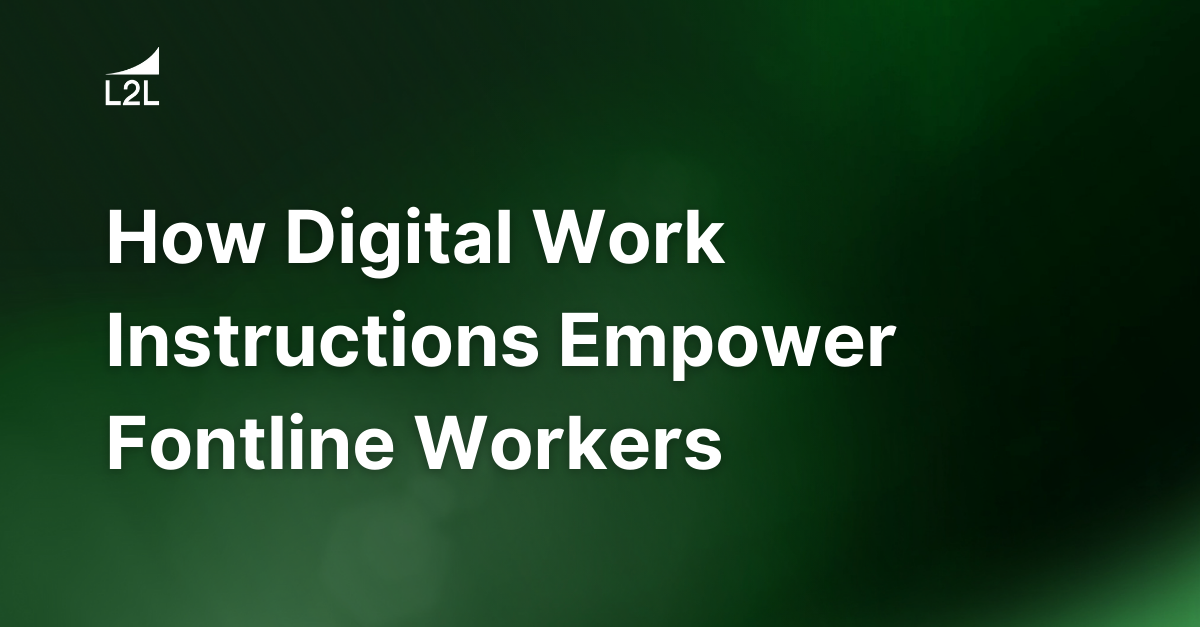
In the rapidly evolving landscape of the manufacturing sector, staying competitive necessitates not only innovation in product design and production methods but also in the ways we support and empower the workforce—particularly the frontline workers. These individuals are the backbone of manufacturing operations, directly involved in the production and assembly processes that turn raw materials into finished products.
As technology reshapes industries, digital work instructions have emerged as a crucial tool in enhancing the efficiency, productivity, and job satisfaction of frontline manufacturing workers. This article explores the transformative potential of digital work instructions, highlighting their importance in empowering workers and boosting overall productivity in the manufacturing sector.
Shifting work instructions from paper to digital
Traditionally, work instructions in manufacturing have been paper-based, meaning they could be hard to find, update, and standardize. Digital work instructions represent a paradigm shift, offering dynamic, interactive, and easily accessible guides through tablets, smartphones, or other digital devices.
This transition from paper to digital is not merely a change in format; it's a fundamental improvement in how we can help workers perform their jobs better, giving them intuitive instructions when and where they're needed.
Enhancing accessibility and clarity
One of the most immediate benefits of digital work instructions is the improved accessibility and clarity they provide. Workers on the shop floor can instantly access up-to-date guides, videos, and diagrams that clearly illustrate complex processes, reducing ambiguity and the likelihood of errors. This clarity not only improves the quality of work but significantly reduces the time spent on training and onboarding new employees, allowing them to become productive members of the team more quickly.
Facilitating real-time updates and feedback
In the fast-paced environment of manufacturing, changes and updates to processes are frequent. Digital work instructions can be updated in real time, ensuring that all workers have access to the most current and accurate information. This capability is crucial for maintaining quality standards and adapting to new production requirements swiftly.
Furthermore, digital platforms enable two-way communication, allowing frontline workers to provide feedback, suggest improvements, and report issues directly through the system. This feedback loop fosters a culture of continuous improvement and innovation, which empowers workers to contribute actively to process optimization.
Boosting productivity and efficiency
The impact of digital work instructions on productivity and efficiency is profound. By providing clear, accessible, and up-to-date guidance, these tools help minimize downtime, reduce errors, and streamline production processes. Workers spend less time seeking clarifications and more time focusing on their tasks, leading to significant gains in overall output.
Additionally, the ability to track and analyze the performance of different processes through digital platforms enables managers to identify bottlenecks and areas for improvement, further boosting productivity.
Supporting a safer workplace
Safety is paramount in manufacturing, and digital work instructions play a vital role in promoting a safer work environment. By incorporating safety guidelines and precautions directly into the work instructions, workers are constantly reminded of the correct procedures to prevent accidents and injuries. Digital platforms can also be used to conduct safety training, ensuring that all employees are knowledgeable about the latest safety standards and practices.
Fostering employee engagement and satisfaction
Empowering frontline workers goes beyond providing them with the tools to perform their tasks efficiently. It also involves engaging them in the process and making them feel valued.
Digital work instructions facilitate this engagement by involving workers in the continuous improvement of processes, recognizing their contributions, and providing them with opportunities for learning and growth. This engagement not only boosts job satisfaction but also motivates workers to take ownership of their roles, leading to higher-quality work and greater productivity.
Modernize work instructions with L2L
The shift towards digital work instructions in manufacturing speaks to the industry's commitment to empowering frontline workers. By leveraging the potential of digital technologies, manufacturers can enhance the efficiency, productivity, and job satisfaction of their workforce, driving improvements in output quality and operational performance.
Technologies like L2L's connected workforce platform are designed to empower frontline workers with the right knowledge at the right time. Providing immediate access to updated work instructions and training documents, L2L keeps workers safe, on-task, and performing at their best — maximizing shop floor efficiency and fostering a culture of continuous improvement and collaboration.
See how L2L transforms the way manufacturing employees work by taking our Interactive Product Tour.
Revisions
Original version: 14 March 2024
Written by: Malcolm Faulds
Reviewed by: Daan Assen
Please read our editorial process for more information
Related Posts
Subscribe to Our Blog
We won't spam you, we promise. Only informative stuff about manufacturing, that's all.