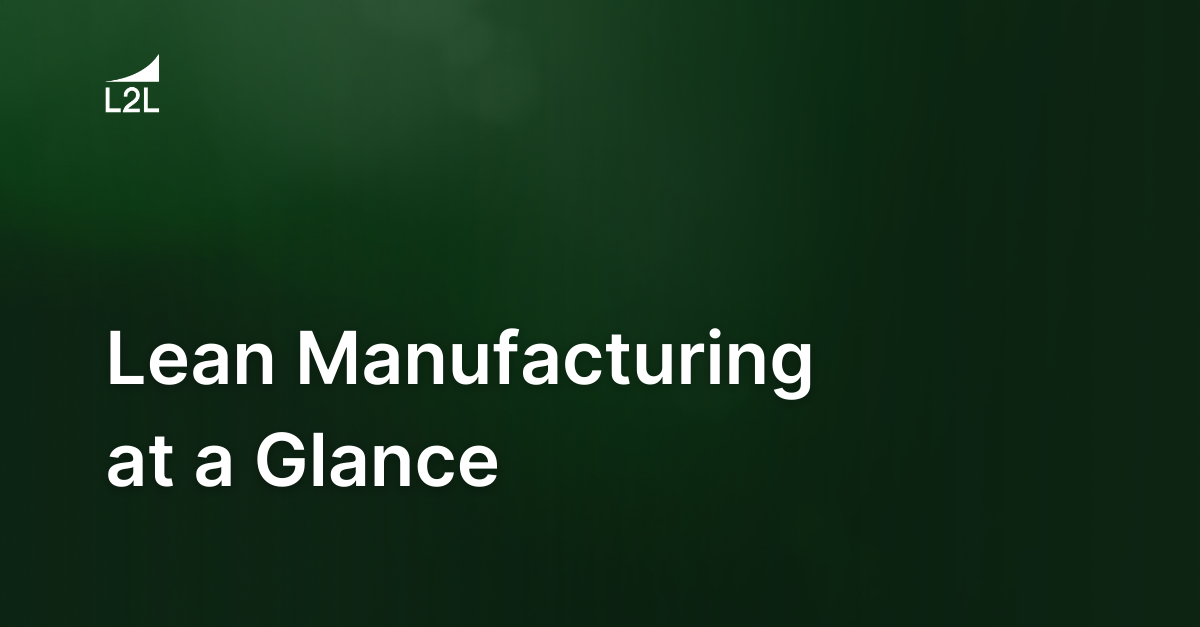
With development of the Toyota Production System (TPS) by Taiichi Ohno and Eiji Toyoda between 1948 and 1975, Toyota positioned itself as a top competitor in the automotive industry; a position it retains to this day. The company’s enduring success stems from their ongoing commitment to and investment in creating innovative products, improving production efficiency, reducing work content and equipment cost in operations, developing skills, and responding to customer needs. Essentially, the firm has mastered creating customer value by maximizing productivity while minimizing waste.
This principle lies at the heart of lean manufacturing, a philosophy used by many of the world’s top manufacturers. While seemingly straightforward, achieving the same success through this process as a Toyota requires discipline and a commitment to fundamentally rethinking how businesses operate. Let’s talk through why.
What is Lean Manufacturing?
Like the agile method for software development, Lean Manufacturing is both a system and a school of thought. Its end goal is to develop a perfect value creation process with zero waste. This probably seems like a pretty aspirational target because it is – accomplishing a zero-waste operation is virtually impossible.
Yet when a company pursues perfection as its ultimate objective, it assures that all other efforts they undertake are oriented and working progressively toward that mission. In case of the lean manufacturing, this means a business is continually incrementally improving customer value: processes are streamlined, wasted is eliminated, and output quality is raised.
Improving process efficiency liberates all plant personnel – from C-suite executives to frontline operators – from the burden of unnecessary, wasteful activities. Instead of fretting over excessive machine downtime or meeting production quotas, employees can now focus on optimizing the processes that help them deliver a better, more brilliant product to the customer. The cycle of improvement perpetuates as employees apply lean manufacturing principles to further relieve overburdened equipment and workloads, improving efficacy and growing profits.
7 Key Lean Manufacturing Principles
Lean manufacturing is based on a set of repeatable principles that are flexible enough to be applied by any manufacturer and produce solutions unique to its operations. There are seven of these tenets:
- Elimination of waste: Most lean schools of thought define waste as anything which does not provide value to the customer. (Toyota’s Seven Wastes: defects, over-production, transportation, inventory, motion, waiting, and over-processing.)
- Continuous Improvement (Kaizen): This is a lean approach to implementing change through executing small, continual positive changes to achieve significant improvements.
- Leverage human capital: Apply the skills and talents of employees to drive the company’s continuous improvement engine by empowering them to propose and execute kaizen.
- Level out production (Heijunka): In Lean Manufacturing, the goal of heijunka is to create goods at a constant rate so production is predictable, thereby allowing waste to be reduced.
- Single-piece flow: Single- or one-piece flow is the lean tenet of building products at the rate of customer demand; this eliminates the waste of excess inventory and articles waiting to be worked on.
- Just-In-Time Production (JIT): The JIT production model where deliverables are produced to reduce production times in the system, response times from suppliers, and delivery times to customers.
- Built-In Quality (Jidoka): Jidoka is the lean practice of controlling variables within a process, evaluating each article’s quality, and ensuring not to pass on poor quality items. This includes the idea of mistake-proofing, or poke-yoke, where mistakes are prevented or are caught early and corrected.
Yet to effectively implement these principles and achieve operational efficiency, it’s not only a matter of what toolkits, processes, or even software a business chooses to implement. A company must capture the most powerful resource available inside the plant: the human brain. Employees need to understand not only how lean manufacturing will benefit the business, but also how it will benefit them and their roles. Knowing how they will be involved and will win is critical to engaging their hearts and minds in instituting change. Only then, lean becomes a way of life.
The Five Steps of The Lean Manufacturing Cycle
The lean principles guide the decisions of companies, so it is valuable to consider how they relate to lean manufacturing cycle. This helps keep the goal of these principles in sight: recall, lean manufacturing is a never-ending process to increase value.
The lean manufacturing cycle is the means to visualize that iterative process:
- Identify Value: define what the end value to the customer is; what is the customer willing to pay for
- Ex) product turnaround time, price point, materials of construction
- Map the Value Stream: assess the process to identify those steps which do not create value according to the first step in the cycle
- Ex) Value-added: ordering materials, assembly, shipping
- Ex) Non-value-added step: inspecting, filing, staging
- Create Flow: Build a tight sequence of steps that bring the highest amount of value to a customer, as quickly as possible
- Ex) redesign production process to remove staging, inspecting, and filing (non-value-added) steps from flow
- Establish Pull: A system that has the purpose of creating a workflow where work is pulled only if there is a demand for it
- Ex) ensure process triggers established such that raw materials, sub-assemblies, and/or finished goods are brought to the next process only when that process can immediately process them
- Seek Perfection: strive for an ideal system by continuously iterating the cycle of eliminating waste, smoothing out processes, etc.
- Ex) return to the start of the process to perpetually define customer value - price, identify value and non-value-added steps – assembly and moving, creating flow – remove unnecessary movement, and establishing pull – subassemblies created and delivered to final assembly individually on as-needed basis
Tangible Benefits From Lean Manufacturing
When organizations implement lean manufacturing principles, they achieve these tangible benefits:
- Lower costs by eliminating non-value-added steps and diminish need to rely on overseas labor for savings:
- Ex) Implement electronic documentation to eliminate unnecessary copying and filing steps
- Reduce expense by preventing a defect versus applying labor to inspect for and rework it:
- Ex) Eliminate the expense of process and product inspection by building defect prevention into the manufacturing process
- Reducing the time needed to complete activities:
- Ex) Modify the paint application process for a product from rollers to automated sprayers to accommodate more
- Minimize inventory while maintaining consistent output that meets customer demand:
- Ex) Establish single-piece flow so materials flow from the warehouse through production and into packaging and shipping as they are demanded by the following process and customers
- Build a motivated workforce by using lean to promote creativity and innovation:
- Ex) Leverage production operators’ expertise to process points at which to install sensors to build quality into the manufacturing flow
Conclusion
Toyota’s Production System is still discussed in reverent tones because it was the first and most prominent example of success lean manufacturing implementation. Yet this accomplishment paved the way for many subsequent companies, such as Autoliv, to also achieve these efficiencies: leaned out operations with increased bottom lines, products with qualities that customers truly need, and an instilled lean culture.
The pursuit of excellence might seem intimidating at first, but lean allows you to start where you are and improve from there because lean is not a destination, but an ongoing journey. If you are ready to transform your plant floor, request a demo with L2L. Our complete manufacturing software solution has lean principles built so you can implement these principles and immediately enjoy its benefits.
Revisions
Original version: 29 July 2019
Written by: Bob Argyle
Reviewed by: Daan Assen
Please read our editorial process for more information
Related Posts
Subscribe to Our Blog
We won't spam you, we promise. Only informative stuff about manufacturing, that's all.