
L2L
A Guide to
Enterprise Asset Management Software
Having assets is one thing. Managing them is another.
To get the most out of those assets you’ve worked so hard to acquire and maintain, you need to understand at any moment how they’re performing. Of course, that’s easier said than done, especially when assets differ in type and may be distributed between multiple factories. Efficiency, visibility, downtime reduction — these are just a few things on the to-do list. Without the right tools at your disposal, they could start to seem impossible. What you need is a set of solutions that can actually make a difference.
The good news is that those solutions are within reach. It’s all about enterprise asset management, or EAM — and that’s what we’re all about, too.
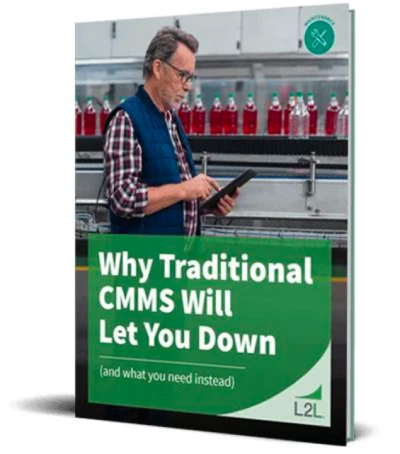
Ready to Get Started? Request a Free Consultation.
What is EAM? In simple terms, it’s your toolbelt for bringing together all the far-flung, disparate elements of your factories in support of one thing: asset performance. It’s somewhat like drawing lines between distant stars to create one cohesive constellation — except the stakes are a whole lot higher.
Done poorly, EAM software can be cumbersome for maintenance teams and require years to implement. However, if you put the right tools instead of more tools in your belt, you’ll start to see how enterprise asset management can be at the heart of manufacturing success. Enterprise asset management enables:
-
Visibility into asset performance analytics
-
Centralized asset data storage
-
Improved data mobility
-
Clearer, more effective communication
-
Simplified resource management
-
Tools for real-time problem-solving
So, what are these “right tools” that can make such a difference? Simple: Modern EAM software.
To better understand what enterprise asset management software is, it’s often helpful to review what it isn’t. One solution that often comes up in conversations about EAM is CMMS. Although many use the terms interchangeably, there is an important distinction.
Let’s compare:
CMMS
Naturally, a computerized maintenance management system is all about maintenance. It’s right there in the name.
As manufacturers know, CMMS is a vital part of organizing, automating, and simplifying elements like work orders and preventive maintenance schedules. In many ways, its focus is on the physical — what steps to take, who needs to perform which asset maintenance task, how many machines are in need of service, and how best to schedule that downtime. Yes, it’s technically a form of asset management, but notice the lack of the word enterprise.
EAM software
EAM software is like CMMS on a much grander, more intricate scale — hence the enterprise.
While maintenance is certainly an important part of extending an asset’s lifecycle or ensuring maximum ROI, it’s only one piece of the puzzle. Enterprise asset management includes connecting to other systems such as ERP or MES and data-gathering techniques beyond what is offered by traditional CMMS. It also engages with each asset beyond its physical attributes, providing data, insights, and performance analytics that can be used to make informed real-time decisions on where resources should be focused.
An EAM system, therefore, should encompass CMMS functionality in a way that enables not just machine performance improvement, but plant and enterprise-wide improvements in efficiency and mitigation of the issues that threaten to disrupt production performance.
Enterprise asset management in manufacturing
This is where enterprise asset management really gets the spotlight: in the day-to-day operations of manufacturing organizations.
To deliver ROI, every EAM solution addresses specific areas of the manufacturing workflow. Those areas include:
Asset performance
The goal of enterprise asset management isn’t just to provide visibility into asset performance. It also illuminates clear paths forward, giving you opportunities to utilize gathered data to simplify and improve each step of the asset lifecycle. In many ways, this process is a cycle: You gather data across your inventory, notice a problem, use data to solve it, and then gather more data to analyze the effectiveness of your approach.
Asset reliability
Another necessary element of enterprise asset management is asset reliability and analytics. To eliminate waste from your workflows and your manufacturing organization overall, it’s crucial to understand which assets are delivering ROI and which are draining your resources. It’s even more important to make sure the former stays consistent over time, while closely monitoring the latter for improvements.
Asset tracking
Asset tracking is critical for facility management and inventory management alike. However, with so many moving parts to keep track of, you need to organize and simplify data related to the location of all physical assets.
A solid asset management solution gives you constant visibility into these movements. As employees add updates, make reports, or scan labels, the software allows them to act as your eyes, showing you exactly what’s happening and where.
Facility management
Without sufficient focus on your facilities themselves, all other elements of an enterprise asset management system could fail. That’s because your facilities are the canvas upon which you create your finest work, like creating simpler workflows, reducing the risk of unplanned downtime, or automating your maintenance strategy. When it comes to your properties and buildings, enterprise asset management helps you take the big picture into account so the finer details are easier to control, allowing you to achieve operational excellence while controlling every maintenance cost.
Data analytics
Enterprise asset management is based heavily on data analytics. As you use EAM software across your organization, tracking the asset lifecycle or addressing asset performance issues, the system provides insights into hidden inefficiencies. Naturally, having that information isn’t enough; you also need to be able to analyze and utilize it to formulate targeted solutions to issues that cause downtime or disrupt production in any way. Luckily, modern EAM software solutions provide the framework for that too.
Preventative maintenance and maintenance management
In a final tip of the hat to CMMS, preventive maintenance and maintenance management are also areas of focus for an effective EAM system. Automation helps maintenance improve efficiency rather than creating workflow interruptions, while timely solutions keep small problems from becoming big, expensive ones.
Now that you know what makes EAM software tick, let’s see how all of these details add up to ROI for your manufacturing organization. To do that, we’ll take a look at some data points and details from our eBook, How to Reduce Operational Costs with Modern EAM.
You’ll cut through the chatter
Up to 60% of manufacturing processes are almost or completely unrelated to actually producing products. That means your organization has a variety of potential disruptors to production and a lot of data — or “chatter” — to cut through before you can find what matters most for asset performance, asset reliability, lifecycle analytics, and more. EAM software helps you distinguish between relevant and irrelevant data, reducing waste and your chances of getting a work headache.
You’ll actually use it
When software doesn’t provide value, you’re less interested in using it. When you’re less interested in using it, you stop feeding it the data it needs to provide value. This is what we call “a negative cycle of mediocre data leading to low system use,” and it’s not good news.
Modern EAM software, however, doesn’t have this problem. It provides measurable ROI from day one — plus it’s intuitive, user-friendly, and great at reducing manufacturing frustrations, which means you’ll actually want to use it.
You’ll see problems of all shapes and sizes.
When it comes to asset reliability and facility management, even the smallest issue can have a huge impact when it becomes chronic. If your tools and solutions only allow you to see the big stuff, little problems could slip right under the radar and add up to big costs over time.
Luckily, modern EAM software approaches all potential inefficiencies from an unbiased perspective. While it can differentiate between an emergency and a small-scale issue and direct your attention to the more urgent of the two, it also doesn’t let small chronic issues, like regularly repeated adjustments or fixes, continue to occur and bleed profitability from your organization. In fact often times we find that these seemingly small, chronic issues are by far the more costly problems that need to be solved in factories.
Enterprise asset management, or EAM software, is your toolbelt for addressing asset performance, asset reliability, facility management, data analytics, and more. It’s built on the foundation of accurate frontline asset data and making that data visible to the right people at all levels of your organization. This enterprise-wide view of asset performance puts the enterprise in enterprise asset management.
Today, we’ve covered why efficient enterprise asset management is a big deal for organizations, how it’s shaped by the manufacturing industry, and how it can benefit manufacturers. However, just reading about it isn’t enough.
Want to see for yourself how much difference the right modern EAM software can make? Our ROI calculator has the proof — and we’ve got the solutions. Contact us today!
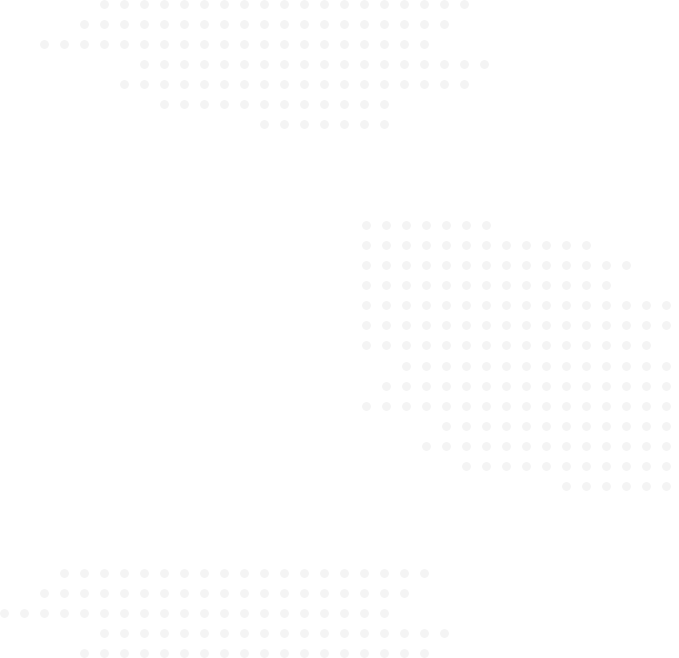
Empower Your Connected Workforce
"L2L is a valuable tool. Having everything at our fingertips creates continuity between maintenance, operators, and leadership."
.png)