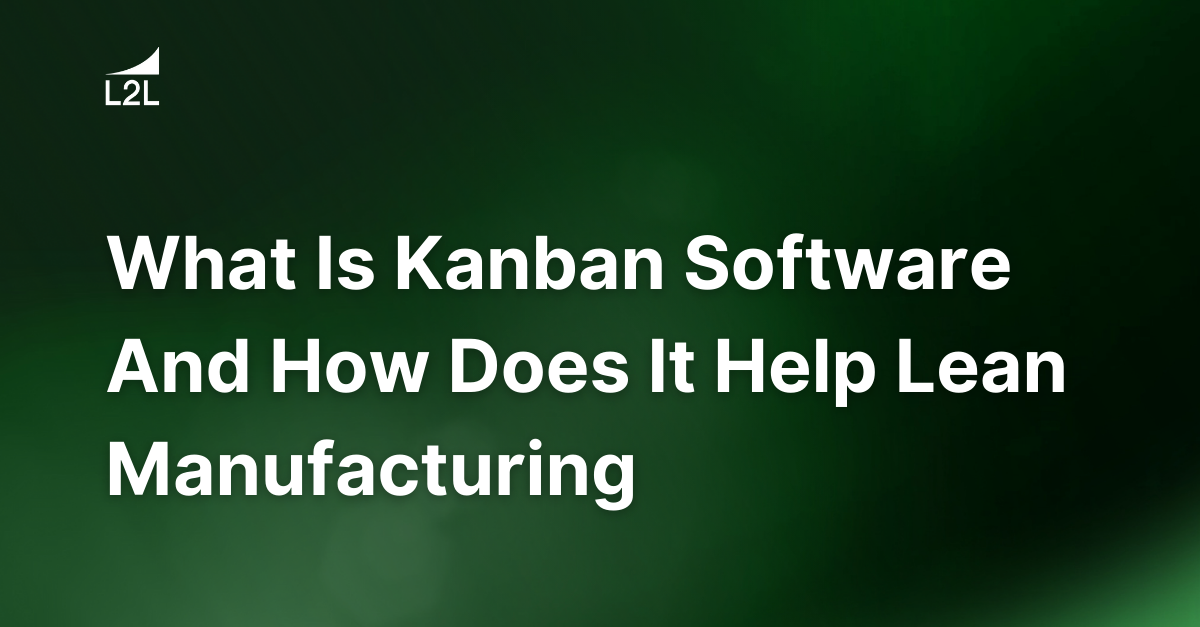
Kanban is any visual signal used to trigger action and its role in lean manufacturing is critical. Toyota introduced and refined the use of kanban in a relay system to standardize the flow of parts in their just-in-time (JIT) production lines in the 1950s.
It was originally developed by Taiichi Ohno, an industrial engineer at Toyota, and takes its name from the colored cards that track production, manage inventory and order new shipments of parts or materials that will be consumed. Kanban is the Japanese word for “Sign,” so the Kanban System simply means to use visual cues to prompt the action needed to keep a connected process flowing.
In the most efficient manufacturing companies today Kanban is used as an inventory control system used in Just in Time Manufacturing in order to connect processes and promote a Pull System.
Kanban Today
Many industries have used the Kanban principles and techniques for many years now, and it has proven to be very effective. I have personally worked with and experienced thousands of processes utilizing a Kanban signal concept to connect processes, control production, and manage material flow.
Today’s factories have become very reliant on their Kanban Systems to be accurate and effective. Many of our processes and operations run very lean and must have an accurate Kanban system in order to maintain a continuous flow of products. The success of factories and processes today depends on the success of a physical Kanban Card and the execution of launching a Kanban signal. This is an essential part of an effective JIT pull system.
Kanban & Waste
In my experiences, I have observed hundreds of occasions when a machine or operator is idle waiting for material to run. How many times have you observed a process or machine idle waiting on material? Nothing is more frustrating to me than watching labor and machine availability wasting away waiting for material.
Once you begin to dig into these situations and issues to determine root cause, you will begin to understand what is needed to eliminate any potential recurrences. It can become very alarming how reliant we are and how imperative it is to our process, and the execution of a physical Kanban Card system is done precisely. Many of these occurrences of wasted labor and wasted machine availability are due to simple failures such as a missing or lost Kanban Card, or the failure in manually executing the Kanban Card or Sign.
Why Kanban Can Fail
The Kanban or signal process is a very effective tool and concept. However, this very critical process is sensitive and has multiple failures that can have devastating results on our processes. Though this Kanban process is not new nor is this workflow complicated or complex, it can bring significant failures that are inherently manually executed.
Fortunately with the power of today’s technology, tools like kanban software enable the industry to leverage best practices to eliminate these frequent failure modes and re-occurrences.
With these modern tools and technology, frequent interruptions of manually executed systems (that are the cause of so much underutilized labor or machine availability) can be eliminated through the use of kanban software to autonomously control and send the Kanban Signal at the precise moment in time.
Kanban + Lean Manufacturing = Dream Team
Kanban plays a huge role and acts as more than just a sign or signal in today’s Lean manufacturing, and using kanban software can add significant value as it is combined with other lean concepts.
- Takt Time- (Rate of Customer Demand / Level Load)
- System- (Continuous Flow /Connect Processes)
- Heijunka- ( Level Load / Balance Work)
- First Time Quality- (Scrap Reduction/Rework/Over Processing)
- FIFO- (Improved FIFO Processes, Eliminate Waiting)
- WIP- (Reduction of Work in Process)
- Inventory Turns – (Increase Raw Goods Inventory Cycles)
- Jidoka- (Stop/Identify Problems and Eliminate Waste)
- Standards- (Eliminate Variation)
Utilizing the Kanban principles with a Lean Execution System allows entire sites, value streams and processes to be connected autonomously, and more importantly eliminate the many causes and simple failures that are inherent in a physical kanban card, and manual execution of signal.
What Your Lean Software Should Tell You About Downtime
Some may think that keeping the total downtime clumped together and not separating it out is best. However, as Kanban has taught us, this isn’t true.
Are you able to breakdown your total downtime and categorize the other incidental tasks? Can your current software categorize the Total Downtime and distinguish wrench time, response time, etc.?
Response time can be a powerful KPI intended to help manage a process. Allowing total downtime to be categorized as one event allows for hidden inefficiencies and poor processes that cannot be improved. You can't resolve an issue until you can clearly see it and define it.
For example, the Response Time to issues can be a good indicator of how efficient your overall facility and processes/procedures are running. Excessive Response Times can be an indicator of:
- An understaffed maintenance team
- Poor communication process to notify of issues
- Lack of real-time visibility to issues as they occur
- Slow/Long travel time to issue
- Under-defined Process and Procedures
- Inefficiencies in obtaining proper tools, work instructions, drawings, etc.
- Technician looking for Spare Parts / Complicated Process
- Technician obtaining spare parts as needed
Not measuring response time (or masking it) skews the perceived amount of time it really took to get the machine up and running after a breakdown.
By measuring and categorizing every minute of the total downtime, you get a much clearer picture of what's lengthening the time it takes to resolve the issue. A large portion of the downtime may be the response time. However, in order to understand this and make improvements, we must separate and measure all the causes of downtime and understand them each individually.
Honor the reality, identify and eliminate waste.
Can Your CMMS Software Give You the Data to Solve Problems?
Once you measure response time and other causes, you can then begin to identify all variables and incidentals that drive up response time. In the past, I have seen some simple procedures and reactive countermeasures put in place to reduce response time. However, you must honor the reality and address these causes. Some very simple and very effective countermeasures include:
- Scooters/Bikes. Transportation for maintenance technicians may reduce lead-time.
- Increased Workforce. Adding skilled technicians.
- Mobile Devices. Technicians are able to access notifications, drawings, and work instructions at the point of use. This eliminates running to offices and/or finding individuals that can provide documents.
- Spare Parts Delivery to Machine. Spare parts ordered from machine/mobile devices can be delivered to the machine or central drop-off locations.
- Visual Indicators. Area/location dashboards can tell you, at a glance, what is Normal vs Abnormal.
- Kits @ Point of Use. Kits for machine/line kept in Kanban locations at the work site and are replenished based on time.
Each site and Facility will bring its own set of unique constraints. However, if you are not measuring Response Time with your CMMS software, you need to. If you are measuring Response Time, ensure you are reviewing this powerful KPI regularly and identifying the waste within this Total Downtime Data.
Need a visual signal based automation software? Most can't. Check out our eGuide on why CMMS will let you down –and the steps you can take to change that.
Revisions
Original version: 20 March 2020
Written by: Jon Richardson
Reviewed by: Daan Assen
Please read our editorial process for more information
Related Posts
Subscribe to Our Blog
We won't spam you, we promise. Only informative stuff about manufacturing, that's all.