Hit your daily production goals with fewer delays.
When every shift counts, L2L helps you stay on track. Identify bottlenecks, adjust in real time, and keep output flowing. Your team consistently hits production targets without last-minute fire drills.
Solving problems with better data and better standards
L2L improves your manufacturing processes by giving your frontline teams the right information, tools, and suggestions in the moment of need.
-
Unplanned downtime
-
No connection to other systems
-
No collaboration
-
Unclear root causes
-
Lack of standardization
Not all downtime is caused by equipment failure. The best maintenance is preventive. Track maintenance by cycle and time to see when machines are due for maintenance and document minor stops by type and time. Operators can raise issues when stoppages occur, so the right colleague can take the right action at the right time.
Most factories have several systems in place, like MES, ERP, and SCADA. However, these tools are usually disconnected from each other, resulting in siloed data and tasks piling up without a clear view of what needs to be done. L2L connects your systems and orchestrates the entire shop floor, so teams can spot and solve issues—fast.
Teams need to be aligned on which tasks need to be done and when. But this can't happen without automatic alerts and digitized work instructions. Seamless collaboration between teams is facilitated by shared tasks, goals, and digitized workflows, ensuring efficient task execution.
Frequent stops, inefficient changeovers, and scheduling conflicts are usually caused by a lack of root cause identification and ineffective preventive maintenance. However, tackling root causes and implementing preventive maintenance optimizes production flow, reduces downtime, and streamlines changeovers.
Without standards, continuous improvement is impossible. Profitability naturally takes a hit if you consistently miss production targets because of delays. Standardized processes and a culture of continuous improvement foster efficiency, minimize errors, and drive consistent achievement of production targets, leading to increased profitability.
-
Unplanned downtime
Not all downtime is caused by equipment failure. The best maintenance is preventive. Track maintenance by cycle and time to see when machines are due for maintenance and document minor stops by type and time. Operators can raise issues when stoppages occur, so the right colleague can take the right action at the right time.
-
No connection to other systems
Most factories have several systems in place, like MES, ERP, and SCADA. However, these tools are usually disconnected from each other, resulting in siloed data and tasks piling up without a clear view of what needs to be done. L2L connects your systems and orchestrates the entire shop floor, so teams can spot and solve issues—fast.
-
No collaboration
Teams need to be aligned on which tasks need to be done and when. But this can't happen without automatic alerts and digitized work instructions. Seamless collaboration between teams is facilitated by shared tasks, goals, and digitized workflows, ensuring efficient task execution.
-
Unclear root causes
Frequent stops, inefficient changeovers, and scheduling conflicts are usually caused by a lack of root cause identification and ineffective preventive maintenance. However, tackling root causes and implementing preventive maintenance optimizes production flow, reduces downtime, and streamlines changeovers.
-
Lack of standardization
Without standards, continuous improvement is impossible. Profitability naturally takes a hit if you consistently miss production targets because of delays. Standardized processes and a culture of continuous improvement foster efficiency, minimize errors, and drive consistent achievement of production targets, leading to increased profitability.
Made for production execution
Knowledge for operators. OEE tracking, product orders, and scheduling for managers. Continuous improvement at scale for leaders. Identify improvements fast and connect people to the tools and knowledge they need.
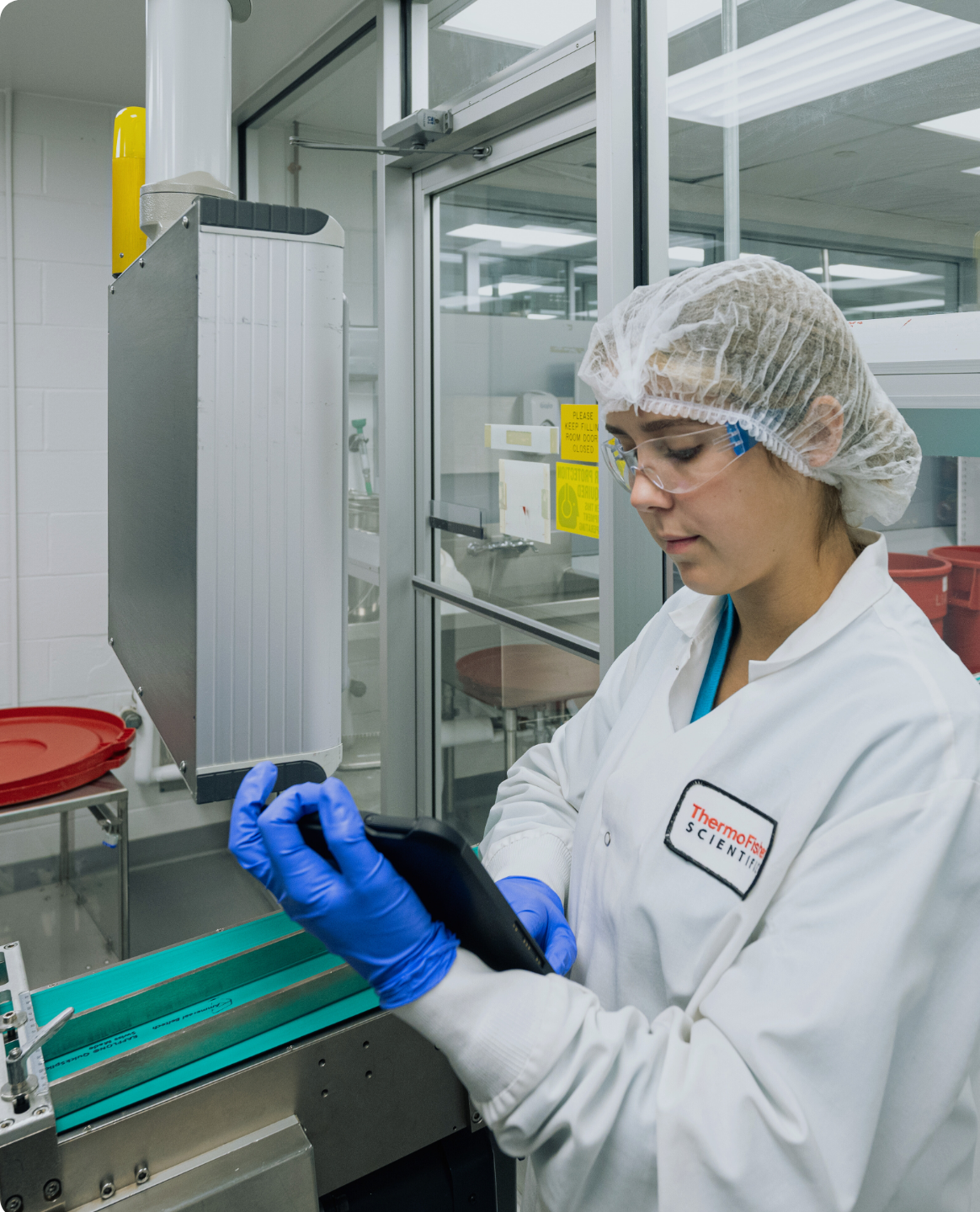
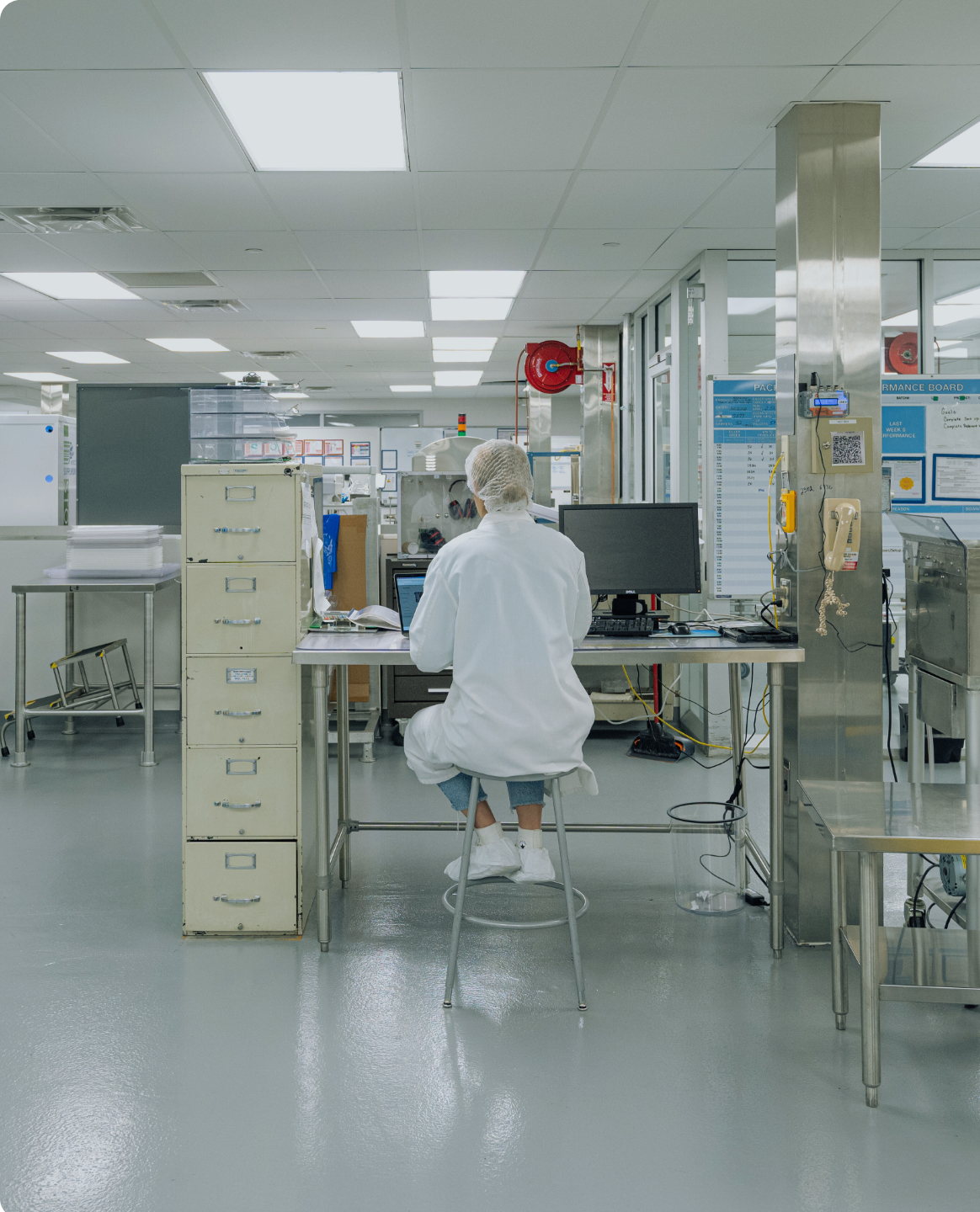
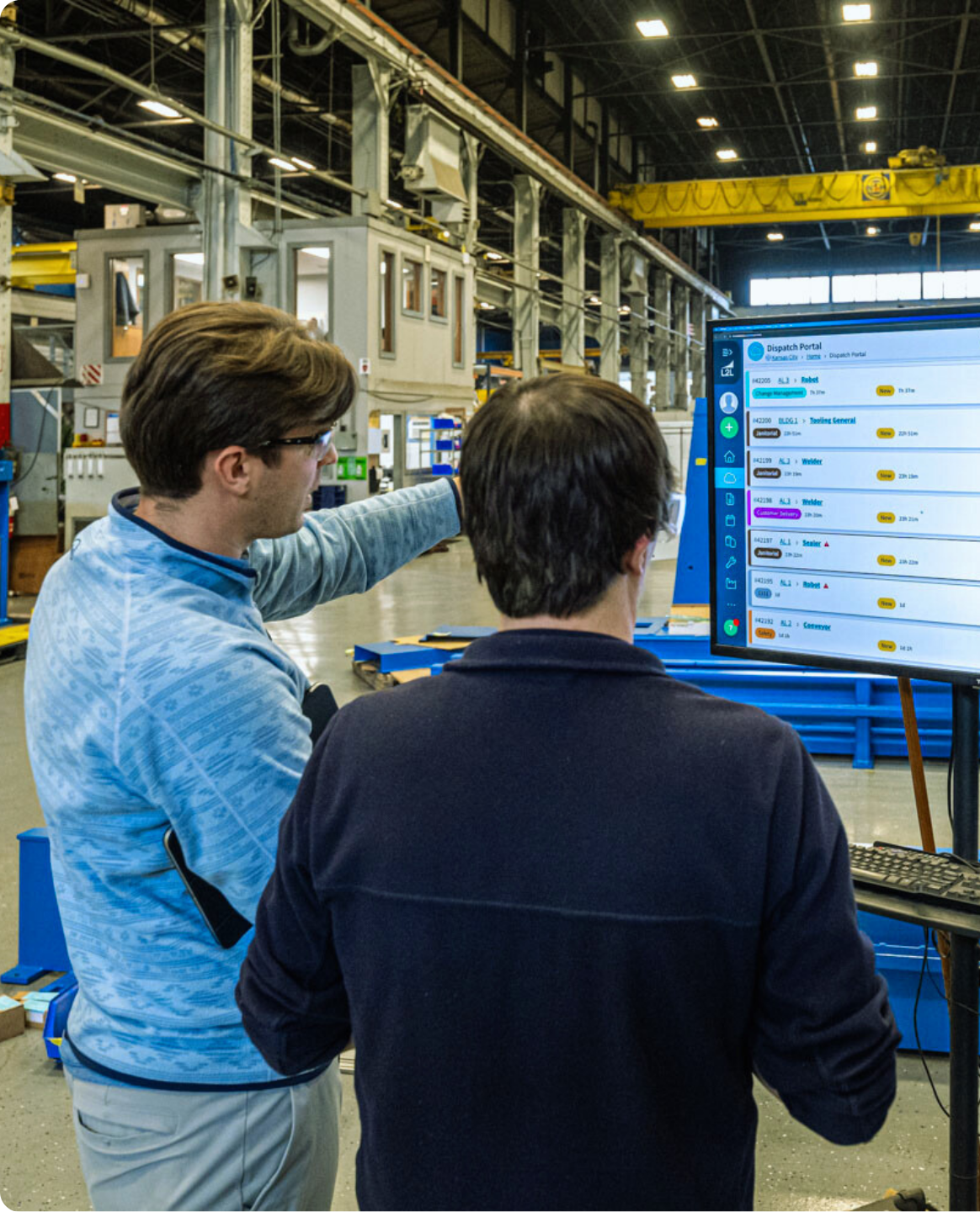
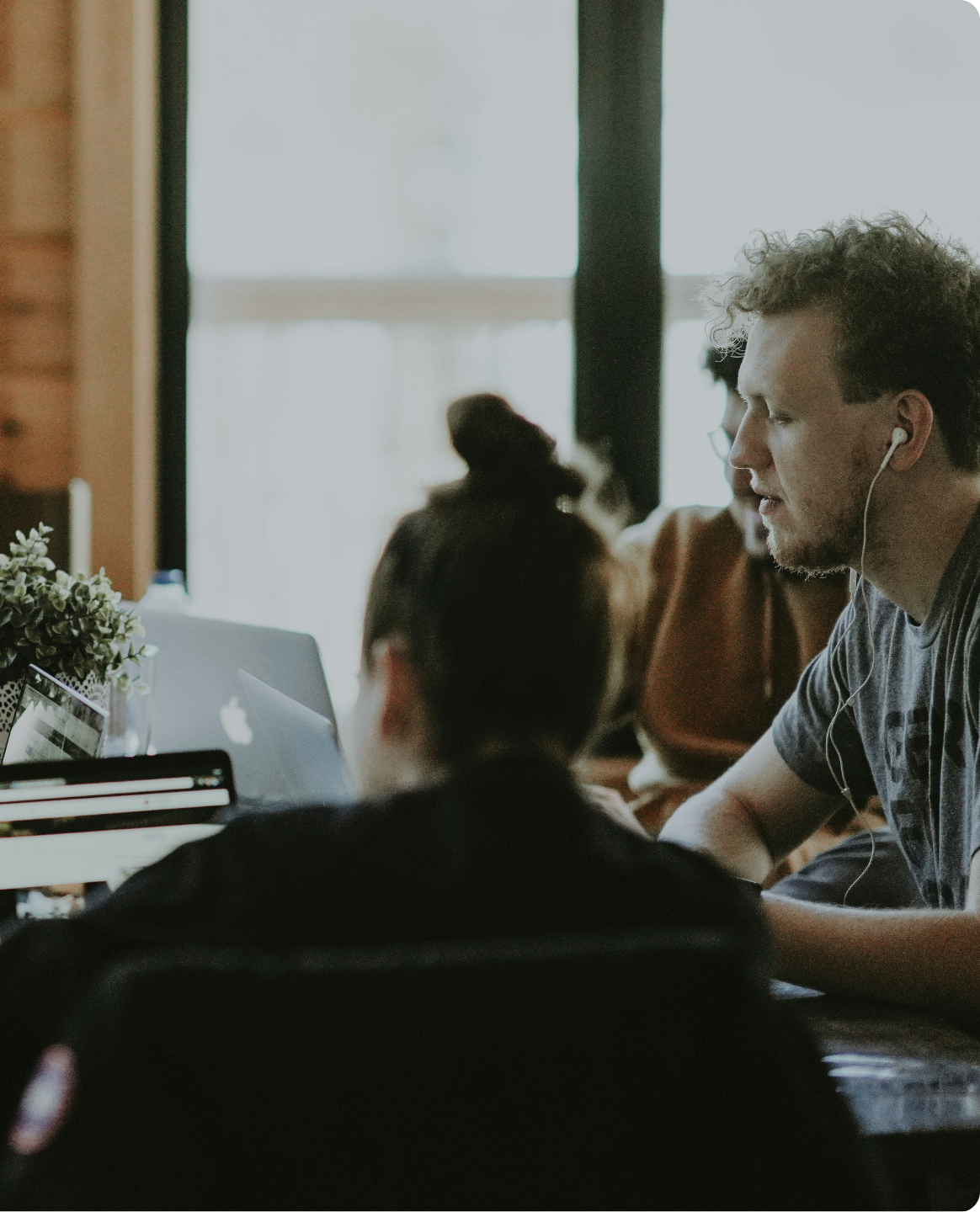
Frontline performance depends on seamless access to the right tools and knowledge. L2L helps teams execute tasks correctly with AI-powered work instructions, checklists, task tracking, and skills management tools.
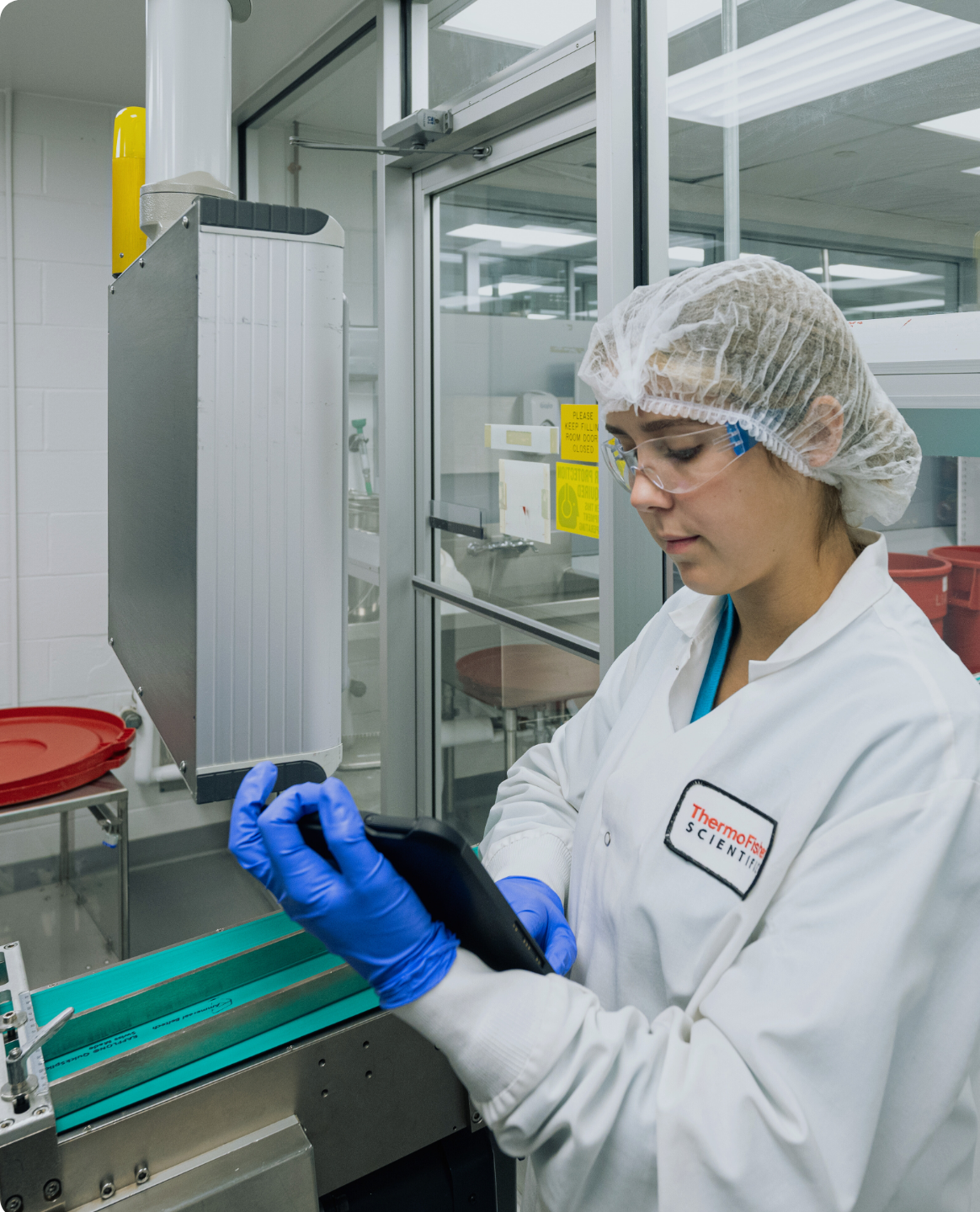
Use L2L Dispatch to identify, track, and solve performance disruptions. Place work orders and schedule actions.
Our production dashboards allow managers and supervisors to connect real-time data with tasks and actions to identify bottlenecks, optimize workflows, reduce downtime, and keep productivity high.
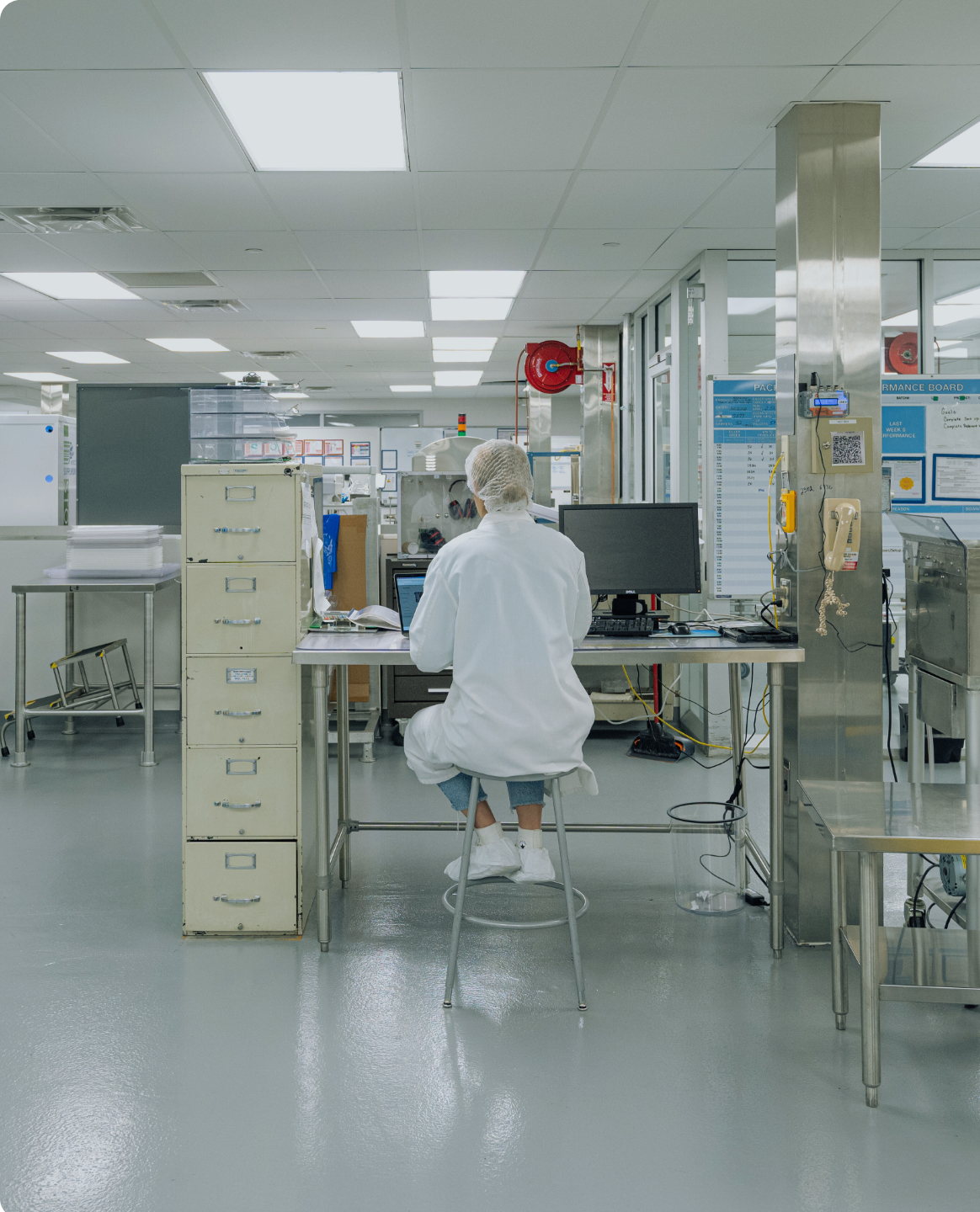
Meet your performance benchmarks and production goals with a complete view of key metrics at scale.
Operational excellence is no longer siloed by location. L2L’s Yokoten module allows you to share and standardize best practices across your operations.
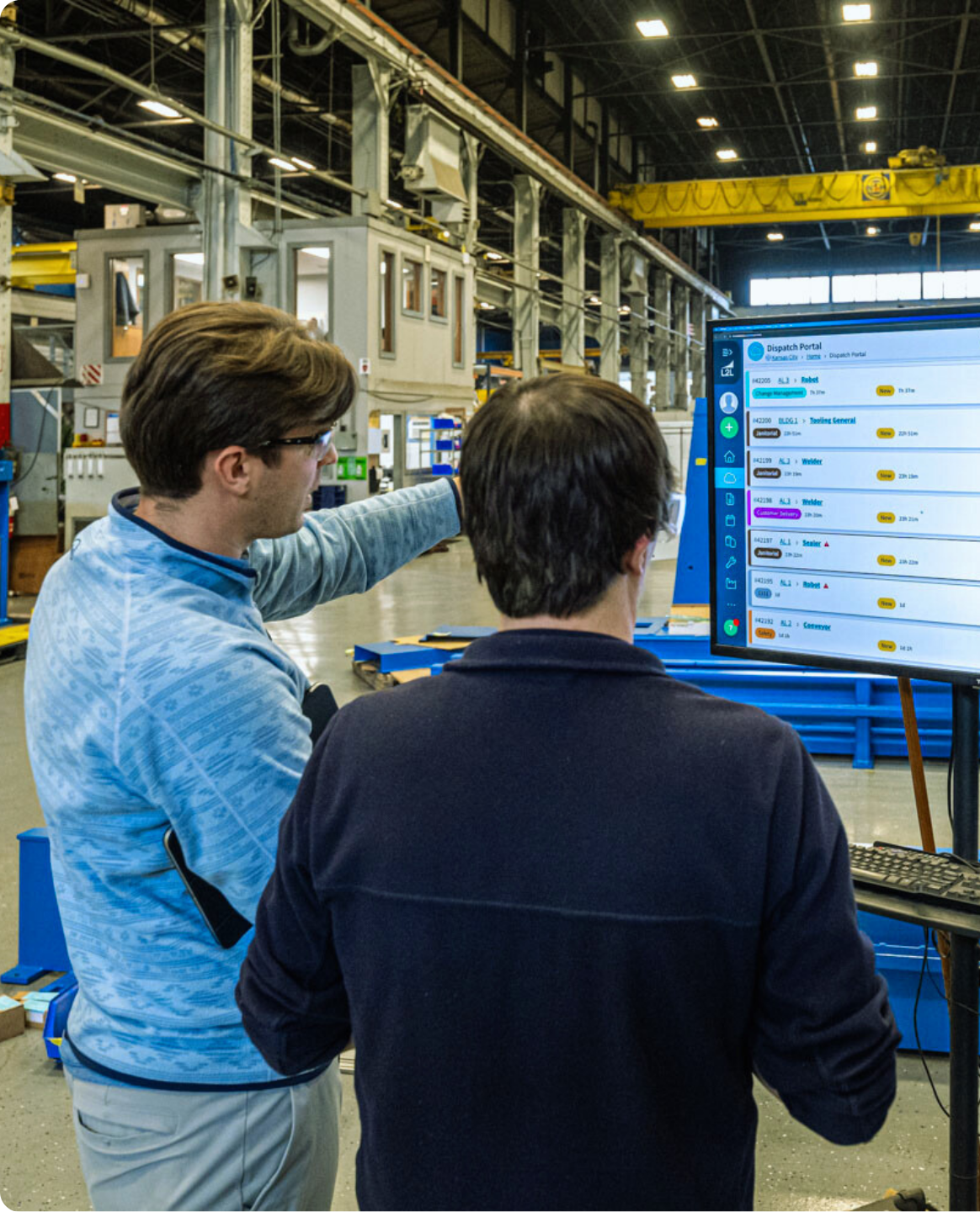
Transform your operations
Drive impact from shop floor to the top floor.
Real-time visibility means real-time action
L2L centralizes and coordinates the tools you need to boost performance and drive continuous improvement at scale.
Overall Equipment Effectiveness (OEE)
L2L’s OEE Dashboard gives teams an accurate and standardized approach to measuring OEE across various lines, departments, and plants.
Product orders
Coordinate product orders using real-time insights into production status. L2L simplifies adding, updating, and retrieving the status of product orders to align your teams and drive performance.
Scheduling
Get your entire frontline on the same page with a unified view of production scheduling. L2L coordinates planned production schedules to improve performance, responsiveness, and the successful resolution of unplanned events.
Key metric monitoring
Make every decision data-driven. L2L tracks and displays the metrics that matter most to production efficiency, including labor minutes per unit, Takt time, run rate, and hourly counts.
Changeover management
Accurate and effective work instructions are essential for performing changeovers. L2L helps teams standardize, distribute, and improve digital job aids across your entire value chain.
Material handling
Remove uncertainty from organizing materials transport and signaling material change. Use real-time data in L2L dashboards to notify material handling and avoid process disruptions (and shortages).

“We were underperforming, understaffed, and it was spreadsheet on top of spreadsheet. Simply keeping track of what was happening was a nightmare, and the team was spending hours gathering data."
Plant General Manager
"What makes L2L so unique is the fact that the product was developed by real manufacturing users. People that truly understand the day-to-day issues and concerns that drive the production floor."
Lean Maintenance Consultant

“Everything our plants could do to improve efficiency, reduce unplanned downtime, drive waste out of the process, and react faster to change is becoming even more critical to keep up with the changing market conditions.”
VP of Operations
Related content
Oetiker Transforms Productivity and Collaboration with L2L TeamBoard
eBook: Maximixing Productivity
Frequently asked questions
Find answers to common questions about how L2L can boost performance, streamline processes, and drive continuous improvement.
How does L2L help improve production performance?
L2L empowers teams with real-time visibility into operations, data-driven insights, and tools to quickly address production disruptions and waste. From tracking OEE to managing production schedules, L2L is designed to maximize throughput and efficiency at every level.
Which performance metrics does L2L track?
L2L monitors key metrics like labor efficiency, OEE, operational availability, performance efficiency, defect rates, and earned hours. Benchmark performance and identify areas for improvement across plants.
Can L2L support continuous improvement initiatives?
Yes, L2L’s Lean Module allows teams to manage CI efforts digitally in the platforms. L2L also provides tools to standardize processes, optimize workflows, and sustain improvements over time. Our real-time data and actionable insights make it easier to identify inefficiencies and implement solutions for lasting performance gains.
Ready to drive performance like never before?
Discover how L2L can transform your production management with real-time insights and actionable solutions.