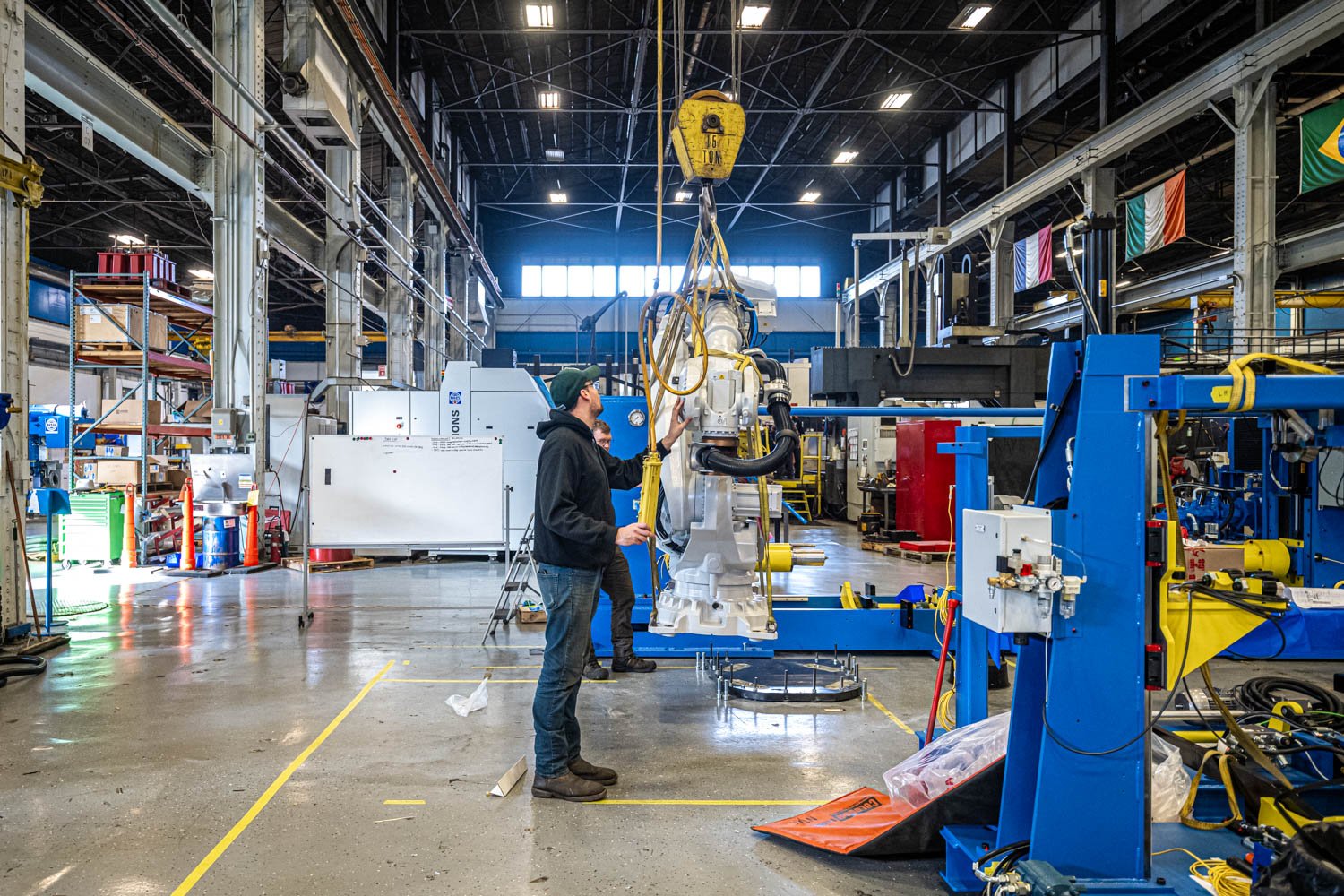
The concept of lean manufacturing has been around for a long time. At its core, it refers to the process of driving continuous improvement within a factory setting. It’s a systematic approach to manufacturing work that relies on several key principles, which we’ll break down below.
Applying lean manufacturing principles to their production processes, manufacturers across industries have been able to slash downtime and waste while improving productivity and efficiency. Essentially, lean manufacturing is all about doing more with less.
Let’s take a closer look at the five major lean manufacturing principles we see at work in today’s leading industrial organizations.
What are lean principles in manufacturing?
Lean manufacturing looks different for every manufacturer, depending on the product, company size, technologies in play, and similar factors. However, every lean manufacturer has the same goal: eliminating waste throughout the production process.
Waste can include material waste (scrap), wasted time, wasted money, and other major inefficiencies that can occur in a plant. In a lean manufacturing facility, you’ll see processes, machinery, and technology that maximize efficiency and prevent or mitigate waste across every aspect of production.
So, what are the basic principles of lean manufacturing? Let’s break it down:
-
Identify value: The first step is identifying the end value you want to gain from your lean manufacturing system. Ultimately, this means sustainably maximizing customer satisfaction.
-
Map the value stream: A value stream refers to a series of steps involved in creating value for the end customer. Therefore, value stream mapping is a method for keeping track of a product as it travels through this process and removing activities that produce waste.
-
Create flow: After eliminating non-value-added activities from production, it’s time to create a steady, predictable flow of materials, information, and work throughout the process.
-
Establish pull: Lean manufacturing relies on a “pull” system, where production is based on customer demand, thereby reducing overproduction.
-
Seek perfection: Once these lean practices are in place, it’s important to continually seek opportunities to make production leaner — a process known as continuous improvement.
By following these five steps, industrial companies can shed inefficient processes and activities and focus on the practices that deliver the greatest value to their end customers. In turn, this approach to manufacturing results in less waste, greater profits, and improved customer satisfaction.
Let’s explore these five principles in greater detail.
1. Identify value
Identifying value involves understanding what the customer truly needs and the value your product provides. This principle ensures that every step in the manufacturing process adds value from the customer’s perspective, thereby maximizing the effectiveness of the production process.
To accurately identify value, manufacturing businesses need to view their operations through the eyes of their customers and prioritize their efforts accordingly. Here are a few steps they can take to do this successfully:
-
Identify the customer for each product.
-
Understand what constitutes value for each customer using market research tools or customer surveys and interviews.
-
Analyze your products to ensure they meet customer needs effectively.
With this information, you can easily decide what to keep and what to eliminate from your production process.
For example, a furniture manufacturer might discover through customer feedback that speed of delivery is as important as the quality of the furniture. By focusing on the value principle, the company optimizes its production and supply chain processes to reduce lead times, ensuring that customers receive their purchases faster. This might involve streamlining the order processing system and working closely with logistics partners to ensure faster delivery times.
2. Map the value stream
Once you identify value, it’s time to map your value stream. This involved laying out the steps involved in delivering a product, from raw materials to the end customer. Distinguish between value-adding and non-value-adding processes by identifying every action required to design, produce, and provide a product. The goal of value mapping is to eliminate processes that don’t add value so you can streamline production and reduce costs.
Mapping your value stream can look like this:
-
Create a value stream map of your product or service and detail every step in its lifecycle.
-
Analyze each step for its contribution to customer value, paying attention to waste and areas for improvement.
-
Eliminate non-value-adding steps and optimize the value-adding ones.
In a packaging manufacturing plant, value stream mapping might reveal that a significant amount of time is spent on checking and re-checking inventory levels manually. By automating its inventory management system, the company can reduce time wasted on manual activities. This ensures that the focus remains on activities that directly contribute to creating customer value, such as design and quality control.
3. Create flow
Once waste has been removed from the value stream, ensure that the remaining processes proceed smoothly and efficiently without interruptions or delays— create “flow.” Achieving a continuous flow of work materials and information minimizes cycle times and reduces the likelihood of bottlenecks. As a result, customers consistently receive orders on time.
Here’s how you can create flow in your plant:
-
Identify and remove obstacles that cause delays, defects, and bottlenecks in the production process.
-
Implement lean tools and techniques such as Just-In-Time (JIT) production, workload leveling, and cross-training employees to ensure flexibility and efficiency.
-
Continuously monitor and adjust workflows to maintain an uninterrupted flow.
For instance, an industrial machinery plant might tackle a bottleneck at the soldering station by investing in automated machines for simultaneous board soldering and introducing a scheduling system to group similar process boards, streamlining setup. This enhances soldering flow, cuts assembly time, and boosts capacity to fulfill orders efficiently.
Bonus: Discover five quick "hacks" to get production flowing—fast.
4. Establish pull
Once you’ve established flow, apply the pull principle to ensure that products are only manufactured in response to customer demand, instead of anticipation of future demand. The goal of the pull principle is to reduce overproduction, one of the biggest sources of waste in manufacturing.
By producing only what is needed, in the necessary amounts and quantities, you can significantly reduce waste and improve efficiency. Here’s one way you can create a pull system in your plant:
-
Implement a demand-driven production system using a Kanban system or similar visual tools to alert the appropriate personnel when more products need to be made.
-
Adjust procurement, production, and distribution processes to be more responsive to actual customer orders.
-
Maintain close communication with customers and suppliers to ensure that production is closely aligned with demand.
A bottling plant, for example, might introduce a pull system by only producing beverages based on real-time supermarket orders. By linking production directly to sales data, the plant can minimize overstock and waste. As supermarkets sell more units, they request more from the plant, ensuring production directly aligns with consumer demand, boosting efficiency, and freeing inventory.
5. Seek perfection
Now that you’ve established flow and pull in your plant, it’s time to focus on continuous improvement—also known as the perfection principle.
The perfection principle is all about looking for ways to enhance quality, efficiency, and responsiveness. To drive continuous improvement, you need to foster a culture where improvement is constant and operational excellence is the standard. This principle challenges organizations to strive for better processes and outcomes, recognizing that perfection is a journey, not a destination.
Here’s how you can improve upon your established lean manufacturing system:
-
Encourage a culture where every team member is empowered to identify inefficiencies and suggest improvements.
-
Regularly review processes, seeking opportunities for improvement in quality, speed, and cost-effectiveness.
-
Use clear metrics and benchmarks to track progress and identify areas to further boost efficiency.
-
Invest in professional development opportunities for your workforce that directly add to your business value.
An example of this principle at work is a medical device factory conducting weekly reviews, where workers from all departments share suggestions for improving the production process. One suggestion could lead to the redesign of the packaging process, reducing material waste and packaging time. This not only cuts costs but also aligns with sustainability goals.
Apply these lean manufacturing principles with L2L
Applying the five lean principles in your manufacturing facility involves every level of your workforce, from the frontlines to the control room. Connected workforce platforms like L2L help businesses facilitate lean manufacturing practices by empowering workers to identify and solve problems quickly. They also streamline knowledge-sharing, helping manufacturers scale best practices and accelerate continuous improvement.
With advanced production management tools, L2L helps teams visualize waste and inefficiencies throughout the production process and easily escalate issues when needed. Real-time plant performance monitoring ensures that manufacturers have the information they need to improve production processes and implement new lean practices.
Ready to see how L2L can “lean out” your manufacturing operations? Take our FREE Interactive Product Tour today!
Revisions
Original version: 28 February 2024
Written by: Evelyn DuJack
Reviewed by: Daan Assen
Please read our editorial process for more information
Related Posts
Subscribe to Our Blog
We won't spam you, we promise. Only informative stuff about manufacturing, that's all.