Boost productivity with AI-powered insights.
L2L’s AI-powered manufacturing intelligence analyzes real-time data from across your plant to detect issues before they escalate and highlight opportunities for continuous improvement. It guides faster, smarter decision-making that drives measurable productivity gains.
Trusted by global manufacturing leaders
Identify downtime instantly
Stop guessing and know exactly when and where issues occur. Our manufacturing intelligence software gives you immediate access to crucial real-time data from across your operations, empowering your teams to respond swiftly and minimize disruptions.
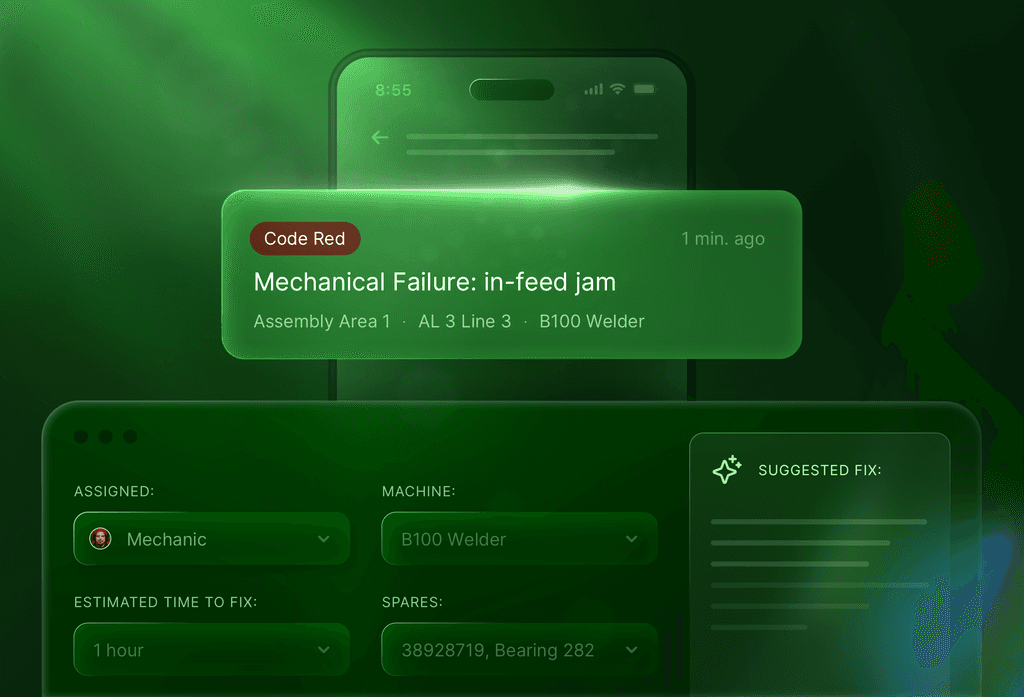
Benchmark, analyze, and act
Benchmark performance against industry standards and track the impact of your improvement initiatives with manufacturing intelligence software. L2L’s reports empower you to adjust strategies, address bottlenecks, and reduce work order response times based on current data.
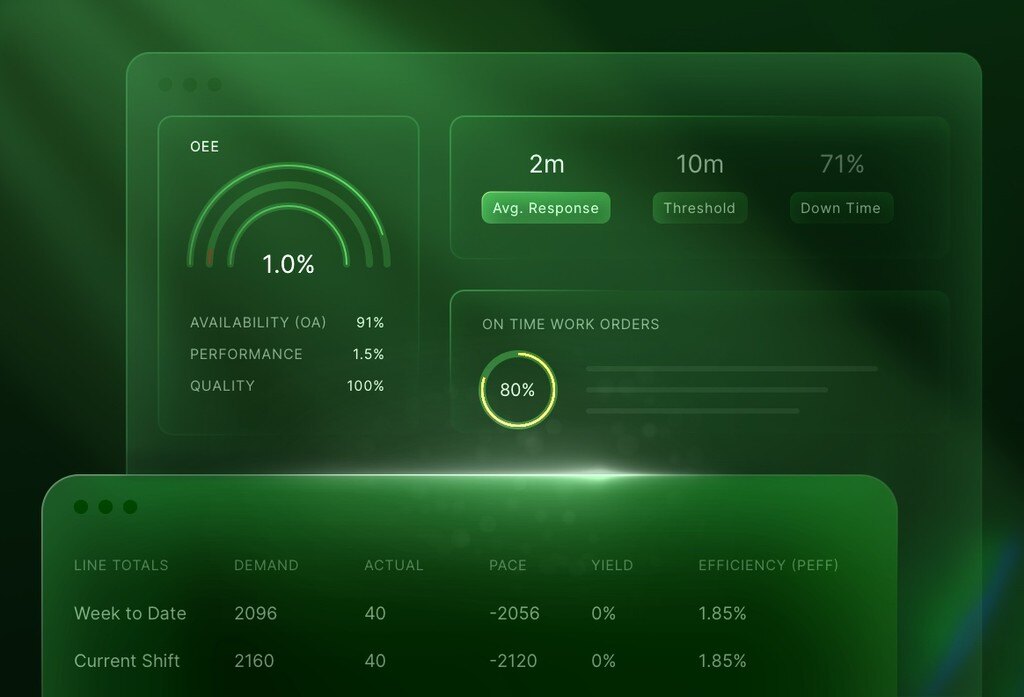
Insights within your workflow
Our intelligent tools don't just present data. They provide guidance, insights, and suggestions to help you make smarter decisions. Get immediate answers to questions, receive data-driven recommendations for probable spare parts, and use historical data to identify root causes and prevent issues from recurring.
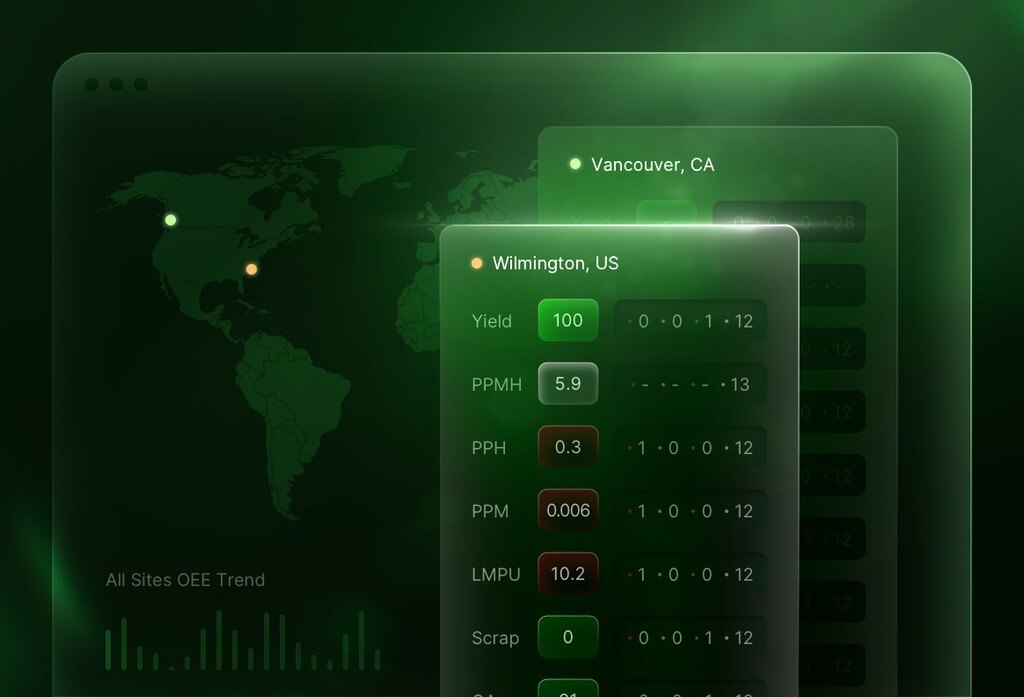
Smarter and faster problem-solving with AI
Guidance, insights, and suggestions.
- L2L Assist: Receive immediate answers to questions around procedures, standard work, locations, and spare parts utilizing documentation in your L2L site.
- Suggested spare parts and fixes: Data-driven recommendations for probable spare parts and solutions based on machine, station, and relevant operational variables.
- Digital documentation: Upload static PDF documentation and watch as L2L instantly transcribes it into dynamic, immediately usable checklists.
- Root cause identification: Identify root causes based on historical data and make sure they never happen again.
- AI-powered SOP creation: Create and transform your digital work instructions, checklists, and SOPs within minutes.
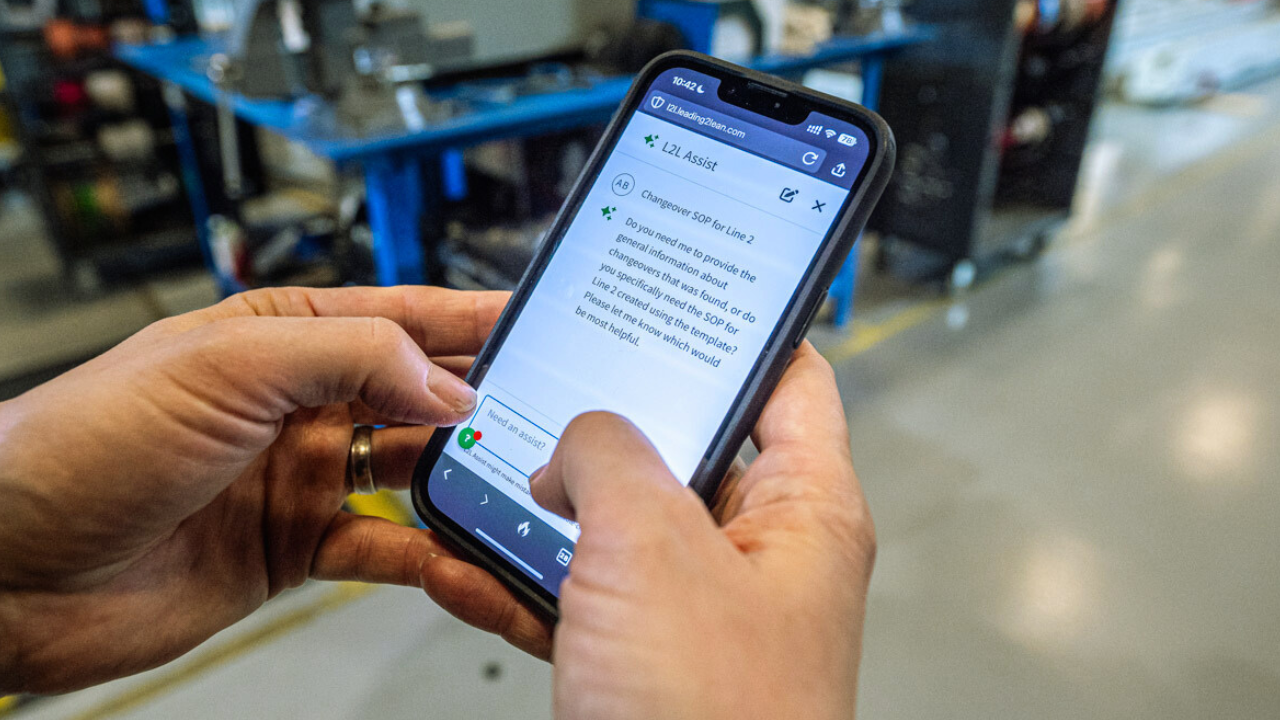
See it in action!
Analytics that have your back
Make informed decisions, every time. Intuitive dashboards and cross-site data consolidation help you spot downtime trends, pinpoint problem areas, and assess the impact of maintenance initiatives.
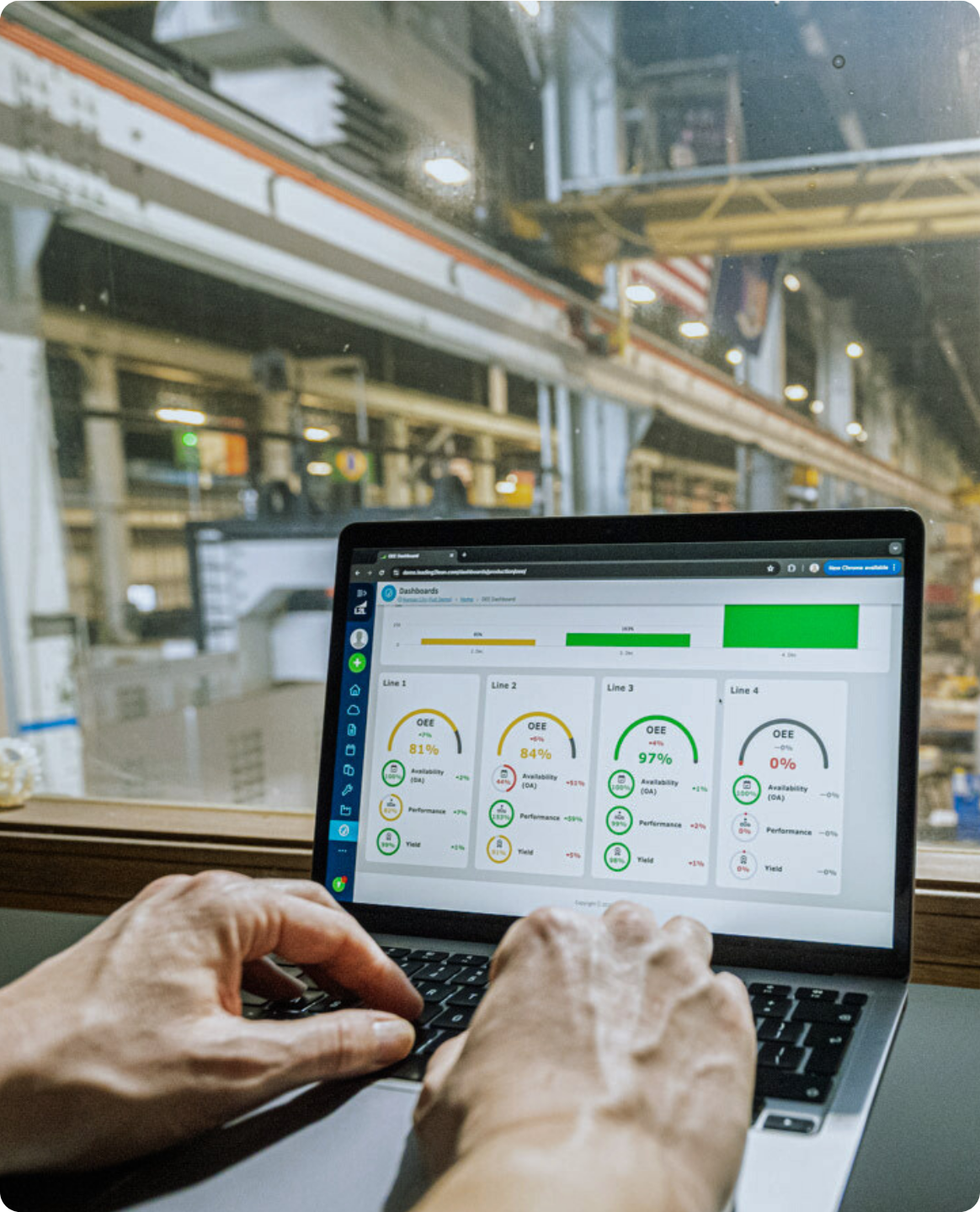
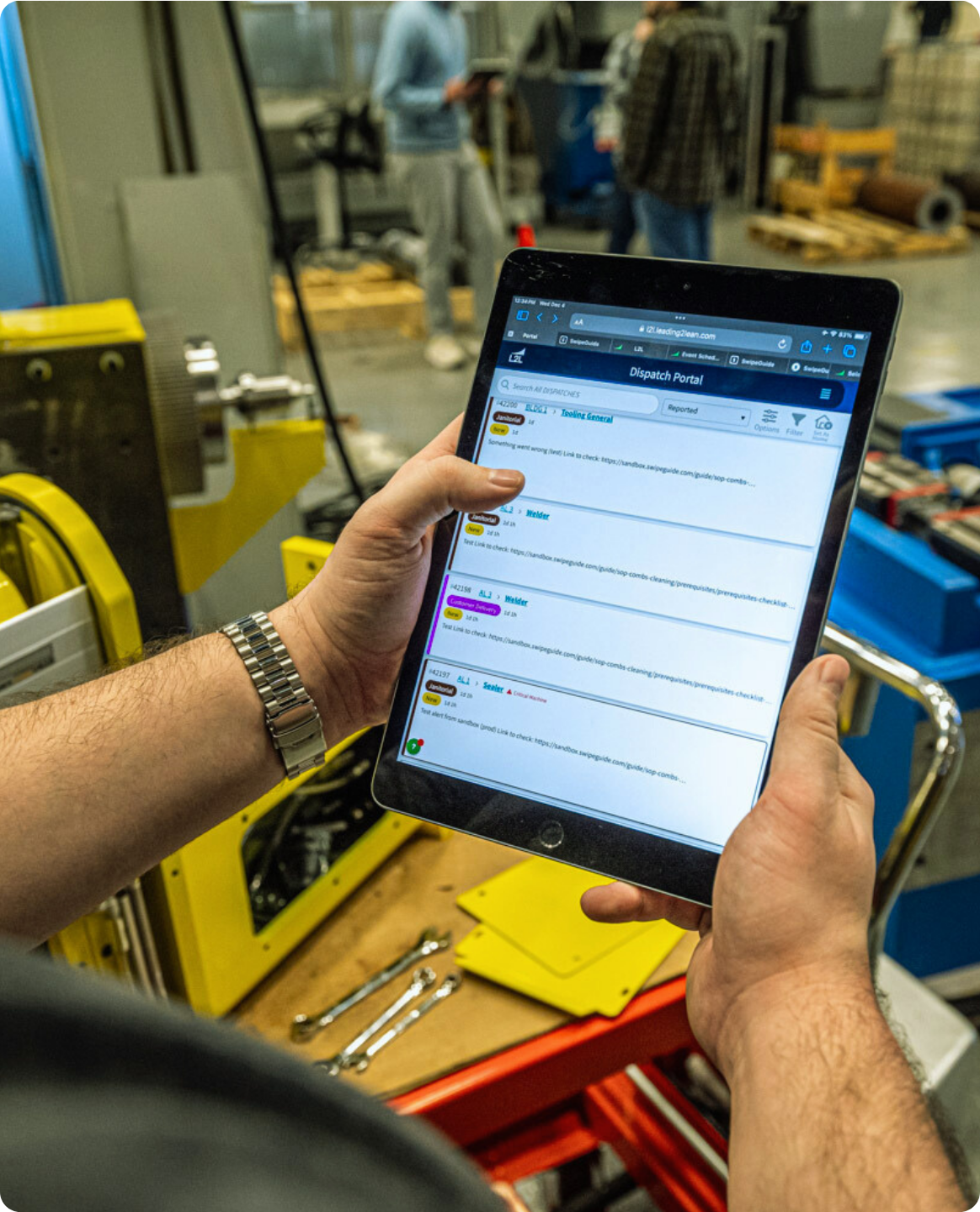
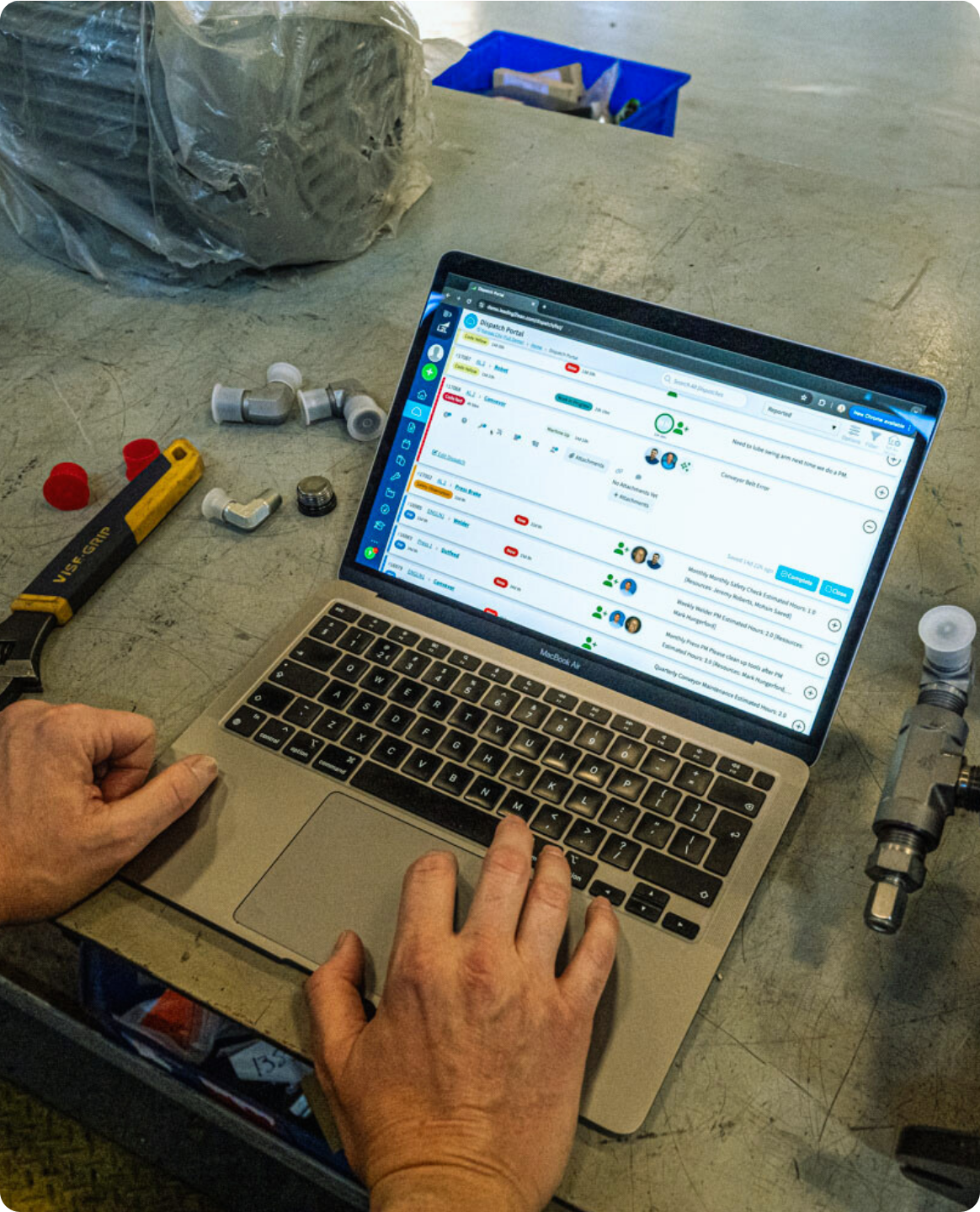
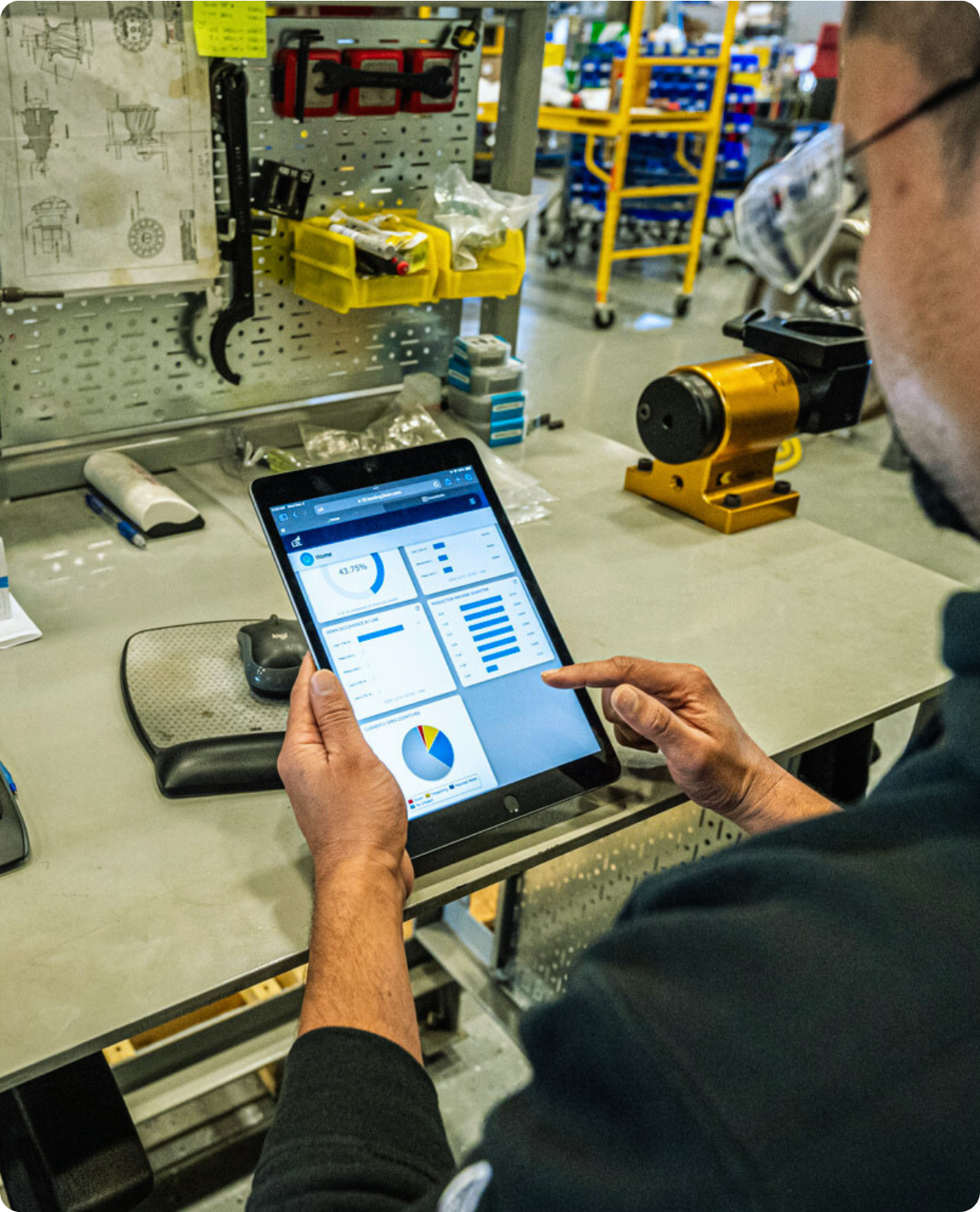
Boost performance and track progress by monitoring the impact of improvement initiatives. Adjust your strategies accordingly with our advanced OEE Pareto, bar chart, and trend reports.
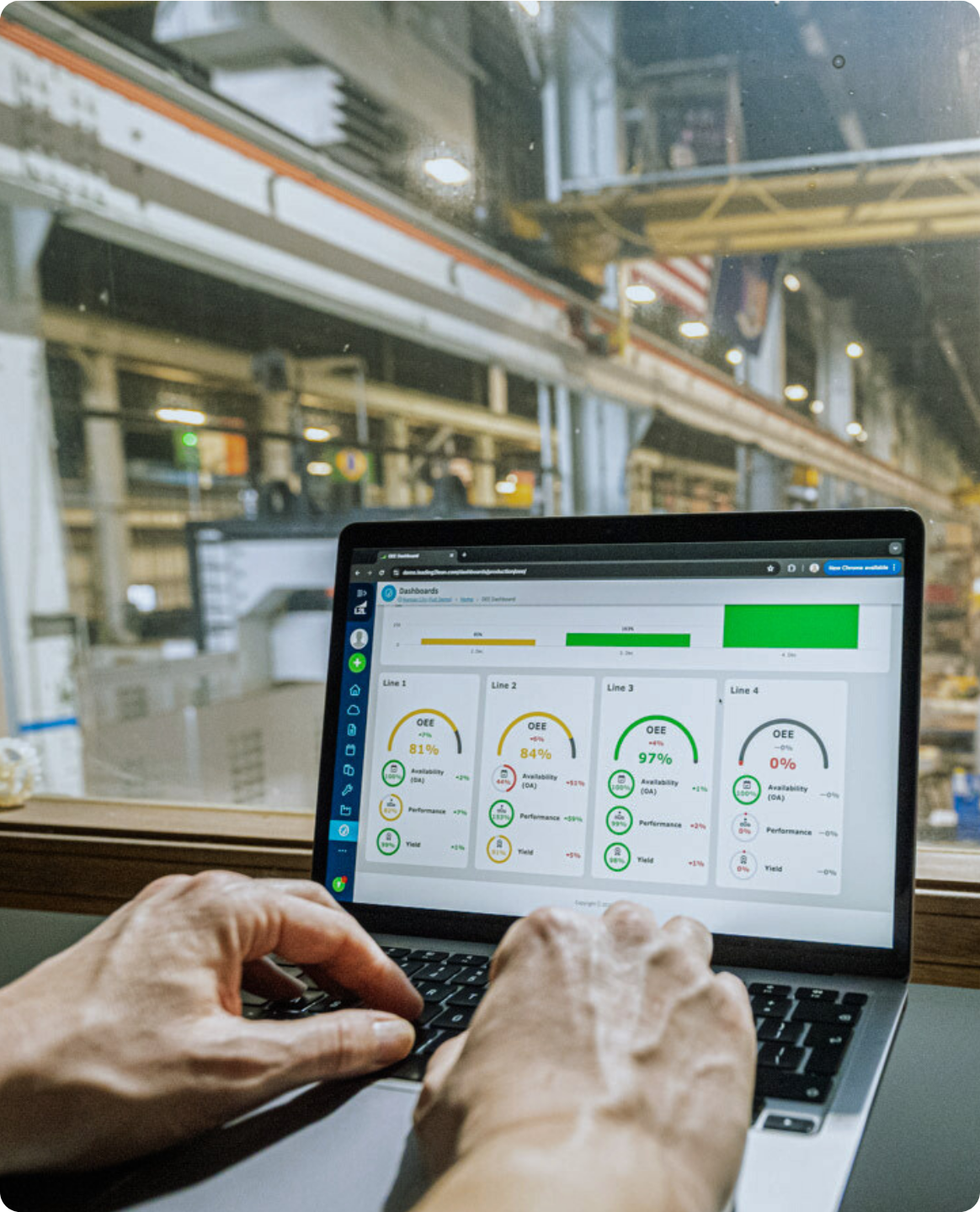
Address bottlenecks by analyzing time and resource allocation. Gain visibility into past, scheduled, and ongoing activities to optimize workflows. Reduce work order response times and enhance overall operational performance.
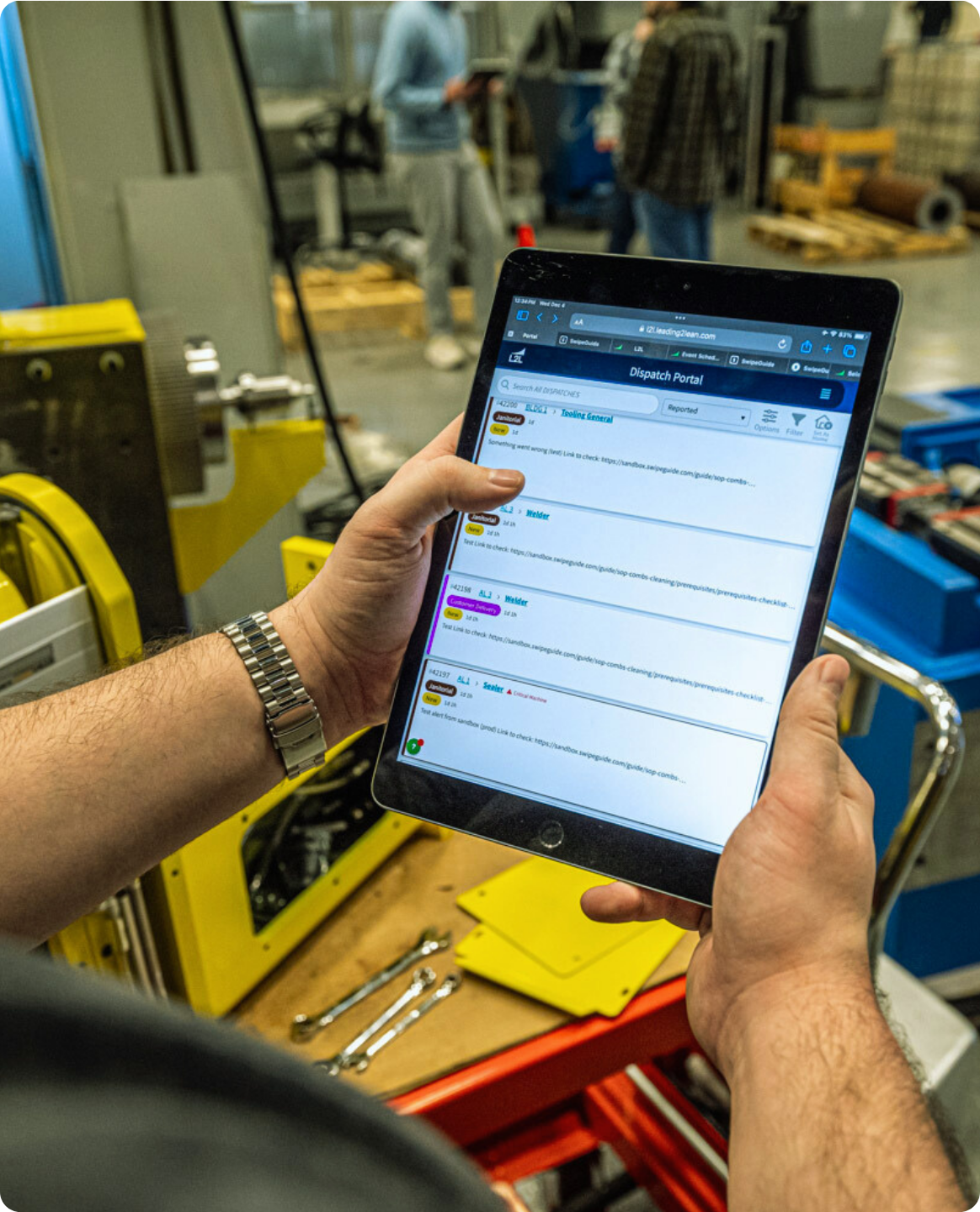
Reduce downtime and improve equipment reliability by identifying root causes and types of reactive maintenance while implementing proactive measures. Make data-driven decisions to justify investments in proactive maintenance and benchmark performance against industry standards.
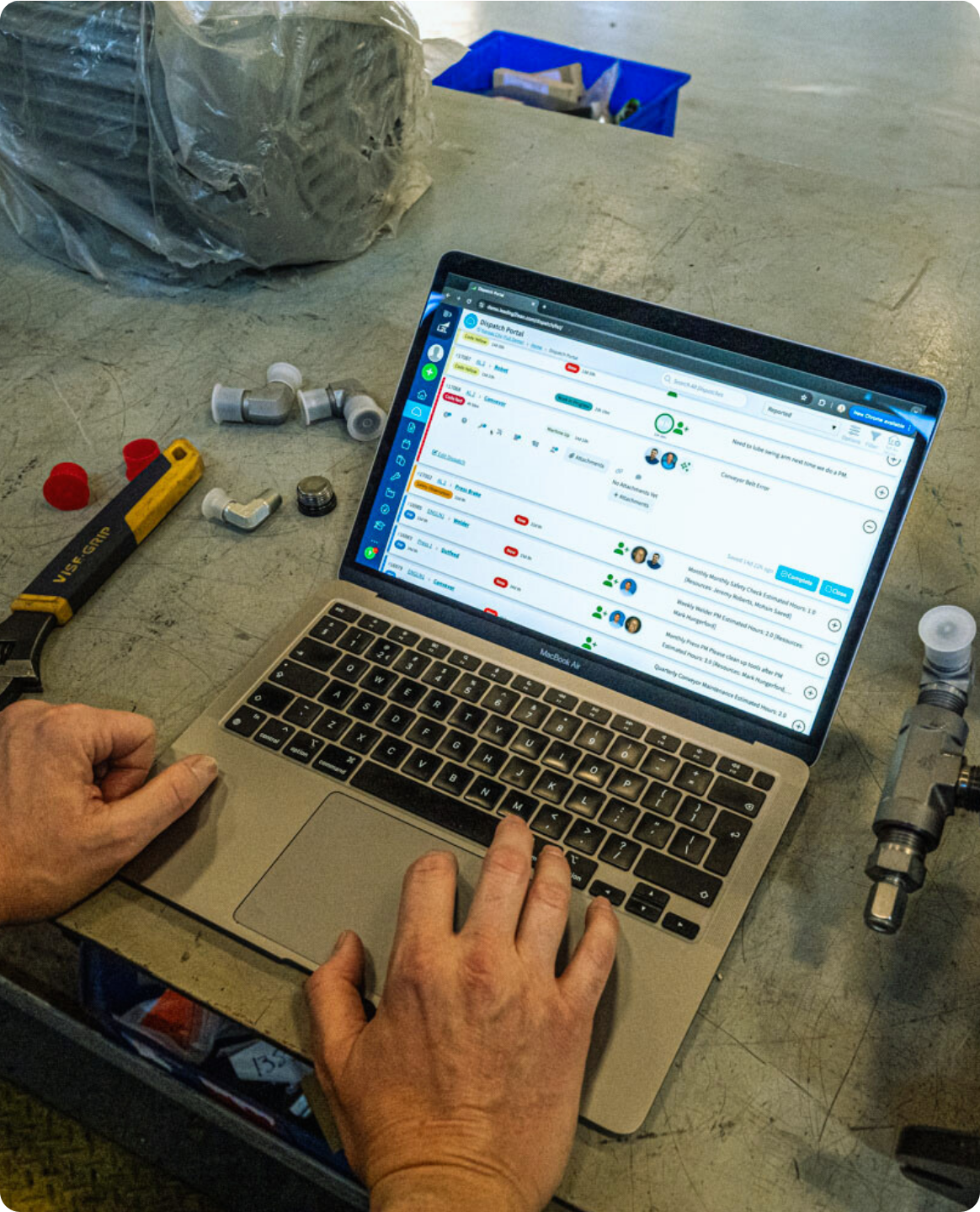
Track progress and ensure compliance by monitoring checklist completion rates and flagging potential issues. Analyze completion times and identify areas for improvement. Ensure adherence to critical procedures with metrics and charts that keep your team on track.
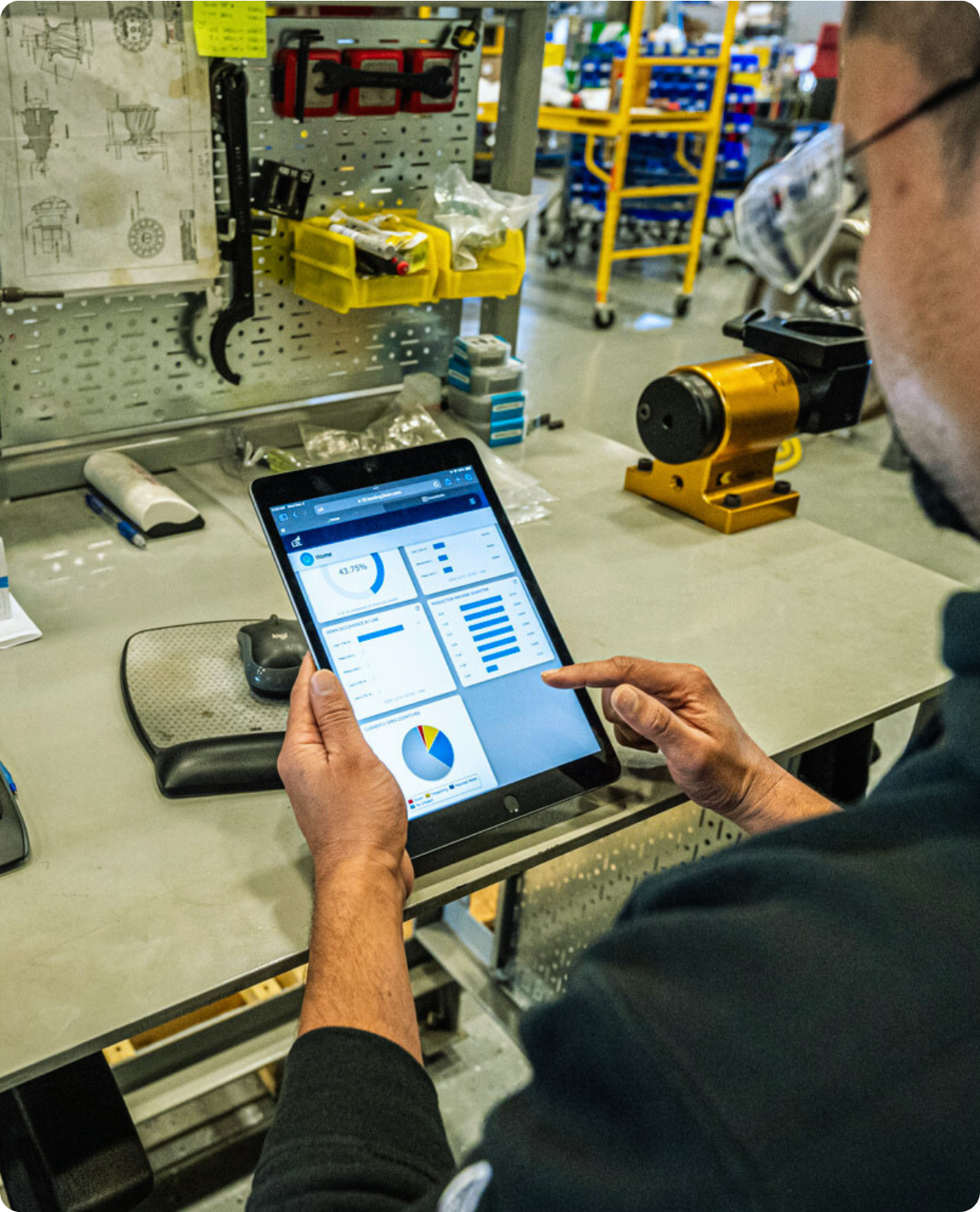
All your important reports in one overview
Focus on what matters most. See multiple screens in a simple interface.
-
Streamline tier meetings with automated data population and customizable SQDC dashboards.
-
Accelerate root cause analysis with drill-down capabilities and automated corrective action assignments.
-
Improve communication and accountability with real-time data visibility and seamless integrations.
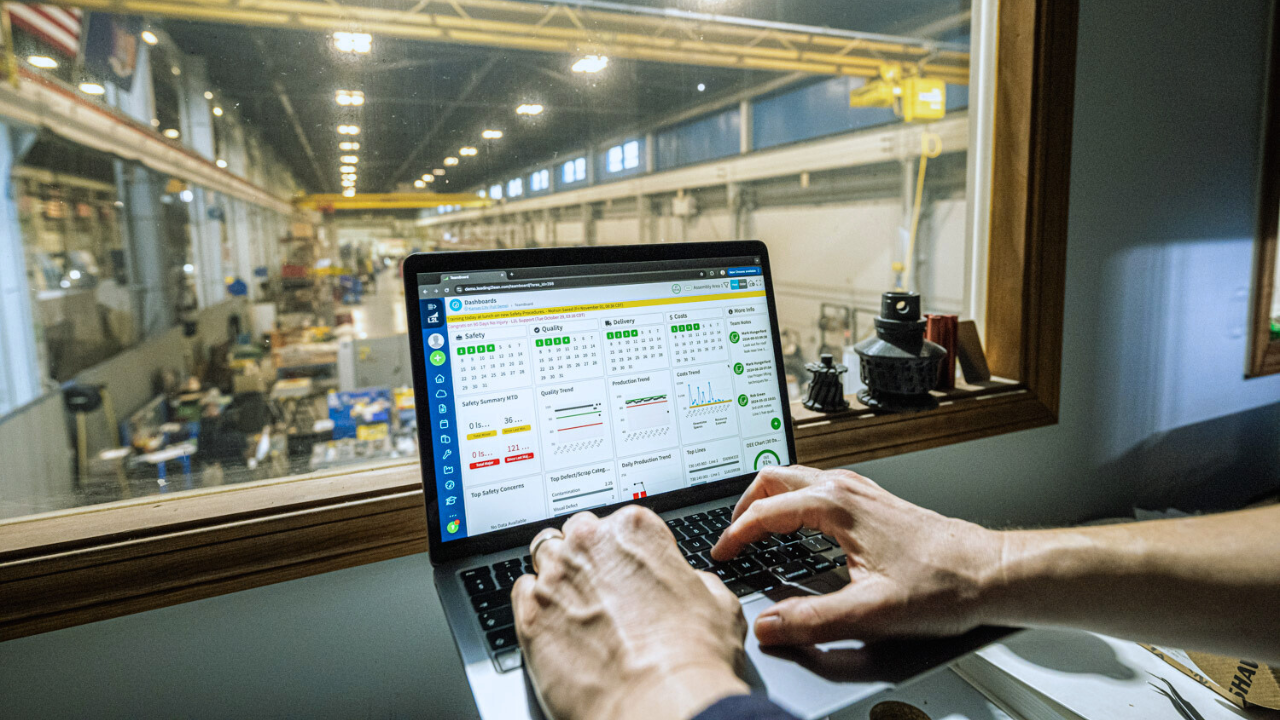
Need a report? Chances are we’ve got it.
Breakdown and downtime reports
Trend and bar charts focused on breakdowns and downtime.
Cost reports
Pareto and trend reports to help you monitor costs across operations.
Production reports
Line cycle times, status, defects, run rates, yield, quality, OEE, PPMH, PPH, and LMPU.
Work order and dispatch reports
Work order and dispatch trends and time to complete that can be scheduled by PM and on-time percentages.
Checklist reports
Monitor completion and compliance.
Kaizen reports
Kaizen trends and submission reports.
List overviews
Lists of notifications, actions, components, lines, and machines.
Spares reports
Spares history, trends, cost, occurrence, cycle count, and part movement.
Summaries
Daily, weekly, and monthly summary reports.
Insights made for real continuous improvement
Keep track of KPIs at scale. Discover trends, catch anomalies, identify root causes, and make informed decisions with L2L’s suite of manufacturing intelligence tools.
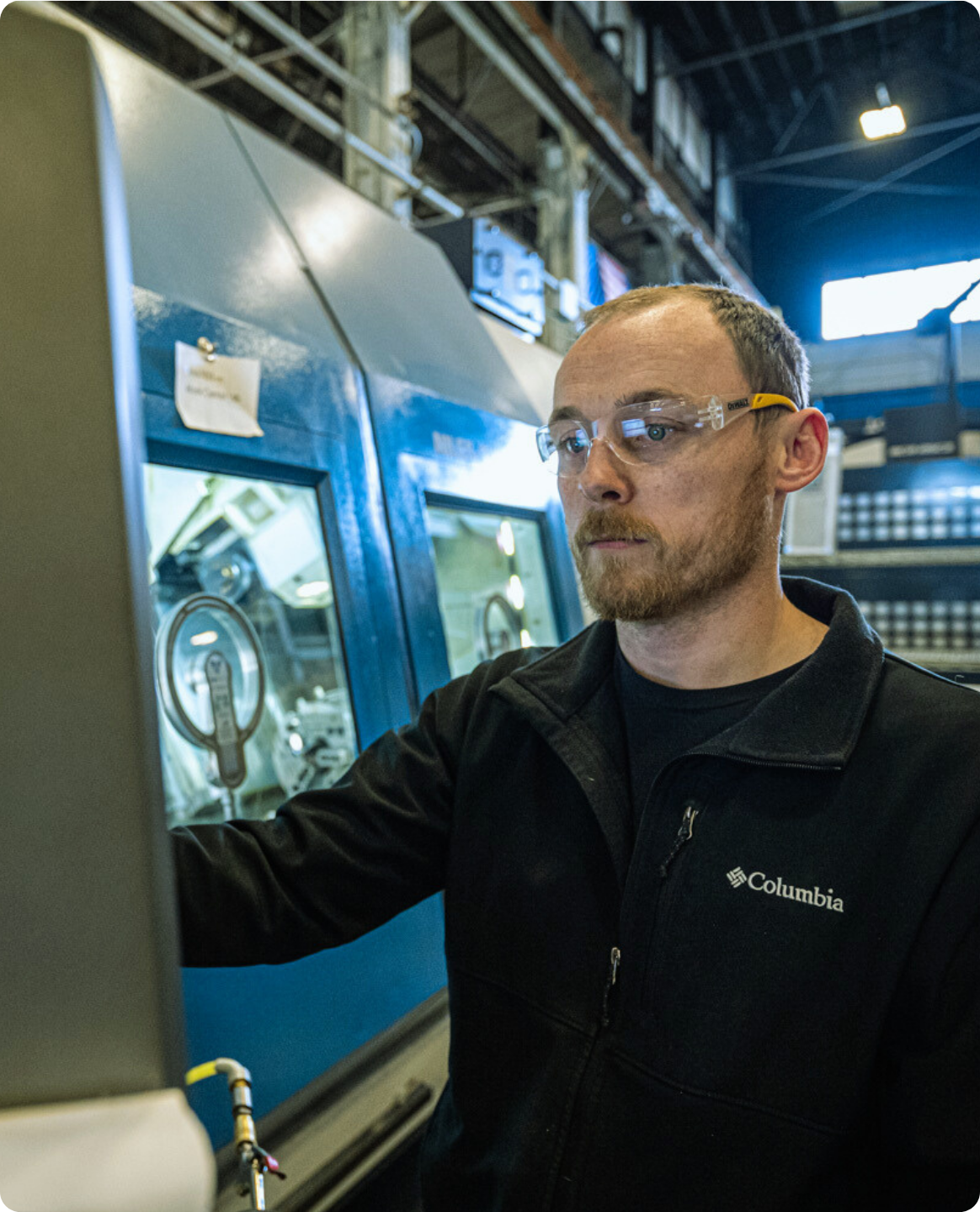
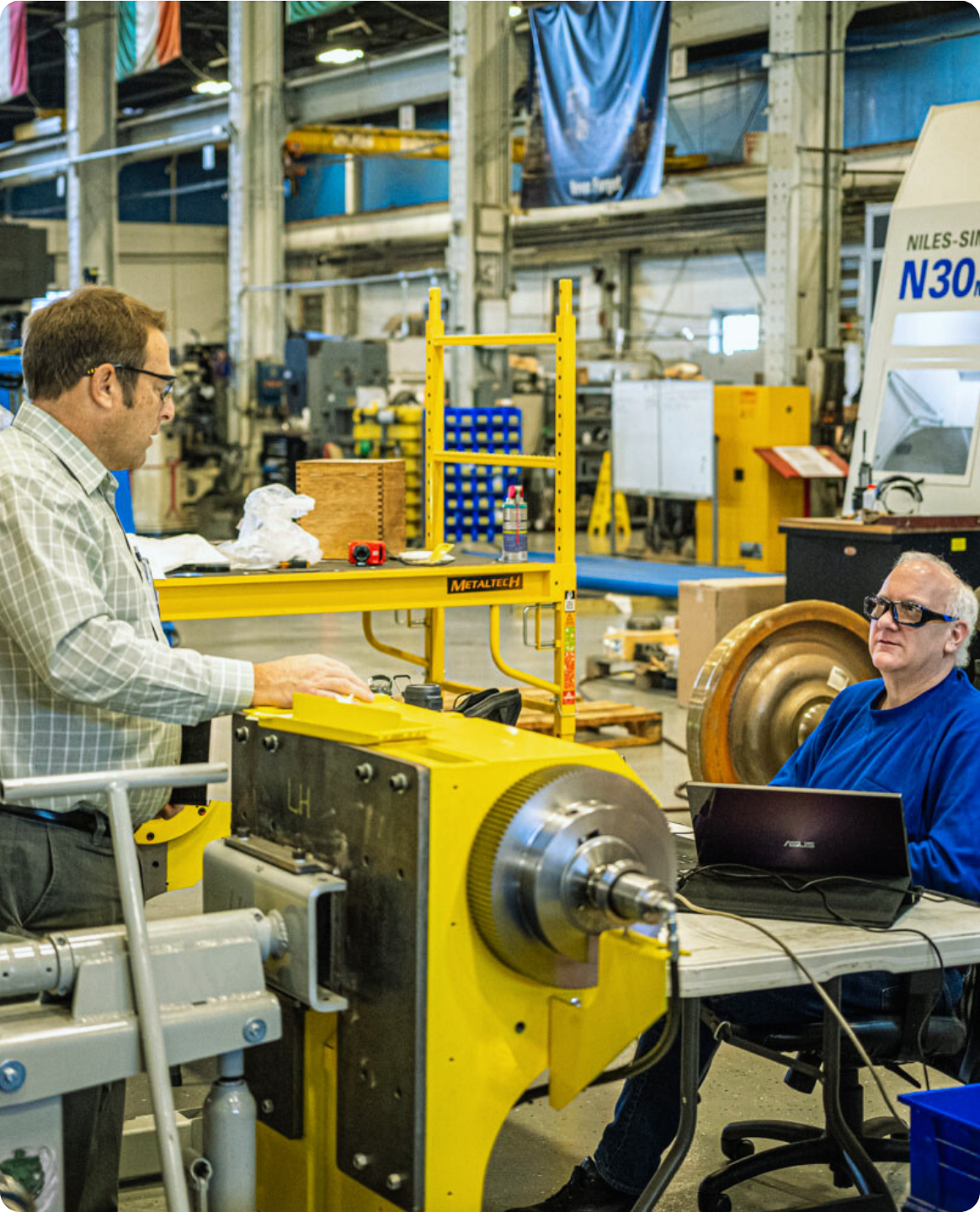

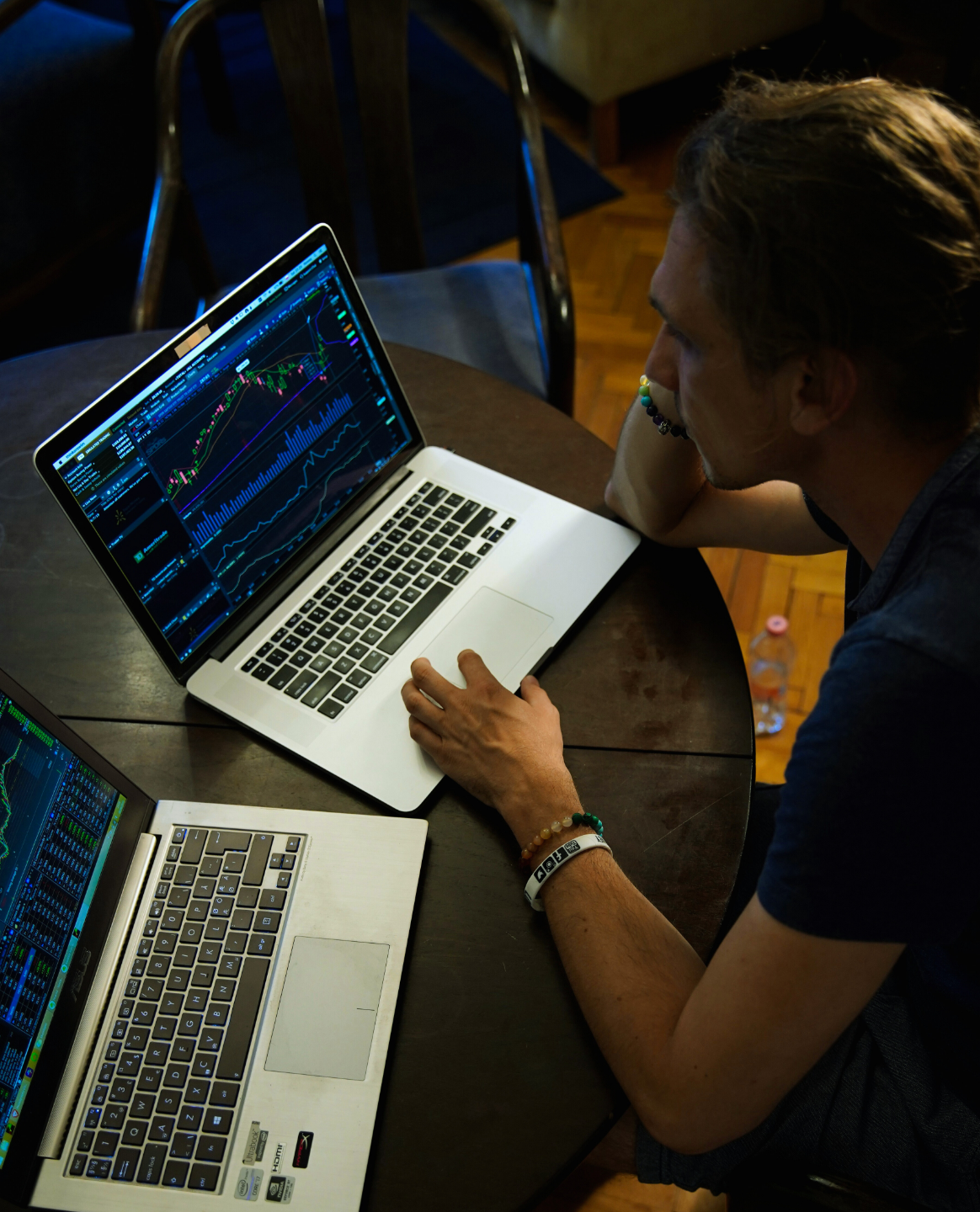
Compare operational performance across different plants, departments, and product lines to identify best practices and areas for improvement. Monitor production output, defect rates, and on-time delivery to track and measure the impact of improvement initiatives.
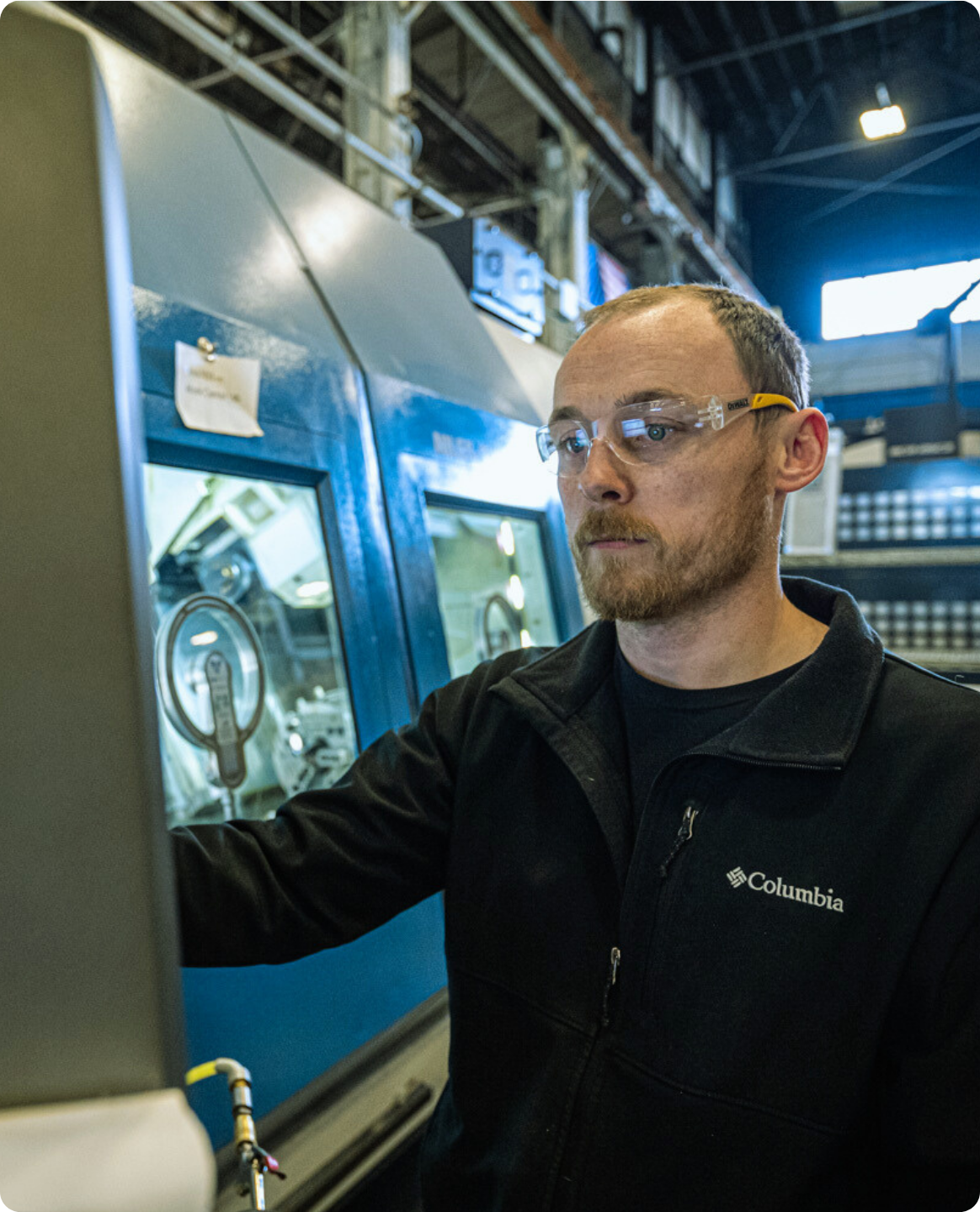
Keep track of production capacity, labor availability, operating costs, maintenance expenses, and expected equipment lifespan. Adjust production schedules and allocate resources while analyzing data on defect types, production batches, and machine performance to pinpoint the root causes of quality issues.
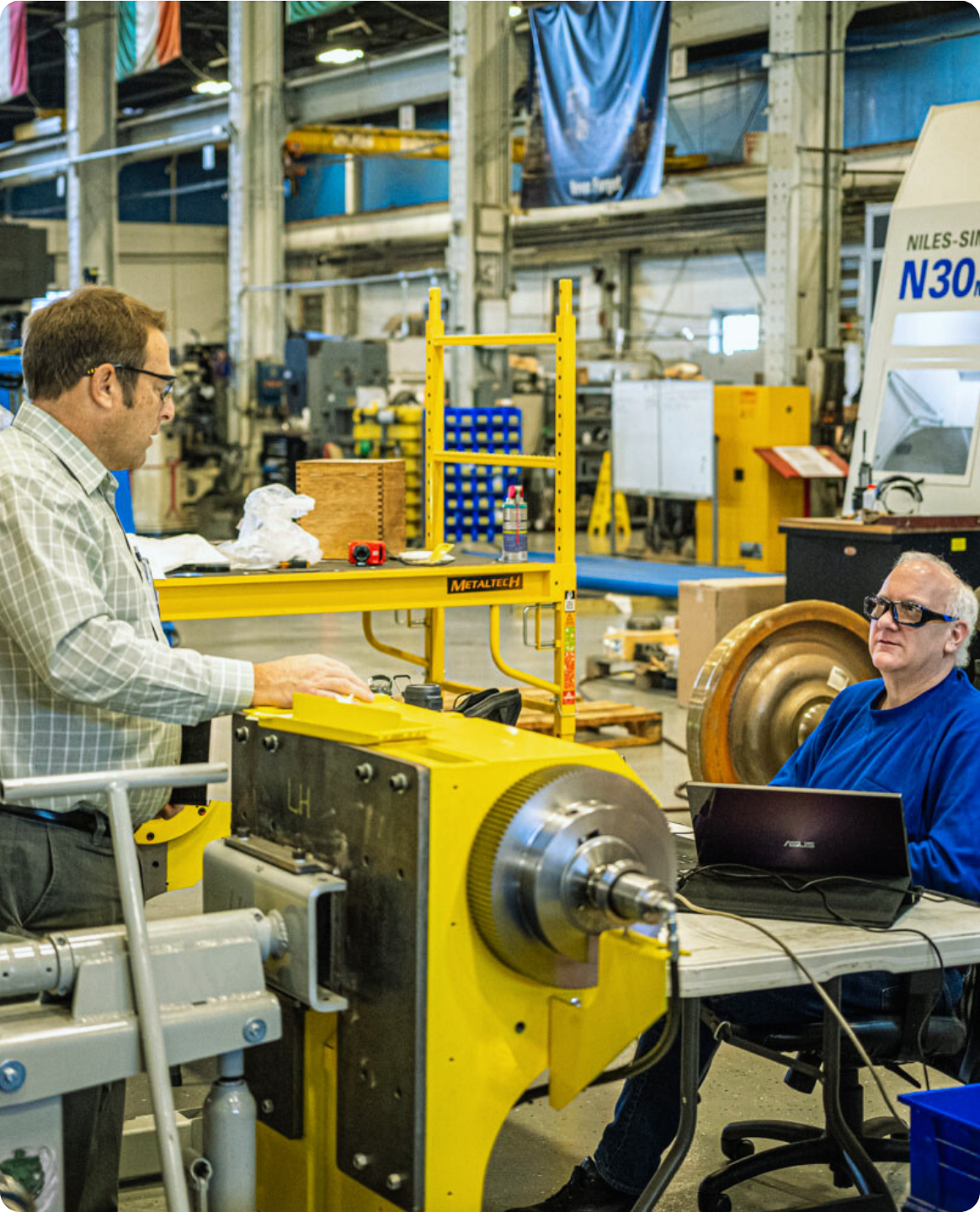
Determine the effectiveness of existing PM schedules and adjust them to minimize unplanned downtime. Keep track of work orders, schedule reports, and get on-time percentages when you need them.

Data only works if you can use it
Unclear reports. Clunky, confusing dashboards. Siloed information that’s hard to use and share. Analytics solutions that don’t provide the insights you need. Sound familiar? L2L ends the struggle.
-
Limited control and accessibility
-
Poor visualization and reporting
-
Siloed data
It’s time to explore your data beyond a set of predefined dashboards and reports. Our analytics software lets users create custom dashboards to zoom in on all of the information they need.
Data analytics needs to be accessible for everyone. L2L delivers insights in a user-friendly, intuitive format to get everyone on the same page. Communicate your needs clearly with better visualizations of your metrics and insights.
Gain a holistic view of performance across the scope of your operations. Consolidate performance data from multiple sites into a single, comprehensive dashboard.
-
Limited control and accessibility
It’s time to explore your data beyond a set of predefined dashboards and reports. Our analytics software lets users create custom dashboards to zoom in on all of the information they need.
-
Poor visualization and reporting
Data analytics needs to be accessible for everyone. L2L delivers insights in a user-friendly, intuitive format to get everyone on the same page. Communicate your needs clearly with better visualizations of your metrics and insights.
-
Siloed data
Gain a holistic view of performance across the scope of your operations. Consolidate performance data from multiple sites into a single, comprehensive dashboard.
“The forward-thinking vision with AI, BI, and rules-based automation is exactly where we all need to focus, and L2L has done a great job in moving quickly in these game changers.”
Vice President of Information Technology
"Highly adaptable to use for a lot of tasks within the manufacturing environment. It covers production and maintenance, but we have also expanded it to track variances, expand notifications for tasks and actions, and we use it for labor time tracking and management."
Maintenance Manager & Sr. Mfg. Eng.
"L2L makes it simple to drill down through categorical data and various collected metrics and plant production information. I most often use this to synthesize scrap paretos and report out on our continuous improvement progress. L2L is an all inclusive interface that I utilize multiple times per week with ease to pull data for our production performance."
Project Engineer
"L2L - THE tool for transformation. [I like] everything... automated dispatches, standard work tools, data accuracy, historical data, dashboards... it's such a powerful tool!"
Plant General Manager
Ready to optimize your operations?
See how L2L’s manufacturing intelligence platform turns data into actionable insights, helping you improve decision-making, efficiency, and collaboration across your sites.