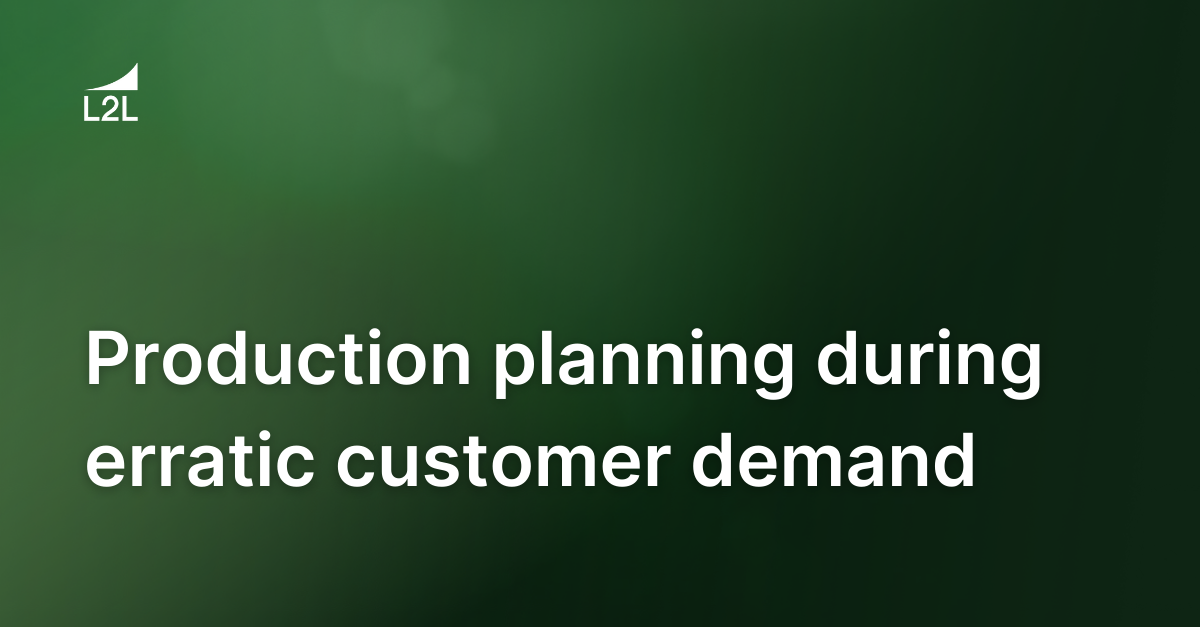
Production planning during erratic customer demand can be extremely challenging because the drastic shifts in demand result difficult to manage.
Looking back at successful manufacturing organizations I have seen and worked with in the past, many have a tremendous ability to respond to the ever-changing fluctuations in production demand. This is not an easy task; however, it can be done and is almost a prerequisite in order to stay competitive and maintain the ability to continue producing.
A Production Planning Yokoten (from Me to You!)
The manufacturing facilities that can quickly add or subtract demand in sharp increments are better able to survive and endure difficult times. These large fluctuations in customer demand bring many challenges such as issues with labor, materials, operational availability, or possibly a large increase in customer demand that exceeds the facility's overall capacity.
The common key to success (a.k.a., yokoten or lessons learned) that I have observed repeatedly in all of these successful world-class manufacturing organizations is the ability to "Get Back to The Basics." The ability to utilize key tools and methods during challenging times.
We have no control over many of the inputs and problems that we experience during these drastic shifts in customer demand. However, there are basic practices that have consistently proven themselves. Applying these to your production planning can lessen the burden during these challenging times.
Operational Availability for Improved Production Planning
Understand and truly honor the reality of your demonstrated OA (Operational Availability). In other words you must understand and have a proven % of demonstrated OA. If your OA is 70% demonstrated over time then you may expect to see 30% Equipment Downtime.
You must have an objective method to understand and measure OA. During difficult times, it is imperative that when the machine is expected to run, it runs effectively and efficiently, every time. Therefore, it's important to also have a method to quickly identify/eliminate all causes of Systemic Downtime.
Make Use of Production Planning Tools
Having a robust production planning tool can be the make or break during these periods. A tool like an LES gives you:
- Capability and flexibility to quickly respond to drastic shifts in customer demand.
- Capability to level load hourly/daily changes in Customer Takt Time for all manufacturing areas.
- Quickly identify potential capacity concerns.
- Understand all manufacturing lines/cells capacity vs demand.
- Plan appropriate production time/resources based upon current volumes.
- Follow up remote live Production Actual vs Demand.
Make Use of Labor Planning Tools
Today's LES Tools provide a flexible planning platform used to indicate the most efficient labor across all ranges of your Takt Time such as the ability to identify the best labor scenario at any given Takt Time, whether reduced or increased. You need the ability to make educated decisions where labor is best utilized.
This approach assumes that you’ve already addressed the issue of having flexible product lines or cells. Processes that require a fixed number of resources to run regardless the demand puts you in a losing position from the start and limits your ability to efficiently react to fluctuations in demand.
Keep Score with Real-Time Dashboards
Are we winning or are we losing? Remotely monitor live production dashboard views with the ability to review all production metrics such as, Quality, OA, OEE and PEFF. The tools must have the ability to understand current condition and make rapid changes.
Pay Attention to Constraint Management
Can we quickly/remotely identify current status of constraints? Is the machine running? How long has it been down? Constraints change quickly and rapidly during times of erratic production, so the ability to monitor current and future constraints is important.
Having a system that can visually communicate priorities and constraints will be a game changer here!
Master Your Resource Utilization
Similar to constraint management: Are we utilizing our resources on the right issue or project? Times like these are typically very lean, so we need to focus on doing more with less. We must utilize the limited resources on the right situation, and at a glance, remotely account for the current location of all our resources.
Again having a system that can communicate priorities will direct resources to the most important and critical issues first. Basically automating you’re resource management to ensure the right resource are addressing the right issues at the right time.
Better Production Planning Starts Here
In order to achieve the flexibility needed to react to the erratic shifts in Customer Demand we must utilize the tools and methods available today. These tools allow us and provide us the capability to Plan, Do, Act, Check and Repeat.
These lean tools provide the ability to "Get Back to the Basics". Use the tools and methods that have proven themselves time after time to be very effective. In today's troubled times one of the great advantages of using a modern digital LES like L2L is navigating and engaging tools remotely.
Revisions
Original version: 18 July 2024
Written by: Evelyn DuJack
Reviewed by: Daan Assen
Please read our editorial process for more information
Related Posts
Subscribe to Our Blog
We won't spam you, we promise. Only informative stuff about manufacturing, that's all.