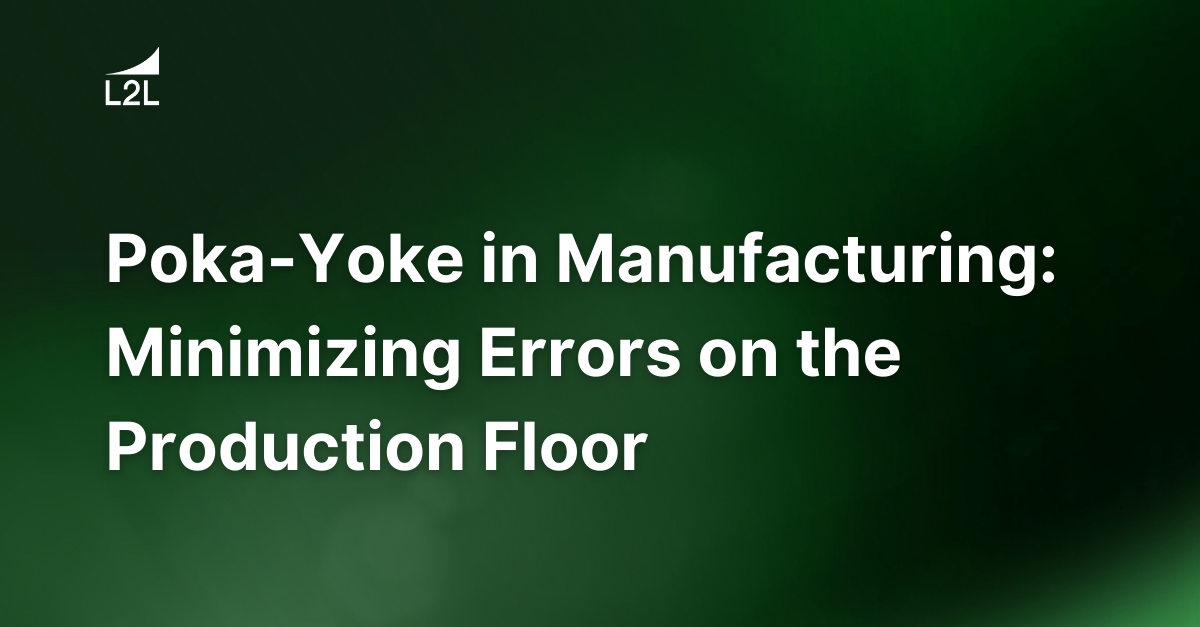
In a factory, a single mistake can have costly ripple effects, from unplanned downtime to defective products. Automation technology has dramatically improved precision and accuracy in manufacturing processes, but there’s still potential for error even in the most high-tech facilities.
This is why poka-yoke — or an extra layer of “mistake-proofing” — is still as relevant as ever.
In this article, we explain types of poka-yoke, use cases, and practical ways manufacturers can implement this concept on their shop floors.
What Is Poka-Yoke?
Poka-yoke is a Japanese term that means “mistake-proofing” or “fail-safing.” In lean manufacturing, it refers to techniques used to quickly identify and fix mistakes in the production process, if not prevent them.
In other words, poka-yoke aims to create processes, operations, or products in a way that makes it impossible or very difficult to make mistakes. There are two main types of poka-yoke systems:
-
Warning poka-yoke: A process that alerts operators to occurring or soon-to-occur defects. It relies on human intervention to stop and correct errors; therefore, it doesn’t stop processes automatically.
-
Control poka-yoke: This type of poka-yoke relies on automation to stop or prevent errors in a manufacturing process. It takes control away from the operator, stopping the system until the error is corrected.
Factors like the nature of certain errors, their criticality, and overall implementation costs often determine whether a facility relies more on one approach or the other.
The Benefits of Poka-Yoke
Applying poka-yoke principles to production processes results in greater efficiency, productivity, safety, and even cost savings. Here are the primary benefits of poka-yoke in manufacturing:
-
Time saved during training: Poka-yoke simplifies processes, making them easier to understand and perform, significantly reducing the time required for training new employees.
-
Promoting a culture of continuous improvement: By identifying and addressing defects at the source, poka-yoke encourages workers to constantly seek ways to improve processes and product quality.
-
Improving safety: With more and better error-prevention mechanisms, poka-yoke reduces the risk of accidents and injuries in the workplace.
-
Reduced waste: Minimizing errors in the manufacturing process leads to less rework and scrap — reducing waste and saving resources.
-
Increased productivity: Streamlining operations and minimizing errors enhance efficiency, which allows for more output in less time.
-
Better quality control: Poka-yoke ensures that products meet quality standards consistently, leading to higher customer satisfaction and lower costs associated with defects.
By preventing and promptly addressing errors, manufacturers significantly improve production metrics while minimizing scrap and safety incidents.
Use Cases and Examples of Poka-Yoke in Manufacturing
Poka-yoke techniques can be applied to the production process in many ways. Below is a list of the most common types of manufacturing errors and how they can be solved using poka-yoke.
Preventing processing errors
In manufacturing, processing errors result from incorrect operations — such as misassembled parts, incorrect machine settings, and improper process follow-through.
Poka-yoke eliminates processing errors by designing systems that make it impossible (or highly unlikely) for these mistakes to occur. This typically includes implementing fail-safes where these issues would naturally occur.
For example, in assembly lines, poka-yoke reduces error by using uniquely shaped connectors, ensuring parts fit only in their correct places, much like a shape-sorter toy. There can also be sensors to verify correct component placement, immediately alerting operators if the placement is incorrect.
Preventing setup errors
Poka-yoke helps prevent setup errors on the shop floor by implementing foolproof mechanisms, such as color-coded components, guided checklists, and automated sensors. These tools ensure equipment is correctly configured before operation, reducing downtime, scrap, and costly mistakes.
For instance, industrial color coding is applied to tools, equipment, and materials to reduce production errors. Color-coded bins for machine parts — red for defective, green for approved — immediately signal to workers where to place or retrieve items. This simple poka-yoke application prevents workers from mixing defective parts with usable ones, thus enhancing efficiency and quality control.
Preventing errors related to missing parts
Using poka-yoke tactics like integrating sensor-based checkpoints in production lines, you can eliminate errors caused by missing parts. These sensors detect the absence of required components before the next manufacturing stage begins. If a part is missing, the system halts, signaling the need for correction.
In an automotive assembly line, a poka-yoke method involves setting up a sensor system that counts the number of components, like bolts or connectors, as they’re added to an engine. If the sensor detects that a part hasn’t been installed by the time it reaches a certain point, the assembly line automatically stops.
This halts production until the missing component is added, ensuring no car moves forward without all necessary parts properly installed.
Preventing errors caused by improper parts or components
Poka-yoke techniques can prevent the use of incorrect parts by making it physically impossible to proceed with assembly. Again, this can be achieved through mechanisms like color-coding or uniquely shaped components that only fit intended slots or connections.
In a bicycle manufacturing plant, poka-yoke can be applied to engineering screw threads, which vary by direction and pitch for different parts of the bicycle. For instance, pedals have left- and right-hand threads corresponding to each side of the bike so can only be screwed into the correct side.
Preventing operational errors
Poka-yoke techniques prevent operational errors on the factory floor by introducing fail-safes, like automated alarms and visual indicators, which alert operators to deviations from standard procedures.
For instance, LED status lights on machinery can alert operators to non-compliance with protocols. A green light could indicate normal operation, whereas yellow could indicate minor issues requiring attention, and red could signal critical problems or stoppages. This immediate, easy-to-interpret feedback enables operators to quickly identify and address issues, reducing downtime and maintaining production flow and safety standards.
Preventing measurement errors
Poka-yoke techniques also minimize measurement errors on the shop floor by employing tools with built-in guides and stops that ensure precise measurement every time. These techniques can be used for many types of measurement — such as dimension, mass, or temperature.
For instance, jigs with preset dimensions for cutting or assembling parts automatically align materials to the correct specifications, eliminating the possibility of deviation. This approach guarantees accuracy, reduces waste, and enhances the consistency of the final product.
Implementing Poka-Yoke in a Production Environment
Now that we’ve explored the concept of poka-yoke and how it can prevent errors in a factory setting, it’s time to outline practical steps for implementing this approach in your facility.
The practice of poka-yoke will look slightly different for every manufacturer. Still, there are some general steps most manufacturers should follow:
Step 1: Identify the problem
The first step to implementing poka-yoke is pinpointing where errors occur in your production processes. This will help your teams identify the nature of the problem.
-
Is it a flaw in the production process?
-
Is it human error?
-
Is it something a slightly different product design could fix?
Now is the time to observe your processes and find out.
Step 2: Identify the root cause of the problem
Once you identify where the problem is happening, it’s time to understand why the problem occurred.
There are many root cause analysis techniques you can use to find the source of the problem. One common way to do it is by using the 5 “whys” method.
For example, if a roller in a plastic manufacturing facility stops unexpectedly, you could ask the following questions:
-
Why did the roller stop? The material jammed.
-
Why did the material jam? The rollers weren’t aligned correctly.
-
Why were the rollers misaligned? Wear and tear made the rollers shift.
-
Why wasn’t the wear and tear addressed earlier? Inadequate maintenance practices.
-
Why did maintenance teams miss this? Checking rollers wasn’t regularly scheduled.
Now, you can create a poka-yoke to prevent this instance of inadequate maintenance from recurring.
Step 3: Determine the most appropriate poka-yoke method to use
If you can easily prevent mistakes from happening, install a control poka-yoke that prevents the process from continuing until a vital step is completed. For example, components can be shaped in such a way that makes it impossible for a product to be assembled incorrectly.
If you can’t prevent a mistake, install a warning poka-yoke that alerts the operator that attention is needed before the process can continue. These warnings can include colors, flashing lights, buzzers, or any type of alerts that tell the employee that something needs to happen before the process continues.
Step 4: Test your new poka-yoke system with a pilot project
After you’ve mapped out your new poka-yoke system and selected the right mechanisms to facilitate it, it’s time to test it on a small scale. A poka-yoke pilot project will help you iron out any issues with the process before introducing it to your shop floor.
Choose a single production line or a specific machine for the pilot. Implement the designed poka-yoke measures in this controlled environment. This allows for close monitoring of the process and makes it easier to adjust or refine the solutions based on actual results.
Make sure to train workers involved in the pilot on the proper steps and objectives of your poka-yoke test, and define and measure metrics essential to determining the effectiveness of your system.
Step 5: Train workers and update your SOPs
After completing a successful pilot, it’s time to fully implement your poka-yoke system. Train your workforce in the new methodology; this can sometimes involve a combination of cross-training and upskilling, depending on the degree of changes implemented.
As you train your workers, remember to update your standard operating procedures (SOPs) to reflect any process changes. Keeping your SOPs up-to-date with current shop floor procedures eliminates confusion and prevents old errors from recurring. Think of proper documentation as another form of poka-yoke.
Support Poka-Yoke Implementation with L2L
One of the most effective ways to support poka-yoke in your manufacturing facility is to ensure that workers have access to real-time machine and process data. Connected workforce platforms like L2L can be used to detect operational and process errors in real time and provide a central hub for error documentation.
Easy-to-understand dashboards help managers visualize opportunities for performance improvement on the shop floor, helping managers identify root causes, implement changes using poka-yoke, and track the effectiveness of those changes.
Check out our free ROI calculator to see how L2L can help your plant save time and money.
Revisions
Original version: 20 February 2024
Written by: Evelyn DuJack
Reviewed by: Daan Assen
Please read our editorial process for more information
Related Posts
Subscribe to Our Blog
We won't spam you, we promise. Only informative stuff about manufacturing, that's all.