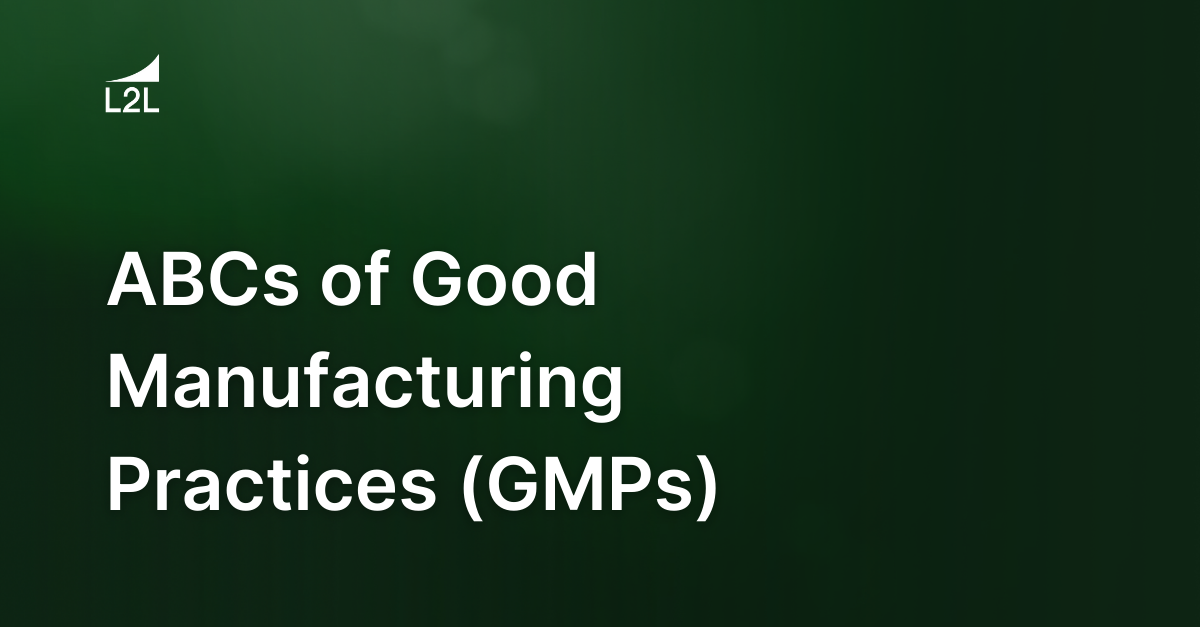
Good manufacturing practices, or GMPs, are the regulatory standards for ensuring high quality products are consistently produced across batches that meet their intended use.
GMPs are needed to meet requirements established by the US Food and Drug Administration (FDA), under Title 21 of the Code of Federal Regulations (CFR), which regulates food, beverage, pharmaceutical, medical device, and cosmetic manufacturing in the United States. Despite the “m” in GMP standing for manufacturing, producers as well as processors and packagers of such goods are beholden to these codes.
GMPs are the Key to Quality Production
GMPs drive a quality-centric approach to production in the targeted industries to avoid production errors that compromise product quality.
Therefore, the principles of GMP include ensuring conditions such as:
-
- product is uniform across batches;
- production is appropriately documented;
- product and its raw materials are free of contamination;
- production equipment and processes are validated;
- personnel are properly trained;
- product quality is confirmed throughout production; and
- product complaints have an established handling process.
GMP requirements are not prescriptive: The published guidance is general. Each firm must interpret the applicability of these rules to its business and determine how to implement the required controls in a scientifically sound manner.
Most businesses elect to establish a quality management system (QMS) to drive their own GMPs and comply with, or often times exceed, regulatory requirements.
Current GMPs
GMPs may also be referred to as cGMPs for current good manufacturing practices. This references the need for firms to strive for continuous improvement of their GMP practices to assure effective and safe products. Particularly when considering technology, practices used to prevent errors ten years ago may not satisfy today’s regulations.
Forward-thinking firms will leverage modern technologies for innovative solutions that surpass today’s cGMPs and will remain viable through several standards revisions.
Why Are GMPs Necessary?
cGMPs are meant to assure product identity, purity, efficacy, and quality. This is done by compelling firms to systemically ensure their physical facilities as well as manufacturing processes are developed, monitored, and controlled appropriately. The controls that cGMPs instill are necessary because the end consumer cannot otherwise know if the product is safe and functional.
While product testing is one part to confirming product quality, it cannot always be completed on each article in a batch. It is critical in such circumstances to have repeatable manufacturing processes and conditions, as driven by GMPs, to guarantee product homogeneity and therefore representative testing.
Measures such as validating product process changes, maintaining production facility cleanliness, and having documented production traceability to the batch level, meet these GMP objectives and protect the consumer.
cGMP Compliance
The FDA assesses compliance with cGMPs by conducting inspections of companies’ facilities; inspections fall into several categories and each are conducted by trained FDA agents. Routine inspections can occur any time the firm is open and are typically unscheduled.
These inspections typically follow a QSIT (Quality System Inspection Technique) format. In the case that serious product risk is identified during a routine inspection, the inspection may be realigned with the “for-cause” format.
“For-cause” inspections are performed to assess a particular issue that has been reported to the FDA or discovered by the agency. These evaluations may have a more dynamic structure, and while centered on a specific portion of the company’s practice, may also encompass related business segments. External reporting on “for-cause” inspection subjects can come from sources such as customer complaints, a manufacturer’s product recall for field alert, or a cluster of adverse event claims.
Inspections also predicate and follow new-product approval. After a firm has submitted an application to the FDA to market a new product, a pre-approval inspection (PAI) will be executed. It will focus on confirming the validity of the data and claims within the application, including the company’s ability to produce the product in accordance with cGMP requirements.
The outcome of the PAI will inform the decision to approve the new product. There are also post-approval inspections, which check for modifications to the production and control methods that occur following approval.
Failure to Comply with cGMPs
If a company produces and distributes a product that fails to meet its specifications and may have harmful implications for consumers, the firm can recall the affected product batch(es) to remove the product from the market and preclude further impact to consumers.
Companies will typically issue recall at their own behest or at the FDA’s request; if they fail to comply with the FDA’s request, the agency can seize the product and issue a warning to the public.
The FDA can also apply legal means as enforcement. Injunctions and seizures are court orders demanding an organization cease from a particular activity, such as selling products that do not meet cGMP standards.
Injunctions prevent the sale of a product, and therefore are a powerful business lever to drive company correction of cGMP infractions. Under specific injunction types, embargoes and seizures, the government can physically impound product that threatens public health and safety.
How to Ensure a Robust Quality System
Good manufacturing practices are critical to ensuring consumer safety and product quality. While maintaining regulatory compliance and supporting the QMS system that maintains it can be a heavy burden for a firm, there are tools that can lessen the load.
Leading2Lean’s multifaceted capabilities to manage workflows, provide notification and escalation on aberrant events, and provide feedback on event reporting, all while integrating with existing compliance-centric systems, makes it a powerful partner in simplifying cGMP compliance. See what L2L can help you achieve and improve today!
Revisions
Original version: 23 March 2020
Written by: Amy Mele
Reviewed by: Daan Assen
Please read our editorial process for more information
Related Posts
Subscribe to Our Blog
We won't spam you, we promise. Only informative stuff about manufacturing, that's all.