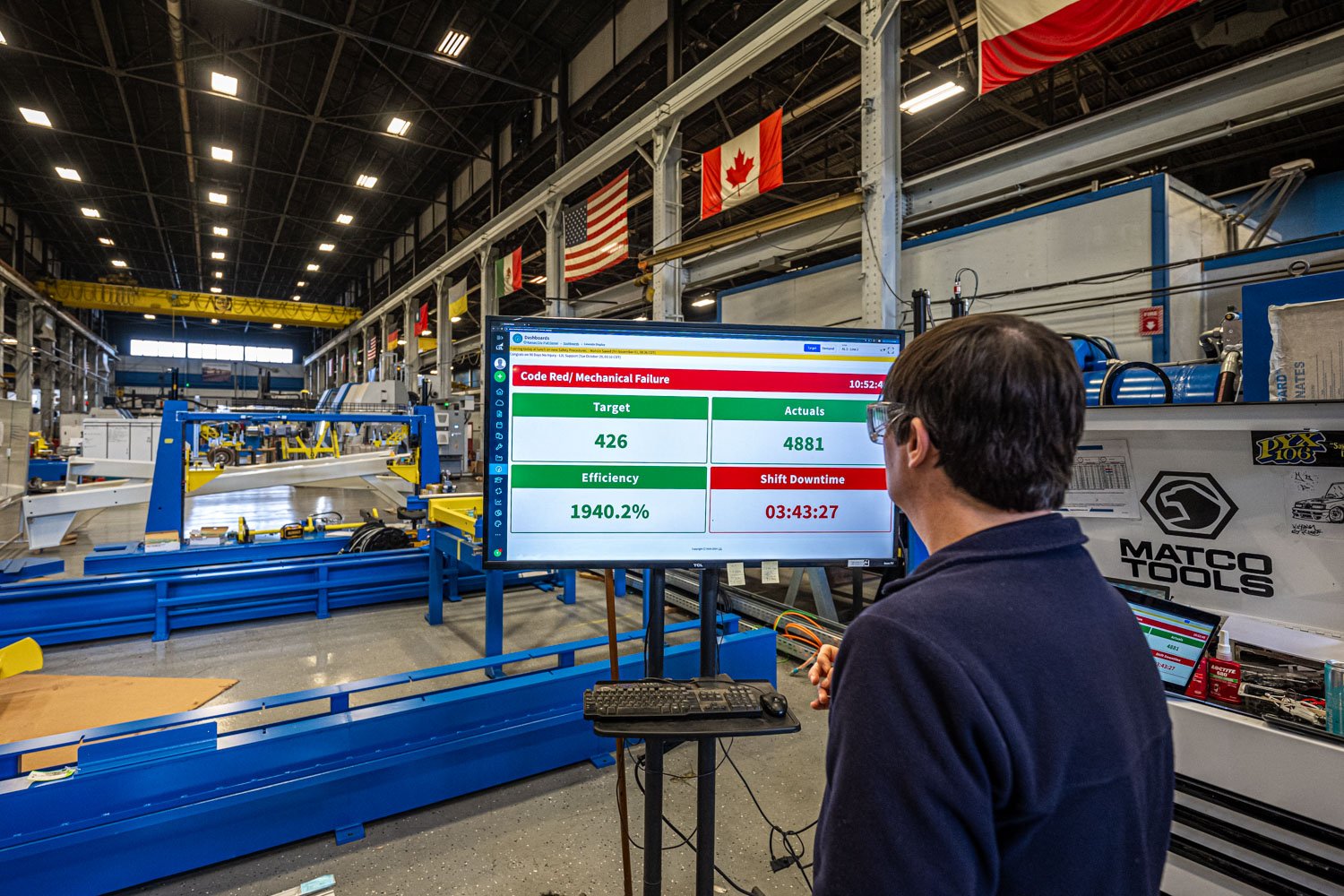
In the wake of the global pandemic and current geopolitical conditions, industries worldwide continue to face significant challenges due to supply chain disruptions and material shortages.
These shortages disrupt production schedules, inflate costs, and complicate inventory management, highlighting the critical need for effective material shortage management strategies.
This article provides a quick overview of what constitutes a material shortage, its causes, and its economic impact on manufacturing. We'll also explore strategic responses and preventive measures that manufacturers can implement to navigate and mitigate these shortages efficiently.
Material shortages: Definition, causes, and economic impact
A material shortage is a situation in which the necessary raw materials or components required for production are insufficient, unavailable, or delayed in reaching the production facility.
Let’s see what causes them and how they affect production.
What can cause a material shortage?
Material shortages can stem from a variety of sources, which can be external or internal. Common causes include:
-
Supply chain disruptions: Unexpected events such as natural disasters, geopolitical tension, or pandemics can interrupt the flow of materials from suppliers to manufacturers.
-
Materials lost in transportation: Issues during transportation, including accidents, theft, or logistical errors, can result in materials not arriving at their destination on time.
-
Poor inventory management: Inadequate internal tracking of material usage and poor procurement practices can lead to unexpected shortages.
-
Inaccurate forecasting: Failure to accurately predict demand can result in either a surplus or shortage of materials, both of which are costly.
-
Excessive scrap and rework: Inefficient production processes resulting in high amounts of waste can deplete usable materials faster than planned.
Effects of material shortages on production
The ramifications of material shortages are far-reaching and can severely impact the operational and financial stability of a manufacturing entity. Key effects include:
-
Decreased productivity: Without the necessary materials, production lines may slow down or halt, reducing overall output.
-
Lost profits: Delays in production lead to delays in sales, directly affecting the bottom line.
-
Production delays and missed deadlines: Inability to meet production timelines can cascade into delays in product availability in the market. Failing to deliver products on time can breach contractual obligations with customers.
-
Damaged customer relationships: Consistent inability to meet delivery schedules can erode trust and damage long-standing business relationships.
Manufacturers need to prioritize and address material shortages proactively to minimize these disruptions and maintain a competitive advantage.
Bonus guide! Learn how to stay ahead of downtime-causing disruptions:
How manufacturers can navigate material shortages
There isn’t a strategy that can make a production plant completely immune to material shortages.
However, there are specific steps manufacturers can take to prevent internal causes of shortages. Plus, they can set up systems for minimizing the negative effects on production and address shortages when they occur.
Stopping preventable material shortages
Effective material shortage management requires manufacturers to be proactive. They need to focus on enhancing production efficiency and supply chain resilience by:
-
Optimizing inventory management: Modern inventory management systems help maintain optimal stock levels through real-time tracking and automated replenishment systems. This reduces the risk of running out of essential materials.
-
Improving forecasting accuracy: Employing sophisticated forecasting tools that incorporate real-time data and predictive analytics can significantly improve demand planning. This allows manufacturers to adjust production schedules and material orders based on accurate market insights and trends.
-
Reducing scrap and rework: Implementing quality control measures at each stage of production can minimize waste and inefficient use of materials. Training staff in best practices and implementing Poka-Yoke, Andon, and other lean manufacturing methodologies can further boost production efficiency.
-
Strengthening supplier relationships: Building strong, collaborative relationships with suppliers ensures better communication, data sharing, and reliability.
-
Developing a comprehensive risk management plan: This includes dentifying potential risks in the supply chain and developing strategies to mitigate these risks. A risk management plan should include detailed actions for different scenarios, including alternative sourcing strategies and emergency funds.
Quickly addressing material shortage situations
Even with the best preventive measures in place, material shortages can still occur. In these situations, there are several reactive measures to consider:
-
Establishing a rapid response team: Setting up a dedicated team to handle material shortages facilitates quick decision-making. This team should have clear authority and access to necessary resources to act as quickly as possible.
-
Utilizing alternate suppliers: When usual supply channels fail, having pre-vetted alternate suppliers can be a lifesaver. Using backup suppliers and integrating them into your supply chain planning allows for quick pivots when necessary.
-
Revising production schedules: Temporarily adjusting production schedules to prioritize products with available materials can help maintain output and meet critical delivery timelines.
-
Implementing substitution protocols: If specific materials are unavailable, having pre-approved substitution protocols can help maintain production continuity. To ensure product integrity, these protocols should be developed with input from engineering and quality assurance teams.
Steps for implementing a material shortage management system
Implementing a comprehensive material shortage management system is predicated on having access to the right tools, technologies, and procedures.
First, manufacturers need access to real-time production and inventory data. This can be realized through an ERP, MES, connected workforce platform, dedicated inventory management software, or a combination of the aforementioned solutions.
These tools can communicate with Internet of Things (IoT) sensors to provide real-time insight into production processes, equipment conditions, levels of materials in stock, etc. Based on received data, they can use predictive analytics and AI to forecast future material needs and help optimize production schedules.
With all of that data at their disposal, managers can set and track KPIs for material management and implement contingency plans and procedures for handling material shortages.
Streamline material shortage management with L2L
L2L is a connected workforce platform that gives manufacturers the tools they need to effectively respond to any type of production disruptions and optimize their manufacturing operations.
It simplifies material shortage management through:
-
Real-time visibility: L2L provides real-time data across your manufacturing operations, enabling quick identification of potential material shortages and allowing for immediate action to mitigate risks.
-
Improved communication: With L2L, communication barriers are broken down as the platform facilitates seamless information sharing between departments and external suppliers. This ensures that everyone is on the same page and can act quickly in a coordinated manner.
-
Data-driven decision-making: The platform's analytics capabilities help manufacturers make informed decisions based on accurate and timely data. This can include adjusting production schedules, reassigning resources, and optimizing inventory levels based on predictive insights.
-
Scalability and flexibility: L2L's scalable solutions adapt to your business needs, whether you are a small manufacturer or a large enterprise, providing customized tools that grow with your company.
-
Proactive problem solving: L2L's features like automated alerts and workflow management help prevent material shortages by proactively managing the early signs of supply chain disruptions.
It's never too late to start being proactive. Schedule a demo today to see how L2L can help you better manage material shortages and transform your production processes.
Revisions
Original version: 27 June 2024
Written by: Evelyn DuJack
Reviewed by: Daan Assen
Please read our editorial process for more information
Subscribe to Our Blog
We won't spam you, we promise. Only informative stuff about manufacturing, that's all.