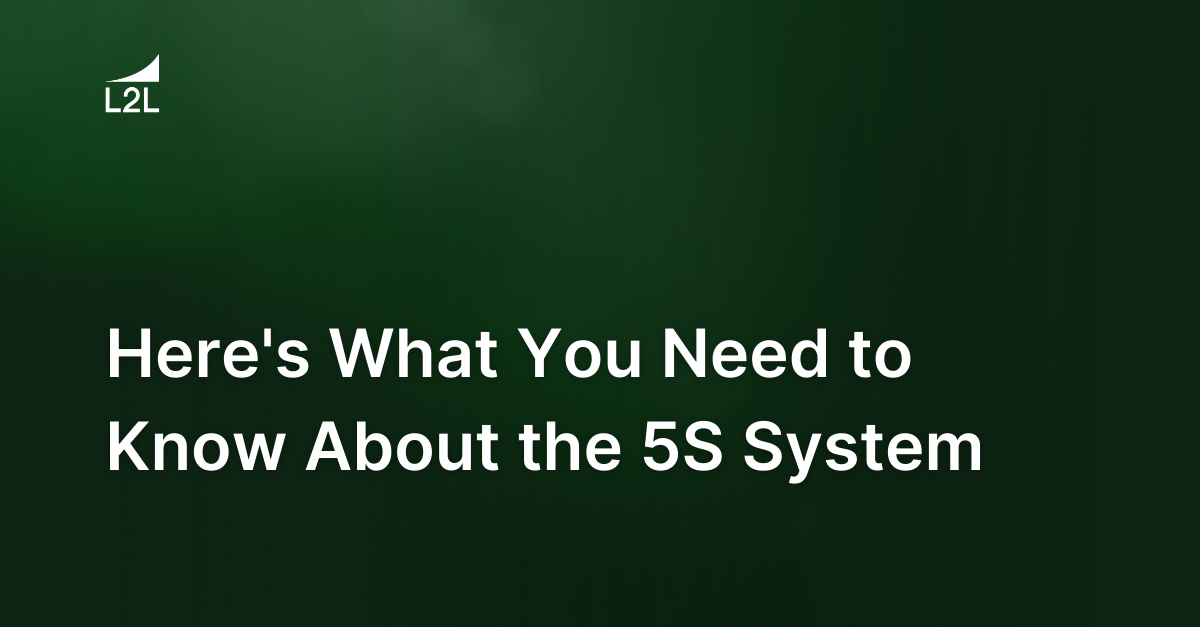
5S or 5 S. Not 5s, or Five-S, or the Five S's. And definitely not 5's. This is not an elite crime fighting group in Hawaii or a Boy Band from another era. 5S is perhaps the most straightforward and yet the most misunderstood and underappreciated of all the Lean Manufacturing tools and principles.
What is 5S?
5S System is based on five Japanese words:
- Seiri
- Seiton
- Seisō
- Seiketsu
- Shitsuke
Here are the English translations for each of these words:
- Seiri - Sort (organize)
- Seiton - Set in Order (straighten)
- Seisō - Shine (cleanliness)
- Seiketsu - Standardize (consistency)
- Shitsuke - Sustain (discipline)
5S System: Sort, Set in Order, Shine, Standardize, Sustain
What's with all the S-words? It's not a coincidence. You will notice a preponderance — scratch that — a whole slug of S-words throughout. And that's the idea. If you just put these babies to music in your head, that's all the smarter of you! The idea is to ingrain these words so they become second nature.
So, what's the point here? It's simple really, and for the most part, pretty simple. The 5S System, and all it stands for, are building blocks, and, some would argue, the very foundation of Lean. Let's take a closer look at each element of the 5S System.
5s System: Sort
Sort seems pretty simple, right? Well, sort of, sure. Who doesn't want to start a new endeavor with a clean slate? I sure do. And so do your teams. They want to begin every day in a clean, clutter free work space.
Sort, as it applies to 5S, means removing everything that is not necessary to perform a task in your work space. While this is a fairly straightforward undertaking, it is surprisingly difficult for many people. It feels like something is being taken away from them, even if they are the ones doing the removing.
These folks aren't pack rats. They've learned the hard way over the years that everything they need is not always readily available. If you've ever run out of a basic necessity, you can understand the urge to keep a few extra on hand, just in case of a rainy day.
So, where's the harm in that? If only one person kept one extra of one thing, no biggie. But when every person keeps extras of everything, that's not good. It's not about housekeeping. 5S improves your workplace environment for better control, productivity, and safety. Why? What does it really hurt? Here's a short list:
- Stuff is everywhere, including where people should be working, where forklifts should drive, walkways are cluttered, etc.
- Not only is your workplace visually unappealing, cluttered work spaces are accidents waiting to happen.
- Working in a pigsty is not a morale booster for anyone. Employee morale is a constant barometer. Don't overlook this opportunity to improve it.
- Unless all those extras everyone wants to stash are free, the organization's money is at least tied up, if not being downright wasted on unnecessary stuff. More is not always better. 5S Systems and Lean are all about eliminating waste.
- The personal belongings you have at work are also neatly stored, out of sight and out of mind. Far fewer distractions. It's easier to separate work and non-work if you're not toting a knapsack around.
- Need another reason? Think about the impact on customers touring your facility. Your plant is a source of pride and it should be showcased that way.
5s System: Set in Order
After you've removed everything that is unnecessary, organize what remains. Neatly arrange and identify parts and tools for ease of use.
- A place for everything and everything in its place.
- The correct place for each item is obvious visually.
- Anything not in its correct place is immediately apparent.
- Items are put away where they belong after use.
- Aisles, work spaces, and equipment are clearly identified and free from obstructions and clutter.
- Quantity and height limits are visually indicated, obvious, and easy to understand.
- Tooling and other elements necessary to perform work tasks are in close proximity to where they are needed and are arranged in a logical order of use.
- Fixed locations with easily identifiable labels: These can be pictures, symbols, or text.
You want to understand the playing field and know where the boundaries are. I can't think of any sport that doesn't have clearly laid out lines so you know what you're supposed to do and where you're supposed to do it.
5S System: Shine
Clean it up! Literally. Put some elbow grease into it! (Elbow grease leaves no residue).
Clean up your act, people!
- Start with your immediate work area.
- No man's land (spaces not specifically assigned to a person or work station) are notorious junk repositories).
- Floors, walls, stairs, work surfaces, and material storage locations should be free from FOD (foreign object debris), grease, clutter, and dirt.
- The importance of Shine as part of your 5S System is not just appearance:
- Anything that does not belong in finished product should not have the opportunity to become a contaminant, hazardous or otherwise.
- My mother (you know her, I quote Mom frequently in my blogs) had this expression: "Don't write anything down on paper you that would not like to see on a billboard some day."
- Think about drawings, CARs (Corrective Action Requests), etc. Do you want those documents lying about where an auditor or potential customer could see them? How about a competitor?
- Cleaning materials should be clearly labeled as to their contents, stored neatly, and close at hand.
Shine is a critical element of your 5S System. When things are neat and tidy, arranged in a logical fashion, it is easy to quickly identify abnormalities in your work space, processes, and products. Think 'Sleeping with the Enemy,' minus the psycho, while marveling at the level of mean on clean and organizational skills. If that thought sent a shiver down your spine, good! That should be your reaction going forward when any element of your 5S System is unfulfilled.
5S System: Standardize
Why is it necessary to Standardize as part of your 5S System? While variety is the spice of life, consistency is the key to happiness, my friend. There's something to be said for having a routine. Utilize checklists, preferably electronic.
You know what has to be done and how it should be done, the same way, every day. It's reassuring to know that no matter where in the world you walk into a McDonald's, your Big Mac is going to be the Big Mac you recognize and expect, made the same way, every time.
What benefits can you expect when you Standardize?
- Repetition: It's vital for training. You train all associates to the Best Practices and continuously monitor for adherence to those practices.
- Ensuring consistency dramatically enhances the potential for reliability and repeatability.
- Procedures are increasingly robust by virtue of maintaining Standardized processes, and not only in how the work required to build product is performed.
- When you Standardize information, it is visible and transparent, enabling more effective communication, both verbal and non-verbal.
- All standards are known and visible. Taking the guesswork out of the equation multiplies predictability exponentially. Quality you can count on, consistently.
Think back on the example of a playing field. You want to understand the layout of that field and know where the boundaries are. Imagine a sporting event where the boundaries are defined by snow cones.
5S System: Sustain
Most of the heavy lifting is behind you! Give yourself and your teammates a well deserved pat on the back! It's all downhill from here. This is the time to practice those first 4 S-words on a daily basis. Ingrain these behaviors and they become habit, the fifth S-word.
Discipline is both the word and the state of mind associated with Sustain in the 5S System. Self-discipline as well as the discipline required to make and keep this commitment to your coworkers, employer, customers, and stakeholders. After all, this is not merely a feel good exercise, although you will undoubtedly feel good. Great, even! The bottom line here is, well, the bottom line. The benefits of your 5S System will positively impact all of the above parties.
How to approach and solidify the 5S System at your plant:
- Let everyone know the objectives. There are no hidden agendas. The whole team understands the big picture.
- Communicate the plan, including the rules.
- Stick to the plan and stick to the rules.
- Train new team members to the standardized practices.
- As 5S becomes a way of life for your site, expect to add new things. The specifics of your 5S System will likely continue to evolve as you continue to improve and raise your expectations.
- Monitor and audit to ensure practices and documentation are accurate and up to date.
- "We're all in this together!" is the perfect attitude.
The 21/90 Rule
Think about sharing the 21/90 Rule with your teams as part of your commitment to your 5S System.
Commit to a personal or professional goal for 21 straight days. After three weeks, the pursuit of that goal becomes a habit. Once that habit is established, you continue to do it for another 90 days. If you can keep up something for three weeks and then ninety days, then it should become a permanent lifestyle change.
It’s all about leadership. It’s always all about leadership. And leadership is always accountable for what happens or fails to happen on their watch.
Sort. Set in Order. Shine. Standardize. Sustain.
You got this!
Revisions
Original version: 18 July 2024
Written by: Evelyn DuJack
Reviewed by: Daan Assen
Please read our editorial process for more information
Related Posts
Subscribe to Our Blog
We won't spam you, we promise. Only informative stuff about manufacturing, that's all.