Uncover anomalies. Eliminate defects.
Improve your products. L2L is the quality monitoring tool that enlists the entire shop floor.
Find quality issues fast.
Solve them even faster.
Quality suffers when teams lack a clear view of processes and standards. Reduce waste with clear visibility, standardized work, and data.
-
Scrap and waste
-
High spare parts inventory costs
-
Paperwork and reporting
-
Product quality
-
No alerts
Identifying scrap during production runs is hard if quality isn't monitored in real time. This can lead to a substantial amount of scrap by the end of the day. Monitor, capture, and display scrap and rework in real time—by line, machine, and scrap code—to pinpoint where material was lost and what caused it.
Spare parts can be a black box. When your spare parts inventory is disconnected from your maintenance and production systems, it’s impossible to predict what spares are needed and when. AI-powered spare part suggestions prevent downtime (and frustration).
An average frontline worker spends 30 to 120 minutes every day on paperwork. Track performance metrics and production goals in real time with comprehensive reports, including: trend charts, checklist reports, Kaizen reports, occurrence charts, time-based reports, scheduling, searchable notification history, setup reports, and cost reports.
Most factories have that notorious underperforming line. With full visibility into all lines, it’s easy to identify root causes and fix problems once and for all. Get a complete view of the entire product process and display an integrated production and maintenance schedule. Identify inefficiencies with the help of AI-powered suggestions that maximize throughput.
Lack of visibility into tasks and actions will stall productivity. Automatically send out Dispatches alerting the right person to take action. Visualize and pinpoint the causes of scrap across the plant.
-
Scrap and waste
Identifying scrap during production runs is hard if quality isn't monitored in real time. This can lead to a substantial amount of scrap by the end of the day. Monitor, capture, and display scrap and rework in real time—by line, machine, and scrap code—to pinpoint where material was lost and what caused it.
-
High spare parts inventory costs
Spare parts can be a black box. When your spare parts inventory is disconnected from your maintenance and production systems, it’s impossible to predict what spares are needed and when. AI-powered spare part suggestions prevent downtime (and frustration).
-
Paperwork and reporting
An average frontline worker spends 30 to 120 minutes every day on paperwork. Track performance metrics and production goals in real time with comprehensive reports, including: trend charts, checklist reports, Kaizen reports, occurrence charts, time-based reports, scheduling, searchable notification history, setup reports, and cost reports.
-
Product quality
Most factories have that notorious underperforming line. With full visibility into all lines, it’s easy to identify root causes and fix problems once and for all. Get a complete view of the entire product process and display an integrated production and maintenance schedule. Identify inefficiencies with the help of AI-powered suggestions that maximize throughput.
-
No alerts
Lack of visibility into tasks and actions will stall productivity. Automatically send out Dispatches alerting the right person to take action. Visualize and pinpoint the causes of scrap across the plant.
Quality is built from the ground up
Reducing defects depends on early problem detection and fast, consistent action from your entire team—not just quality inspectors.
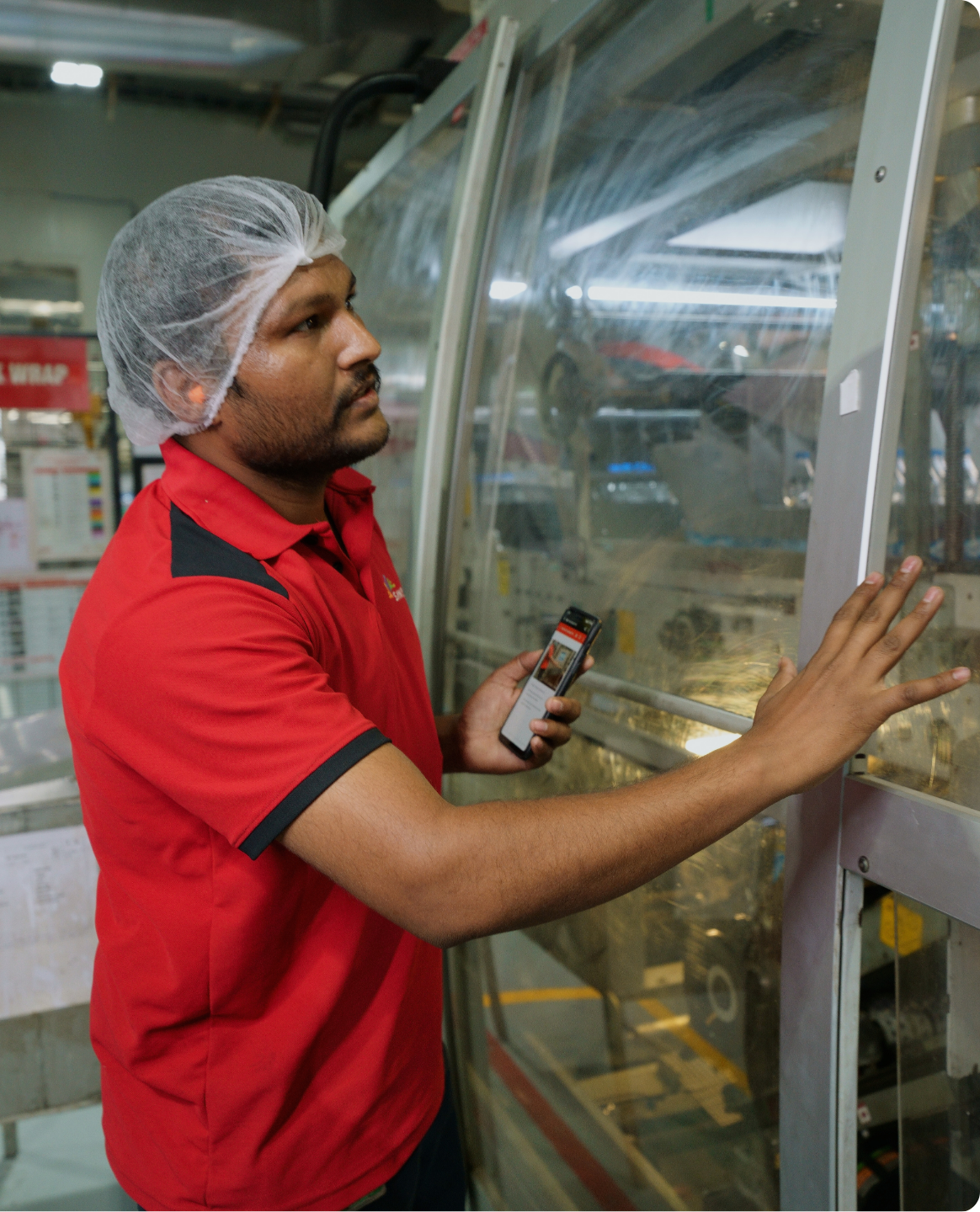
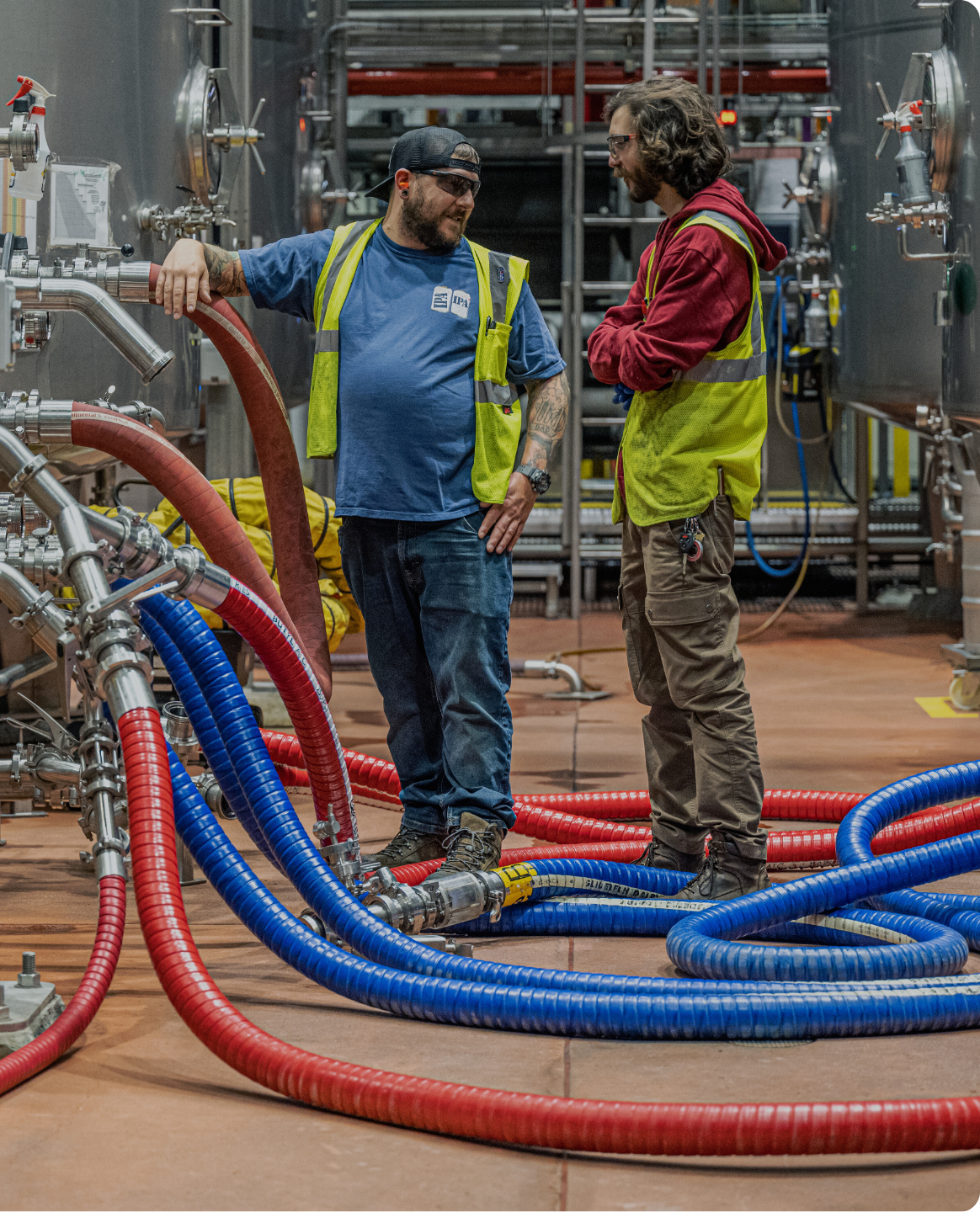
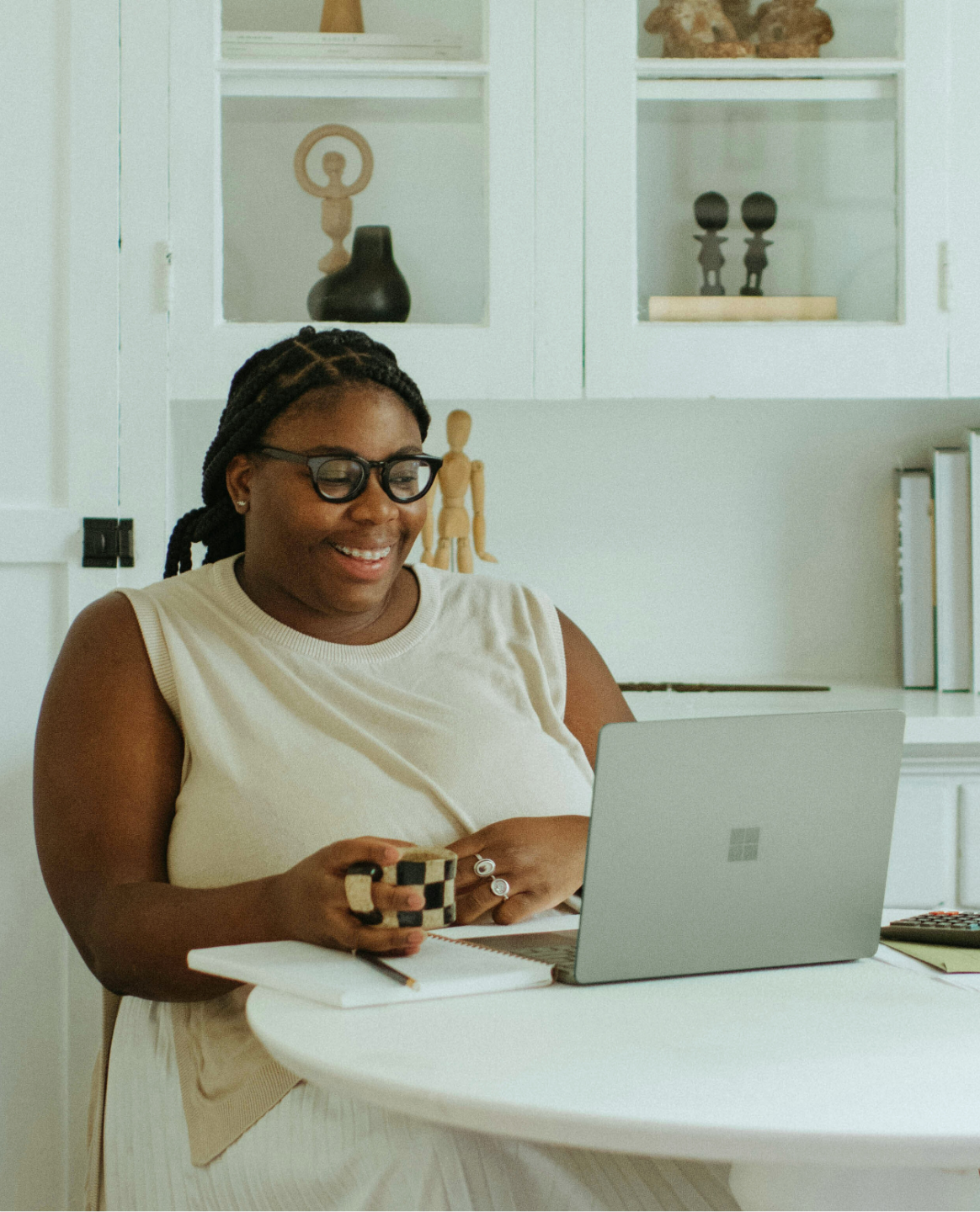
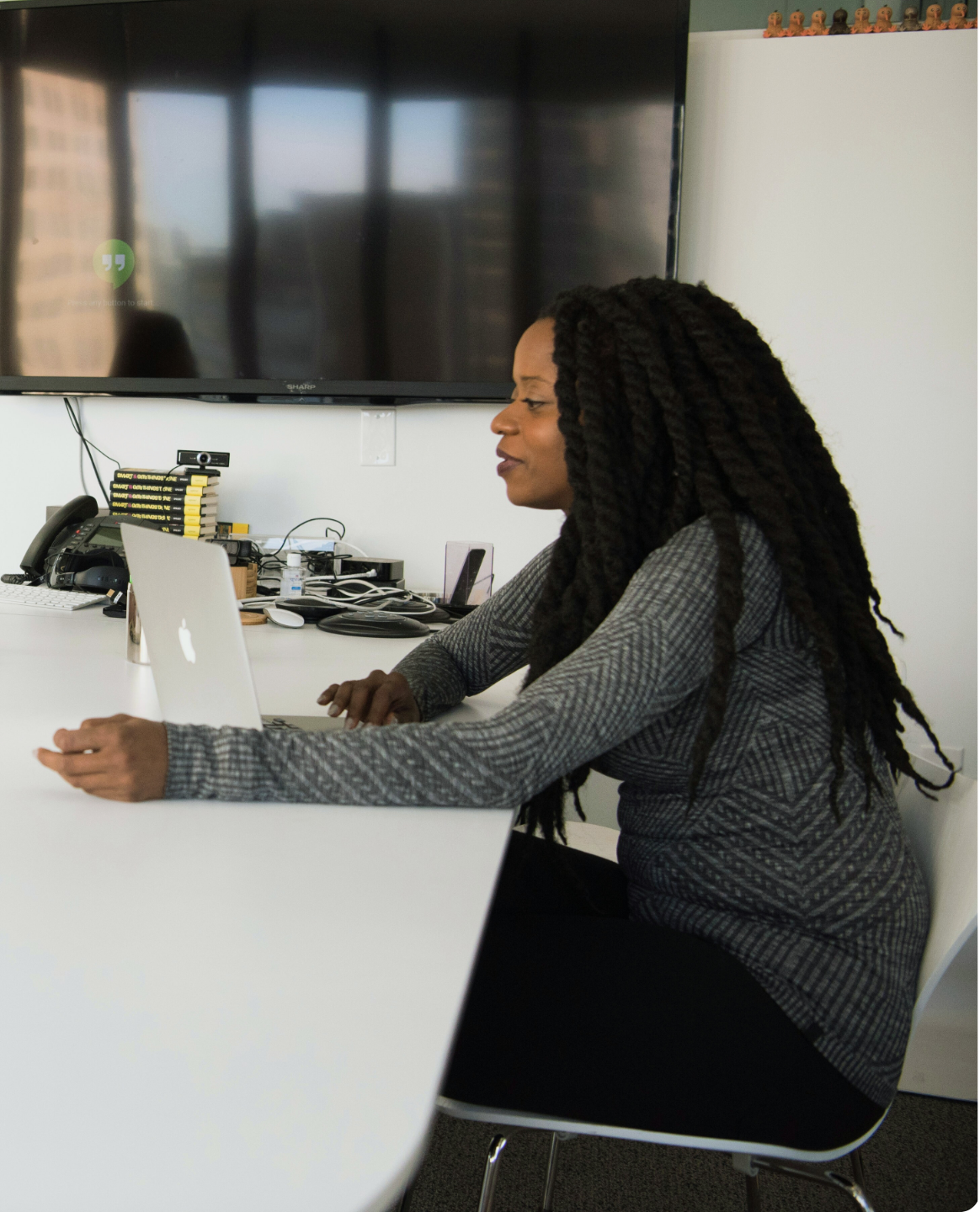
Identify and understand anomalies in real time with in-process inspections, real-time quality monitoring, and root cause analysis.
Digital scrap collection and standardized work instructions prevent defects and reduce waste while simplifying audits and regulatory compliance.
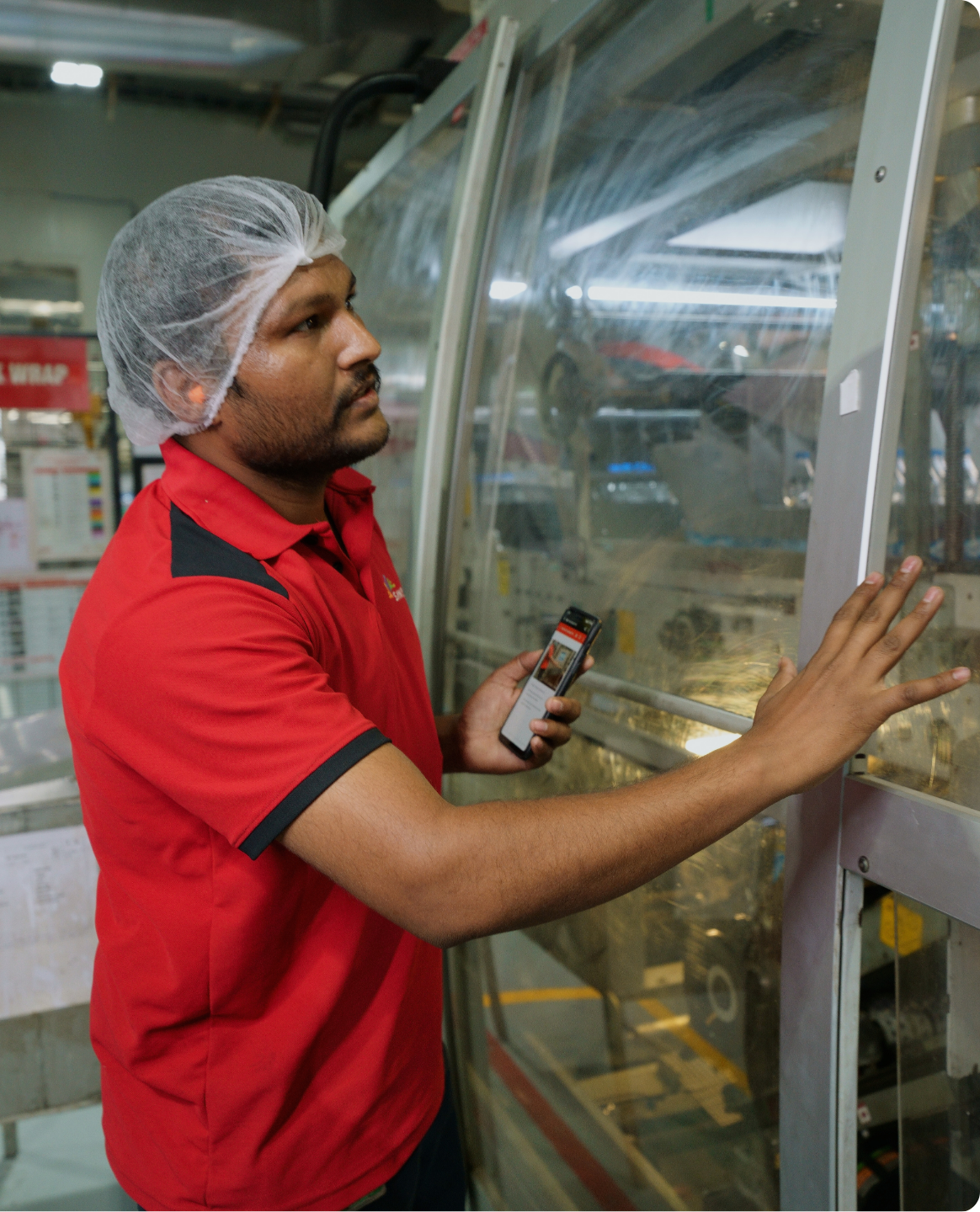
Eliminate quality defects and hit your targets with L2L. Get real-time visibility into quality issues to quickly identify, prioritize, and resolve problems.
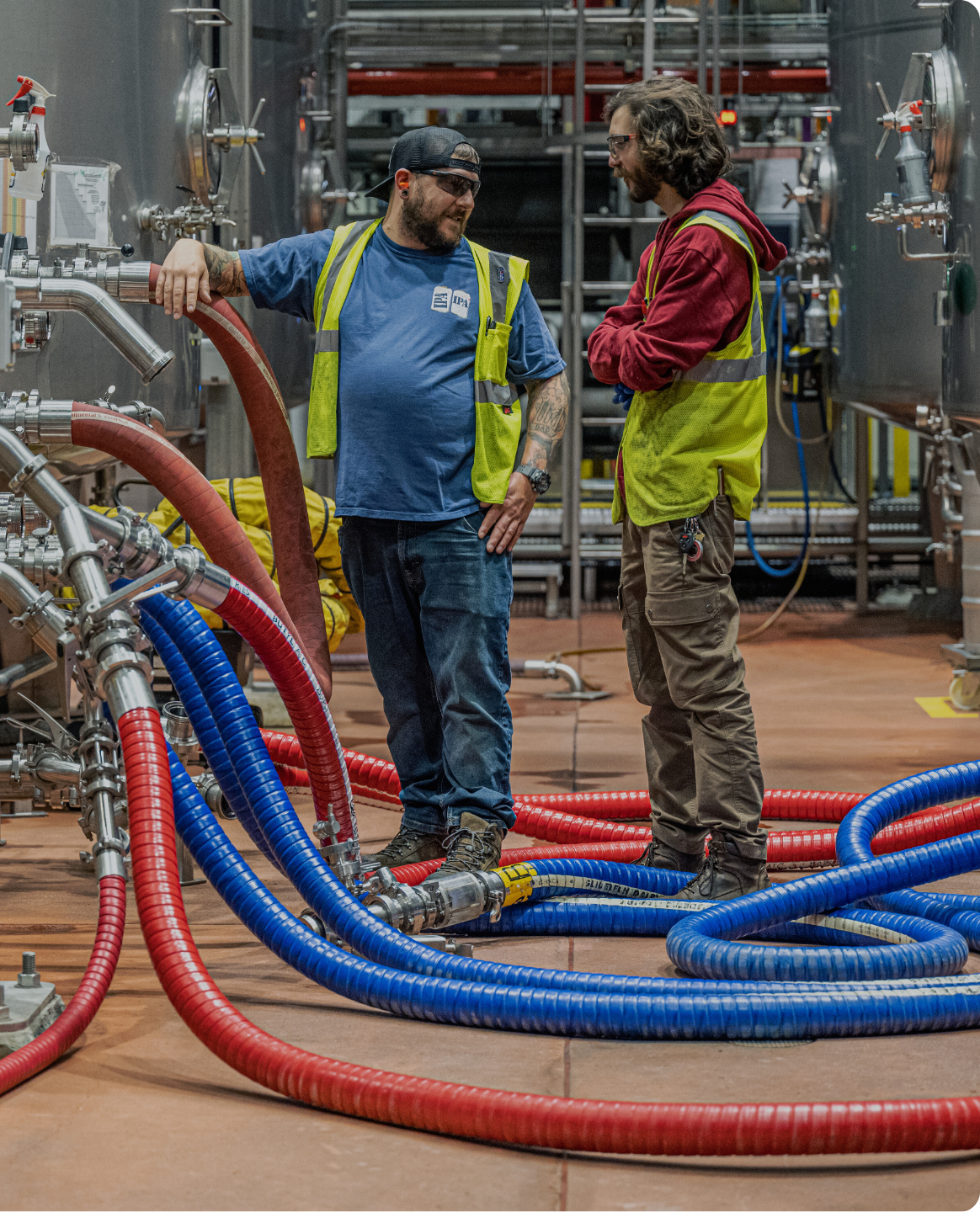
Our Site Reports give manufacturing leaders multi-plant visibility into key quality metrics to benchmark performance, identify trends, and make informed decisions at scale.
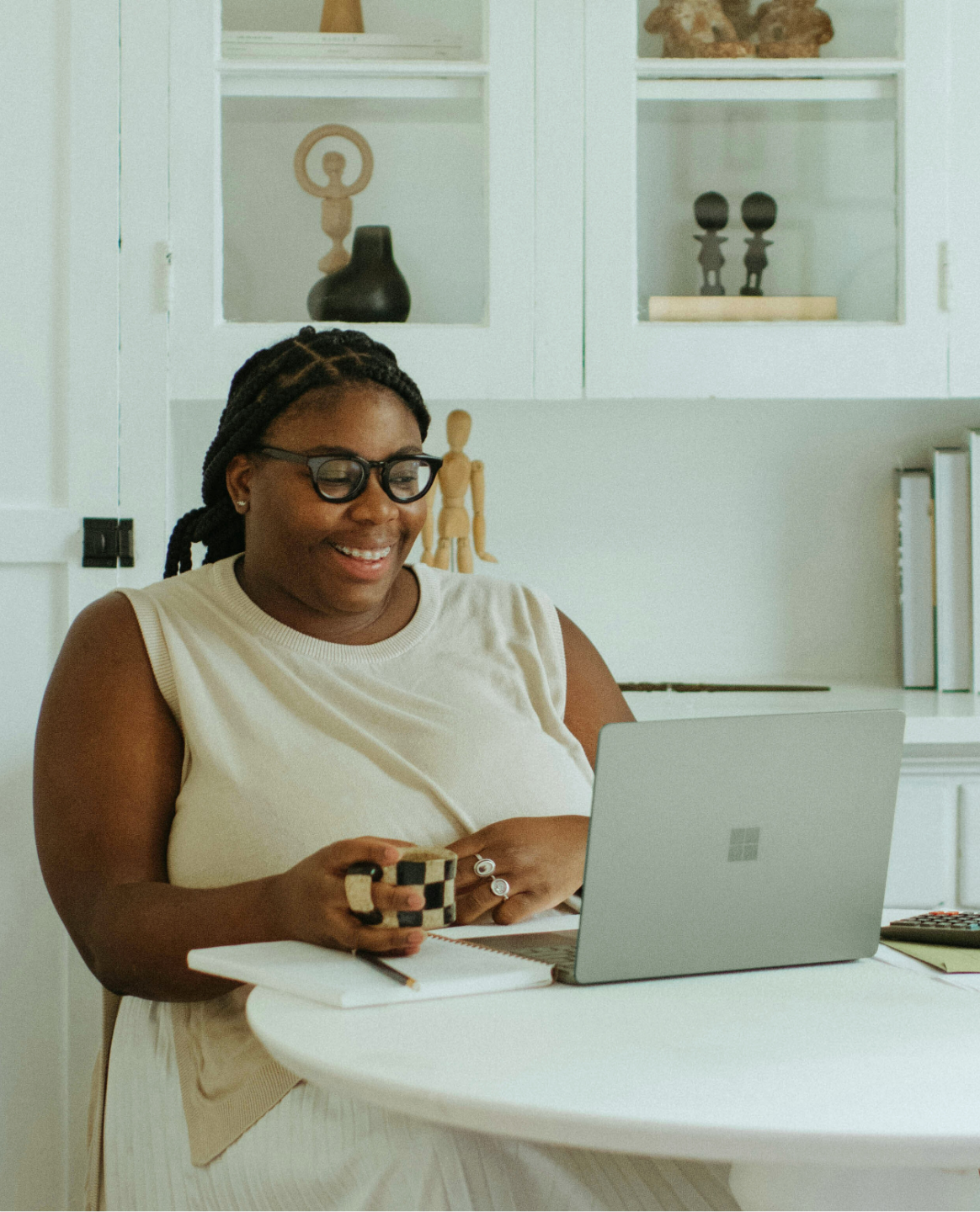
See quality improve within 2 weeks
You’ll see reduced downtime, increased productivity, better quality, and engaged team members.
See it, solve it, go.
Quality flows when teams can find and solve problems without a second thought. L2L delivers the visibility, checks, and standards to reduce defects and improve compliance.
5S and layered process audits
L2L digitizes 5S processes and makes them accessible on the shop floor via mobile-friendly checklists. Layered process audits systematically audit quality at multiple levels, driving standardization and accountability.
Material and issue containment
Make it easy for operators to identify and report problems through Dispatch before they affect your products. Quality checkpoints at every stage of the production process identify anomalies early to contain and solve issues.
Quality checks and alerts
Give everyone the power to identify and solve problems. Digital quality checklists allow the entire frontline to identify any deviances from standards and escalate them immediately for a faster solution.
Rework and scrap management
Reduce waste with our scrap and rework tracking. L2L lets teams capture scrap by machine and categorize waste in real time to proactively identify quality issues.
PCQI compliance
Meet strict compliance standards like Preventive Controls Qualified Individuals (PCQI) while using L2L to streamline the Observation and Corrective Action Reporting (OCAR) process.
Material inspection
L2L elevates material inspection with interactive checklist and SPC features to eliminate material variations and the minor stops they cause on production lines.

Everything our plants could do to improve efficiency, reduce unplanned downtime, drive waste out of the process, and react faster to change are becoming even more critical to keep up with the changing market conditions.
VP of Operations
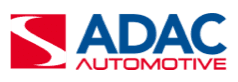
With L2L, ADAC captures and details hundreds of operational activities every day: from lab samples and first part checks to preventative and reactive equipment maintenance, calibrations, and beyond.
VP of Quality
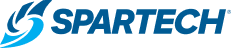
Spartech cut scrap by 10% in the first month by empowering workers to identify the causes of scrap and quickly intervene.
Frequently asked questions
Get answers to your most pressing questions about how L2L improves quality, reduces defects, eliminates scrap, and ensures compliance across your operations.
How does L2L help reduce defects and improve quality?
L2L enables clear visibility to quality issues with real-time monitoring, in-process inspections, and root cause analysis. These tools help teams identify and resolve problems quickly to reduce waste and improve product quality.
Can L2L support compliance and audit readiness?
Yes, L2L digitizes records, inspections, and quality checks to streamline regulatory compliance and ensure audit readiness. This reduces errors and simplifies preparation for even the most stringent audits.
Which quality metrics can L2L track?
L2L tracks essential quality metrics like scrap reasons, yield trends, machine performance, and process variability, providing real-time visibility to help you make data-driven decisions.
Ready to eliminate defects and boost quality?
Discover how L2L’s quality management tools provide real-time insights, reduce scrap, and standardize processes to improve your products and streamline compliance.