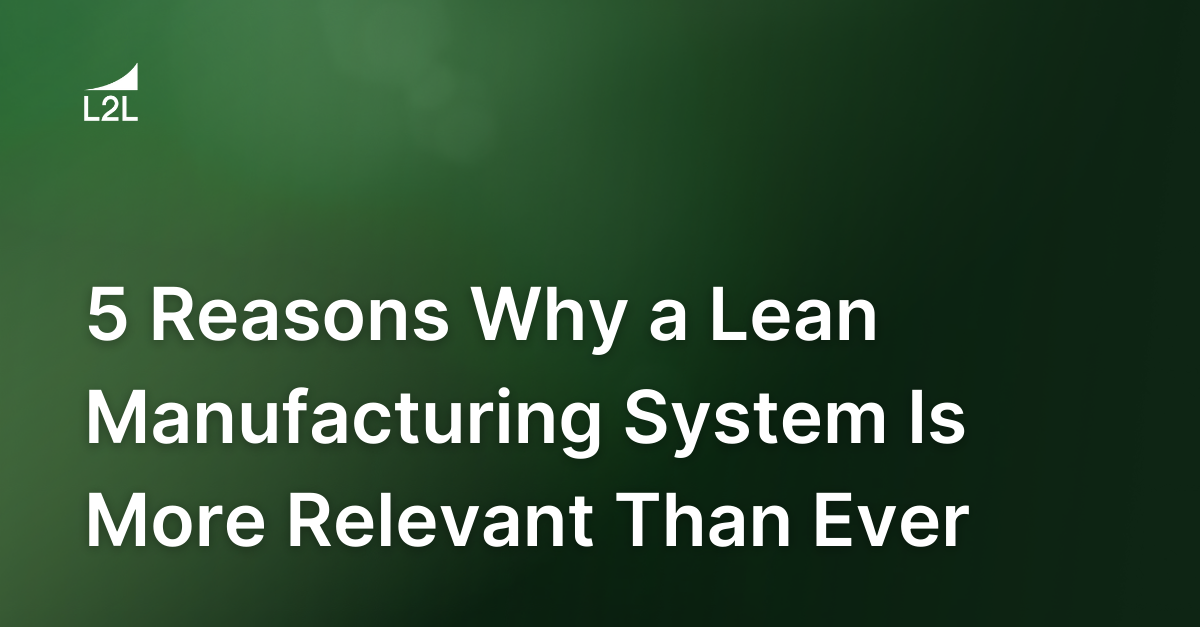
There’s a reason many of the world’s greatest manufacturers practice lean.
Simply put, lean manufacturing creates value for customers by maximizing productivity while minimizing wasted effort and expense. It has its roots in manufacturing, and was popularized by Toyota, but because the principles behind a lean manufacturing system are so versatile they can be applied to almost any operation.
In fact, lean thinking has been applied to industries as diverse as hospitality and healthcare to government. And no wonder—operations that adhere to lean principles enjoy all kinds of benefits.
However, I often hear statements like “lean doesn’t work here,” “we tried it and it didn’t work,” or “Lean is about getting rid of people.” These people have seen management philosophies come and go and see Lean as just another management “flavor of the day” of 10+ years ago.
With today’s global market and the competition that companies face, lean manufacturing is actually more relevant today than it has ever been. It goes hand-in-hand with the current evolution of Industry 4.0 (i.e., IoT, AI, and other smart technologies).
Here are five ways that lean manufacturing is more relevant today than ever.
1) A Lean Manufacturing System Is Not About Getting Rid of People (and never was)
A lean manufacturing system is about getting rid of waste. Waste typically shows up in the form of overproduction, inefficient processes, etc.
However, one of the biggest wastes that I’ve seen in manufacturing is wasted human potential.
The greatest asset we have in our plants is the minds of our people, so when we marginalize that asset, this represents significant waste.
For example, I see workers doing mind-numbing jobs that may be better suited for automation. These people are not using their minds, they’re just wearing out their bodies. These people could be doing more value added work that utilizes their brain power and creativity. What if we repurposed their time and energy to focus on problem solving?
The goal of any company is to make a profit. In order to continue to make a profit in today’s competitive marketplace, you have to become more efficient. I’ve seen companies move plants to low labor cost countries, and those jobs were lost to that community.
There’s always going to be a lower labor cost region somewhere in the world. That’s a losing strategy in the long run. The companies that win long-term are the ones that do it through increased efficiency, regardless of their location.
In the end, the goal is to truly understand the value of our people and utilize their potential. That’s the winning strategy.
Joe Kennedy of the Information Technology and Innovation Foundation said it well: “If the history of automation teaches us anything, it is that while automation can temporarily displace some workers, it also raises living standards for society by reducing costs, improving quality and allowing people to concentrate on higher-value work."
2) A Lean Manufacturing System is a Journey, Not a Destination
I see many companies approach lean manufacturing as more of a program or project than a culture or way of life. The problem with that is that it sets an expectation that there’s a completion to the “lean project.”
The reality is that a lean manufacturing system should provide the guiding principles that are used to run the business.
When I hear companies say something like “we’ve still got a long way to go,” I know they have the right mentality.
When I hear them say, “we’re world-class,” what I’m really hearing is that they’re done improving.
When I visit those factories, it becomes apparent that they’ve stopped driving improvement, and they’re typically in worse shape than those that feel like they’ve still got a long way to go.
In summary, lean manufacturing is really a journey that never ends, and that’s where the satisfaction is found. Coming to work every day knowing that you’ll make a difference is much more fulfilling than knowing that nothing is going to improve.
3) A Lean Manufacturing System Eliminates Waste On All Fronts
Waste elimination in lean methodology includes several types of waste:
- Overproduction: Producing ahead of what’s actually needed by the next process or customer. This is the worst form of waste because it contributes to the other six.
- Waiting: Operators standing idle as machines cycle, equipment fails, needed parts fail to arrive, etc.
- Conveyance: Moving parts and products unnecessarily, such as from a processing step to a warehouse to a subsequent processing step when the second step instead could be located immediately adjacent to the first step.
- Processing: Performing unnecessary or incorrect processing, typically from poor tool or product design.
- Inventory: Having more than the minimum stocks necessary for a precisely controlled pull system.
- Motion: Operators making movements that are straining or unnecessary, such as looking for parts, tools, documents, etc.
- Correction: Inspection, rework, and scrap.
A culture of problem solving to eliminate waste is no mistake. It comes from lean manufacturing system's commitment to kaizen, or continuous improvement.
Effective waste elimination comes from engaging the minds of everyone on the plant floor, especially those that interact with the problem every day. Often, those people already know the solution to the problem.
Continuous improvement calls for a mindset that is committed to problem-solving. Even if a manager knows a way out, the point is to allow employees or learners to develop the habits required for working through issues.
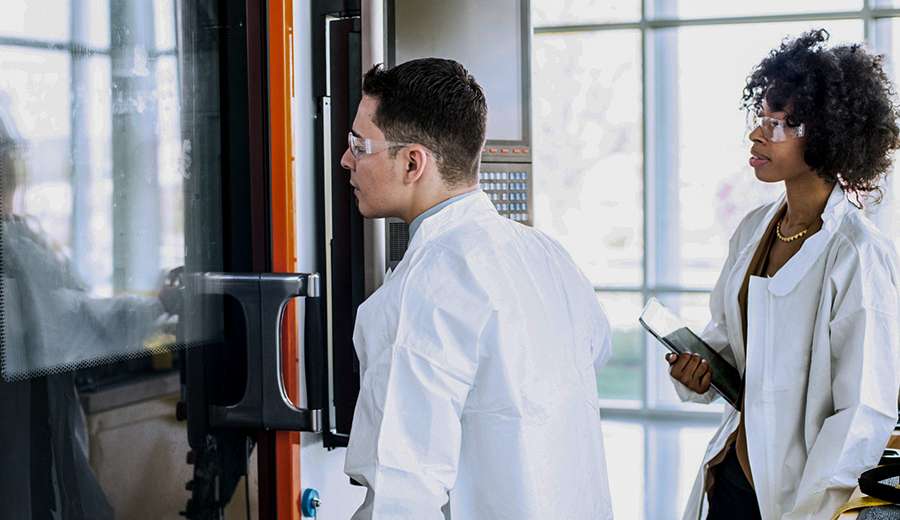
4) Quality and Safety Control Is Built Right In
Lean manufacturing principles need support. And quality control is that support.
Workers can catch issues as they occur, including:
- Downtime,
- Defects in equipment
- Accidents in production and operations
That’s what lean manufacturing encourages. This mistake-proofing approach to production means that quality control is built into the process while the process is ongoing, rather than relegating it to a stage of checks that occur after the fact.
Because we’re engaging people, we’re not just mistake proofing, we’re creating a culture where people are seen as an asset, and we rely on them to recognize problems and to stop and fix those problems.
Today cars have sensors and safety features that can help a driver be safe, but relying solely on those causes a driver to rely less on their own senses. In that situation, it’s too easy for the driver to go into autopilot mode. There are dangers on the road that our senses are much better at detecting than technology.
In a manufacturing environment, there are also things that people are able to sense much more effectively than technology. If your workers are on auto-pilot, then they’re not using their senses, and this is extremely dangerous and costly.
The fact that a lean manufacturing system fosters and relies on employee engagement means you’re in a much better position to have a safer environment and a higher quality product.
5) Standardization brings competitiveness
One of the key principles of a lean manufacturing system is standardization. Standardization of both process and product.
By standardizing processes, then we can actually improve them. If a process is performed in a different way by every person in the factory, then you have no best practice to improve upon. You need to establish a standard best practice in order to improve. You have to have a standard in place or improvement becomes haphazard at best.
For example, standard work for operators ensures that the work is done the most efficient way that we know today. If we find a more efficient way, then we just change the standard baseline and train people on this new and better way.
Some people see standardization as a way to stifle creativity, but it actually has the opposite effect: It opens the way for creativity.
Usually the default for people is to use the easiest way to accomplish an objective, but, what we need is the right way used consistently. This requires brain power and innovation to find the best method and establish it as the standard, which as we stated before, provides the baseline to improve upon.
Standardization of your products can also be a way to reduce costs and improve quality.
For example, to compete with Toyota, Volkswagen introduced something called an MQB or “Modular Transversal toolkit.” It was a methodology that allowed front-wheel-drive cars that shared the same components to be put together in different modular configurations.
By bringing standardization as a focus, and applying creativity and methodical discipline, Volkswagen was able to win on several fronts: MQB managed to increase efficiency, cut costs, and reduce the build time by 30%.
Conclusion
A Lean Manufacturing System Brings Financial Gain
Lean’s focus on waste elimination encourages companies to employ techniques like just-in-time production and built-in quality control. This creates a positive cycle of cost savings that never ends.
- Standardization provides the baseline for improvement
- Engaging human minds creates solutions to problems
- Continuous improvement leads to continual cost savings
Lean’s success necessitates a mindset shift that must be accompanied by the right tools, the right training, an improvement focused workplace culture, and a commitment from top management.
But then, so do most winning strategies. It’s why lean manufacturing will continue to win as companies transform—and why the process could save you millions.
If you’re ready to revolutionize your plant floor, request a demo with L2L. Our lean manufacturing system has lean manufacturing principles built in, so you can enjoy all the benefits of lean manufacturing with less of the hassle. It hardwires lean into your factory floor.
Revisions
Original version: 2 August 2019
Written by: L2L
Reviewed by: Daan Assen
Please read our editorial process for more information
Related Posts
Subscribe to Our Blog
We won't spam you, we promise. Only informative stuff about manufacturing, that's all.