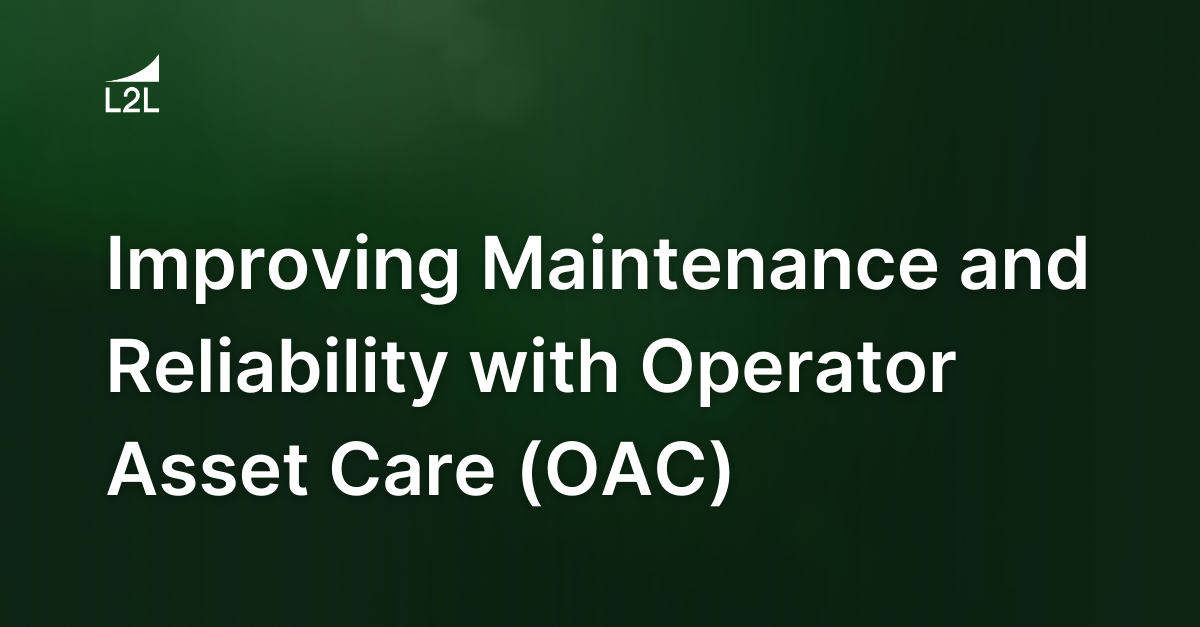
Your operators are the backbone of your manufacturing facility. They’re the people keeping your machines running and the first line of defense against mechanical problems. As such, they tend to have substantial insight into common problems, and process inefficiencies that lead to suboptimal mechanical performance.
This is why every factory needs a comprehensive operator asset care (OAC) system. Simply put, operator asset care is all about including operators in the maintenance and performance optimization of their machines. It not only helps manufacturers identify equipment issues early, but it also lets maintenance teams concentrate on complex issues.
In this article, we’ll cover the basics of operator asset care, its benefits and challenges, and best practices for implementing an OAC program in your organization.
What is operator asset care?
Operator asset care refers to the inclusion of manufacturing operators in the upkeep of machines and equipment. This concept comes from the principles of autonomous maintenance, a core building block of Total Productive Maintenance (TPM) — a popular approach to planned maintenance developed in the 1950s.
The goal of OAC is to mitigate asset failures by equipping operators to perform simple maintenance tasks. This involves training operators to identify and address mechanical issues and developing simple preventive maintenance checklists they can complete on their own.
OAC checklists include basic machine upkeep tasks that operators can perform independently.
An OAC checklist could include some or all of the following tasks:
-
Machine cleaning: Ensuring assets are clean by removing dust, debris, and other materials that could interfere with their operation.
-
Lubrication: Making sure that moving parts are adequately lubricated to prevent wear and tear.
-
Wear and tear inspection: Inspecting machinery and equipment for signs of excessive wear and tear, such as fraying cables, cracks, and worn-out belts.
-
Safety checks: Ensuring all safety guards are in place and that emergency stops and other safety devices are functional.
-
Leak checks: Inspecting for leaks in hydraulic systems, air compressors, and other areas where fluids or gases are used.
-
Electrical systems: Checking electrical connections for any signs of overheating, corrosion, or loose connections.
-
Control system calibration: Verifying that all control systems are calibrated and functioning correctly, including temperature, pressure, and flow controls.
-
Air filters: Inspecting and replacing air filters as needed to ensure proper airflow and prevent contamination.
-
Cooling systems: Making sure that cooling systems are working effectively, including checking coolant levels and inspecting radiators and fans.
When they’re included in the asset maintenance process, operators can spot — and sometimes even fix — emerging issues before they turn into costly breakdowns.
OAC, TPM, and autonomous maintenance: Explaining the differences
Although OAC is often part of a plant’s TPM strategy, it’s a unique process that manufacturers can use with or without TPM. Additionally, the term operator asset care is often used interchangeably with autonomous maintenance — a method from which OAC was developed.
To avoid confusion among these maintenance concepts, let’s break down the differences:
-
Total Productive Maintenance: TPM is a holistic approach to asset maintenance that involves the whole factory. By integrating different maintenance strategies and optimization initiatives, TPM aims to maximize asset effectiveness by reducing downtime, defects, and safety incidents.
-
Autonomous Maintenance: Autonomous maintenance is a component of TPM where operators perform rudimentary troubleshooting and maintenance tasks traditionally completed by technicians. It’s broader in scope than OAC, shifting more maintenance-specific responsibilities to operators than a typical OAC program.
-
Operator Asset Care: Unlike autonomous maintenance, OAC focuses on daily, repeatable maintenance tasks that ensure equipment runs smoothly. Tasks within the scope of operator asset care don’t require extensive training or specialized maintenance knowledge.
While there are plenty of similarities among TPM, autonomous maintenance, and OAC, it’s important to remember that these are distinct concepts with unique goals and purposes.
Best practices for implementing operator asset care in your plant
Implementing operator asset care in a factory involves systematic planning and integration of processes that empower operators to effectively maintain their equipment.
Here are some steps manufacturers can take to ensure success in their OAC programs:
1. Develop a comprehensive training program
Provide operators with basic and advanced training on the specific machinery they operate. For example, you can use a connected workforce platform to deliver this training digitally and on-demand, ensuring all operators have access to consistent and up-to-date training materials and tutorials.
2. Establish clear maintenance protocols
Create detailed checklists and maintenance schedules for each machine, and distribute these protocols digitally. A connected worker platform can send reminders to operators, track task completion, and update protocols in real time based on machine performance data and operator feedback.
3. Implement routine inspections and reporting
Schedule regular inspections and encourage operators to report any issues or abnormalities. Opt for a digital communication system that allows operators to submit real-time reports and photos directly from the factory floor via mobile devices. Immediate reporting can speed up the response time to potential problems, reducing downtime and maintenance costs.
4. Foster a culture of continuous improvement
Encourage operators to contribute ideas for improving maintenance practices and equipment efficiency. Facilitate idea-sharing and collaboration across the factory and allow operators to engage in discussions, share best practices, and provide direct feedback. This not only improves maintenance practices but also boosts operator engagement and job satisfaction.
5. Monitor and analyze equipment performance data
Utilize sensors and IoT devices to collect data on equipment usage and performance. Analyze this data to glean insights into maintenance needs and operational efficiencies. Using a data-driven approach to performance analysis enables predictive maintenance, where operators can address potential issues before they lead to equipment failure.
6. Review and adjust your OAC program regularly
Regularly review the effectiveness of the operator asset care program and make adjustments based on feedback and performance data. This iterative process ensures the maintenance program adapts to meet changing factory and equipment needs while maintaining high standards of operational efficiency and safety.
By integrating these steps with the capabilities of a connected workforce platform, manufacturers can improve the effectiveness of their operator asset care program and enhance communication, increase efficiency, and foster a proactive maintenance culture within the factory.
Challenges associated with operator asset care
Here are some common obstacles even the most advanced industrial companies face when implementing and optimizing their operator asset care programs.
Lack of senior management support
Senior management support is crucial for the success of operator asset care programs. Without it, there may be insufficient funding, resources, and prioritization, making it difficult to implement and sustain the program effectively. Management's commitment is also essential for cultural changes and to drive the importance of maintenance across the organization.
Insufficient operator training
Properly training operators to perform maintenance tasks is a cornerstone of a successful asset care program. Challenges arise when there is inadequate training or if the training does not match the specific needs of the equipment or the skills of the operators. This can lead to improper maintenance actions, which might cause equipment damage or inefficiency.
Poor communication between maintenance and operator teams
Effective communication between maintenance technicians and operators is vital to coordinating maintenance tasks and sharing crucial information about equipment status and performance. Poor communication can lead to duplicated efforts, missed maintenance opportunities, or unresolved equipment issues, impacting overall plant productivity.
Unclear separation of responsibilities
Defining clear boundaries and responsibilities between operators and maintenance technicians can be challenging. If responsibilities are not well-delineated, it can lead to confusion over who is accountable for specific maintenance tasks, potentially resulting in neglected duties or overstepping of roles. This negatively affects both morale and operational efficiency.
Cultural resistance to change
Cultural resistance from both operators and maintenance teams can be a significant barrier. Operators might be reluctant to take on what they perceive as additional duties, while maintenance personnel may view the sharing of tasks as a threat to their roles.
Overcoming this resistance requires a clear demonstration of the benefits and continuous engagement from all levels of the organization. It’s also important that operators receive adequate training on the tools and methods required to execute maintenance tasks. This streamlines technology adoption — a common stumbling block to successful implementation of operator asset care.
Resource allocation
Allocating resources effectively between routine production tasks and maintenance duties can be challenging. Manufacturers tend to prioritize production, especially in high-demand scenarios, which can lead to maintenance being put off, which increases the likelihood of equipment failure.
Manufacturers can better handle resource allocation if they treat maintenance activities, including OAC, as a vital part of the production process. Moreover, digital solutions like connected workforce software help plant leadership better coordinate maintenance and production schedules and balance short-term production goals with long-term equipment health.
Streamline OAC with the L2L Platform
If you’re implementing or optimizing an OAC program in your factory, you need to ensure that your operators have the right instructions available at all times. Connected workforce platforms like L2L are designed to digitize and democratize critical, job-specific information across the shop floor, making it easy for operators and maintenance teams to solve problems faster.
Platform features like L2L Production give operators real-time visibility into machine performance and instantly alert them to mechanical problems. From an intuitive operator console, workers can view digital instructions for basic troubleshooting guidance and easily create dispatches if the issues require a maintenance technician’s expertise.
On the flip side, maintenance technicians can use L2L Maintenance to log into a role-specific portal, diagnose mechanical problems, order the correct parts, perform the fix, and document it. With the right information at their fingertips, maintenance teams can make repairs quickly and correctly — minimizing both downtime and maintenance costs.
To get a personalized look at how L2L can streamline operator asset care tasks in your plant, contact us today for a personalized demo of L2L’s unique capabilities!
Revisions
Original version: 15 April 2024
Written by: Evelyn DuJack
Reviewed by: Daan Assen
Please read our editorial process for more information
Related Posts
Subscribe to Our Blog
We won't spam you, we promise. Only informative stuff about manufacturing, that's all.