process to predict probable outcomes and prescribe corrections. Compared to lagging indicators, or data points that show outcomes, leading indicators represent the process inputs that lead to those outcomes. Historical data can help identify leading indicators in a system by correlating variations of input factors to outputs. For example, the number of near-miss safety events that occurred may be a leading indicator of OSHA recordable events.
How Do You Share Operational Data?
As demonstrated, data that is accessible across an organization is a key component to building operational excellence. But what's the best way to share such information throughout the business? Fortunately, there are many tools available to help employees visualize where issues should be addressed and in what order.
Traditional methods of data display are primarily manual, like using whiteboards to document and broadcast periodic throughput, stacking Kanban cards to indicate demand volume, and switching on an andon light to indicate when equipment is down. Although somewhat outdated, these tools require employees to actively engage with the data. Leveraging these methods when beginning your operational excellence journey can be a way to cultivate process ownership and accountability within your teams.
Today’s efforts toward IoT and automation, which create data-rich environments, are also coupled with digital transformations. Through these efforts, a tapestry of inputs and data points are woven together to virtually depict a factory with dashboards representing the critical measures across processes. This technological approach ensures real-time information capture and sharing to promote issue resolution and innovation. Furthermore, a digital factory allows individuals from across the shop floor to monitor and manage processes remotely, removing physical barriers to support and engaging a broader team in ensuring operational excellence.
Operational excellence, the ability to execute strategy more effectively, more consistently, and more reliably than the competition, can seem like an unobtainable company goal. But by leveraging its existing information assets, a company can build the right management infrastructure and instill a mindset of operational excellence in employees.
See how L2L can put your data to use in achieving operational excellence. Book a demo with us today!
Revisions
Original version: 9 June 2020
Written by: Amy Mele
Reviewed by: Daan Assen
Please read our editorial process for more information
Related Posts
Subscribe to Our Blog
We won't spam you, we promise. Only informative stuff about manufacturing, that's all.