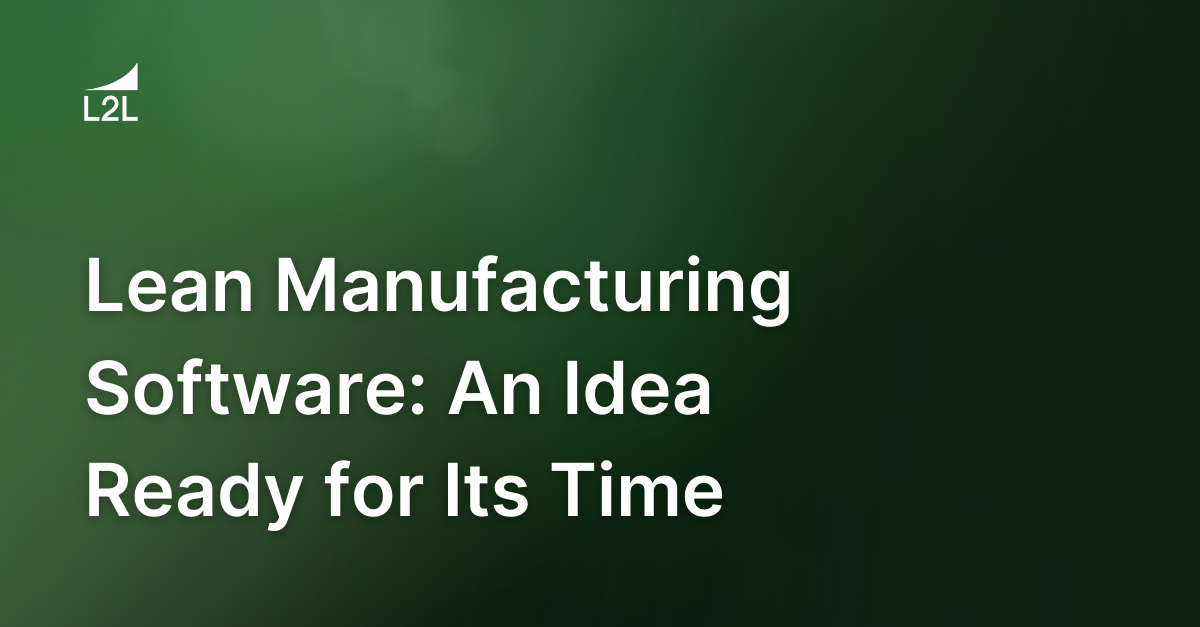
The year is circa 1984.
Four people are walking a plant floor in North America. One of those individuals is the legendary Lean Sensei, Shigeo Shingo; the second is a gentleman named Norman Bodeck; the third is translator Drew Dillon; and the fourth is Mr. Bodeck's assistant, named Maureen Fahey.
In these early years of Lean, Mr. Shingo walks (Gemba as we now call it) and talks with Mr. Bodeck, while a 19-year-old Maureen transcribes what Drew would translates. These writings and talks will become some of the most influential books authored by Mr. Shingo through a newly formed company known as Productivity Inc.
I mention this story to illustrate how long we have been learning and teaching the lean philosophy here in the West. Although I never had the opportunity to meet Mr. Shingo, I did have the opportunity to work side-by-side with the other three individuals in the story.
Once in the capacity as a client, while implementing TPM at Autoliv in the early 1990's, and again when I had the opportunity to work at Productivity as a Lean Consultant in the 2000's (where, just as a side note, Maureen Fahey, the very one who walked and learned some 20 years before, was an owner and my boss). For me, these are memories of exciting times as we watched individuals and American manufacturing embrace Lean Manufacturing principles.
The Evolution of Lean Manufacturing Software
Back then, all of lean was done on paper with handwritten instructions and standard work constructed of laminated Polaroid photos taped to 11"x17" sheets of paper and hung on machines. Operator checklists were compiled during Kaizen events by a team that had the time to write out what was needed.
The issue was – and still is, in some cases – that these handwritten documents were forgotten, or at best very difficult to keep up to date and use in a practical application.
Lean theory and Lean application has come a long way since those days. Now these principles are being taught as requirements in Management courses and trade schools alike. Every organization is thick with knowledge experts who 20 years ago could have made a good living being a Lean consultant. But as always, things needed to change and improve and boy have they.
So why is today different from back then? A few things have had to happen to really move Lean Manufacturing into modern times. One of those things is the advent of Lean Manufacturing Software or as it's also know, a Lean Execution System. These systems have now allowed the same lean principles we have always known to be available at your fingertips.
Lean Manufacturing Software: Where Technology Meets Philosophy
Technology has finally caught up with the needs of Lean Manufacturing. What I mean is that a Lean Manufacturing Software like L2L uses the power of the Cloud and the versatility and convenience of mobile devices all backed up by proper infrastructure to bring about the perfect storm of technology, philosophy and knowledge. This puts into play systems that actually create an easy to implement and manage Lean system.
Features like Kaizen events can be managed in the software that allows for action items, documents, team responsibility, cost savings and metrics to all be integrated into a single feature.
Another prime example of the application of Lean Manufacturing Software is the advent of digital documentation and having those documents launch directly to the Operators on the shop-floor for tasks such as TPM tasks, Quality Checks, and Safety walks; all while being revision-controlled so that only the latest and most current revision is being used, virtually (no pun intended) eliminating audit findings for out-of date documents on the shop-floor.
These are just a couple of examples how a Lean Manufacturing software system can take tried and true Lean Principles that have been used for years and bring them into the present to help drive even more effective improvements in your factory.
Revisions
Original version: 18 July 2024
Written by: Evelyn DuJack
Reviewed by: Daan Assen
Please read our editorial process for more information
Related Posts
Subscribe to Our Blog
We won't spam you, we promise. Only informative stuff about manufacturing, that's all.