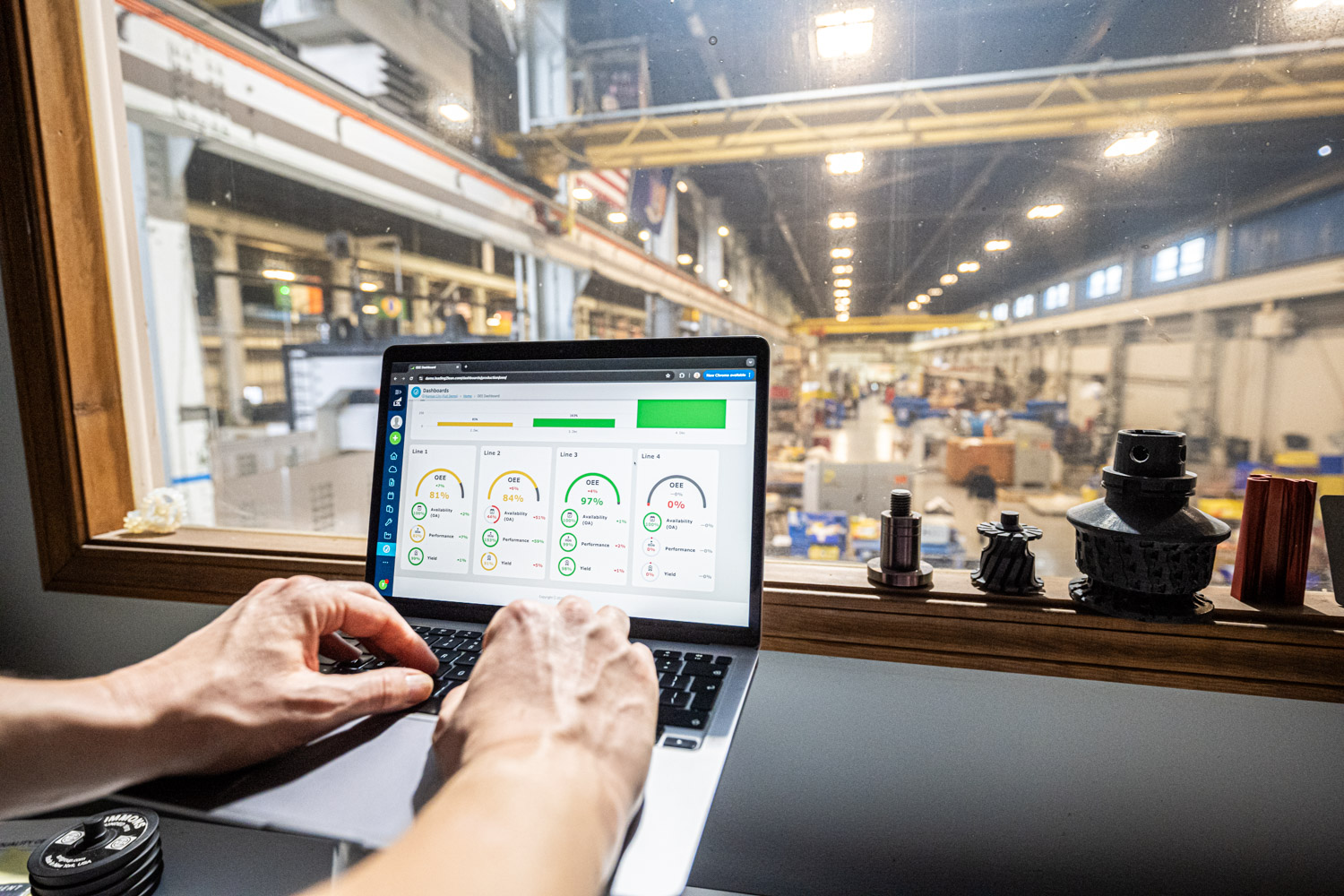
With more and more manufacturers investing in new technology and equipment, getting the most out of your production process has never been so important.
High production efficiency can lead to significant cost savings and improved profitability. Manufacturers who master it not only optimize their operations but also position themselves for long-term success.
In this guide, we explore the concept of production efficiency, showcase various measurement methods, and present actionable strategies manufacturers can use to achieve higher efficiency in production.
What is production efficiency?
Production efficiency can have different meanings depending on the context in which it's used. To make sure we're on the same page, let’s look at the two most common definitions.
Productive efficiency as an economic concept
Productive efficiency, as an economic concept, refers to a situation where an economy or a business is operating at its maximum potential, using all available resources in the best possible way.
In this state, it is impossible to produce more of one good (read product) without reducing the output of another. This concept is closely tied to the idea of the production possibilities frontier (PPF), which illustrates the trade-offs between different goods or services that an economy can produce.
The visual representation of the PPF curve on a graph. Source: Educba
In simpler terms, productive efficiency occurs when a company or economy is producing goods and services at the lowest possible cost. Every resource — whether it’s labor, capital, or raw materials — is being used to its fullest potential, and no resources are wasted.
Production efficiency in a manufacturing context
In manufacturing, production efficiency refers to the ability to convert inputs (raw materials, labor, energy) into outputs (finished products) in the most effective way possible. This involves optimizing processes to ensure that resources are used with minimal waste, downtime, and inefficiency while maintaining product quality.
Manufacturing production efficiency is not just about producing goods quickly — it’s about striking the right balance between speed, quality, and cost.
The key to improving production efficiency lies in continuously analyzing and refining production processes. This can involve automating certain tasks, reorganizing workflows, and investing in better equipment or technology.
Production efficiency vs manufacturing efficiency
While the terms "production efficiency" and "manufacturing efficiency" are often used interchangeably, they aren't exactly the same.
Production efficiency is a broader concept that encompasses all activities involved in creating a product, from sourcing raw materials to delivering the finished goods. Its focus is on overall resource utilization and process optimization across the entire production process.
Manufacturing efficiency, on the other hand, is more specific to the manufacturing floor. It concentrates on the effectiveness of the manufacturing processes themselves — how well machines are used, how efficiently labor is deployed, and how quickly and accurately products are assembled.
In essence, manufacturing efficiency is a subset of production efficiency. While production efficiency takes a holistic view of the entire production chain, manufacturing efficiency zeroes in on the actual process of making the product.
Factors affecting the efficiency of production
Many internal and external factors can influence production efficiency. Let’s quickly go through the most impactful ones.
Internal factors:
-
Quality of raw materials: High-quality materials reduce defects and waste, leading to more efficient production.
-
Workforce skill level: A well-trained workforce operates machinery more effectively and responds quickly to issues.
-
Equipment performance: Well-maintained and modern equipment runs more efficiently, minimizing downtime and errors.
-
Production floor layout: An optimized layout reduces movement and time wasted, enhancing overall productivity.
-
Process efficiency: Streamlined and well-designed production processes reduce bottlenecks and improve workflow.
External factors:
-
Supply chain reliability: A dependable supply chain ensures a steady flow of materials, preventing production delays.
-
Market demand: Fluctuations in demand can influence production scheduling, affecting efficiency.
-
Regulatory requirements: Compliance with regulations may require changes in processes or equipment, potentially impacting efficiency.
-
Economic conditions: Economic factors such as inflation, currency fluctuations, and labor costs can affect production efficiency.
-
Technological advancements: New innovations can offer opportunities for process improvements or pose challenges if not adopted.
Understanding these factors can help you prioritize areas for improvement and develop strategies to mitigate any inefficiencies.
Methods and formulas for measuring production efficiency
There is no single metric that perfectly captures production efficiency. Manufacturers can (and should) use various methods and formulas to better understand how well their resources are being utilized.
To do that effectively, you need accurate data. This is why software solutions that collect real-time data on production processes — like MES, ERP, and CMMS — play a critical role in tracking efficiency.
Calculate efficiency based on capacity utilization
Capacity utilization measures how effectively a manufacturing facility is using its production capacity.
This formula provides the capacity utilization rate as a percentage, showing how much of the available capacity is being utilized.
Example: Suppose a factory has a maximum production capacity of 10,000 units per month. In a given month, the factory produces 8,000 units.
Capacity Utilization = (Actual Output / Maximum Possible Output) x 100
Capacity Utilization = (8,000 / 10,000) x 100
Capacity Utilization = 80%
This means the factory is operating at 80% of its total capacity, indicating relatively efficient use of its production resources. However, there may still be room for improvement, depending on demand and other factors.
Track efficiency through OEE
Overall Equipment Effectiveness (OEE) is a comprehensive metric that measures the efficiency of manufacturing processes by evaluating how effectively equipment is utilized. OEE takes into account three key factors: Availability, Performance, and Quality. It provides a clear and actionable picture of where losses are occurring and how well a manufacturing process is running.
Each of the three metrics has to be calculated separately before you can plug them into the OEE formula. Here’s a guide on OEE calculation for those who want to see an example.
The final result is expressed as a percentage, with 100% representing perfect efficiency. Hence, an OEE score of 76% indicates that 76% of the total manufacturing time was truly productive. The remaining 24% was lost due to issues like downtime, slow cycles, and defects.
The formulas for calculating OEE are simple. The hard part is getting the right data. Ideally, you should automate the whole process with software. Here’s how manufacturers use the L2L platform to track efficiency across time, production facilities, and even production lines:
Track efficiency based on yield rate
Yield rate measures the proportion of good products produced compared to the total number of products started. It provides insight into the effectiveness of the manufacturing process in terms of quality and waste reduction.
This formula gives the yield rate as a percentage, showing the ratio of good units to the total units produced.
Example: Suppose a production line produces 1,000 units in a day, but 50 units are found to be defective.
Yield Rate = (Number of Good Units / Total Units Produced) x 100
Yield Rate = (950 / 1,000) x 100
Yield Rate = 95%
This means that 95% of the units produced met the quality standards, while 5% were either defective or required rework.
A high yield rate is a clear indicator of production efficiency because it shows that the manufacturing process is producing a high percentage of acceptable products with minimal waste.
Calculate manufacturing cycle time efficiency
Manufacturing cycle time efficiency measures how efficiently a product moves through the production process from start to finish. This metric is crucial for understanding how well the production process is optimized in terms of time. It helps identify bottlenecks, delays, and inefficiencies that can slow down the production cycle and increase costs.
Cycle time efficiency uses two variables:
-
Value-Added Time is the time spent on activities that directly contribute to transforming raw materials into finished goods.
-
Total Cycle Time includes both value-added time and non-value-added time (such as waiting, transportation, and delays).
Example: Imagine the total cycle time to produce a product is 10 hours, but the value-added time (the time actually spent working on the product) is 6 hours.
Cycle Time Efficiency = (Value-Added Time / Total Cycle Time) x 100
Cycle Time Efficiency = (6 hours / 10 hours) x 100
Cycle Time Efficiency = 60%
Improving manufacturing cycle time efficiency involves reducing the non-value-added time through process optimization, better scheduling, and reducing downtime.
Strategies for increasing productivity and efficiency in production
Improving production efficiency is an ongoing process that requires a combination of strategic planning, continuous improvement, and the adoption of best practices. Let’s review some practical strategies that can help you improve efficiency on the shop floor.
1. Process optimization
The goal of process optimization is to eliminate inefficiencies, reduce waste, and enhance output quality. By streamlining operations, manufacturers can maximize resource utilization and minimize production costs.
You can do this in many different ways:
-
Standard Operating Procedures (SOPs): Standardizing work helps reduce variability in processes, improve quality control, and make it easier to train new employees. Make SOPs easy to use by digitizing them and including one-point lessons.
-
Total Quality Management (TQM): TQM is a comprehensive approach that focuses on continuous improvement in all aspects of production. It involves the systematic identification and elimination of defects and inefficiencies.
-
Bottleneck analysis: By analyzing production flows and identifying bottlenecks, manufacturers can take targeted actions — such as reallocating resources or redesigning workflows — to eliminate delays and increase throughput.
2. Lean manufacturing
Lean manufacturing is a systematic approach to minimizing waste without sacrificing productivity. It focuses on delivering value to the customer by eliminating activities that do not add value to the product.
Lean manufacturing employs strategies like value stream mapping, JIT production, continuous improvement, 5S, Poka-Yoke, Andon, and Kanban to streamline operations, reduce costs, and improve efficiency.
3. Supply-chain optimization
By refining and improving the supply chain, manufacturers can minimize delays and ensure a steady flow of materials, leading to smoother and more efficient production processes.
Key areas to focus on include:
-
Supplier relationship management: By working closely with suppliers, manufacturers can negotiate better terms, improve communication, and resolve issues quickly, which helps prevent material shortages or quality issues.
-
Inventory management: Effective inventory management ensures that the right amount of materials is available when needed. Avoid overstocking or understocking by investing in demand forecasting and using safety stock calculations.
-
Logistics optimization: Efficient production requires that materials move smoothly through the supply chain. Optimizing transportation routes, selecting the right carriers, and leveraging technology for real-time tracking can reduce lead times, lower transportation costs, and improve overall supply chain reliability.
-
Cross-functional collaboration: Encouraging collaboration between different departments, such as procurement, production, and logistics, can lead to better decision-making and more efficient operations.
By investing in supply chain optimization, manufacturers can create a more resilient and efficient production process.
4. Workforce development
A well-trained, motivated, and versatile workforce can significantly impact the effectiveness of production processes.
You can achieve that through:
-
Training programs: Regular upskilling ensures employees are proficient in the latest technologies, processes, and best practices. This reduces the likelihood of mistakes, fosters innovation, and lowers the number of safety accidents.
-
Employee engagement and motivation: Motivated employees are more likely to take initiative, suggest improvements, and work efficiently. Try to regularly recognize achievements, offer growth opportunities, and foster a positive workplace culture.
-
Cross-training: Training employees in multiple roles provides flexibility. It reduces bottlenecks and improves operational continuity as employees can step into different roles as needed.
By focusing on workforce development, you can cultivate a stronger, more efficient team that contributes to both immediate and long-term success.
5. Proactive maintenance
Proactive maintenance is key for minimizing downtime and ensuring that manufacturing equipment operates at peak efficiency. From preventive maintenance to more advanced approaches like predictive and prescriptive maintenance, various strategies can be used to reduce unexpected breakdowns, extend equipment lifespan, and maintain consistent production output.
Ideally, you would implement a mix of proactive maintenance strategies, using the more advanced methods for complex equipment that is critical to production.
6. Technology integration
Managing manufacturing operations is a complex endeavor. And complex problems require advanced solutions. Think automation, IoT, and AI-driven programs.
Automation and robotics speed up production, IoT provides real-time data and monitoring, and AI and machine learning help identify inefficiencies, optimize production schedules, and improve decision-making across the whole company.
Improve manufacturing efficiency with L2L
L2L is a modern connected workforce platform designed to help manufacturers improve efficiency by providing real-time visibility into production processes, streamlining communication, and facilitating continuous improvement initiatives.
It takes the best pieces of a CMMS, MES, and workforce management platform and combines them into one centralized solution. You can use it to track and manage all of your shop floor processes, from production planning to quality management — and everything in between.
By integrating L2L into your manufacturing operations, you can optimize workflows, reduce downtime, and enhance overall productivity. Learn more by booking a personalized demo or sending your questions to sales@l2l.com.
Revisions
Original version: 21 August 2024
Written by: Evelyn DuJack
Reviewed by: Daan Assen
Please read our editorial process for more information
Related Posts
Subscribe to Our Blog
We won't spam you, we promise. Only informative stuff about manufacturing, that's all.