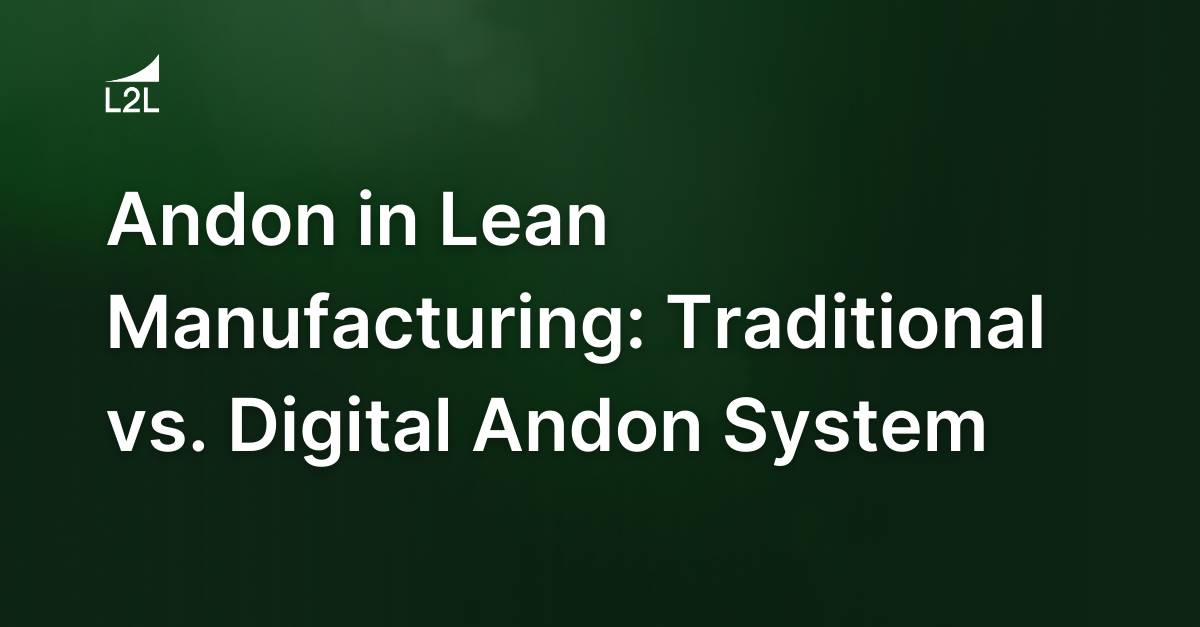
In the quest for operational excellence, manufacturers constantly seek tools that not only boost efficiency but also ensure quality and worker empowerment. One such lean tool is the Andon system. Originating from the Japanese word for 'lantern,' Andon is a critical component of modern manufacturing environments, helping plants streamline processes and highlight production issues in real time.
In this article, we're going to explore the essence of Andon in lean manufacturing. We'll discuss its benefits, look at traditional and modern implementations, and provide real-world examples to illustrate its impact on the production floor.
What is Andon in lean manufacturing?
Andon is a visual aid system used to alert floor managers and line workers to a problem in the production process. It's traditionally represented through a system of lights or a display board, with different colors signifying specific issues or statuses within the production line.
Andon enables quick response to issues, reducing waste and ensuring product quality. It provides a practical way to implement the principles of Jidoka, making it an integral part of lean manufacturing.
The main benefits of implementing Andon include:
-
Immediate problem detection: Andon signals allow workers to quickly identify and report problems without leaving their workstations, resulting in reduced downtime and improved productivity.
-
Scrap reduction: By addressing issues as they occur, Andon helps ensure that resources are used efficiently and only high-quality products continue through the production line.
-
Enhanced communication: Andon systems foster better communication between workers and management and ensure that alerts can be acted upon swiftly.
-
Empowerment of employees: Workers are empowered to stop the production line if they detect a quality issue. promoting a culture of quality and accountability.
-
Continuous improvement: Andon systems support Kaizen, or continuous improvement, as they help identify frequent stumbling blocks in the production process.
By implementing Andon, manufacturers can maintain a smooth and efficient production flow. This significantly improves both output quality and operational efficiency.
How a traditional Andon works
The traditional Andon is a straightforward yet powerful mechanism designed to alert and communicate issues in real time on the production floor. It typically involves visual cues such as lights, cords, and boards, each element playing a specific role.
Key components of a traditional Andon system include:
-
Lights: Different colored lights signify different statuses or alerts. For example, green might indicate normal operations, yellow could signal a minor issue that needs attention, and red might signify a stop in production due to a serious problem.
-
Cords: Pull cords or buttons are strategically placed within reach of line workers, allowing them to easily stop the production line and trigger an alert when they detect an issue.
-
Boards: Simple information boards that show the current state of the line and any alerts that have been activated.
Andon setups can vary by plant, but the color codes are largely universal. Source.
Here’s a quick example of how a traditional Andon system might work.
Imagine a car manufacturing plant where each assembly station has a pull cord connected to an overhead Andon board. If a worker at the station spots a defect in the part assembly, they can press a nearby button, which immediately lights up a red light on the board and stops the conveyor belt. This action draws immediate attention to the issue, allowing supervisors to quickly address the problem and minimize downtime.
An example of an automatic Andon system
The evolution of technology has led to the emergence of automatic Andon systems which integrate digital tools and software to enhance the efficiency and responsiveness of traditional systems. They leverage sensors, software, and real-time data analytics to automatically detect and communicate issues with minimal manual intervention.
Key features of an automatic Andon system include:
-
Automated alerts: Sensors installed on equipment can detect anomalies and automatically trigger alerts on digital displays or directly to relevant personnel via mobile devices or computers.
-
Real-time data integration: Automatic systems often integrate with other manufacturing software, providing a comprehensive view of production metrics and enabling data-driven decision-making.
-
Customizable alerts: Digital Andon systems allow you to create customizable alerts for specific production needs or particular quality standards.
-
Digital boards: These information boards display real-time production data. They can be customized to include the number of units produced, the current state of the line, active alerts, and more.
An example of a digital Andon display board. Source.
Let’s see another example of how an automatic Andon could be implemented.
In a high-tech electronics assembly line, an automatic Andon system is used to monitor assembly errors and equipment malfunctions. Sensors detect when components are incorrectly installed or when a machine deviates from operational parameters.
These issues automatically trigger a visual alert on digital dashboards throughout the plant and send notifications to the maintenance team's handheld devices. This facilitates quicker response, reducing downtime and ensuring continuous production flow.
Digital Andon systems represent the next step in manufacturing efficiency, providing a seamless, highly responsive approach to problem-solving on the production floor. They not only reduce the burden on human operators but also enhance the capability to maintain high-quality standards.
Implement a digital Andon system with L2L
Andon is a key feature of L2L’s connected workforce platform.
Our digital Andon solution integrates seamlessly into your manufacturing operations, providing a sophisticated interface for real-time data monitoring and issue reporting. Alerts are not only displayed visually on shop floor monitors but can also be sent directly to mobile devices and computers, ensuring that the relevant personnel are informed instantly — no matter where they are on the production floor.
The main advantages of L2L’s digital Andon system include:
-
Enhanced real-time response: With instant notifications, teams can address issues faster, significantly reducing downtime and improving production continuity.
-
Data-driven insights: L2L provides analytical tools that help identify common production bottlenecks and areas for improvement, fostering a proactive approach to maintenance and quality assurance.
-
Customizable interface: The system can be tailored to meet the specific needs of many different manufacturing environments.
-
Scalability: It scales with your operations, accommodating increased production demands without sacrificing performance or efficiency.
Simply put, manufacturers that adopt L2L's digital Andon system have a much easier time following lean manufacturing principles and maintaining operational excellence.
To get a direct look at L2L’s platform and Andon system in action, schedule a quick product demo with our team!
Revisions
Original version: 8 May 2024
Written by: Evelyn DuJack
Reviewed by: Daan Assen
Please read our editorial process for more information
Related Posts
Subscribe to Our Blog
We won't spam you, we promise. Only informative stuff about manufacturing, that's all.