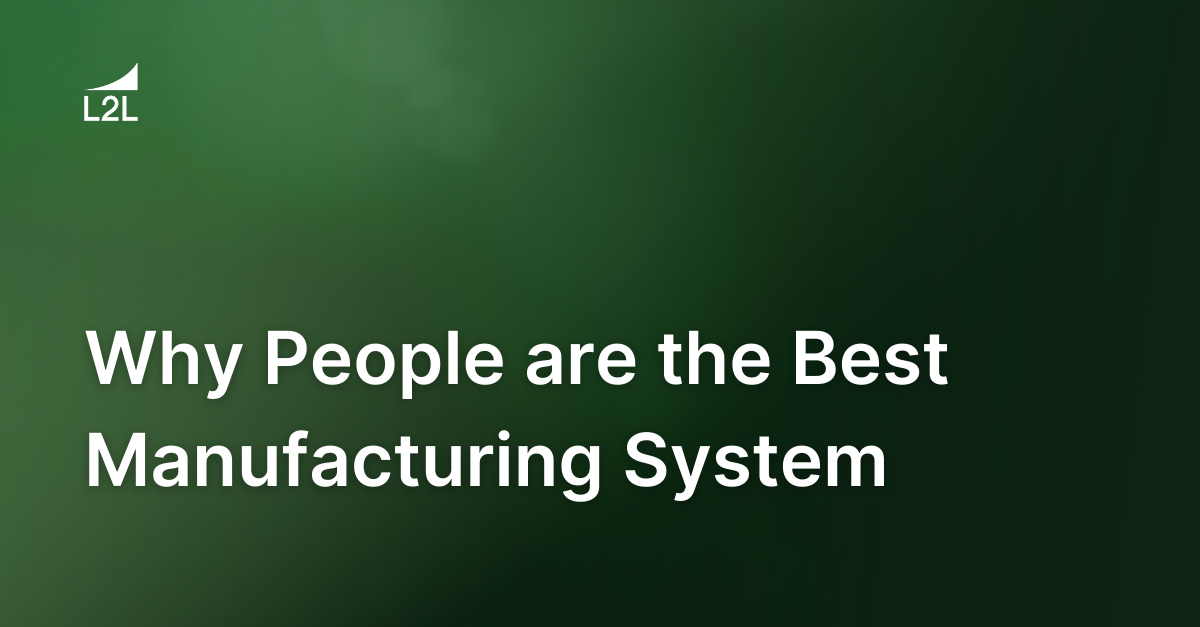
In this blog post we'll explore:
- Why sensors aren't the answer
- A case study example of the importance of human problem-solving on the plant floor
- How you can revolutionize your plant floor and achieve your best KPIs to date
The problem with sensors is that if we become reliant on them, we stop using our own senses. For example, I have a car with smart sensors on them: lane sensing, driver assist, rear-view camera, etc. I love these features, but what I've learned is that there's risk in it because as I start to rely on it too much, I stopped using my senses. I was driving my truck the other day, and it was a bad rainstorm and lane sensing on my vehicle completely was useless. But I could still see the lines on the road. My vehicle could not, though.
And I can't overemphasize the importance of using our senses. Our senses are there to keep us out of trouble. When we start relying on technology too much, we stop using our senses. That's when bad things can happen—because technology fails.
Now think of this in the context of a manufacturing system. When people feel that vision systems and sensors are ensuring that operations are executed correctly, the believe a bad product can’t be produced; we don't need operators to use their senses and identify issues.
That's very scary. That's very risky.
I'm not saying the technology isn’t great. The technology is there to serve a very important purpose, and sometimes the technology can do things that we humans cannot do.
However, when the operator sees or notices something that's not right, we want them to bring that issue to the surface. If they're totally turned off, the chances of issues like that being caught and addressed decrease dramatically.
And that's when bad product gets out the door. That can cause major quality issues.
Your Manufacturing System Needs People
Let me give you an example.
At one of our customer facilities, the operator sees a component on the floor. Interestingly enough, this component is not assembled in this facility. This component goes into a sub-assembly that comes from one of their suppliers and it somehow got out of the sub-assembly and fell to the floor.
Red Flag, red flag, red flag.
The operator knew there was a problem. Using L2L’s software, they created a Dispatch. They came out, looked at the quarantined product and actually found the part that was missing the component. It was in a finished box, ready to go out to a customer.
If that operator hadn’t been using his sense and they didn’t catch that, there could have been a major issue. A manufacturing system could not have done what the operator did.
Furthermore, they were able to dig into the root cause of the problem. They were able to address the issue and work with the vendor to address what could have happened along the way. What was the systemic issue at play?
Great news: They found the problem. The problem was in the design, and they were able to correct it so that it would never happen again.
They were able actually able to make a change to some tooling at the vendor site, which turned out to be the root cause of the problem.
The moral of the story is somebody knew their job was important. All the technology in the world wouldn’t have solved that problem, and it was left to people to identify an issue and notify the team.
Nobody’s talking about this. Everybody is talking about all the cool technology out there. The sensors. The AI. And I'm not saying it's bad, I'm just saying it's not the answer. In the meantime, companies are ignoring their most valuable asset: the minds of the operators out on the floor.
How L2L Can Help Your Manufacturing System
So, let's talk about how these issues get addressed in a manufacturing system. I gave you a few examples, but there are hundreds of different processes that are being managed in our system to address very specific issues on production floors. Before L2L, a slew of ineffective solutions were used including:
- Radio communications
- Passing the problem off to a supervisor
- Telling someone to put in a maintenance order and hoping it gets addressed
- Excel spreadsheets
- Tick sheets
- White boards
- Pen and paper
The list goes on and on and on. And you see it in every factory in the world, because there are hundreds of different processes and abnormalities that need to be managed out on that production floor—and nobody is addressing them.
That's what makes L2L different. That's what makes it so powerful. We're addressing everything.
We have a system that doesn't look at production efficiency just from a machine and downtime standpoint. We look at all the efficiency.
And I would say that machine downtime isn't even close to half of the problems. In my experience, it was maybe 20%.
But companies focus on that 20% and throw all their money at it.
It doesn't make any sense.
Ready for a better way? Schedule a demo with us today and discover how L2L’s proprietary software can revolutionize your operations.
Revisions
Original version: 5 November 2019
Written by: Bob Argyle
Reviewed by: Daan Assen
Please read our editorial process for more information
Related Posts
Subscribe to Our Blog
We won't spam you, we promise. Only informative stuff about manufacturing, that's all.