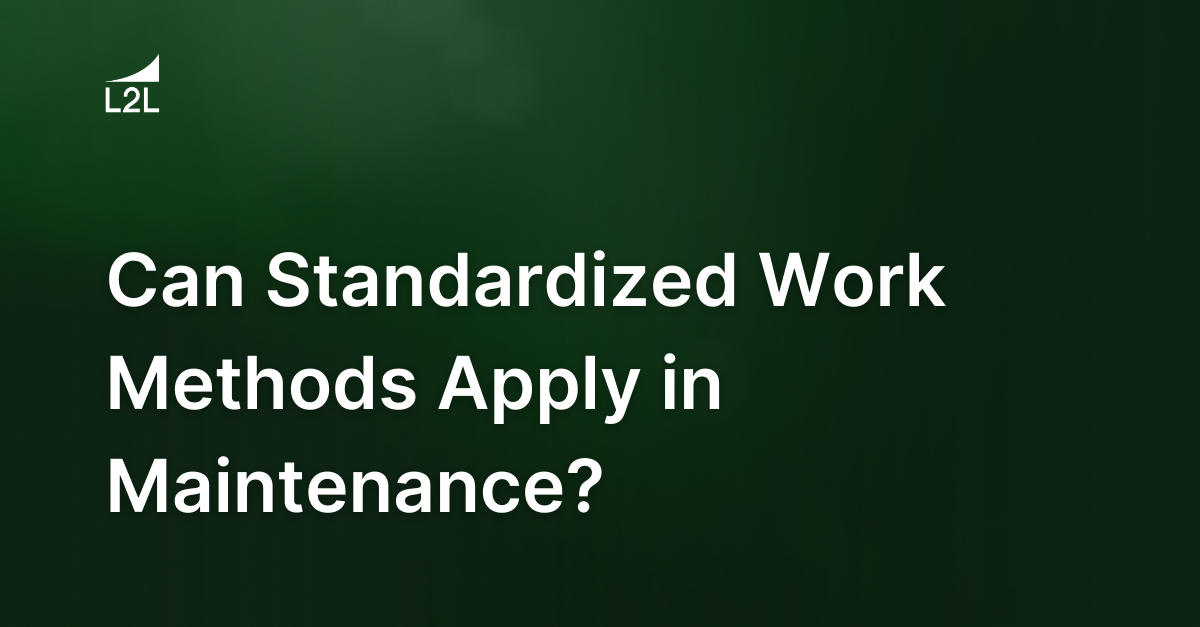
We've all heard the expression that standard work (a.k.a., standardized work) is the foundation for continuous improvement and employee empowerment. And if you haven’t, you should read The Toyota Way, principle six.
Why You Need Standard Work Instructions
How do we apply what some would consider a production lean principle of Standard Work Instructions (or Standard Operating Procedures) to the technical resources in the plant? Does that same principle apply to the support groups like maintenance and engineering? Absolutely yes, as their services are needed to help stabilize the production process, and to help eliminate variation so that you can achieve continuous flow of material through the plant.
Here is also another reason why standards are important in maintenance: The Labor Department has reported that 10,000 Baby Boomers are retiring each day, and that this trend is expected to continue over the next several years. So how do we deal with the knowledge transfer that absolutely needs to happen in your plant today?
That knowledge is vital for the newer technicians that are coming into the plant.
Use Standard Work Instructions to Address These Challenges
Some of the challenges that technicians face today include where to look up machine history, and if they find something, is there enough detail on repairs, etc. to be useful.
Another challenge is there are a few techs that are reluctant to share their knowledge. They want to be the hero and be packed around the plant on the shoulder of management for what they think is job security, when in reality, they are the cancer in your organization. When I was a maintenance supervisor I sometimes heard statements like, “the newbies can be baptized by fire, just like I was!”
These challenges can result in long periods of downtime, missed shipments, and possibly even the quality of your product.
So how do we address these concerns by the use of standard work?
1. Make Data Retrieval Easy
The first step is to make it easy for the maintenance techs to pull the machine history. It is important that when they're on the job, they're able to quickly look it up so they can make a better decision to help with their troubleshooting, what's been done in the past, what may have caused this issue before and what spare parts have been recently changed.
Oh and by the way, a problem statement: "Broken - Solution: Fixed," doesn’t count as machine history.
2. Create the Standard Work Instructions
The second step is to put into place a process that addresses significant issues like a downtime threshold that will trigger an RCA (Root Cause Analysis) project to address the issue. During this activity, one of the steps should be to create troubleshooting guides.
TWI’s or technical work instructions are standards on how to troubleshoot and repair the equipment. At home, technicians are using standards like Chilton or Haynes manuals to work on their truck, or even using YouTube as a way to learn how to tune their chip in the diesel. But at the plant it seems like they don’t have access to useful information
Now, I've had a few technicians tell me in the past that, “Hey, you're taking away my creativity to troubleshoot if I'm always having to work from standards to do my job.” But in reality, you want their creativity in developing these standards so that the repair can be done quicker in the event the machine breaks down again. At least with a standard you can now have a baseline to work from and you can creatively improve.
3. Audit Your Standard Work
The third step is to be able to go out and audit those technical standards being used on a call, and to audit the standard itself periodically to see if Kaizen is needed.
The people who are the best at making and revising these standards are the ones that work with them every day. They are the most valuable resource you have to help build the continuous improvement culture you need in order to survive in the competitive market.
You will need to be disciplined to use those standards so step 3 is the follow up needed to make this a habit in your plant.
So if you get machine history in the hands of the techs, create a process that allows you to build these troubleshooting guides and to audit those standards, you will see the gains and more importantly the knowledge transfer and teamwork.
The Power of Standard Work
With those three simple ideas, you're going to:
- Get quicker repair times, and therefore less downtime
- Your quality and the validation of the repair is going to be better
- Have happier technicians, who have the confidence that they can get the down machine up and running again. Building their skill level will raise the morale as well.
With standard work instructions, you can escalate the rate of improvements for your facility. However, in order to do all this you're going to need a next gen CMMS or LES system to help manage the standards and track the progress of the improvements with good data. L2L has just what you need help in managing issues.
Revisions
Original version: 18 July 2024
Written by: Evelyn DuJack
Reviewed by: Daan Assen
Please read our editorial process for more information
Related Posts
Subscribe to Our Blog
We won't spam you, we promise. Only informative stuff about manufacturing, that's all.