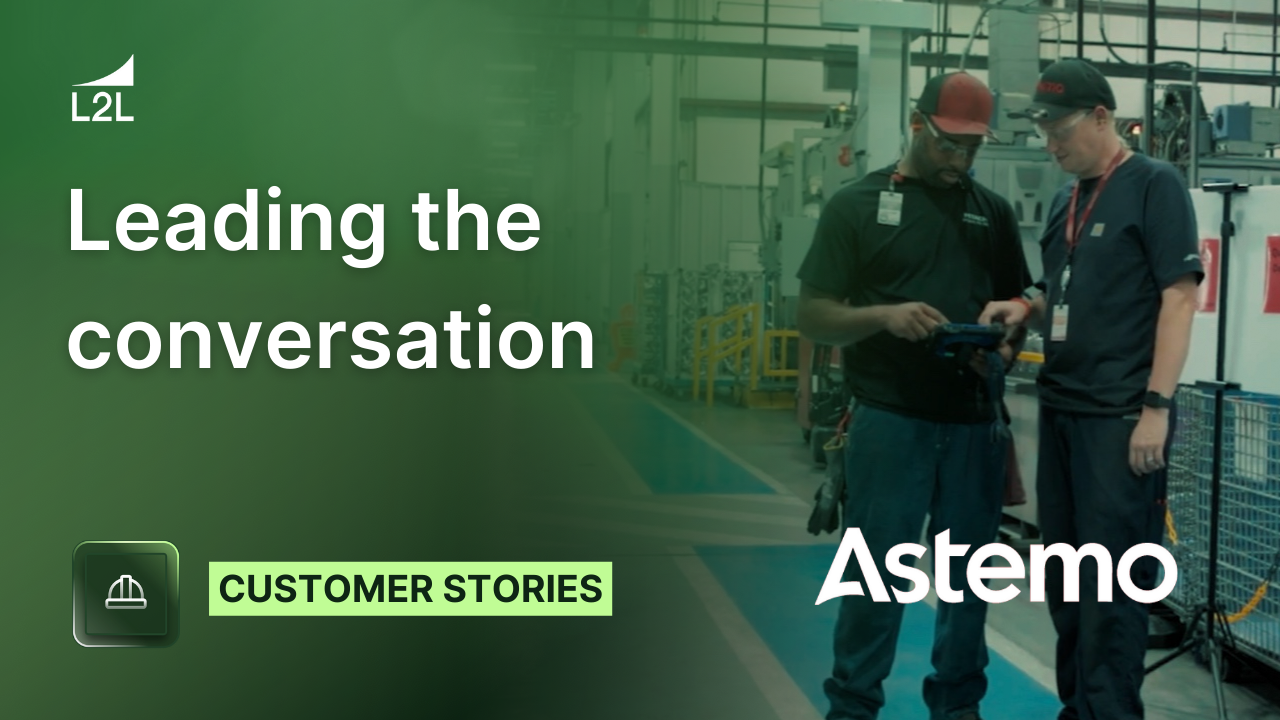
Customer success video of the Hitachi Astemo Rock Spring, GA site.
Learn more about a Smarter Approach to Smart Manufacturing
Maximize production throughput by giving your workforce the tools it needs to drive continuous improvement.
Each machine has it's own unique landing page. On that landing page there is an image of the machine, real-time data about dispatches, machine status, mean time to repair, mean time between failures, and information about top spares and dispatch types. At the bottom, you can do additional research on the machine if necessary. If you discover an issue with the machine, we’ve got an easy green dispatch button at the top so that you can quickly trigger a dispatch with information about that machine already filled in.
Request a Demo