Win the day, together
Retain and attract star players while developing a more competent, skilled, and engaged frontline.
Train and upskill connected manufacturing teams with L2L’s workforce management software.
Skilled and connected frontline teams
L2L helps you build a competent frontline workforce for the long haul. Elevate and support them with better training while improving skills management across the organization.
-
Low productivity
-
Old data
-
Skills deficit
-
Communication gaps
-
Inefficient training
When supervisors and managers don’t have visibility into all activities happening on the shop floor, plant productivity is negatively impacted. Real-time dashboards help the entire team quickly see if they are keeping up or falling behind.
When plant operations are managed manually and across separate systems, frontline teams don’t have direct access to the information they need, which makes them frustrated and less engaged. When frontline teams have the information required to do their jobs correctly and know what is expected of them, orders are filled faster and output is higher.
Ineffective training leads to knowledge gaps, workforce disengagement, and lower productivity. Effective skills development and upskilling tools equip your workforce to maximize productivity and drive innovation while keeping them engaged.
If team members can only raise issues verbally, problems slip through the cracks, and nothing gets done. When employees can report disruptions and suggest improvements in a central location, everyone becomes a data-driven problem-solver, and communication between departments is smoother.
With average employee turnover in manufacturing hovering around 39%, consistent and standardized frontline onboarding and training methods are crucial. AI-powered work instructions and action-driving knowledge management tools guide less-tenured employees on tasks so they can make decisions faster and perform their jobs better.
-
Low productivity
When supervisors and managers don’t have visibility into all activities happening on the shop floor, plant productivity is negatively impacted. Real-time dashboards help the entire team quickly see if they are keeping up or falling behind.
-
Old data
When plant operations are managed manually and across separate systems, frontline teams don’t have direct access to the information they need, which makes them frustrated and less engaged. When frontline teams have the information required to do their jobs correctly and know what is expected of them, orders are filled faster and output is higher.
-
Skills deficit
Ineffective training leads to knowledge gaps, workforce disengagement, and lower productivity. Effective skills development and upskilling tools equip your workforce to maximize productivity and drive innovation while keeping them engaged.
-
Communication gaps
If team members can only raise issues verbally, problems slip through the cracks, and nothing gets done. When employees can report disruptions and suggest improvements in a central location, everyone becomes a data-driven problem-solver, and communication between departments is smoother.
-
Inefficient training
With average employee turnover in manufacturing hovering around 39%, consistent and standardized frontline onboarding and training methods are crucial. AI-powered work instructions and action-driving knowledge management tools guide less-tenured employees on tasks so they can make decisions faster and perform their jobs better.
Build success from the shop floor up
You rely on competent and connected frontline teams for top-line productivity and high-quality products. L2L is here to deliver the training and knowledge they need to perform every day and every shift.
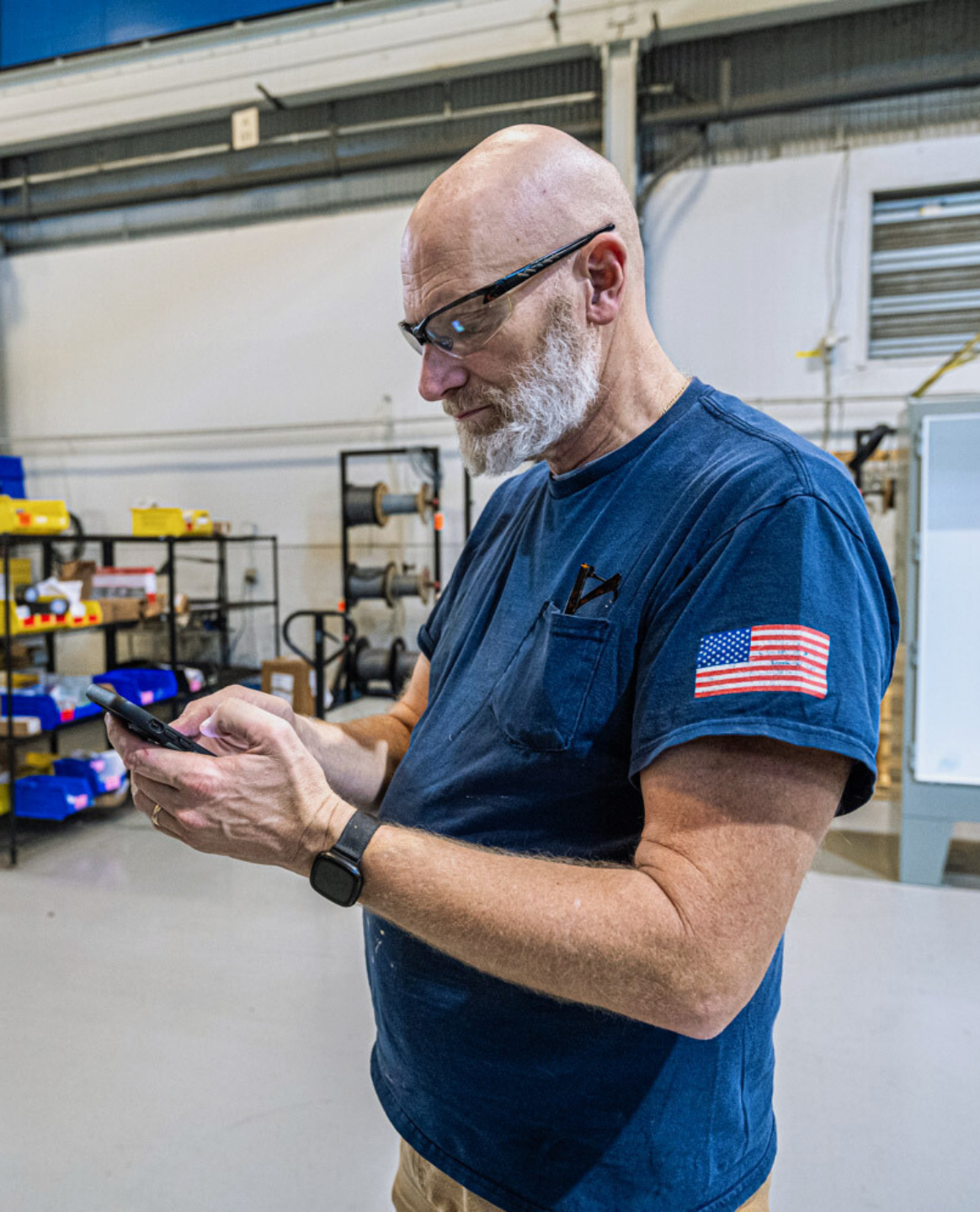
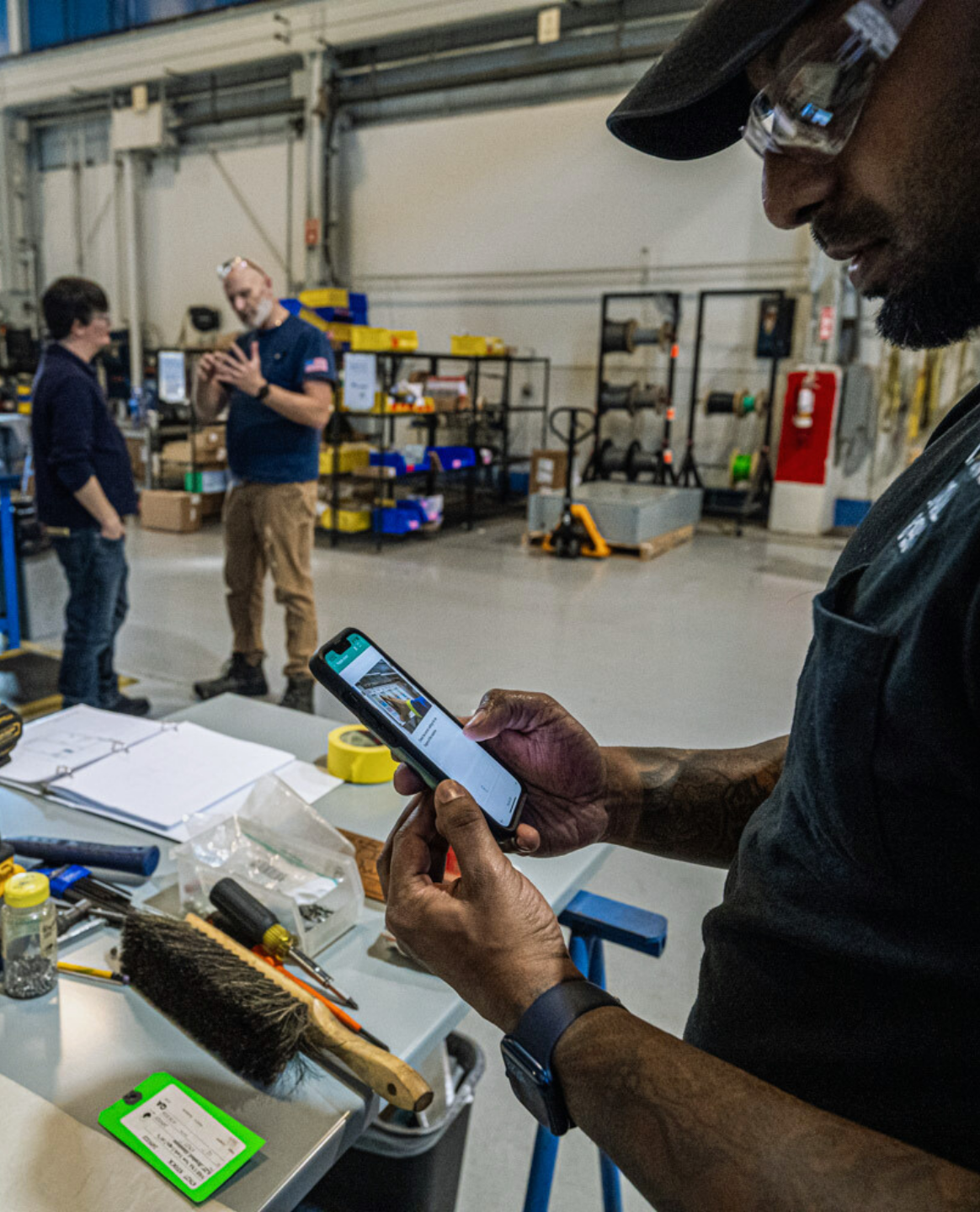
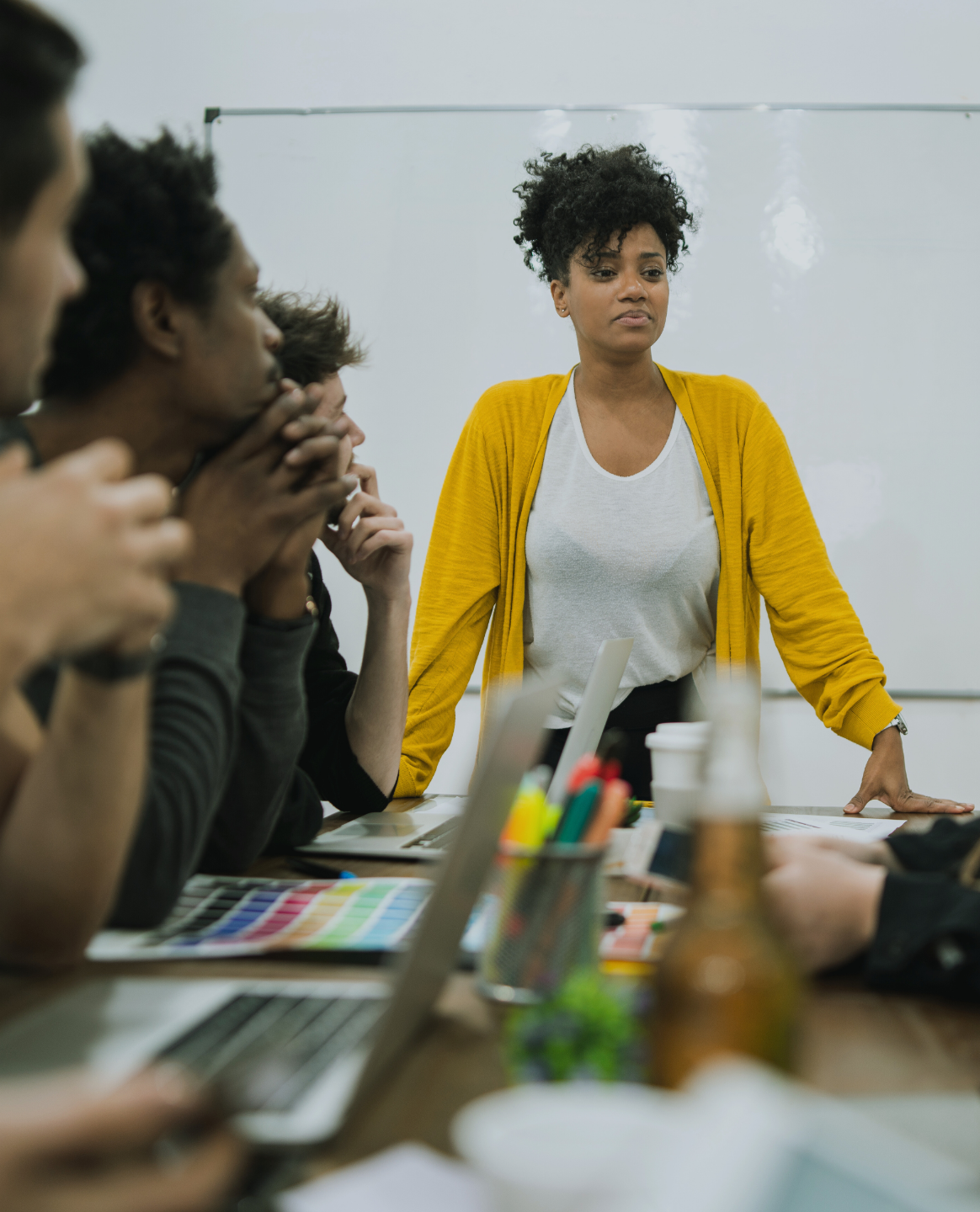
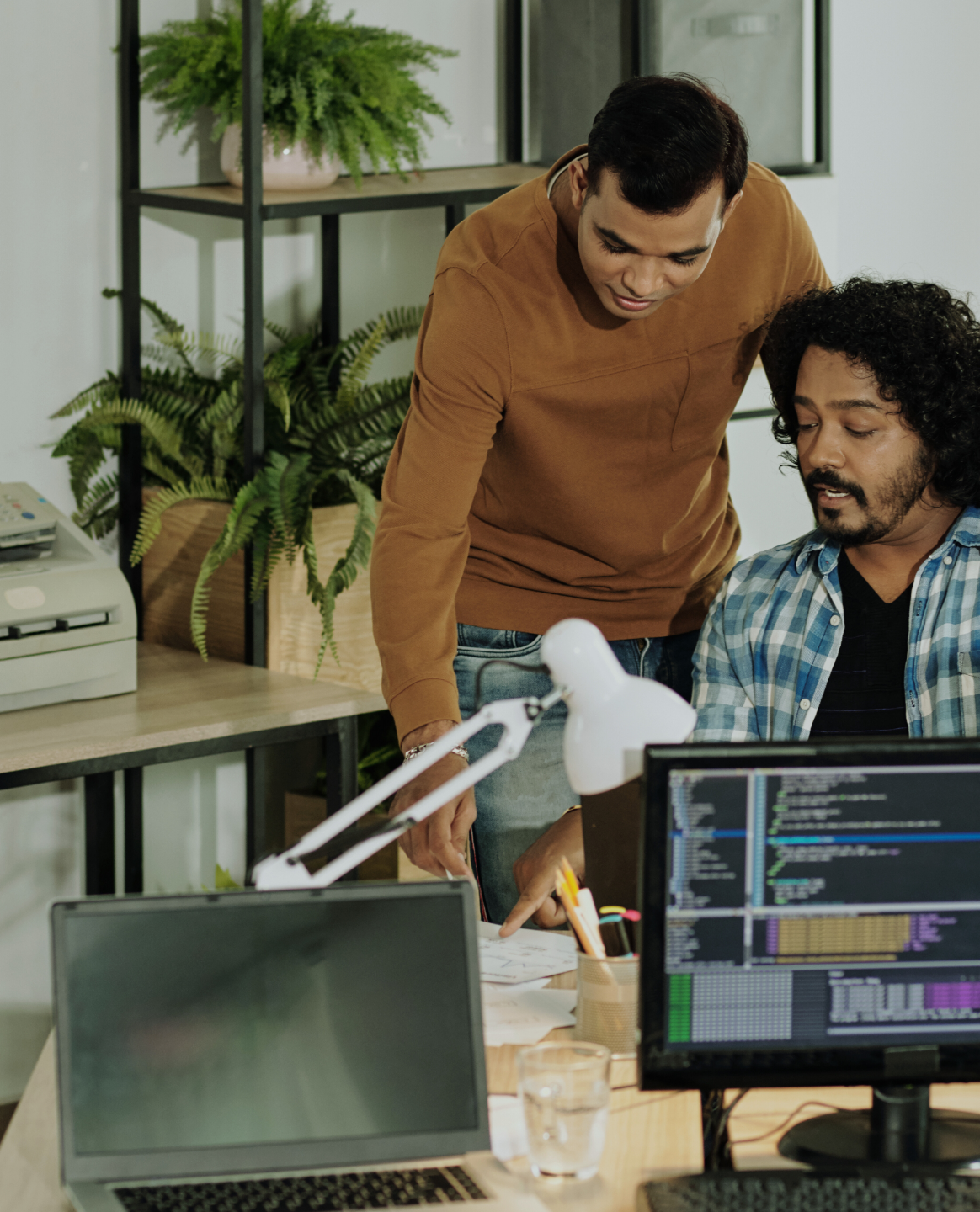
Frontline teams get clear, standardized mobile work instructions in their language, providing the operational knowledge they need to get the job done right.
The Smart Skills app seamlessly connects upskilling, assessments, and skills development to real tasks, workflows, and step-by-step guidance.
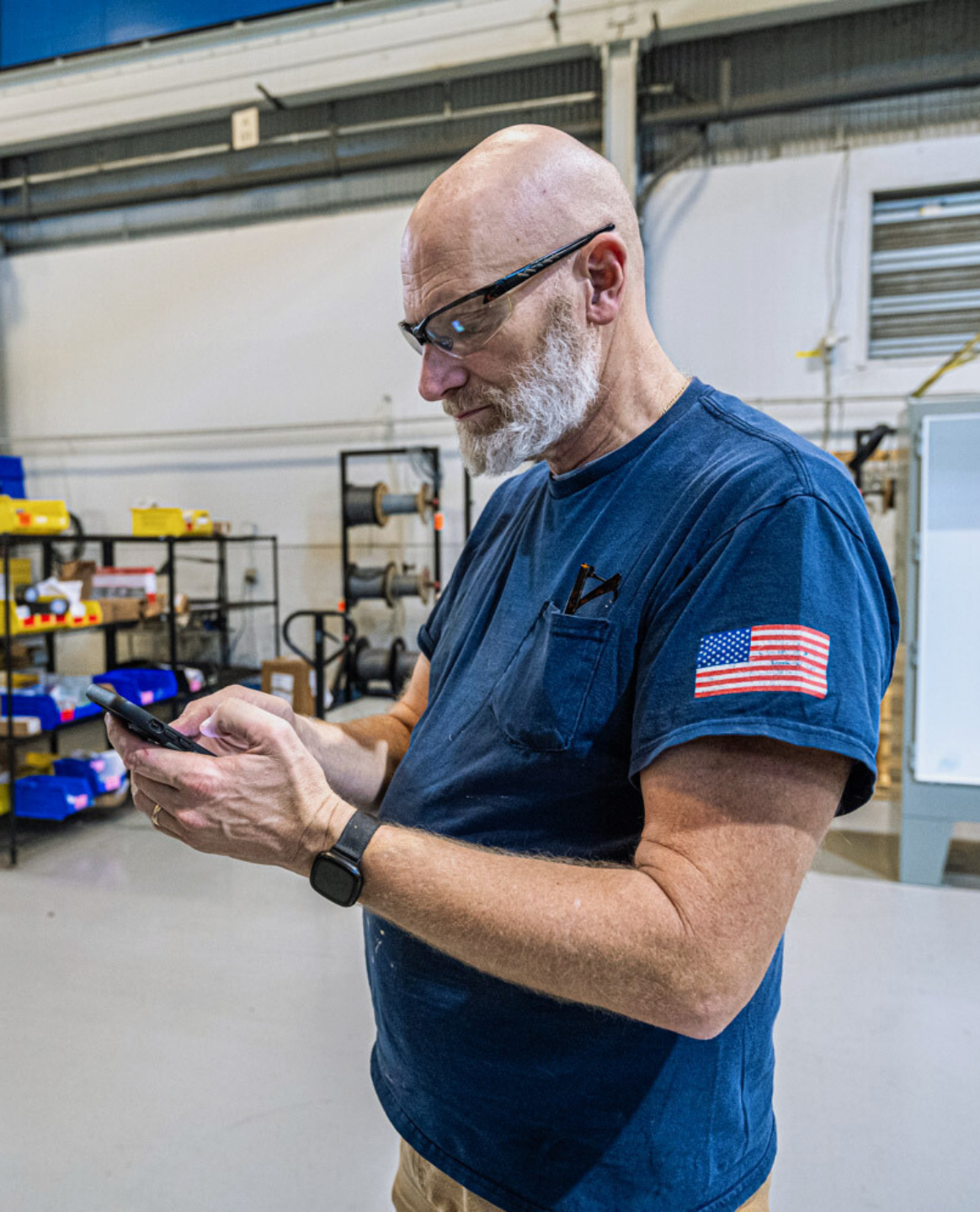
Hit your targets and ensure smooth operations with qualified team members who know how to get it done.
Visual work instructions, standard operating procedures, and learning modules ensure continuous training and skills management across teams, lines, and shifts.
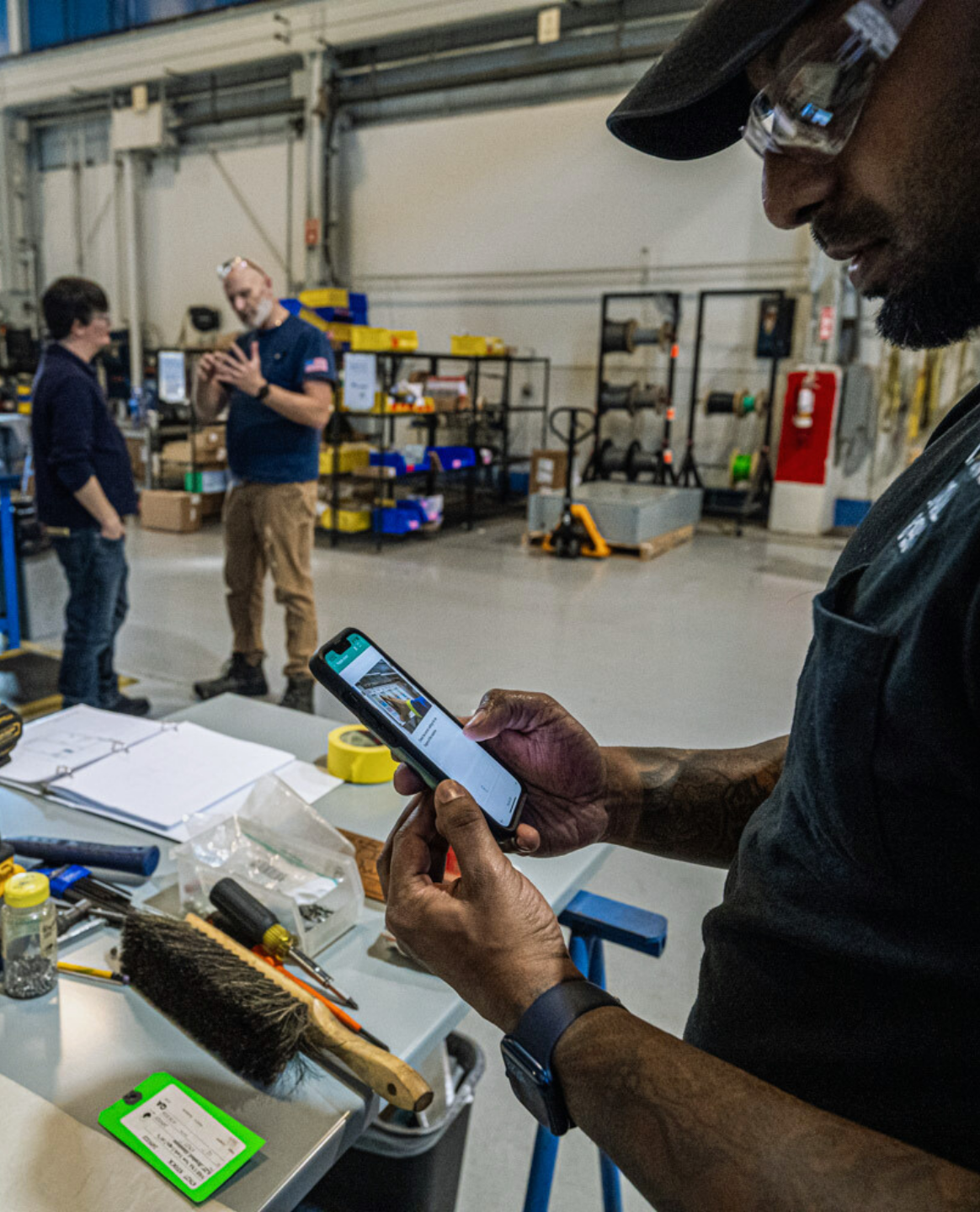
Boosting productivity and standardizing operations at scale starts with high adoption of user-friendly digital tools by your frontline teams.
Share job profiles across all of your sites to simplify standardization across global operations (in 52+ languages), while improving employee competency.
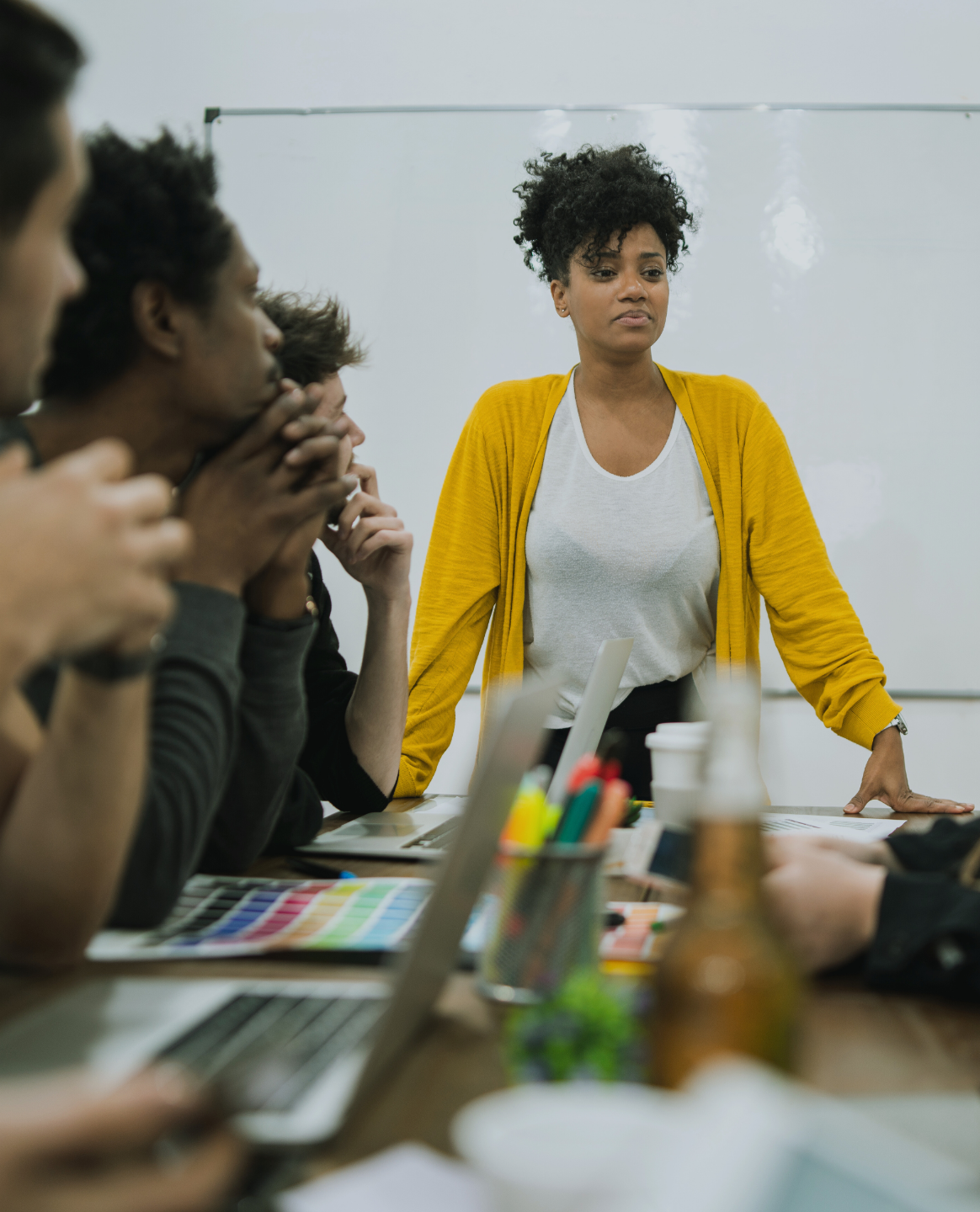
Digitally transform your workforce
When people collaborate, performance is exponential.
We’re here for the frontline
Skills-based training. Performance visibility. Exceptional job aids. Allow your latest hire to perform like your most tenured team member.
Task management
Dispatch is the missing link between disruptions and action. Create unique Dispatches for any event in your production flow and use them to trigger and track the correct response from your teams with custom workflows.
Employee training
Deliver faster onboarding and time-to-competency with skills-based training modules and learning journeys in L2L. Make sure everyone’s on the same page—from new hires to tenured employees.
Digital work instructions and SOPs
Capture and distribute operational knowledge with intuitive, visual digital work instructions and SOPs available in 52+ languages. Monitor adoption and effectiveness while capturing feedback for continuous improvement.
Knowledge management
L2L helps you capture critical fixes and improvements from expert team members and share best practices across the entire organization.
Skills management and certification
Efficiently manage skills, streamline operations, and validate training with our dynamic skills management tools. Verify competencies, identify skills gaps, and deliver the right training to upskill where needed.
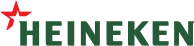
Clear and interactive visual work instructions and training materials. What I particularly like is the user-friendly interface and the ability to quickly create and distribute step-by-step guides. These guides are easy to follow, which helps improve efficiency and reduce errors in various processes.
Team Leader

Everyone began using it right away. I’ve been part of software rollouts in the past, and I’ve never seen that eagerness. The moment they had the tablets in their hands and saw what L2L could do — getting updates, making work requests through Dispatches. They just took it and ran with it, never looking back.
Plant General Manager
L2L is really a system focused on the people at the plant. That’s what struck a chord with us.
Head of Engineering
Frequently asked questions
Get answers to how L2L supports training, upskilling, and empowering your frontline for success every shift.
How does L2L help improve frontline team performance?
L2L empowers frontline teams with access to up-to-date digital work instructions, intuitive job aids, and skills development tools. This ensures teams can execute tasks accurately and consistently, reducing errors and driving efficiency.
Can L2L help reduce employee turnover?
Yes, L2L fosters employee engagement by providing opportunities for skills development, meaningful job growth, and streamlined processes. These tools help retain workers by creating a more connected and fulfilling work environment.
Which training tools does L2L offer for workforce development?
L2L includes skills-based training modules, digital work instructions, and real-time knowledge management systems. These tools enable faster onboarding, continuous upskilling, and enhanced competency across teams.
Related content
The 2025 Manufacturing Skills Report: Are Frontlines Equipped for Success?
Connect and Empower Your Frontline Workers
Everything You Need to Know About Connected Workers
Driving ROI: The Business Case for a Connected Worker Platform
Ready to transform your frontline?
Discover how L2L connects, trains, and upskills your teams to reduce turnover, boost engagement, and drive operational success.