Performance Management
Platform
Pricing
Measured Improvement
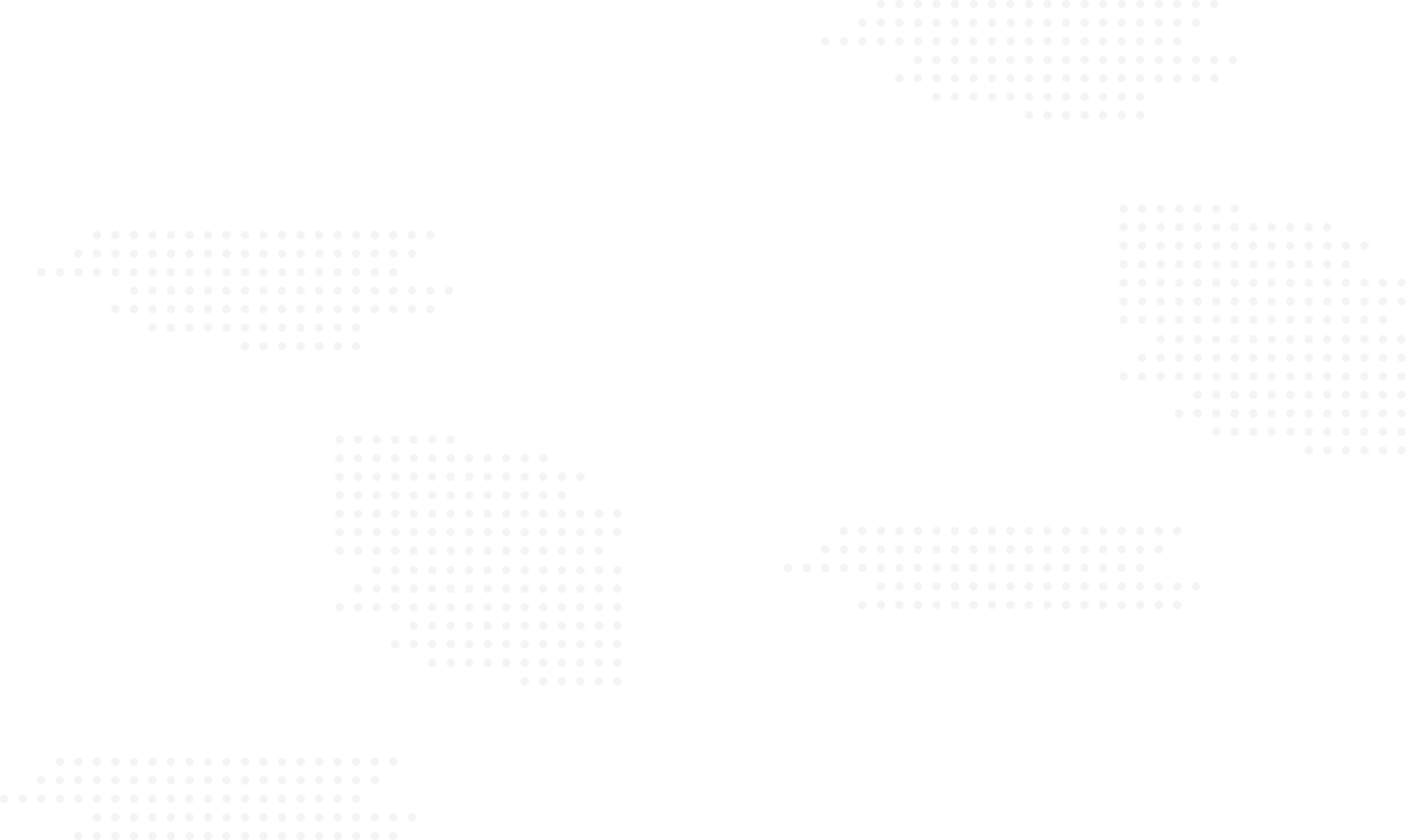
L2L Case Study
Mueller Industries Accelerates Shift to Proactive Maintenance with L2L Studio
Mueller’s reactive maintenance process was an ongoing issue. In the company’s Great Lakes Copper plant, maintenance teams were laden with static preventive maintenance (PM) schedules, manual methods of data management, and a cumbersome spare parts requisition process.
The company wanted to move to a more proactive maintenance approach but lacked the required data visibility to execute this vision.
This was the perfect use case for L2L Studio. Download the case study to learn why!
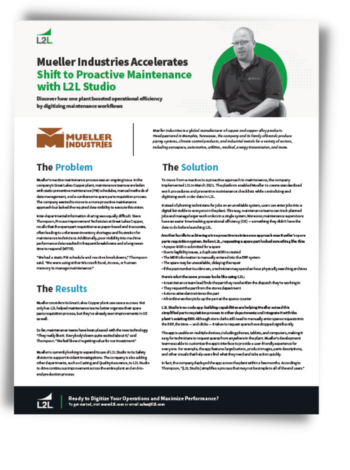
Download the Case Study
L2L has a vast selection of reports for analyzing our site downtime data.
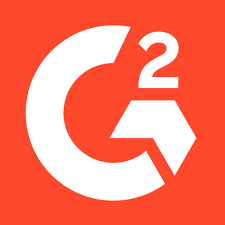
The software is easy to use and yields meaningful data. The data can be extracted and used to show the weaknesses in the workflow.
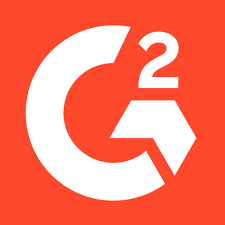
I have really enjoyed working with this system. It is one of the easiest systems I have used. I like the fact that we can bring in new team members and in a really short time.
.png)
We love not having to use paper Kanban cards anymore, plus our internal traceability system is able to talk to L2L tracking our build rates on over 150 production cells.
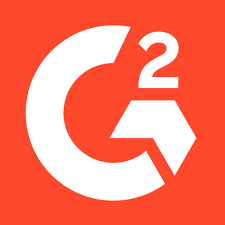
The downtime information that is collected allows the engineering department to isolate major problems and attack the root cause.
.png)
So far, we're seeing success with it. By responding to real time data, we have avoided costly unplanned catastrophic failures. We're happy with the results.
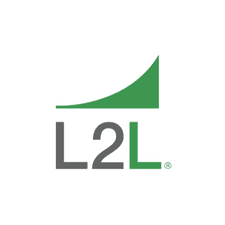
L2L is a gamechanger.
Our Digital Production Platform provides visibility, priority and structure that enables you to solve problems in real-time on the factory floor. Our Digital Production Platform provides visibility, priority and structure that enables you to solve problems in real-time on the factory floor.
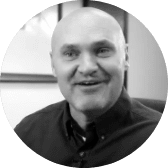
Bryan Crowell
Contact
- Mailing L2L
299 S. Main St
Suite 1300
PMB 96928
Salt Lake City, UT 84111
+1 (877) 225-5201
sales@l2l.com
Integrations
About Us
© 2025 L2L