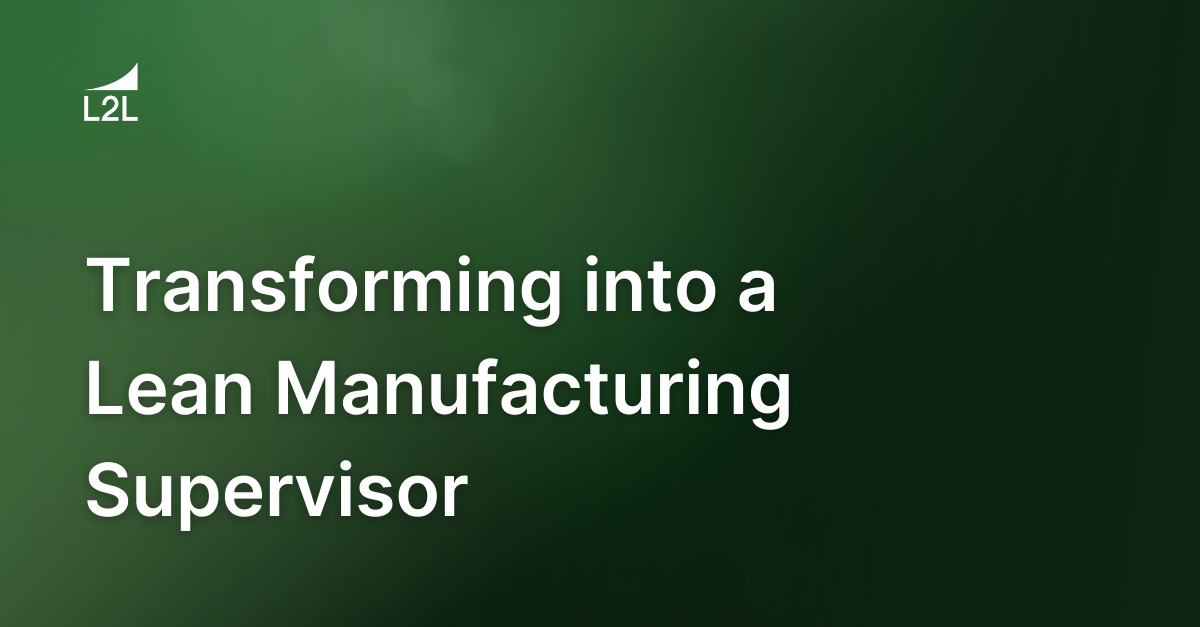
As the manufacturing sector becomes more global and Industry 4.0 kicks into full swing, the role of the traditional operations supervisor is prime for a refresh as well. We are seeing companies streamlining operations in an effort to compete globally, and this has typically led to a reduction in the number of front line supervisor positions. This, in turn, has them leading sometimes significantly more direct reports than even 10 years ago. This shift is forcing supervisors to adopt lean manufacturing software to continue to be effective. In particular, digitizing work activities is having the biggest effect on their ability to be successful in the changing environment.
For anyone who has ever supervised, it can be a bit of a thankless job. When things go well, there aren't usually a lot of kudos given. But when things aren't going well, the supervisor is usually the first one getting grilled. They are the direct link between "Corporate" and the Shop Floor workers. They often have to maintain a delicate balance to ensure company objectives are met, while keeping morale and teamwork from spiraling out of control.
The Successful Lean Manufacturing Supervisor
Let's dig into some of the keys to succeeding in this challenging position. The good news is that there are Lean Manufacturing software solutions that make maintaining this balance easier than ever before. Traditionally, most supervisors used to manage by walking around their areas of the plant, reviewing performance on hour-by-hour boards, and reviewing and auditing safety and quality standards. This isn't especially difficult to do when you have 20 people to supervise, but when you now have 200 people or more, it's nearly impossible.
Lean software solutions allow the supervisors to focus only on the areas that need the most support. For example, L2L's Production Dashboards allow the modern supervisor to be able to see at a glance if they are winning or losing in production and quality from anywhere in the plant, thus being able to direct their support where it's needed most. This is a huge time saver versus making the rounds.
In addition, Leader Standard Work (LSW), has been a staple in Lean Manufacturing for years. Supervisors often had the dreaded clip board with a paper LSW document for the day or week. Now there are digital systems that auto launch LSW based on the day of the week. These digital systems can automatically manage the tasks as well as keep electronic records of your LSW. This allows front line operation supervisors to monitor trends and create follow up actions for deviations. This is a huge step in monitoring adherence to standards and ensuring critical areas of LSW don't slip through the cracks of an antiquated paper process.
L2L's automatic escalation protocols have all but eliminated the dreaded overhead paging system and walkie talkie days of old. Now supervisors are equipped with mobile devices that notify them immediately when there are critical issues that require attention on the shop floor. The integrated workflows ensure there is a process to follow from point of discovery all the way through to resolution. Not only does this allow the supervisor to have more bandwidth in covering more square footage in the plant, it ensures he or she is equipped with all of the necessary information to be in the know when management starts asking questions.
Software for the Lean Manufacturing Supervisor
Lean Manufacturing Software is making it easier than ever for supervisors to teach and coach their shop floor colleagues, engaging them in the use of lean tools such as Kaizen, Yokoten and 5S. Tracking these Lean Manufacturing achievements digitally allows you to broaden your web of lean thinkers in the plant. By doing that, they are able to create a stronger culture of lean in the organization vs the traditional pilot or benchmark area. Not only are they able to engage them in these tools, but they can also monitor their engagement and recognize their successes, further solidifying this lean culture.
Lastly, the supervisor often did very little data analysis and problem solving. Well, to be honest, that was mainly because they really didn't have good, accurate data. The CMMS and ERP systems of old were so difficult to extract actionable, real time data from, analyzing it was next to impossible. Cloud solutions are now making it easier than ever for supervisors to monitor their production processes on one or multiple shifts, and drill into the main issues plaguing their lines. This allows them to be more involved in the reliability process with engineering and maintenance at the daily tier or startup meetings. The free and transparent exchange of information across departments is eliminating the finger pointing between these groups, bringing them together to rally behind improving plant performance.
Process Improvements, or Cutting Jobs?
Lean Manufacturing really got a bad rap in the past several years as companies often used it as the vehicle for slashing heads and cutting jobs. But many companies have seen the light, and have really embraced the core values of eliminating waste and focusing on process improvements. The great news is that there are software solutions that have made it even easier to take your supervision to the next level.
For more information on Lean Manufacturing software solutions, contact Leading2Lean (L2L) to learn more and schedule a free demo. You will be glad you did.
Revisions
Original version: 18 July 2024
Written by: Evelyn DuJack
Reviewed by: Daan Assen
Please read our editorial process for more information
Related Posts
Subscribe to Our Blog
We won't spam you, we promise. Only informative stuff about manufacturing, that's all.