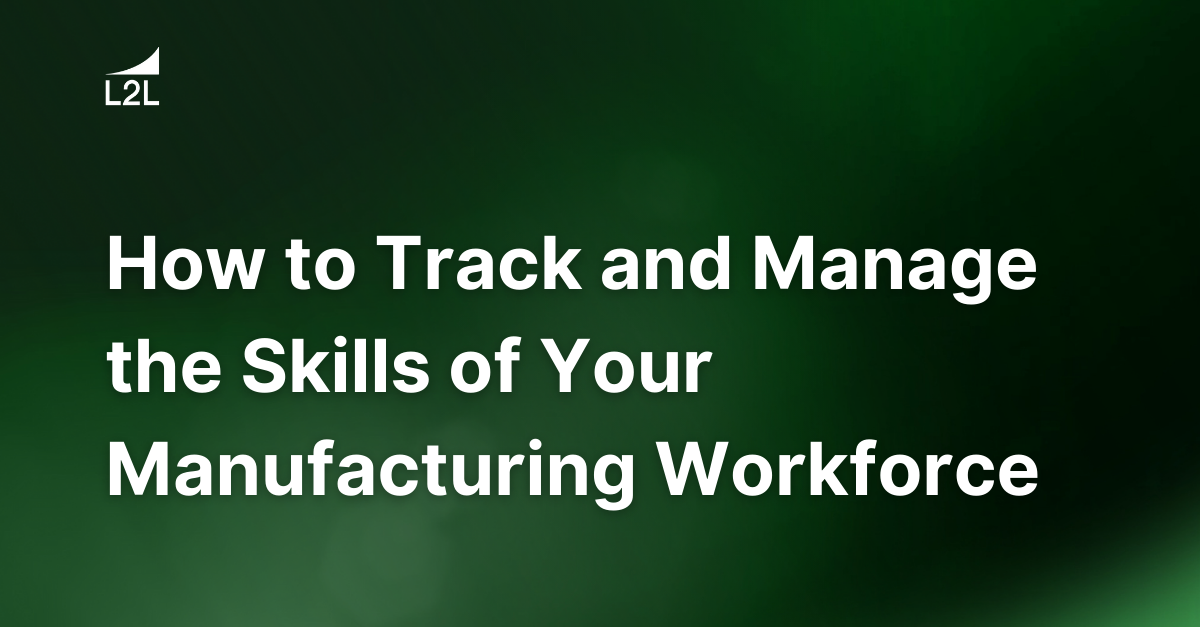
Concerns over hiring and retention are at an all-time high in the manufacturing industry. Among the top reasons for frontline worker turnover is manufacturing skills management. In other words, industrial companies are having a hard time retaining skilled workers due to weak training strategies, poor skill set utilization, and lack of upskilling opportunities.
However, developing and executing a successful skills tracking and management strategy comes with its fair share of challenges. For instance, quantifying and measuring skill levels (especially for soft skills) can be difficult. Without the right tools and systems, managing workers by skill type and proficiency can be time- and resource-intensive.
However, manufacturers can easily mitigate these challenges and dramatically reduce worker turnover with the right tools and resources. In this article, we’ll cover the importance of workforce skills management, practical strategies for tracking and managing skills, and how digital manufacturing technology can help.
Understanding skills tracking and management
Tracking worker skills and effectively delegating tasks according to those skills will always be an essential duty within manufacturing environments. Skills tracking and management typically happen in three stages:
-
Identifying critical skills
-
Determining the organization’s capacity to provide those skills
-
Equipping employees to meet the organization’s needs
Of these stages, manufacturers typically struggle with the third. Before we address how manufacturers can bridge the gap between worker skills and business goals, let’s take a closer look at the aspects of skills management.
What does skills management entail?
Manufacturing skills management is a dynamic and ongoing process to ensure that an organization’s workforce remains skilled and competitive as the industry evolves. It’s essential for maintaining a competent workforce and even improving worker retention.
Here are some of the primary components of skills management in manufacturing:
-
Skill Assessment: The first part of developing a manufacturing skills management system is determining which skills your business requires to keep production flowing. This involves a thorough analysis of job roles, tasks, and the skills needed to perform them efficiently.
-
Employee Skill Profiling and Tracking: To determine their workforce’s strengths and weaknesses, manufacturers evaluate their employees’ skills and competencies. Then, a skills profile is created for each worker. Any new skills or certifications an employee gains can be tracked through software like a connected workforce platform.
-
Training and Development: Comprehensive training programs are critical for addressing skills gaps and promoting continuous learning. Manufacturers can facilitate training and development activities through on-the-job training, online courses, or workshops.
-
Skills Database: Maintaining an up-to-date skills database allows manufacturers to collect and centralize employee skills data. This enables better skills matching and improves resource allocation.
As manufacturing technology evolves, a solid skills management system will help your workforce remain efficient, productive, and adaptable to change.
The importance of skills tracking and management in manufacturing
Despite rapid advancements in artificial intelligence (AI), machine learning (ML), and robotics, human workers remain the backbone of the manufacturing industry. That’s why developing a skills management strategy is so important; why wouldn’t you maximize your most critical assets’ potential?
The benefits of manufacturing skills management are manifold, but the top five include:
-
Increased Productivity: Successful skills management ensures that the right employees with the right skills are assigned to tasks, reducing errors and inefficiencies, and ultimately increasing production output.
-
Cost Reduction: By identifying and addressing skills gaps, companies can minimize training and rework costs while optimizing resource allocation.
-
Quality Assurance: A skills management system helps manufacturers maintain consistent product quality by ensuring that critical tasks are handled by qualified workers who follow best practices.
-
Adaptability: Manufacturers can quickly respond to changing market demands and technology advancements by identifying skill gaps and providing the necessary training, keeping the workforce versatile.
-
Talent Retention: Employees are more likely to stay with a company that invests in their skills development. This reduces turnover and the associated recruitment and training expenses.
Refining and broadening your workers’ skill sets helps your company stay competitive in virtually any market condition. Additionally, prioritizing skills management leads to better worker retention — a critical component of long-term success.
Building a skills inventory
To accurately measure and track your workforce’s skills, you need to build a skills inventory. A skills inventory is a catalog of skills that are relevant to the specific jobs within your organization. Typically in the form of a digital database, this skills catalog lets you view information about employee skills, qualifications, and competencies.
A centralized view of manufacturing skills data makes it easier to effectively manage workers and make informed decisions related to human resource planning, training, and task assignments. Creating one begins by identifying key skills across three categories:
-
Technical skills: Technical abilities and competencies crucial for performing physical manufacturing tasks, such as machine operation, quality checks, maintenance, data entry, and welding.
-
Soft skills: Interpersonal skills that enable harmonious working relationships. These can include communication, leadership, and critical thinking.
-
Adaptive skills: The ability to adapt, or “shift gears,” based on new information or changes in the working environment. In practice, this can include learning new technologies, methodologies, and techniques.
In the following sections, we’ll outline the process of establishing a skills management system in greater detail.
Methods of skills tracking in manufacturing
Manufacturers use a variety of methods to track workers’ skill levels. Below is a short list of the most commonly used skills tracking systems among industrial companies.
Skills matrix
A skills matrix is a visual framework that evaluates and categorizes employee skill sets and competencies. It typically lists employees on one axis and the required skills on the other, using a rating or color-coding system to indicate proficiency levels.
An example of a skills matrix template. Source: SlideBazaar
This method allows manufacturers to easily assess the skills of the workforce and match them to the needs of specific tasks or projects. When properly utilized, skill matrices help organizations improve resource planning and allocation — and better visualize skills gaps.
Periodic assessments
Periodic assessments involve scheduled evaluations of employee skills at specific intervals to track growth, identify areas for improvement, and measure performance. Three common types of periodic assessment include:
-
Direct assessment: Involves one worker directly evaluating another, usually through peer review or managerial observation.
-
Self-assessment: Requires employees to assess their own performance through periodic surveys.
-
Anonymous peer assessment: Involves workers anonymously observing others’ performance on the job.
Digital tools and software
Manufacturers can also use digital applications to assess employee performance. Some manufacturers opt for a learning management system (LMS) as their preferred method, where employees can provide training updates and track their progress. Many HR systems can serve the same purpose.
Larger organizations will likely require more robust digital skills tracking technology. For instance, today’s integrated skills management systems use AI technology to gather worker data on the job and document performance instantaneously. Combined with connected worker technology, these solutions can provide real-time feedback and guidance as workers perform tasks.
Solving skill gaps through upskilling
As employee turnover rates climb, manufacturers must act fast if they want to keep skilled workers in their plants. Not only do retention issues cost companies millions in training and slowed production, but they also create massive skill gaps if qualified workers don’t stay long enough to address those gaps.
Upskilling has drawn significant attention as a means to solve the problem of manufacturing skill gaps. In theory, it’s more economical to train existing workers in new techniques and methodologies than to hire someone else to perform them. Upskilling and cross-training also give your employees opportunities for advancement and promotions, encouraging longer tenures.
If you’re thinking about creating an upskilling program within your organization, here are some basic offerings that can make a big difference in your employee experience:
-
Training programs: Create structured training programs that allow workers to learn new skills and technologies that are relevant to your organization’s needs and will help them level up in their careers. These can include classroom training, on-the-job training, digital modules, or a combination of each.
-
Cross-training: Similar to upskilling, cross-training allows workers to learn new skills — but with the main purpose of increasing workforce adaptability and flexibility. While the skills gained this way may help workers advance their careers, cross-training is designed to boost their value at their respective levels.
-
Certifications: Certifications are prerequisites for many manufacturing jobs. By giving your employees the chance to earn certifications and use them within your organization, you’ll incentivize them to stay long-term.
While upskilling won’t completely solve the global labor shortage, it helps manufacturers attract and retain skilled workers by providing opportunities for professional growth.
Technology for effective skills management
In addition to skills inventories and tracking methods, manufacturers can use advanced digital technologies to streamline professional development and skills management.
You can use the following technologies to enhance your skills management system:
-
AI and ML: AI and its subset, ML, can aid in manufacturing skills management practices by using algorithms to both analyze and guide worker performance. Furthermore, they can help organizations identify their workforce’s strengths and weaknesses while predicting skills trends and future needs.
-
Virtual Reality (VR): VR is playing an increasingly important role in manufacturing training programs. Using devices like headsets, computers, and even smart glasses, workers can complete training activities in simulated environments that mimic real-world factory scenarios, enabling them to gain near hands-on experience with no risk involved.
-
Data Analytics: By analyzing vast amounts of data on employee performance and training progress, manufacturers can make more informed decisions about skills management, hiring, and resource allocation.
-
Skills Tracking and Management Software: Today’s skills tracking and management software helps manufacturers gain a full picture of their workforce’s skills and qualifications. Oftentimes, skills management features are built into solutions like connected worker platforms and HR systems, but you may need to purchase software specifically designed for that function.
Smart technologies like these require a significant upfront investment. However, their enhancements to the skills management process result in long-term cost savings, productivity gains, and even improved workforce retention.
Simplify manufacturing skills management with L2L
Keeping your workforce current on job-specific training, industry standards, and emerging manufacturing technologies is non-negotiable in today’s market conditions.
Connected worker solutions like L2L empower manufacturers to track and manage worker skills with easy-to-use visualization, analytics, and reporting capabilities. L2L’s skills management tools let you monitor employees’ training progress and automatically notify you when it’s time for recertifications. Compliance management is easy, too, with built-in skills charts and automated procedure non-compliance alerts.
With a detailed real-time view of your workforce’s skills and certifications, you can make data-driven decisions with confidence. But don’t take it from us — see for yourself when you explore our Product Tour and Demo Video Page!
Revisions
Original version: 8 November 2023
Written by: Evelyn DuJack
Reviewed by: Daan Assen
Please read our editorial process for more information
Related Posts
Subscribe to Our Blog
We won't spam you, we promise. Only informative stuff about manufacturing, that's all.