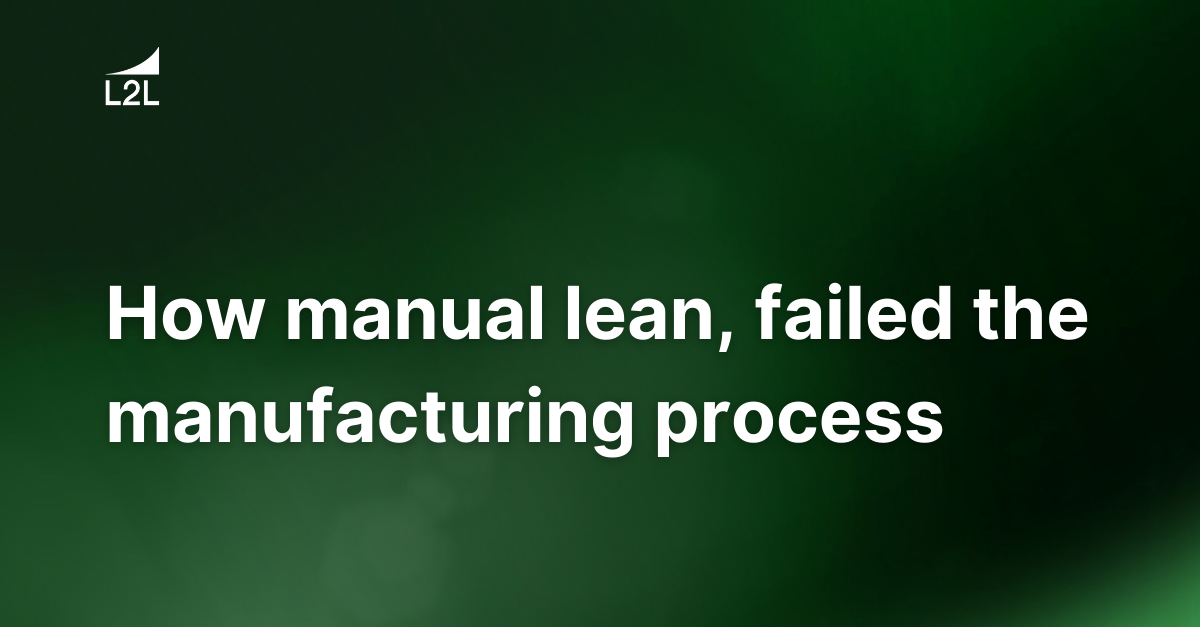
As a student of lean manufacturing myself, early in my career I was challenged to transform a large multi-national consumer electronics company into a lean manufacturing organization. Meanwhile I was a supervisor on third shift, barely keeping my eyes open between my routine strolls around the shop floor.
The Manual Manufacturing Process We All Know
It's safe to say I managed by walking around. Not only did it help to keep me awake, but it was a great way to get to know the process and the people, most importantly. The company even provided some sleeping material in the way of a few lean books such as "Andy and Me", "The Toyota Way" and "Creating a Lean Culture." These books were and continue to be staples in the management and cultural transformation of lean in manufacturing process. I personally probably never read any of them cover to cover, but cherry-picked the nuggets relevant to whatever challenges the plant faced.
We had a corporate lean organization at the time who would identify waste opportunities and then leverage lean events or Kaizens to focus on improving the process. I was fortunate to participate on these events and even lead a few.
Most were week long events comprised of a cross-functional group of hourly and salary colleagues. The hourly colleagues were always a bit skeptical of the whole thing, as it usually ended up with them being the guinea pig of our cardboard, makeshift manufacturing process. And we would move their "cheese" sometimes multiple times before landing on a semi-improved process.
Following these events we would often manually develop kanban cards, metrics on white boards and standard work to ensure success. Long-term, we always struggled to sustain the gains and would often backslide when orders got tight or staffing was short.
One time, we even rolled out a paper ticket process for capturing small "Ks," (or mini kaizens) and also a defect tag process. This sounded like a great idea until we engaged 500 people and the machines looked like a Christmas tree on New Year's Day, dangling with dozens of pink and yellow tags. I'm sure – to this day –there are still a few oil-soaked tags hanging.
But you couldn't knock us for trying: We took the principles from the lean consultants and publications and did what we thought was the right thing to do. We really had no choice, as our industry was globally competitive and manufacturing processes stateside were under the gun.
Most of the books and consultants we relied on during our lean journey preached start small, start manual. So, we did, despite it leaving us with limited results and stacks of kaizen cards with no plan in sight for actually getting them completed.
Your Manufacturing Process Must Be Digital
Back in 2009 I was introduced to L2L by my corporate maintenance manager who had heard about it at a lean conference. He was really impressed with how it helped an automotive company transform the way they managed lean principles and execution.
He went out on a limb and signed us up, implementing it in our plant. For once, this system opened a glimmer of light in an otherwise dark tunnel.
I have since moved on from that company after 10 good years...only to join L2L, as luck would have it. This also allowed me to work closer to where I grew up. I was on a call last week with a customer in China who made a comment that prompted this blog.
He said "This is the first time that I have ever seen in my career where a manual lean or manufacturing process just doesn't work." His plant was coming out of a month long hiatus as a result of Covid-19, and he and his support staff were forced to manage the workforce from home.
He said "Without L2L I don't know what we would have done." I shared the same feeling after implementing the system 10 years ago in my first plant.
The manual lean process in theory is sound: But my experience working with hundreds of manufacturing plants all over the world is that it simply isn't sustainable. It can work in small pilot areas where you focus enormous amounts of time babysitting the improvement, often with a consultant, but for most that just isn't an option and doesn't scale fast enough.
In addition, all plants are streamlining their salary staff. As a result, managing manual systems creates an even greater burden on the manufacturing process...in addition to just putting out fires and getting product out the door.
Fortunately, there are digital lean execution systems like L2L that make it exponentially easier to not only manage with lean principles but do it from anywhere. Even your couch, if you have been cooped up there for the past several weeks like me.
You don't have to be another victim of the manual lean fiasco. Digital lean execution systems like L2L are making it easier than ever to manage using lean principles, and also scale and engage everyone on the shop floor. Don't wait for the next financial or health crisis to cripple your operation.
Revisions
Original version: 18 July 2024
Written by: Evelyn DuJack
Reviewed by: Daan Assen
Please read our editorial process for more information
Related Posts
Subscribe to Our Blog
We won't spam you, we promise. Only informative stuff about manufacturing, that's all.