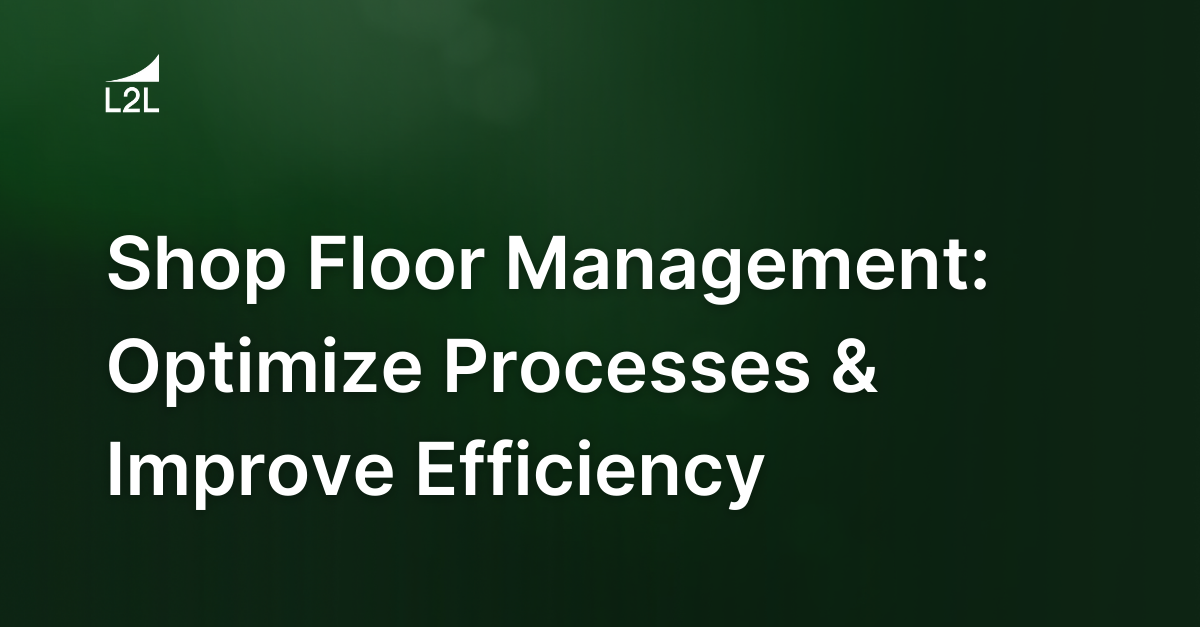
The shop floor is the heart of every manufacturing facility. It’s where people and machines work together to transform raw materials into finished products. Managing the shop floor effectively is crucial for manufacturers to ensure smooth operations, maintain high quality standards, and achieve optimal efficiency.
A systematic approach to shop floor management helps coordinate all the moving parts, from layout planning and workflow optimization to managing people and equipment.
In this article, we will cover how to do all of that and discuss the roles and responsibilities of different personnel, the technologies used to streamline operations, and practical tips to enhance shop floor efficiency.
Let’s start from the top.
What is shop floor management?
Shop floor management refers to the structured approach to overseeing and optimizing the day-to-day operations on the production floor. Its primary goal is to ensure that production runs smoothly, efficiently, and cost-effectively while meeting customer demands and maintaining high-quality standards.
To achieve that goal, shop floor management encompasses a broad range of activities and responsibilities, including:
-
Strategic planning of the shop floor layout
-
Planning, monitoring, and controlling the production processes
-
Managing personnel
-
Maintaining equipment
-
Ensuring that quality and safety standards are met
Effective shop floor management plays a critical role in achieving manufacturing efficiency. It creates a well-coordinated and responsive manufacturing environment where all elements work in harmony to produce high-quality products efficiently.
The key elements of manufacturing shop floor management
Effective shop floor management hinges on several critical elements that need to work together to deliver an optimized production process.
Layout planning
Whether you’re building a new facility or just expanding existing production, strategic layout planning is crucial in maximizing efficiency and minimizing waste on the shop floor.
A well-designed layout ensures that the flow of materials and products is smooth and uninterrupted, reducing unnecessary movement and delays. This not only speeds up the production process but also minimizes the risk of errors and accidents.
A core part of the process is workflow analysis. It involves mapping out each step of the production process to identify the most efficient paths for materials and products through the production process.
Depending on the results of the analysis and other factors, manufacturers will select one of many layouts, such as fixed-position layout, U-shaped layout, or hybrid layout.
Each layout has ideal use cases and comes with a specific set of pros and cons, making this decision all the more important.
Workflow optimization
Optimizing the workflow on the shop floor involves arranging physical operations and the flow of work in a manner that reduces delays, minimizes waste, and ensures a smooth and continuous production process.
Here are the key techniques for workflow optimization:
-
Value Stream Mapping (VSM): Analyzes and designs the flow of materials and information to identify and eliminate waste, creating a more efficient production process.
-
Standardized work: Establishes consistent procedures to ensure quality and reduce errors, making training easier and promoting continuous improvement.
-
Kanban system: Uses visual signals to manage workflow, limiting work-in-progress and visualizing the production process to identify and resolve bottlenecks.
-
Total Productive Maintenance (TPM): Focuses on proactive maintenance to maximize equipment productivity, reducing downtime and ensuring a smoother workflow.
-
5S methodology: Helps organize the workplace in a way that reduces waste, improves safety, and boosts productivity.
As a part of workflow optimization, manufacturers should also look at their parts and product inventory management processes in order to prevent or eliminate any logistics issues.
Equipment management and maintenance
The more machine downtime there is, the less work is being done, resulting in lower output. A robust maintenance strategy can significantly enhance productivity and prolong the lifespan of machinery.
The best way to reduce downtime is to focus on proactive maintenance. The two most common strategies are preventive and predictive maintenance. However, choosing the right maintenance strategy is just one part of the equation.
Effective production management requires that production and maintenance teams work together closely. This means coordinating production and maintenance schedules, involving operators in asset care, and promoting collaboration instead of competition between these two teams.
Roles and responsibilities in production shop floor management
Effective shop floor management relies on the clear definition and execution of various roles and responsibilities:
-
Team leaders: Team leaders are responsible for setting daily priorities, managing personnel, maintaining a safe working environment, and ensuring that production targets and quality standards are met. They coordinate activities on the shop floor, resolve issues as they arise, and provide guidance to their teams.
-
Machine operators: Machine operators are responsible for operating machinery safely and efficiently. Their duties typically include setting up equipment, monitoring production processes, and reporting any quality or equipment issues they find.
-
Maintenance staff: Maintenance staff are essential for keeping equipment in optimal working condition. They help install new equipment, perform routine maintenance, and troubleshoot and repair broken machinery.
-
Production planners: Production planners develop and manage production schedules to ensure that production targets are met while optimizing resource use. They coordinate with other departments, such as procurement and logistics, to ensure that materials are available when needed.
-
Logistics coordinators: These coordinators are responsible for managing the flow of materials and products within the production process. They oversee inventory levels, coordinate the movement of materials between different stages of production, and ensure that finished products are properly stored and shipped.
With so many different roles involved in the production process, interdepartmental coordination and communication are essential for optimizing shop floor performance and crucial for aligning production processes, quickly resolving issues, and meeting operational goals.
7 ways to improve shop floor efficiency
Most discussions about shop floor management inevitably end with trying to find the best ways to improve shop floor efficiency. Below is a list of seven different approaches that can work in almost any production setting.
The concept of standard work has long been a staple of continuous improvement. Standardizing work procedures helps maintain consistency, reduces errors, and improves efficiency on the shop floor.
It can be implemented in just two steps:
-
Develop Standard Operating Procedures (SOPs): Create detailed SOPs for all tasks on the shop floor. These documents should outline the best practices, steps, and quality standards for each process.
-
Make those SOPs digital: Use digital work instructions to make SOPs more accessible and easier to maintain. This will also help workers follow procedures more accurately and simplify training for new employees.
SOPs are usually developed for repetitive tasks performed by operators, technicians, and similar roles. And to some degree, there are ways to streamline work for their team leaders as well. Learn how in our full guide to leader standard work.
2. Track and analyze your KPIs
Tracking and analyzing Key Performance Indicators (KPIs) is vital for understanding how well your shop floor operations are performing and identifying areas for improvement. KPIs provide measurable values that help gauge the efficiency and effectiveness of production processes.
First, you need to identify KPIs that are most relevant to your operations. Manufacturers will often look at:
-
Cycle Time: The total time from the beginning to the end of a process.
-
Throughput: The amount of product produced in a given period.
-
Quality Rates: The percentage of products that meet quality standards without rework or scrap.
-
Production Downtime: The amount of time production is halted due to maintenance, breakdowns, or other issues.
-
Overall Equipment Effectiveness (OEE): A measure of how well equipment is performing relative to its full potential, considering availability, performance, and quality.
-
Scrap Rate: The percentage of materials that are wasted or deemed unusable during the production process.
Regardless of the metrics, every manufacturer aims to gather and analyze as much operations and production data as they can to make data-driven decisions. After all, understanding the root causes of performance issues is the only way to implement targeted improvements.
3. Implement lean manufacturing principles and tools
For a manufacturing facility, being lean means eliminating waste from production processes. There are numerous ways to do that. We recommend following the basic lean manufacturing principles.
On top of that, manufacturers should also look into lean tools such as Andon, Heijunka, Jidoka, Kanban, Kaizen, 5S, and Poka-Yoke. Some of them will be crucial for creating a leaner production floor.
4. Invest in employee training
There is no better way to improve safety and productivity on the shop floor than having a skilled workforce. Key are some key aspects of effective employee training:
-
Role-specific training: Ensure employees receive comprehensive training tailored to their specific roles. This includes understanding the machinery they operate, the processes they follow, and the quality standards they must meet.
-
Safety training: Regular safety training is crucial to minimize accidents and ensure a safe working environment.
-
Cross-training: Encourage cross-training to increase workforce flexibility. It enables workers to fill in for absent colleagues, adapt to changing production needs, and contribute to different stages of the production process.
-
Onboarding programs: Develop structured onboarding programs for new hires to ensure they are quickly integrated into the team and understand their responsibilities.
-
Feedback and performance evaluation: Regularly evaluate employee performance and provide constructive feedback. Identify areas where additional training may be needed and recognize employees' achievements.
By investing in comprehensive and continuous employee training, manufacturers can build a knowledgeable, versatile, and motivated workforce.
5. Utilize automated solutions
When they can leave certain repetitive tasks to a machine, workers are able to focus on more complex and value-added activities.
Since machines are more precise and less prone to errors, it’s no surprise to see manufacturers using them for tasks such as assembly, welding, material handling, and product quality control.
How represented they should be on your production floor will ultimately depend on the price of the technology and the volume of work you can automate this way.
6. Optimize layout and material flow
Optimizing the layout and material flow on the shop floor is crucial for maximizing efficiency and minimizing waste. Here is a list of key things to focus on:
-
Strategic layout design: Design the shop floor layout to minimize the distance materials and products need to travel. Position workstations and equipment in a logical sequence to streamline the production process.
-
Minimal movement: Arrange equipment and workstations to minimize unnecessary movement of materials and workers. Reducing travel distances decreases cycle times and improves overall efficiency.
-
Lean manufacturing principles: Apply lean manufacturing principles such as cellular manufacturing and line balancing. These techniques help create a more efficient flow by grouping similar processes and ensuring balanced workloads across stations.
-
Visual management tools: Use visual management tools like floor markings, color-coded areas, and signage to clearly indicate material flow paths and workstation locations. Consider implementing Andon as well.
7. Foster a culture of continuous improvement
Fostering a culture of continuous improvement is essential for driving long-term efficiency and innovation on the shop floor. Outside of regular employee training which we already covered, here are some additional ideas to consider:
-
Encourage employee involvement: Create an environment where employees feel empowered to suggest improvements. Regularly solicit feedback and ideas from staff, as they are often best positioned to identify inefficiencies and potential solutions.
-
Implement Kaizen practices: Kaizen philosophy focuses on making small, incremental changes that collectively lead to significant improvements. Organize regular Kaizen events or workshops to address specific areas for improvement.
-
Establish clear goals and metrics: Set clear, achievable goals for continuous improvement efforts and track progress using relevant metrics. Regularly review these goals and adjust strategies as needed to ensure ongoing progress.
-
Celebrate successes: Motivate employees by recognizing and rewarding them for their contributions to continuous improvement.
-
Promote open communication: Maintain open lines of communication across all levels of the organization. Encourage transparency and information sharing to ensure that everyone is aware of ongoing improvement efforts and their impact.
Encouraging employees at all levels to contribute ideas and participate in improvement initiatives often results in finding opportunities for optimization that would otherwise be flown under the radar.
Technology used to streamline shop floor operations
There are many digital technologies and systems manufacturers use to get real-time insights and data they need to optimize shop floor operations. The most common ones are:
-
Enterprise Resource Planning (ERP) systems: Used to integrate business processes like inventory control, order processing, and production scheduling for seamless information flow and improved decision-making.
-
Manufacturing Execution Systems (MES): Used to monitor and control production in real-time, providing insights into machine performance, production status, and quality control to enhance decision-making.
-
Maintenance software (EAM or CMMS): Used to manage maintenance activities by scheduling preventive maintenance, tracking repairs, and managing spare parts inventory to reduce downtime and extend machinery lifespan.
-
Collaborative Floor Workflow (CFW) Tools: Used to facilitate communication and collaboration with digital workboards, mobile apps, and messaging platforms for real-time updates and task management.
The good news is that most of these solutions can be replaced with connected workforce software like L2L, minimizing the number of tools manufacturers need to use to streamline production and shop floor operations.
Optimize people and production with L2L’s connected workforce platform
The L2L Connected Workforce Platform offers a comprehensive solution that helps manufacturers achieve optimal efficiency and productivity on the shop floor by connecting people, processes, and data in a seamless, integrated system.
It empowers employees with lean tools and the data they need to take ownership of their tasks and contribute to continuous improvement initiatives. Furthermore, robust maintenance management features help schedule and track preventive and predictive maintenance, minimizing unexpected equipment failures and maintaining smooth production flow.
Here’s how Dart Container, the world's largest manufacturer of foam cups and containers, used L2L to improve productivity and efficiency across its production process:
In this short video (3:45), hear how Dart Container increased uptime by streamlining its processes with L2L's connected workforce software.
To learn more about how L2L can transform your shop floor operations and drive continuous improvement, contact our team for a personalized demo or take our interactive product tour.
Revisions
Original version: 5 June 2024
Written by: Evelyn DuJack
Reviewed by: Daan Assen
Please read our editorial process for more information
Subscribe to Our Blog
We won't spam you, we promise. Only informative stuff about manufacturing, that's all.