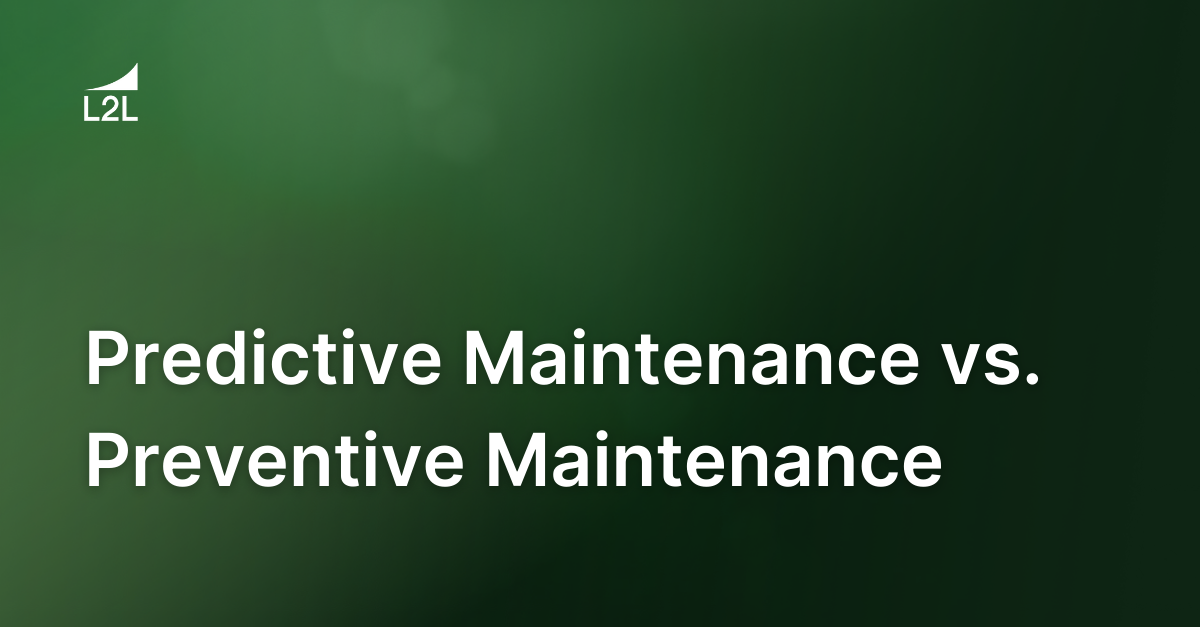
Read time: 12 mins
Menu
What Is Preventive Maintenance?
What Is Predictive Maintenance?
What Do Preventive and Predictive Maintenance Mean to Factories?
A Surprising Preventive Maintenance Case Study
Evolving Factory Maintenance with the Right Software
5 Mindful Maintenance Concepts to Get You Started
Take Control of Your Maintenance Strategy
Have you ever tried to meet your daily quota when one of your machines was out of commission? That’s probably not a memory you want to relive. Let’s face it: Unplanned maintenance is nobody’s idea of a fun day.
For a factory to meet production goals, manufacturing equipment must be available. It’s that simple.
What’s not simple is designing a maintenance strategy and finding available resources to keep the equipment running. Not to mention, you’ll always have to overcome the one certainty in manufacturing: Machines are going to break down. If a factory practices only reactive maintenance, technicians will never gain the upper hand. Plus, reactive maintenance is expensive because no planning process exists to accrue cost savings.
For that reason, many factories utilize ongoing preventive maintenance. Some equipment maintenance teams also practice predictive maintenance.
Today, we’ll explore preventive vs predictive maintenance and discuss the advantages of each.
What Is Preventive Maintenance?
Preventive maintenance is when specific elements trigger factory maintenance workers to inspect equipment and identify failures before they occur, thereby reducing the risk of an unexpected breakdown and helping protect equipment condition. Machines can have hundreds of parts, so preventive maintenance typically focuses on anything that has a limited lifespan or is critical to product quality and throughput.
There are generally two kinds of triggers that start maintenance action:
-
Usage-Based Preventive Maintenance: In this case, the number of completed production cycles acts as the trigger to inspect and replace parts.
-
Time-Based Preventive Maintenance: Instead of production cycles, this trigger is informed by the number of hours a certain part has been in use.
Either of these specific triggers helps maintenance teams stay ahead of basic repairs, thus preventing major stoppages and downtime. However, this doesn’t really mean anything until you know when to utilize preventive maintenance.
Some preventive maintenance makes good sense no matter what. Think of annual flu shots: If you’re in a high-risk demographic, you're going to get that flu shot every single year. It's the right thing to do for you — so in this example, preventive maintenance is not a waste. Now, is that true for everyone all the time? Not necessarily.
That’s because, in some cases, you can get away with a little well-planned procrastination (as long as it’s part of your overall maintenance strategy). Take, for example, oil changes on your vehicle. We all know what the recommendations are, but do we always follow them to the letter? Nope — not if we can get away with waiting a few more months or driving a few more miles. Sure, we stay alert for any signs of failure, but we’re confident enough in the equipment performance to decide preventive maintenance isn’t immediately necessary.
Now say you’re using that same vehicle to transport something really important — secret nuclear codes or all the money you’ve ever made or maybe just your dog. You might err on the side of caution and make regular oil changes a priority. In this case, it’s not a waste of time or money to add predictive maintenance to your routine. After all, you’re creating peace of mind for yourself (and whatever’s in that vehicle).
Essentially, the rules for predictive maintenance are the same as the rules for anything else in manufacturing: It all comes down to common sense.
What Is Predictive Maintenance?
Now that you know what preventive maintenance is, let’s take a look at its more sophisticated sibling, predictive maintenance.
The first thing to know about these two is that they both have the same goal: proactively preventing major shutdowns and downtime. However, to get the job done, predictive maintenance relies on system-generated data to trigger repair notifications. Teams perform maintenance when sensors, Programmable Logic Controllers (PLCs) and other Internet of Things (IoT) applications indicate that a part or component is failing or has reached a standard where failure is imminent.
In other words, predictive maintenance is based on real-time asset and component conditions. This is different from time- and usage-based preventive maintenance, where you build your maintenance strategy on predetermined component life expectation standards. With predictive maintenance, you have more control over your maintenance and rely on much less guesswork.
But when should you utilize predictive maintenance?
To answer this question, let’s go back to the vehicle carrying whatever important thing you imagined. To make sure this vehicle does its job, you have preventive maintenance responsibilities like changing the oil. However, you might also have predictive maintenance tasks, which are essentially part of a standardized maintenance program. These tasks are required at specified intervals — like switching to snow tires in late autumn — so you always know exactly when and what you should be doing. That way, there’s no guesswork necessary. You do your job so your equipment can do its job. The result is less unplanned downtime and fewer spikes in your overall maintenance cost (and, ideally, equipment you can trust).
What Do Preventive and Predictive Maintenance Mean to Factories?
Factories need to incorporate a combination of both preventive and predictive maintenance approaches to optimize equipment performance, longevity and repeatability.
Preventive maintenance is important to manufacturing because it’s a best practice that reduces the likelihood of significant production disruptions and downtime that can impact supply chain logistics, manufacturing costs, asset reliability and ROI. In general, it also reduces the total cost of your maintenance program because many preventive maintenance tasks can be performed by even entry-level associates. Unfortunately, the deployment of preventive maintenance can be challenging if your teams are caught up in the cycle of endless reactive maintenance issues.
Predictive maintenance is designed to forestall, if not eliminate entirely, breakdowns and downtime altogether. Using historical data derived from a number of sources, you can accurately predict the frequency with which predictive maintenance will be performed. In turn, production can anticipate when asset maintenance work will take place — even if the equipment is running with no issues or concerns (which is precisely the idea).
Although these philosophies make a great team, there’s one noteworthy difference between them.
Preventive maintenance is planned in advance so as not to disrupt production processes. While these tasks are performed at regular intervals, those intervals are easier to pinpoint, thus enabling operations to be scheduled around them. Predictive maintenance, on the other hand, lends itself to advanced planning of a slightly different nature. These tasks can be anticipated based on known, quantifiable variables, like how many cycles have been completed or how many hours a certain asset has been operated.
A Surprising Preventive Maintenance Case Study
We can talk about maintenance program planning, maintenance cost management and asset life-cycles until we start seeing sensors in our dreams — but that’s still not the same as knowing what these approaches look like in real life. That’s why I’m bringing your attention to a story some maintenance friends shared with me.
There was a type of equipment in their plant that required removing a high-voltage cable and greasing the end of it every month. But why? This preventive maintenance was not the result of any proven defect or failure rate in their shop; they were doing it because that's what the equipment manufacturer told them was supposed to happen.
The problem was that every time they removed that cable to grease it, something broke or went wrong. And then the line was down. Way down.
So why did they continue down this path without question? Because the manufacturer said so. Coincidentally, the manufacturer also sold replacement parts — which was really lucky, because remember, some other component broke almost every single time.
Finally, a Preventive Maintenance Tech said, "Why are we doing this? There are no failures reported by the line, so what are we responding to?" Someone listened, and they decided not to perform the prescribed preventive maintenance on an individual machine until they had a failure.
A month went by.
Then another.
Then another.
Wait, what? Three whole months?
They decided to expand the scope of their experiment. They stopped performing the monthly cable removal and greasing for every asset on the plant floor. To their amazement, they did not have one single failure for an entire year — and no adverse impact on product quality, either.
They changed their preventive maintenance strategy to “replace upon failure.” They saved a ton of time, a bunch of money and loads of downtime on the lines.
The replacement part manufacturer called one day to inquire why they weren’t buying replacement parts at the same rate as before. “We’re not performing the monthly preventive maintenance,” they said. “What do you have to say about that?”
The manufacturer, in fact, had nothing to say about that. They could only throw their hands up out of concern (for their bonuses, of course).
The moral of the story: It's your plant, equipment, time and money. Make sure your preventive maintenance benefits you instead of bossing you around.
Remember, the goal isn’t to perform more preventive maintenance — only what’s necessary. To do that, you’ll need software like L2L Maintenance, which tracks events in real-time and helps identify when preventive maintenance is really just unnecessary maintenance. If you’d like to take control of your own preventive maintenance destiny, let’s talk.
Evolving Factory Maintenance with the Right Software
The decision to implement predictive vs preventative maintenance is based largely on what type of maintenance system you’re currently using. If you’re stuck on a system that keeps you guessing, you need to break the cycle.
At this point, you may wonder how you escape the waste generated by reactive maintenance. You’re not alone. Every day, large and small manufacturing maintenance teams across all verticals have the same issues:
-
Manual maintenance systems don’t work because they’re paper- or spreadsheet-based, capture limited data and never create a culture of continuous improvement.
-
As factories increasingly embrace Industry 4.0, manual maintenance processes fall behind.
-
Maintenance functions in MES and ERP systems are not user-friendly and require system experts to enter and extract data.
-
Companies’ “standard” CMMS systems are frequently hard to use, don’t show real-time data and have no information on spares. Even worse, they don’t help Maintenance integrate with Production or facilitate problem-solving.
The solution to this is to move toward a system that’s user-friendly, built for the factory floor and has enough robust data to make it possible to conduct maintenance proactively. Easier said than done, right?
Consider L2L’s Maintenance software. It successfully breaks these paradigms by providing maintenance departments with a user-friendly tool built for the factory floor. Here’s how it works: With L2L, line operators can generate real-time digital dispatches for maintenance. Upon receipt, the maintenance technician can see the abnormality details, the machine repair history, spares availability, and access to procedures and manuals – all in one digital solution.
Most importantly, L2L Maintenance easily integrates with sensors and PLCs to capture IoT data so you can perform best-in-class preventive and predictive maintenance processes.
5 Mindful Maintenance Concepts to Get You Started
Mindfulness Maintenance. It's the new ideal for production efficiency for many industries. Ready to get on board?
First things first: Preventive maintenance is a key ingredient in the reliability of equipment and asset performance. To effectively manage a preventive maintenance program, there are several best practices to build discipline and achieve overall system and equipment reliability.
Here’s how to put these best practices to work and become a Mindfulness Maintenance champion:
Gather data regularly
Data is paramount in a preventive maintenance strategy. It not only serves as a historical record but also forms the core statistics you’ll use to implement proactive maintenance and avoid unplanned downtime.
Another important element of data collection is enabling your teams to know when equipment and components were installed, repaired or maintained. Such data tells you which parts were changed, when, where and why. It helps drive future decisions and enables you to budget, plan and spend wisely.
Use the data you gather
Often maintenance managers will go to extreme measures to gather and record data, but then fail to put it to use. It’s what we call analysis paralysis.
To get back in motion, start by calculating the time between repairs, replacements, failures and servicing. Build averages and mean-time-between failures or repairs as a guide to stocking part inventory levels and planned downtime. You can also use this data to inform predictive analytics tools that tell you when to schedule equipment overhaul, change a filter or perform other mission-critical tasks. This pays great dividends by allowing your spare parts inventory levels to be lean while preventing disruption from failures and unnecessary maintenance.
Understand the life-cycle of your equipment and systems
Preventive maintenance pays the most dividends when a life-cycle approach is applied. Don’t just look at the next few months or years; instead, focus on the lifespan of equipment and how it can achieve a full-service life. It costs far more to replace a machine or process than it does to maintain it properly and keep maintaining it.
Understand what failure looks like
Knowing when faults occur is a very important part of crafting your preventive maintenance program. When gathering data and recording performance, record when parts fail or wear to the point of replacement. Recording this type of asset data will help identify what parts and subsystems are most prone to failure.
These days, a motor rebuild because of a worn component probably doesn't make sense. However, having sensors that tell you when the motor is getting close to failure is critical to having the right spare on hand for a quick replacement.
By accurately capturing and recording failures, faults and worn parts, you’ll discover how to repair and maintain equipment now and well into the future. If you know where your risk of failure is, you'll be greatly rewarded with leaner inventories and less time spent on asset repairs.
Be mindful of time dedicated to maintenance
Any preventive maintenance program deserves a healthy culture. Train personnel in preventive maintenance and tell it like it is: Planned, preventive maintenance is far better than reactive maintenance.
Share data across your maintenance team about repairs, failures and maintenance schedules. Educate them about equipment lifecycles and solicit their input to help parts and equipment last longer and wear less. Make them part of the overall preventive maintenance strategy by using their feedback, educating them on historical maintenance data and training them to take actions that will prevent premature failures. Get them excited about preventive maintenance by building a culture where everyone thinks long term, without waste in material and time, and with a great appreciation for lifecycle extension and reliability.
Take Control of Your Maintenance Strategy
Predictive and preventive maintenance are two sides of the same coin — a coin you need in your back pocket. They’re an industry best practice you should adopt if you want to boost your efficiency and uptime, lower your overall maintenance cost and improve revenue. Luckily, neither maintenance strategy is out of reach, and having the right maintenance software can help.
If you’re ready to take control of your maintenance strategy, book a demo to see how our next-gen maintenance software can make it happen.
Check out this 1 min video about how West Liberty Foods has benefitted from L2L's platform:
Revisions
Original version: 16 March 2019
Written by: Trent Maw
Reviewed by: Daan Assen
Please read our editorial process for more information
Subscribe to Our Blog
We won't spam you, we promise. Only informative stuff about manufacturing, that's all.