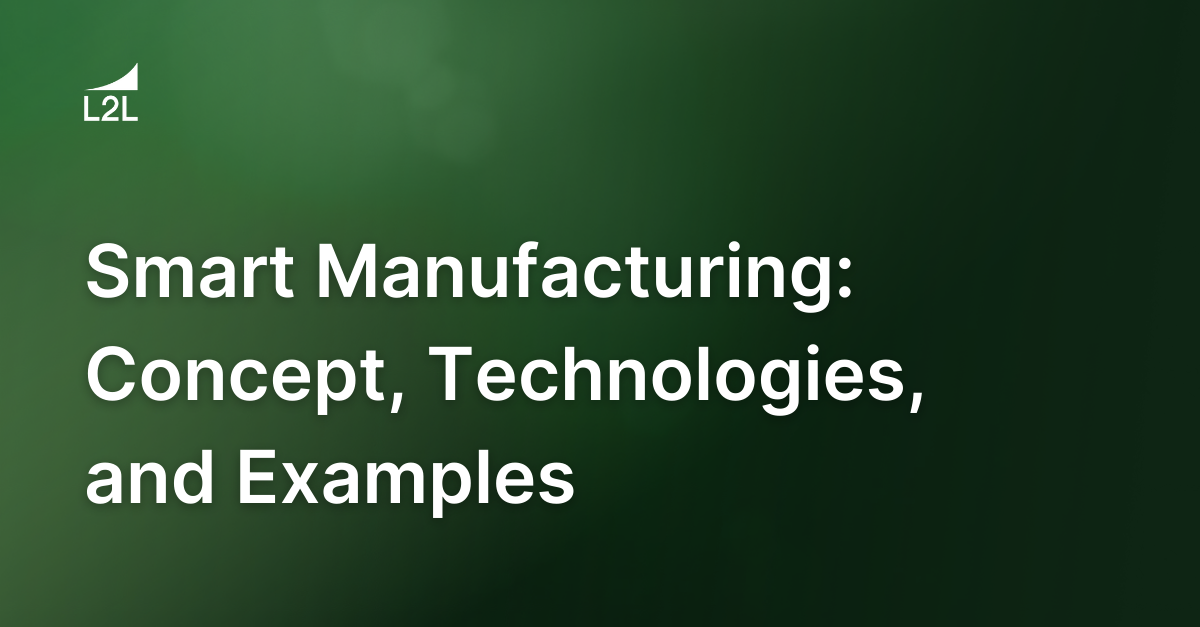
When people think about “smart technology,” they tend to picture consumer electronics like smartphones and smart appliances. But this technology’s applications extend much further in industrial facilities. Smart manufacturing is an approach to manufacturing that combines traditional manufacturing principles with advanced digital technologies to make factories better — much better.
Worldwide adoption of smart factory technology is rapidly accelerating. In fact, the global smart manufacturing market is expected to grow to at least $650 billion by 2029.
Below, we’ll explore the core technologies that make smart manufacturing “smart,” its benefits and challenges, and real-world examples of successful smart factories.
What Is Smart Manufacturing?
Smart manufacturing refers to the use of new technologies like data analytics, the Industrial Internet of Things (IIoT), automation, and cloud computing to make basic manufacturing processes more efficient. By extension, a smart factory is a manufacturing facility that employs smart manufacturing principles.
Smart manufacturing differs from traditional manufacturing in several key ways. While a traditional manufacturing model incorporates digital technology to some extent, most applications are limited to basic automation, rigid systems, and integrations that rely on manual processes and periodic updates.
On the other hand, advanced digital technologies are in a smart factory’s metaphorical DNA. Smart manufacturing infuses innovations like big data, IIoT devices, connected worker platforms, augmented and virtual reality (AR/VR), and robotics into the end-to-end production cycle.
Smart manufacturing benefits everyone inside a plant. Features like real-time machine monitoring enable predictive maintenance, dramatically reducing downtime. Real-time collaboration and centralized knowledge hubs streamline communication and democratize access to important information. Plus, smart factories can integrate with other vendors’ systems and adapt to changing customer needs much faster than traditional factories.
Core Smart Manufacturing Technology
Smart manufacturing facilities can employ a wide range of innovations to accomplish their production goals. However, there is a handful of innovations that we consider core technologies of a digital factory.
These technologies include:
-
Cloud computing: Cloud computing enables access to various computing services over an internet connection. Users can utilize these services on demand, typically paying for only the resources they consume, making it a flexible and cost-effective approach to IT infrastructure.
-
Machine learning: Machine learning (ML) is an AI application that uses insights from factory data to enable predictive maintenance and improve process efficiency. This allows plants to optimize maintenance schedules and resource consumption to save costs and improve quality.
-
Augmented reality: AR, through wearable devices like smart glasses, enhances workers’ functionality in smart factories by providing real-time information overlays. It accelerates maintenance tasks, reduces errors, and improves overall efficiency.
-
Sensors: Sensors in smart factories enable real-time monitoring of production disruptions, detecting abnormalities using various measurements like optical, vibration, and pressure. These IIoT sensor technologies are becoming more affordable and efficient for pragmatic and purposeful deployment.
-
Additive manufacturing: Additive manufacturing (3D printing) builds precise 3D objects using various materials. Industries like automotive, aerospace, and medical devices, often use additive manufacturing to build specialized products.
-
Digital twins: A digital twin is a smart factory application that serves as a virtual replica of a physical factory. Digital representations of products, equipment, and processes allow for data-driven improvements and testing of changes before implementation.
If you want to take a deeper dive into the world of smart manufacturing technology and its applications, check out our in-depth guide to smart factories.
Smart Manufacturing Examples That Prove the Concept
From single-product implementations to entire system overhauls, thousands of factories around the world have seen drastic improvements in efficiency, productivity, profitability, and company culture as a result of digital transformation. Here are two examples of smart manufacturing in action.
Example #1: West Liberty Foods
West Liberty Foods, a food processing company in Iowa, made a massive shift from reactive to proactive maintenance using smart manufacturing technologies. Slow, manual data entry and reporting processes meant technicians took days to respond to maintenance issues. To address these problems, the company implemented L2L’s connected worker platform, enabling real-time machine data analytics and full visibility into shop floor operations.
By digitizing and centralizing maintenance data, operators and maintenance personnel could easily access the right information at the right time, and plant leaders gained visibility into operational availability and asset management.
The company saw an 88.5% improvement in resource utilization and a 10% increase in operational availability — saving $2 million in maintenance costs.
Example #2: John Deere
Landscaping machinery manufacturer John Deere addressed long-standing precision issues in its welding process by using Intel's AI technology. Using the Gas Metal Arc Welding (GMAW) process, a high-volume steel welding method using robotic arms, the company frequently dealt with porosity issues in its products — a problem difficult to solve with its manual defect inspection process.
To tackle this challenge, John Deere implemented an integrated AI solution that utilizes Intel's hardware and software. This quality assurance system employs computer vision and neural network-based inference engines to identify defects in real time during the welding process. When a defect is detected, the system automatically stops the welding process, enabling immediate corrective action.
As a result, the company substantially reduced scrap and rework costs.
Creating a Smart Factory Comes with Some Challenges
The smart manufacturing journey, like any major technological overhaul, comes with challenges you need to overcome as an organization. Below are some of the biggest and most common difficulties manufacturers face when implementing smart factory solutions.
-
Implementation cost: Implementing technology on an organization-wide scale can be expensive. This is why it’s crucial to identify what your factory really needs and calculate both short-term and long-term costs. While smart factory technology requires a substantial financial investment, remember that the cost of resisting digital transformation is much greater in the long run.
-
Integration: Integrating new smart manufacturing technologies with existing systems and infrastructure can be time-consuming and disruptive to operations. Make sure that your new technology is compatible with the systems you plan to keep. Additionally, seamless integration, along with implementation, often requires external expertise — which will come at an additional cost to your business.
-
Technology adoption: With new technology comes new learning curves. For successful digital transformation, you need to make sure your teams receive adequate training on the new tools and systems coming their way. You may need to set aside a portion of your budget for necessary upskilling costs, such as new certifications or help from experts outside of your organization. Seamless adoption only happens when your workers are prepared and understand the new technology’s benefits.
-
Change management: The disruptive nature of change on a mass scale cannot be overstated. Not only does adoption take time and careful planning, but cultural shifts that happen as a result of digital transformation need to be managed as well. It’s important to effectively manage change through asset planning, collecting feedback, monitoring implementation and adoption progress, and making necessary adjustments.
Challenges are a part of every smart manufacturing transformation. However, with strategic implementation planning, proper change management, and expert guidance, navigating these challenges will be much easier.
Remember to lay out clear objectives and KPIs for your smart manufacturing journey so everyone in your plant can visualize progress. Your workforce will thank you when they reap the many benefits later.
Start by Implementing L2L’s Smart Manufacturing System
The process of becoming a smart manufacturing facility is a long journey. For most organizations, it takes years. But the good news is that you don’t need to wait that long to see ROI.
L2L’s connected worker platform accelerates the journey to smart manufacturing by empowering your shop floor to solve problems faster. Our solution helps you maximize the value of your existing systems like MES, CMMS, and ERP while driving continuous improvement across your plant — no rip-and-replace required.
Our smart manufacturing technology democratizes access to real-time data and enables full visibility into shop floor operations, increasing productivity and efficiency across the end-to-end production cycle. Modules such as L2L Production, L2L Dispatch, and L2L Maintenance help you frontline address issues in real-time so they can spend more time producing and less time fixing.
If you’re ready to take the next step toward a smart factory, begin by taking a free smart manufacturing maturity assessment. Then, see L2L’s connected worker technology in action when you request a demo with us today!
Revisions
Original version: 12 September 2023
Written by: Evelyn DuJack
Reviewed by: Daan Assen
Please read our editorial process for more information
Related Posts
Subscribe to Our Blog
We won't spam you, we promise. Only informative stuff about manufacturing, that's all.