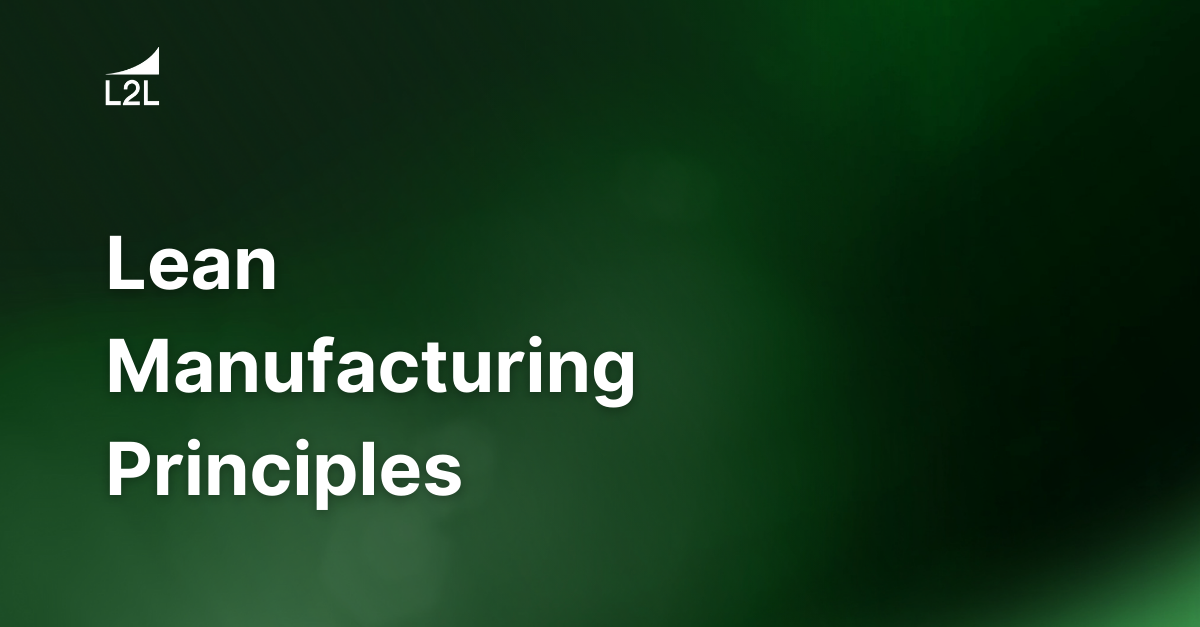
You may have read our popular article, “What Is a Lean Manufacturing System?” by now, where we discuss the basic principles of lean manufacturing. If that post left you wanting to learn more, you’re in luck; we’re about to embark on the next chapter of our Lean pilgrimage.
Now that you understand the basic philosophy behind a digital lean system, let’s dig a bit deeper into the principles.
Lean Manufacturing Principles
Lean Manufacturing principles are as follows:
-
Identify Value
-
Map the Value Stream
-
Create Flow
-
Establish Pull
-
Seek Perfection
Let's take a closer look at each of these lean manufacturing principles.
1. Identify Value
Why would "identify value" be the first lean manufacturing principle?
Unless you have a clear understanding of what is valuable — and of the most value — how can you seek to attain it?
What does every business value? Money, profits? Sure, those are handy. But those are byproducts of providing value. Producing the best product? Yes, there is value in all of those things. But they are not the value.
Value is defined by the customer and no one but the customer. Value, in the eyes of the customer, is everything the customer is willing to pay for. Think "value-added." Customers do not pay for and do not value anything but the product itself. Non-value-added equals anything that does not increase the desirability of your product (think waste elimination). Seeking to maximize value is the emphasis behind Lean Manufacturing.
-
Creating products that individual customers want = Value
-
Eliminating what customers don't want in the product = Value
When we understand value in terms of lean manufacturing principles, value is the principal principle — the cornerstone of all that is lean manufacturing. That means you need to do whatever is required to preserve and increase Value as perceived and defined by the customer. That's the bottom line.
Remember this: Value is the principal principle, the primary premise around which all else is built. These alliterations are a great little brain trick to point you toward the lean manufacturing "promised land": Value; Customer Satisfaction, and Successful Business.
2. Map the Value Stream
In order to map the value stream, you must first know what a value stream is and how to identify one.
In lean manufacturing principles, a value stream is a series of steps, or a sequence of activities, from the start of creating value (producing a product) through its completion (delivering it to the end user). A value stream encompasses all the processes required to design, produce, and make available your product, goods, or service to the customer.
The name alone conjures images of gentle flow. They didn’t name it value typhoon or value raging rapids. A value stream is a path along which all information, materials, and processes travel to create value: the product.
A value stream is where and how information, materials, and processes work in unison to create value for the customer. It's the vehicle utilized to create and bring value to the customer. A Value Stream helps identify potential causes of waste and eliminate that waste from the production process, creating the most efficient system possible.
Value stream mapping, therefore, is a way to keep track of a product as it travels through the process. Value stream mapping is a physical illustration that starts with the introduction of raw materials to the facility at the very beginning of the lean manufacturing process.
The value stream map then follows those materials throughout value-added manufacturing processes, ultimately arriving at the final destination: the point where the customer pays for the product.
Value stream mapping is a critical lean manufacturing principle. Without a map, we don’t know where to start, where to go, or where we’ve been. Value stream mapping is invaluable to capturing current state, where all critical steps are displayed, and time and volume are quantified at each step.
While the current state value stream map illustrates where you are at present, the future state value stream map shows what the ideal will look like after you implement process improvements.
3. Create Flow
This may be the easiest lean Manufacturing principle of them all; resist the temptation to overcomplicate this.
Creating a good flow should employ as much common sense as possible. Pro tip: Guess who are great advisers about flow? The folks on the shop floor. Although they may be going about their jobs, doing things the way they've always done them, consult them and include them in this process. They have a good grasp on those elements of performing their jobs that are unnecessary.
If you're open to the ideas and suggestions of the people who create the value your customers pay you for, you may find that things are being done the way they've always been done because management inadvertently communicated that message. And if you're not the manager, the message often sounds like, "My way, or the highway."
Creating flow is intended to maximize the efficiency of the product’s manufacturing journey. Given that your product has likely changed since your company first started manufacturing it, and that technology has evolved so much in recent decades, it stands to reason that your current flow could benefit from a closer look. Along with your experienced labor force, this is a lean manufacturing principle that lends itself to unique insights from new sets of eyes.
Where do you start? Why, at the beginning, of course. The benefits of "walking" the process can’t be overstated. What seems to make sense? Where are you doubling up or backtracking? Can you identify areas and procedures where redundancy has been built in over time? Visualize places that seem really well organized, where it’s easy to get from A to Z in a logical, effortless manner. That’s what you’re shooting for.
Approach creating flow in the same logical manner you would any aspect of your life. Look for ways to:
-
Streamline
-
Cut waste
-
Minimize possible damage opportunities
-
Make sure your processes build quality into the product (rather than trying to inspect problems out)
-
Make job performance easier, faster, and more ergonomically sound
A well-thought-out work area results in reduced production time, reduced levels of inventory, and less redundancy in material handling. Good flow allows you to get from A to Z without skipping letters, without circling back, and without having to buy a vowel, Vanna.
4. Establish Pull
Now that you have created a good product flow, you have seen a tremendous reduction in lead time. Because you are able to produce more efficiently.
-
You no longer require the huge buffer of inventory you once did
-
You don’t have to stock nearly as many raw materials and components
-
You’re not racing the clock
-
When you find a problem, your folks are not having to disrupt production to search the mountain of finished goods you had in inventory to isolate potential defects
Before your newly implemented flow, any time drawings were revised to reflect a new requirement, you went into instant panic mode. How would you locate the components and finished goods that were now effectively obsolete? That inventory would never be usable.
Pulling instead of pushing means that the customer lets you know when they’re ready for your product. When you’re not scrambling to catch up because you’re making what the customer wants when they want it, you are no longer paying expedited freight and delivery costs to get components from your suppliers. You no longer keep a fleet of vehicles, complete with drivers, to get the product on a plane so you don’t shut down your customers.
Think of how much more available real estate you’ll have now that you don’t have Olympic stadiums full of inventory. You don’t have to overbuild or underbuild because inventory is no longer the boss.
The manufacturing realm is most definitely the real world. In my experience, I have found that translating these truisms into everyday vernacular and situations people can relate to tremendously reinforces the message.
Want to explain the theory behind Pull when the people you're teaching have had PUSH! shoved down their throats their entire manufacturing life? Try this approach: Have them think of their own families, their own kitchens, and their own budgets. You know every member of your household wants to eat, practically every day it seems. When you go to the grocery store, do you buy ingredients so you can prepare the exact same meal every day? Do you keep preparing food whether it's mealtime and whether anyone is hungry or not? Do you pile it up on the table or in the spare closet, just in case someone is willing to eat it later? Tomorrow maybe? Of course you don't. And if you do, please don't invite me over for dinner.
Put these concepts in words people can relate to and understand. You will quickly see that they can appreciate the philosophy and concepts you're sharing with them. This is a lean manufacturing principle that manifests itself in their real worlds.
5. Seek Perfection
Like the other lean manufacturing principles we’ve reviewed, seeking perfection is not one-and-done.
Perfection isn't attainable, but that doesn’t mean it’s not worth pursuing. Even if you manufacture horseshoes or hand grenades, you’re not satisfied with "pretty close."
To improve your processes, keep looking at all elements from a different perspective. Switch things up. Have folks from different departments look at processes and flow outside the area where they work. Hold a cross-functional Kaizen event with people from all of your departments. Your Kaizen event can even be virtual. Just make sure there's some true interaction so your attendees stay engaged and have something to take away from the experience. These are great segues to further your continuous improvement efforts.
Encourage your associates to speak up with suggestions. You won’t be able to implement every idea, but you never know where your next, “Hey, why don’t we try this?” moment will come from. Learn from others who've been down this path before you. When your teams find something that works really well, share that across your shop and across other facilities within your organization. There's no need to reinvent a perfectly good wheel. That's what Yokoten is all about: Sharing learning laterally across an organization. And not just inside your facility — across your company. You may produce different products than your sister sites. That does not mean sites cannot learn from one another. Any efforts to improve — production, communication, relationships, and performance — will yield benefits.
Try something new yourself! If it doesn’t work exactly like you'd hoped, try something else. As long as new approaches don’t create safety issues or compromise the integrity of the product, take those new ideas out for a spin. New ideas should be recognized and rewarded. That's the opposite of shutting people down before they even get started.
Don’t limit all this great energy and optimism to engineers alone. Every single person can see ways to improve by implementing lean manufacturing principles. If you don't at least see every single person in your organization, let alone interact with them, maybe your journey toward perfection is still a work in progress, too.
Having a system to facilitate the right lean behaviors consistently makes taking these steps much easier, and much quicker to see the benefits. See how L2L's Lean Tools can help your operations improve.
Revisions
Original version: 3 February 2020
Written by: Cara Winther
Reviewed by: Daan Assen
Please read our editorial process for more information
Related Posts
Subscribe to Our Blog
We won't spam you, we promise. Only informative stuff about manufacturing, that's all.