DO MORE WITH YOUR DATA
The right information can come from anywhere. And with the right information, your team can make better decisions.
L2L makes it easy to liberate data from existing software systems. Across the array of acronyms and databases—CMMS, MES, QMS, ERP, and PLCs—L2L lets you quickly access the data you need in a single source of truth.
.png?width=960&height=540&name=Integration%20graphic%20(1).png)
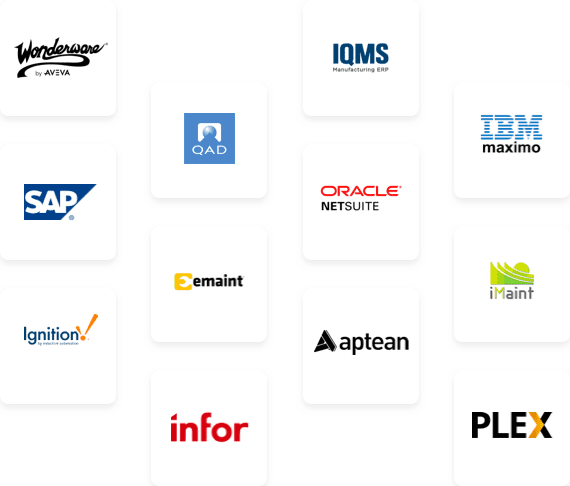
TURN YOUR DATA INTO ACTION
Many shop floor issues stem from each department using different systems and focusing on different KPIs. The underlying data is trapped within systems and can't be used broadly to provide real-time visibility or drive alignment and action across teams.
That's where L2L is different. L2L integrates data from across your systems and presents a "single pane of glass" to your workforce. With a shared view of what's happening, they know what needs to be fixed and when, and who's working on what.
L2L integrates with legacy systems through specific modules (L2L FlowEngine and L2L Connect) and our Open API Library.
TYPICAL INTEGRATIONS
Our customers integrate all sorts of data with L2L to gain real-time visibility across all functions and improve shop floor efficiency.
Typical integration types include:
- ERP: Sync spare parts and inventory levels to increase input transparency.
- MES: Use production and scrap count data to update KPIs, trigger notifications, and enable dynamic scheduling.
- EAM/CMMS: Eliminate silos and share real-time data with production. No more finger-pointing!
- SCADA/OPC: Connect machine-level data with the teams that need it most!
- IIoT: Use IIoT data to monitor real-time conditions and trigger condition-based workflows.
- BI Tools: Export L2L data into your BI solution and merge it with other data for advanced analysis.
- And many more: QMS, LMS, Safety, EH&S—nearly all industrial data can be put to work in L2L!
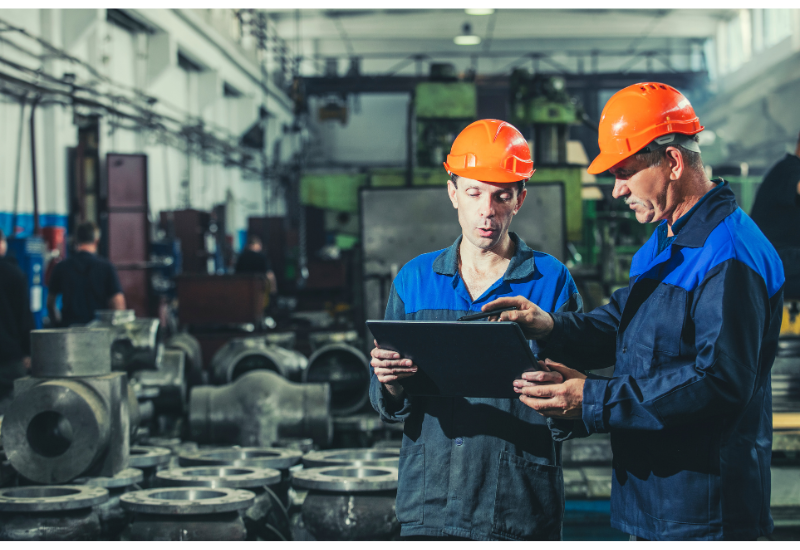
LEARN ABOUT WORTHINGTON INDUSTRIES' DATA INTEGRATION STRATEGY WITH L2L
Worthington Industries (WI) integrated L2L with machine sensors and existing IT/OT systems to form a single view of production metrics previously tracked on whiteboards and spreadsheets. WI also deployed mobile devices and wearables to get the software closer to where the work was done on the shop floor. A cross-functional group of IT, Transformation, Operations, Reliability, Engineering, and Quality worked with L2L consultants to shape the group of technologies into a scalable deployment playbook and maturity model that could be replicated across plants.
DOWNLOAD THE CASE STUDY
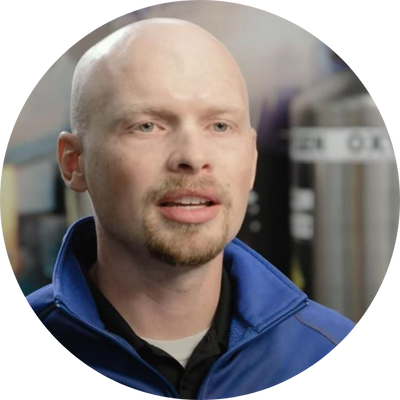
"We’re excited about continuing to tie more things into L2L, automate more things, integrate more things, and ultimately use the power of the system to make our plants more successful. L2L is our smart factory platform moving forward."
- Justin Skaggs, Director, Enterprise Applications, Worthington Enterprises