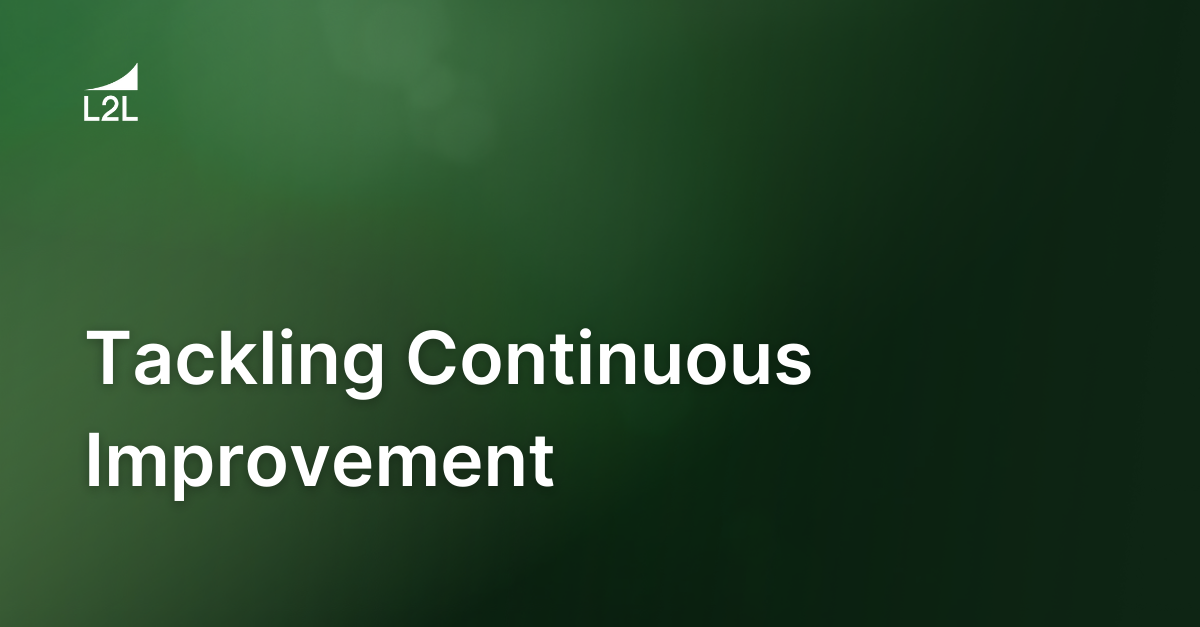
Continuous improvement is the ongoing practice of implementing change to better products, processes, or services. Several methods to achieve continuous improvement leverage data, analytics, experience, and observation to identify and pursue opportunities for improvement. This includes DMAIC (Define, Measure, Analyze, Improve, and Control) and PDCA/PDSA (Plan, Do, Check/Study, Act).
Historically, continuous improvement practices have been applied in manufacturing environments. With the proven success in production, many firms expanded these techniques to business processes, such as Purchasing or Safety. This has led, in recent years, to the service industry adopting continuous improvement tenets.
Basic Continuous Improvement Management
While there are multiple models to follow for continuous improvement management, the four steps outlined in Deming’s Cycle (PDCA/PDSA) demonstrate their general collective process.
Plan:
Identify an improvement and determine how to achieve that objective. When starting a continuous improvement journey, this often seems like the easiest step; people tend to have their anecdotal ideas of the bottlenecks and defects plaguing their processes and output.
However, it is critical to analyze the current state thoroughly: capture the workflows present, the desired outcomes of these workflows, and the metrics which indicate performance against those goals.
Once the business knows objectively where it stands, it can determine where it wants to be against those same measurable criteria and identify all the avenues to get there. Defining the current and future states of the business in quantifiable terms ensures projects with maximal value to the business are prioritized.
Example: If quality metrics for a bank indicate a 10% error rate in the past year on loan paperwork completed by customers, the bank could define a goal of achieving no more than a 5% error rate by the end of the following year. Working with loan officers and processors to capture the most common errors observed (such as missing entries or wrong information completed) a plan is developed to transition the paperwork to an electronic format with fields requiring completion before submission and with entry fields restricted to only numerical inputs.
Do
With the implementation plan established, the next step is to execute the plan. However, the “Do” stage is not a thoroughgoing application of the selected changes. It is meant for metered implementation of change and subsequent data collection around the affected workflow. A small-scale approach and monitoring of impact ensures that any unintended consequences can be identified in the next “Check” phase and contained with minimal effect on the business overall.
Example: The example bank develops an electronic version of its loan paperwork with required fields and restricted field formats based on the original errors observed. The electronic form is deployed at a single branch of the bank alongside a process for the existing loan officers to review the electronic submissions and record any errors observed.
Check/Study
Once a pilot change has been established and the new workflow is generating data on its performance, the business studies the information gathered. The pilot results must be compared against the expectations established in the “Plan” stage to determine whether the change had a measurable impact on performance as expected.
If a negative effect or insufficient improvement is realized, the business returns to the prior “Do” phase to trial alternative or modified solutions. For changes proven successful, the project then moves into the “Act” stage.
Example: According to the data collected at the trial bank branch by the loan officers on the electronic loan paperwork, the current version of the electronic document produced a 7% error rate. Therefore, because the desired error reduction to 5% was not achieved during the trial, the bank will return to the "Do" phase and reconsider design of the electronic document, required field, and entry formatting restrictions. The revised document will then be reissued for trial.
Act
In this stage, a trialed change with demonstrated improvement is installed as the new standard for applicable workflows going forward. The tested improvement is deployed to all applicable processes as the new standard, and the supporting business infrastructure is updated to reflect and to sustain this new mode of working.
Example: After observing a 4% error rate at the trial bank branch using the revised electronic loan paperwork, the paperwork was released for use across all the bank branches. Training was provided to all loan officers on the contents of the loan paperwork, and a link for the electronic documents added to the bank member website. All paper copies of the document are removed from each bank branch and obsoleted in the bank’s document control system.
Sustaining Continuous Improvement
It is important to note that the Deming Cycle and continuous improvement overall is an iterative process. A project through the “Act” phase establishes a new baseline for the operations and becomes the groundwork on which to create further change.
Therefore, the metrics identified in the initial “Plan” phase must continually be monitored to target additional gains and also ensure that improved workflows do not revert to their old ways. Perpetuating this cycle may seem like a large management task; however, designing a company’s continuous improvement program with the following elements will instill it in the company culture as standard way of working.
- Make it visible - Provide everyone across the company visibility into the company’s continuous improvement efforts. This includes access not only to the c-suite metrics but also their root process indicators as well improvement projects being proposed, trialed, and implemented. When individuals across the organization can see how their workflows and output impact the business at a whole, it can encourage them to raise concerns and share ideas.
- Make it participative - Inviting employee participation through a visible continuous improvement process requires ready means by which people can request support and submit ideas. Subsequently, businesses must act on employee inputs, particularly with a visible request management system: taking action on employee-generated items creates a sense of involvement and buy-in around the company’s objectives. This drives further employee engagement and continues the cycle of improvement.
- Make it accountable - Along with showing every employee how their work ties into the business's final performance measures, responsibility for achieving these goals must be cascaded to each department and group through their own meaningful metrics. This disperses the drive for success throughout the company, inspiring each person to take action by the means they control, whether reporting roadblocks, removing obstacles, or designing improvements.
Although there seem to be many elements to the continuous improvement process and managing it within the business, an off-the-shelf lean execution system (LES) such as L2L's CloudDISPATCH is ready to meet these needs. Whether standalone or partnered with existing MES, ERP, and/or CMMS systems, L2L’s modules are built to capture the current state of the business, capture workflow faults, and manage project execution while remaining accessible and visible to all employees.
Revisions
Original version: 31 January 2020
Written by: Amy Mele
Reviewed by: Daan Assen
Please read our editorial process for more information
Related Posts
Subscribe to Our Blog
We won't spam you, we promise. Only informative stuff about manufacturing, that's all.