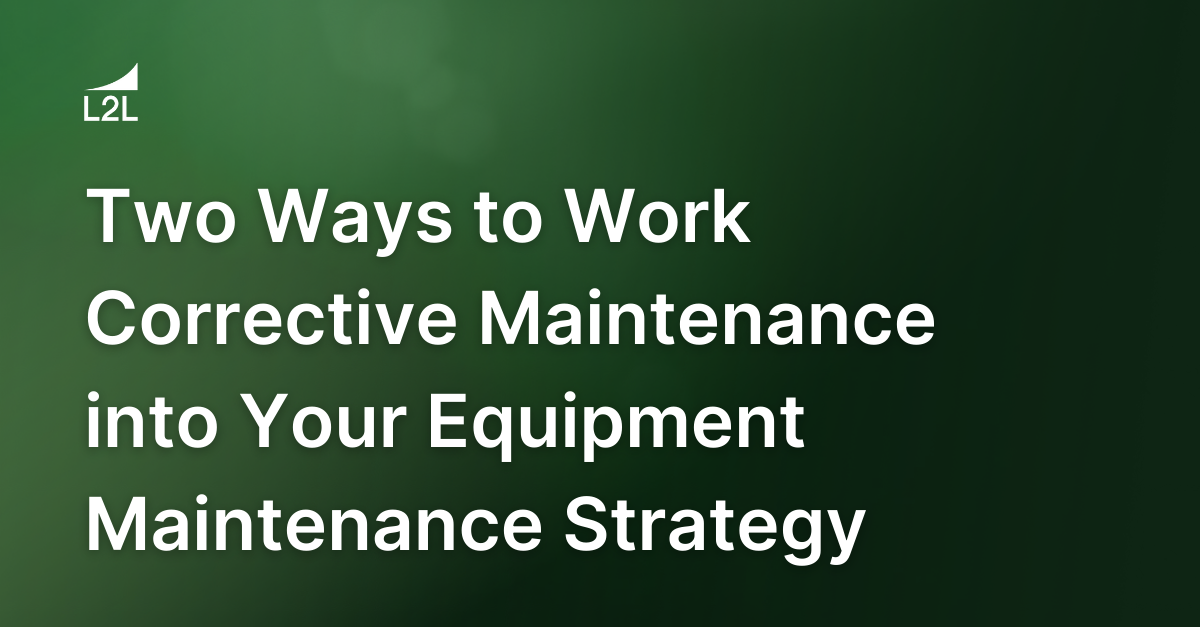
There are many different strategies for equipment maintenance that teams can use to help raise and keep the Operational Availability (OA) up on the production lines. However, every one of those strategies comes at a cost. It’s a balancing act between keeping the right number of technical resources on staff, keeping the lines up and running, and of course, keeping profits up.
Four Equipment Maintenance Strategies
There are four main equipment maintenance strategies:
-
Reactive or Run to Failure Maintenance
-
Corrective Maintenance
By using a combination of these maintenance strategies, you can make your uptime successful — or it can cost you a lot of time and money.
This post will cover corrective maintenance as a good equipment maintenance and production efficiency strategy; that is, if it's fully adopted by your shop floor.
What Is Corrective Maintenance?
I used to teach Total Productive Maintenance (TPM) classes for the 900 production associates at the plant where I worked. It was a lot of fun because the operators are the people who really know how the equipment is running. Like in NASCAR, they (production) are the drivers of the cars and can report what they experience back to the crew chiefs (maintenance and engineering).
The day before the start of each training session, I'd sneak out to the production line where the three-day workshop was going to be held and take photos of some items that needed to be addressed, like cuts in cables, small leaks in hoses, and missing bolts. I'd show my students those photos in the opening presentation. I would hear comments like, “Wow! I’m glad I don’t work on that line,” and “This can't be here at our plant.” You can imagine the shock to these same people when I would tell them that those photos were taken from the very line they run each day. It seems to me that the operators were so focused on building the product that they had developed tunnel vision. Sometimes, they really could not see the machine itself.
Making Your Corrective Maintenance Approach Work for Your Operators
Oftentimes, people do see these problems, but one of several things happens. They don't take the extra time required to acknowledge individual items because their plant's work order reporting system is too cumbersome. Worse yet, they think nothing will be done if they do document what they've seen, or maybe they don't even have a system that they are allowed or trained to use. Maybe they don't have anywhere to document these issues. So, they think they'll remember to tell their supervisor. But when they go back to running the equipment, it slips their mind.
Maintenance teams see these same issues but are usually in a hurry to do their checks and repairs on the equipment. They, too, make a mental note to tell their supervisor, but they forget. And if they write it down, they don’t find an opportunity to create that work order until a few days or weeks later. Unfortunately, by that point, it's probably too late, and the issue they saw has already created the downtime they were hoping to prevent.
These small things are what contribute to breakdowns when left unattended. My colleague's mom has this great expression: "You can sit on a mountain, but you can't sit on a tack." In other words, it's the small stuff.
In order to address small issues before they cause downtime, you must do two things to promote a corrective maintenance approach:
First, train everyone running the equipment, including the maintenance staff, to recognize what abnormal looks, sounds, feels, and smells like; the same goes for normal (the desired state). Discuss the costs these seemingly small issues can have on the production line, such as:-
Safety issues (When it comes to safety, the cost is always high)
-
The quality of the product
-
The cost of premium freight to expedite shipments caused by delays because the machine or line is down
Second, provide an easy way for the teams to log and note these issues. Allow maintenance and production to plan for a time when the line is scheduled to be down to make those needed repairs before returning the equipment back to normal operating conditions.
This reminds me of a time when I was part of our maintenance team and went to a downtime call out on the line. After talking to the associate and asking how long the air had been leaking from the cylinder, he said, "Well, it’s been getting progressively louder these past couple of days, until now it won’t open the door.”
They heard the noise, but they just didn’t know or acknowledge what was going on or realize what was about to happen.
This could have been corrected by maintenance on the off shift or at lunch break, costing the line zero downtime. Training is key to recognizing abnormalities and learning to use all sensory systems to detect problems. In short, an effective corrective maintenance strategy must include proper training on how to identify different types of problems — and a quick way to document them.
Implementing a Digital Equipment Issue Reporting Process
Okay, so now you've taught your employees how to identify issues using nothing more than their basic human senses. However, that's only the first step in building an effective corrective maintenance plan. Your next step is to create a process to report issues and schedule for them to be corrected. This process should be as close to real-time as possible and use a digital system that is linked to machine history.
I have seen systems in the past where the teams would fill out a tag and affix it right to the issue. This does make it visual, but also easy to forget. In time, the tag gets soaked with oil or dirt from the very leak that they were reporting, rendering it illegible.
Today, I see more and more people using a software system that's easy for the operators to use to report abnormalities. They don't even have to step away from their work area. This software makes it much faster for the people on the plant floor to capture the details needed to execute corrective maintenance. It also makes it much faster and easier for the maintenance teams to quickly follow up on reported abnormalities. They can then coordinate with production to schedule a time to complete the work.
These capabilities are found in L2L's Lean Execution System. The Maintenance and Production modules are a powerful combo for unifying operators and maintenance in improving uptime — a must-have for any corrective maintenance strategy.
If your maintenance people see an issue while out on a PM or repair, they can use the same system that is tied to machine history to put in a follow-up work order. Scheduling and completing the corrective maintenance work can happen during planned production downtime of the equipment, saving time and money, and further reducing unplanned downtime for the line.
Corrective Maintenance Bonus Idea
Here's another tip for optimizing your corrective maintenance plan. When the teams are doing equipment inspections, you can provide them with a list of previously reported items on their tablet so they can see what else can be taken care of during the downtime of the inspection or repair they are performing. It can also help the planner prioritize the work based on their professional judgment.
I urge you to consider active corrective maintenance as part of your overall equipment maintenance strategy using the modern tools, like L2L, that are now available.
Revisions
Original version: 18 July 2024
Written by: Evelyn DuJack
Reviewed by: Daan Assen
Please read our editorial process for more information
Related Posts
Subscribe to Our Blog
We won't spam you, we promise. Only informative stuff about manufacturing, that's all.