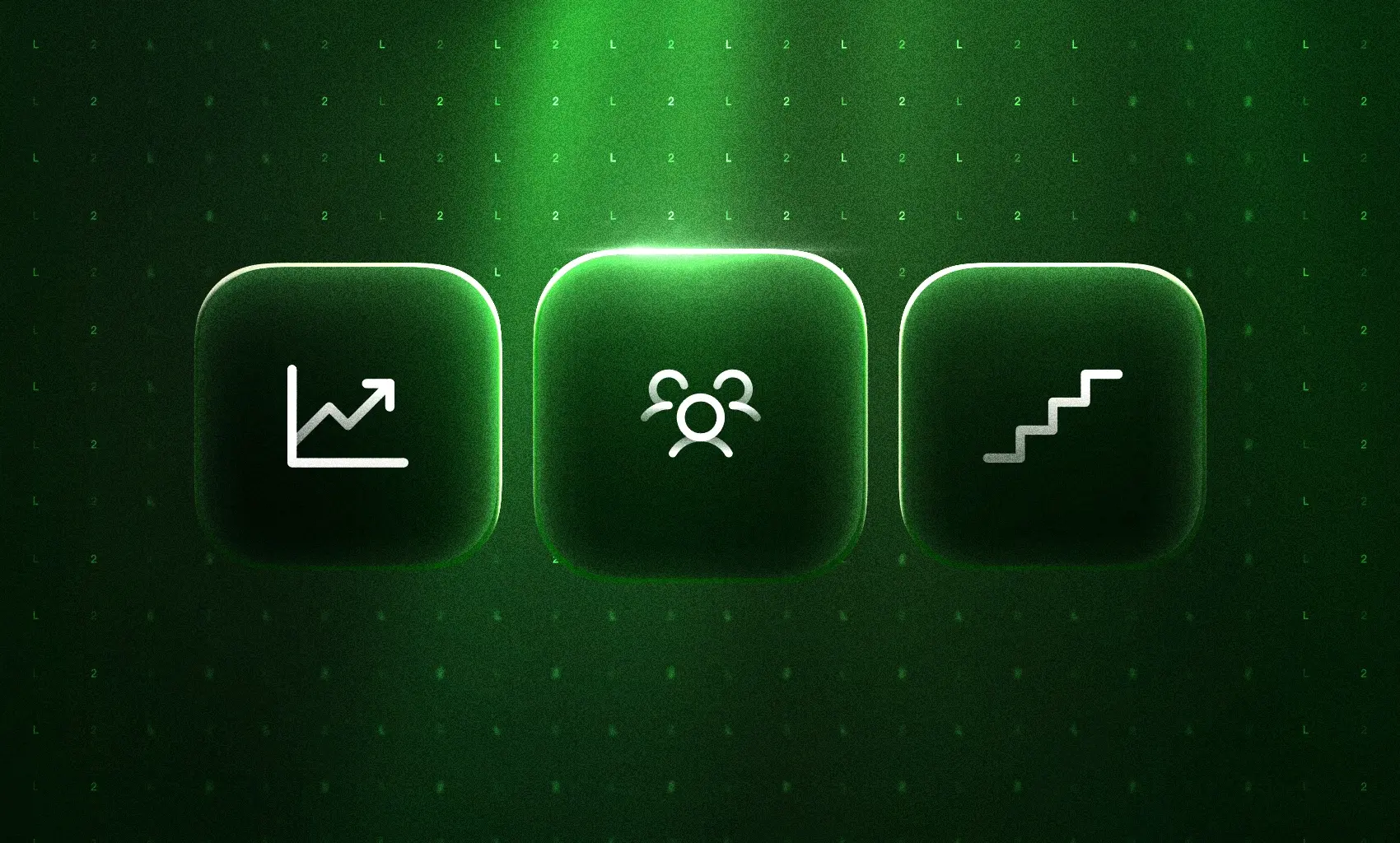
Here's a loaded opinion: in times of uncertainty, nimble and flexible manufacturing is your competitive advantage.
Economic challenges, including tariffs and supply chain disruptions, have created a perfect storm for manufacturers worldwide. Having worked with thousands of manufacturing teams, we've gathered valuable insights on how forward-thinking plant managers are responding to these challenges to become more flexible in times of uncertainty.
Here are three proven approaches to add to your playbook:
- 🔗 Maximize Existing Plant Capacity
- 🔗 Invest in Workforce Transformation
- 🔗 Adopt a Phased Approach to Efficiency Improvements
... but before we dive in, let's look at the current economic situation plant managers face in 2025.
Understanding the new manufacturing reality
Manufacturing has undergone significant transformations over the past several decades. From the NAFTA-driven exodus of manufacturing jobs to cheaper labor markets, to the housing market crash, to periods of economic stability—the industry has weathered many storms.
In 2025, we face a new challenge: tariffs and supply chain uncertainty have disrupted the status quo, forcing companies to rethink their global manufacturing strategies to be more flexible and nimble. This can be a blessing and/or a curse—depending on how you look at it.
For decades, chasing cheaper labor was the default strategy. Operations moved from the U.S to Mexico, from Sweden to Poland, from Mexico to China. But this cycle is breaking down. With new tariffs in place, many products manufactured in Mexico now face a high additional cost when entering the U.S. market. Similarly, operations in China face increased costs due to tariffs and geopolitical tensions.
This isn't just an economic shift. The move towards flexible manufacturing operations requires a fundamental change in how companies approach the way they operate.
The only question is - are you ready?
The plant manager's challenge
When supply chains are unpredictable, plant managers must adapt to daily challenges that require immediate action. This means everything from:
- Excessive changeovers consuming productivity
- Unpredictable material supply disrupting schedules
- Capacity constraints limiting output
The most successful plant managers are implementing nimble systems that provide crystal-clear direction on who needs to take action, what specific steps are required, when those actions must be completed, and where resources should be deployed. This level of operational clarity transforms reactive facilities into proactive, problem-solving environments.
As one plant manager at a leading automotive parts manufacturer told us:
"When supply chain disruptions hit, we needed to be nimble. The difference between surviving and thriving came down to how quickly we could redirect resources and adapt production schedules. Having contextual information at our team's fingertips at the moment of need made all the difference."
The hidden cost of downtime
With rising costs from supply chain disruptions (and tariffs), the cost per hour of downtime has become an even more critical metric. Even for smaller operations, thousands of dollars evaporate with each minute of unplanned stoppage. Today, this kind of waste is simply unsustainable.
For a typical automotive manufacturer, each hour of downtime costs $1–2 million.
The "Who-What-When-Where" dilemma
In uncertain times, clarity drives action.
Manufacturing facilities (many of them reshoring operations to the U.S.) are embracing flexibility in order to outperform their competitors. They're also implementing systems that provide instant visibility into the "who-what-when-where" to drive action:
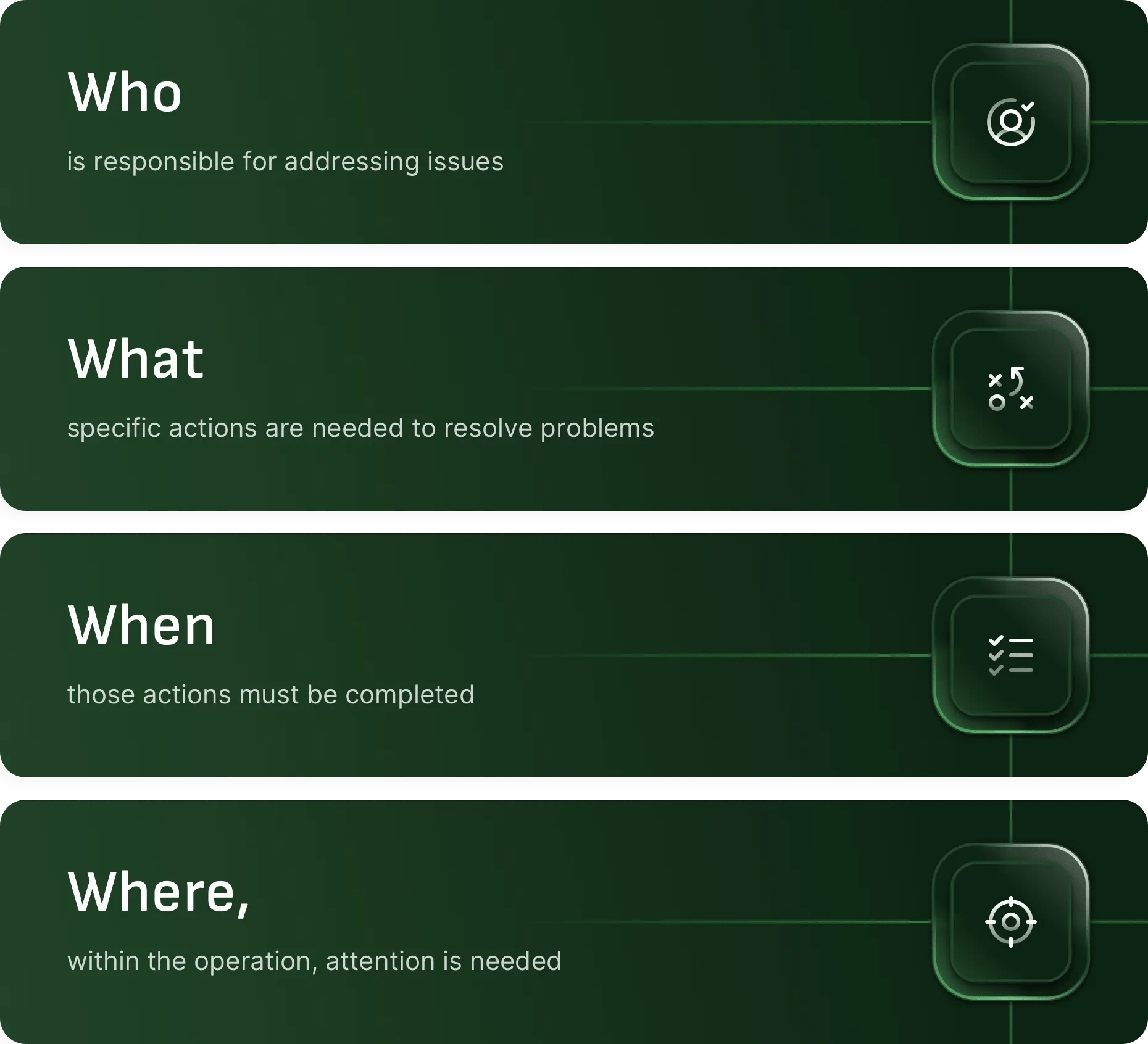
This simple but powerful framework eliminates the information gaps that often paralyze decision-making during supply chain disruptions. Rather than conducting multiple meetings to discuss who should handle emerging issues, you can use digital platforms to automatically dispatch the right information to the right people at the right time.
For instance, the impact of this approach is particularly evident during excessive changeovers—a common challenge in today's environment. By digitizing changeover procedures and providing step-by-step process guidance, plants have reduced changeover time by as much as 35% while maintaining quality standards.
As uncertainty becomes the new normal, the ability to drive clear, decisive action across all levels of the organization becomes the critical differentiator between plants that merely survive and those that thrive.
3 proven strategies to drive flexible manufacturing
1. Maximize existing plant capacity
Opening new manufacturing facilities is a long, expensive process. The companies adapting most successfully are focusing on getting more from what they already have.
Ask yourself: How can you increase production by 30% in your existing U.S. facilities to reduce reliance on importing products?
The immediate focus should be on unlocking hidden capacity in your current operations.
This approach aligns plant-level and corporate goals, streamlining decision-making in uncertain times.
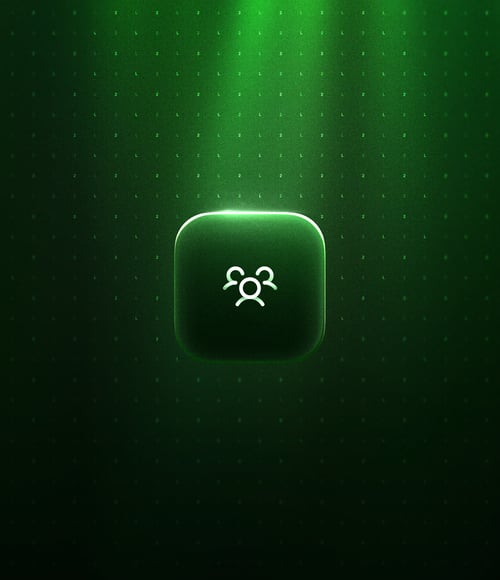
2. Invest in workforce transformation
While automation is part of the solution, companies are finding that the most valuable asset is often the human knowledge already on the factory floor.
As one major auto manufacturer discovered after attempting to fully automate, "the human mind is just another piece of automation"—one that's often underutilized.
The most successful manufacturers are implementing systems that capture worker insights, experience, and problem-solving capabilities.
This shift comes without the supply chain disruptions of importing physical automation equipment (which itself may be subject to tariffs). It's cost-efficient to collect data and insights that help you continuously improve your processes to stay flexible in the short term.
Forward-thinking plant managers are putting digital standard work at their teams' fingertips, similar to how YouTube has transformed learning at home. This approach allows them to rapidly upskill inexperienced operators when they need to run unfamiliar lines, putting players in the game who may have never run a line before and making them productive immediately.
Making sure your production lines are flexible is key to staying competitive.
The result? A more flexible manufacturing workforce that can adapt quickly to supply chain inconsistencies, excessive changeovers, and shifting production requirements, without relying on specialized labor that may be unavailable or too expensive.
3. Adopt a phased approach to efficiency improvements
Rather than attempting wholesale transformation, leading manufacturers are taking incremental steps:
- Phase 1: Focus on people, turning frontline workers into problem solvers
- Phase 2: Standardize processes across operations with flexible production lines
- Phase 3: Eliminate recurring errors and improve plan execution
- Phase 4: Scale solutions regionally‚ then globally
This approach allows for quick wins while building toward operational excellence across the organization.
By starting with targeted efficiency improvements in maintenance or changeovers, companies can demonstrate ROI before expanding to broader initiatives.
Flexible production lines as a competitive advantage
The current economic uncertainty presents both challenges and opportunities. When budgets tighten, the ability to be nimble becomes your greatest asset.
Companies that view this economic situation as a catalyst for efficiency improvements rather than a temporary disruption will emerge stronger.
By focusing on:
- Extracting more value from existing operations
- Transforming your workforce into nimble problem-solvers
- Providing contextual information that drives immediate action
- Taking a methodical, phased approach to transformation
Plant managers can unlock hidden capacity when every production hour matters more than ever.
You can not only weather this storm—but position your operations for a long-term competitive advantage.
The most resilient manufacturers won't be those who can relocate operations the fastest. They'll be the ones who develop unmatched flexibility in their existing operations and production lines.
In times of uncertainty, nimble and flexible manufacturing is your competitive advantage.
Ready to unlock hidden capacity in your plant?
- Are excessive changeovers consuming your productivity?
- Is your output limited by material supply chain issues?
- How flexible are your production lines when change occurs?
- Do you need to become more flexible without additional capital investment?
→ SCHEDULE A CONVERSATION TODAY
Revisions
Original version: 15 May 2025
Written by: Eric Whitley
Reviewed by: Mohsin Saeed
Please read our editorial process for more information
Related Posts
Subscribe to Our Blog
We won't spam you, we promise. Only informative stuff about manufacturing, that's all.