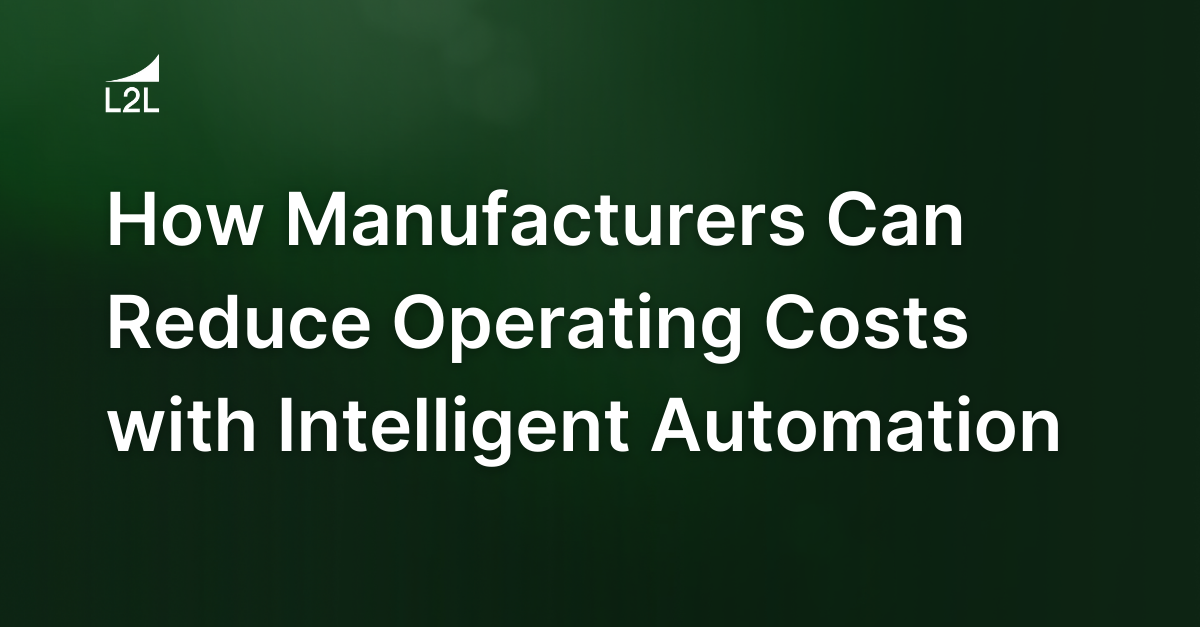
From supply chain disruptions to rising labor and material costs, manufacturers are constantly bombarded with complex challenges. As competition tightens and profit margins shrink, they are under increasing pressure to reduce operational costs — while maintaining high standards of quality and efficiency.
One of the most effective ways to tackle these challenges is with intelligent automation. By adopting advanced technologies, manufacturers can streamline processes, boost productivity, and ultimately, cut down on operational costs.
In this article, we'll dive into what intelligent automation is, explore its key benefits, and show how it’s transforming manufacturing operations today.
What is intelligent automation in manufacturing?
Intelligent automation in manufacturing refers to the integration of advanced technologies — such as AI, IIoT, and RPA — to streamline and enhance production processes.
Unlike traditional automation, which focuses on repetitive and predefined tasks, intelligent automation is designed to learn, adapt, and make decisions in real time.
The primary goals of intelligent automation are to reduce manual intervention, enhance operational efficiency, and improve overall productivity. By combining AI with automation, manufacturers can optimize their processes, reduce costs, and make better decisions.
Technologies used for manufacturing automation and intelligence
Several advanced technologies drive intelligent automation in manufacturing, each playing a crucial role in optimizing operations and reducing costs:
-
Artificial Intelligence (AI): AI in manufacturing powers predictive analytics, smart decision-making, and self-optimizing systems that continuously learn and improve production processes.
-
Robotic Process Automation (RPA): RPA automates repetitive, rule-based tasks, freeing up human workers for more complex activities.
-
Low-code Process Automation (LPA): Low-code automation solutions, like L2L Studio and Flow Engine, allow manufacturers to design and implement automated workflows with minimal coding skills.
-
Industrial Internet of Things (IIoT): IIoT connects machinery, sensors, and devices across the factory floor, enabling real-time data collection and analysis to enhance machine performance, monitor production conditions, and drive predictive maintenance.
-
Digital twins: A digital twin is a virtual replica of a physical manufacturing process or system. It enables manufacturers to simulate, predict, and optimize operations in real time, reducing errors and improving efficiency.
-
Intelligent Document Processing (IDP): IDP uses AI and machine learning to extract, process, and analyze unstructured data from various documents. This can significantly improve administrative tasks such as invoicing, compliance, and record-keeping.
These technologies work together to create an agile, data-driven manufacturing environment where operations can adapt to changes quickly and precisely.
A few examples of intelligent automation and how it reduces operational costs
Below, you will find numerous examples of how intelligent automation directly impacts operational efficiency and cost savings in modern manufacturing.
Improving production efficiency
One of the most impactful ways intelligent automation reduces operational costs is by improving production efficiency.
Automated production lines, powered by AI and robotics, streamline the manufacturing process, reducing bottlenecks and ensuring consistent output. These systems can operate around the clock, drastically increasing production capacity without the need for additional labor.
Predictive maintenance is another critical element of improving efficiency. Using sensors and machine learning, manufacturers can predict when equipment is likely to fail or require maintenance. This prevents unexpected downtime and reduces overall maintenance costs.
Additionally, real-time monitoring and adjustments enabled by IIoT and AI-driven systems allow manufacturers to continuously track production. Any deviations from optimal performance can be automatically adjusted.
Optimizing supply chains
Intelligent automation extends beyond the factory floor to optimize supply chain operations, which are crucial for reducing operational costs.
Again, technologies like AI and machine learning can improve inventory management by predicting demand more accurately. This helps manufacturers maintain optimal stock levels and avoid costly material shortages.
Advanced demand forecasting allows manufacturers to analyze market trends, sales data, and external factors like economic conditions to predict future needs. By automating this process, businesses can make smarter procurement decisions, preventing overproduction or underproduction.
Intelligent automation also improves supplier coordination and logistics. Automated systems can track supplier performance, optimize delivery schedules, and even suggest alternative suppliers in case of delays. This level of control helps reduce delays, ensures timely delivery of materials, and minimizes transportation costs.
Reducing labor costs
One of the most significant benefits of intelligent automation in manufacturing is its ability to get more work done with fewer resources.
By automating repetitive tasks, such as assembly line processes, data entry, or material handling, manufacturers can free up human workers for more complex, value-added activities. Employees can be trained and redeployed to more strategic roles, such as overseeing automated systems or managing data insights.
Enhanced human-robot collaboration is another key aspect. In many cases, robots and automation systems are used to assist human workers rather than replace them entirely. For example, collaborative robots (or "cobots") can work alongside employees, handling physically demanding or dangerous tasks.
Automating quality control
Automated quality control systems use computer vision and AI to perform automated inspection and testing at various stages of production. This ensures that products meet specifications with minimal human intervention.
Defect detection and reduction are other areas in which intelligent automation excels. AI-powered systems can analyze production output in real time, identifying defects that might go unnoticed by human inspectors. These systems can learn from data to continuously improve detection accuracy.
In the long run, this can reduce waste and rework costs tremendously.
Simplifying energy management
Energy consumption is a significant cost factor in manufacturing, and intelligent automation offers solutions to optimize it:
-
Smart energy consumption monitoring: Sensors and AI track real-time energy usage across equipment and production lines, identifying inefficiencies and enabling immediate action to reduce wasteful consumption.
-
Optimization of equipment usage: AI-driven systems can schedule machines to run during off-peak energy hours or automatically power them down when idle.
-
Predictive energy management: Similar to predictive maintenance for machinery, intelligent automation can predict energy usage patterns and identify potential energy drains.
By simplifying energy management, intelligent automation enables manufacturers to reduce operational costs associated with energy use while also supporting their sustainability goals.
The differences between traditional manufacturing automation and intelligent automation
Traditional automation has been a staple in manufacturing for decades, focusing primarily on mechanizing repetitive tasks.
Intelligent automation takes things a step further. It integrates advanced technologies that enable systems to learn, adapt, and make decisions.
Here are some key differences between traditional and intelligent automation:
-
Task automation vs. process optimization: Traditional automation automates specific tasks based on predefined instructions. Intelligent automation, on the other hand, focuses on optimizing entire processes by analyzing data in real time, predicting future outcomes, and making adjustments accordingly.
-
Static vs. dynamic systems: Traditional automated systems are static, following fixed rules and workflows. Intelligent automation allows systems to continuously learn from data and adapt to changes in the production environment.
-
Human supervision vs. autonomous operation: Traditional automation often requires human oversight to manage errors, interruptions, or changes in production. Intelligent automation enables more autonomous operation.
-
Reactive vs. predictive: Traditional automation typically operates reactively, responding to errors or breakdowns after they occur. Intelligent automation is predictive, using data analytics to foresee issues like equipment failure or supply chain disruptions before they happen, minimizing downtime and improving overall efficiency.
-
Limited scope vs. comprehensive integration: Traditional automation is usually applied to individual machines or production lines. Intelligent automation can integrate across the entire manufacturing ecosystem.
In essence, intelligent automation elevates manufacturing by making systems smarter, more adaptive, and better equipped to handle the complexities of modern production environments.
Step into the future with L2L
Intelligent automation is not just about reducing operational costs today — it’s about future-proofing your manufacturing processes. By embracing new technologies, manufacturers can unlock new levels of efficiency, flexibility, and resilience in their operations.
The future of automation is evolving rapidly, and L2L is leading the way. Our manufacturing platform integrates real-time data monitoring, predictive maintenance, and process optimization, helping you stay agile and efficient. You can automate workflows, monitor performance, and make data-driven decisions that drive operational excellence.
If you’re ready to take the next step toward a smart factory, start by taking our free smart manufacturing maturity assessment.
Alternatively, see the L2L platform in action by requesting a personalized product demo!
Revisions
Original version: 10 September 2024
Written by: Evelyn DuJack
Reviewed by: Daan Assen
Please read our editorial process for more information
Related Posts
Subscribe to Our Blog
We won't spam you, we promise. Only informative stuff about manufacturing, that's all.