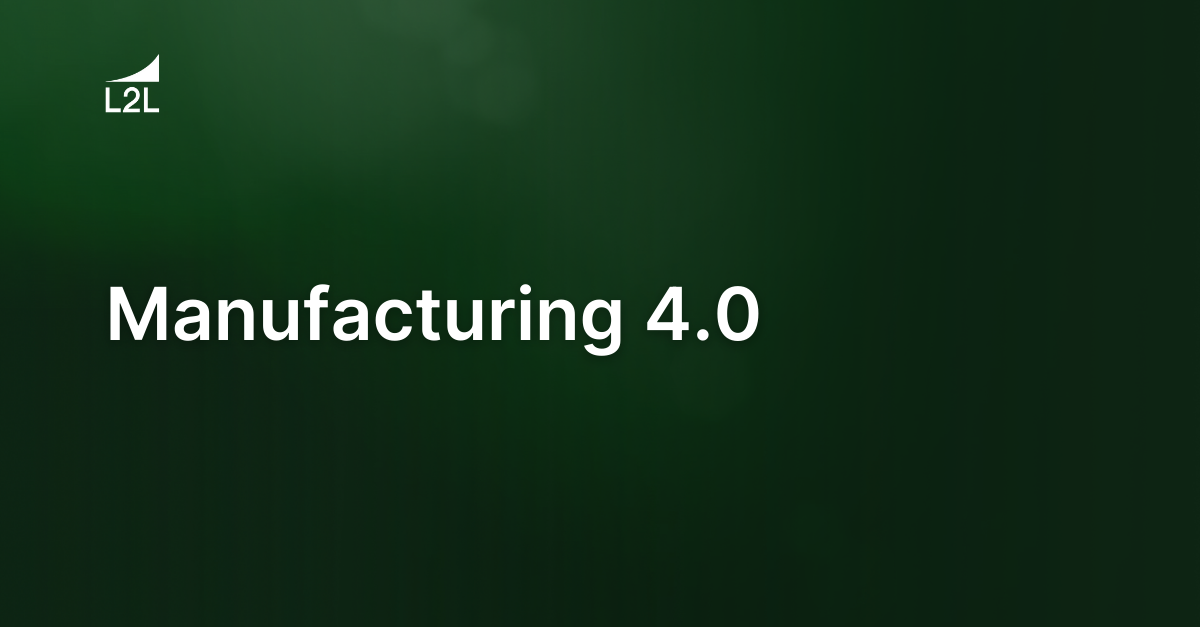
Manufacturing 4.0 is upon us, and is helping many manufacturing sites become very efficient and flexible. And more than ever, manufacturing can no longer afford to suffer extended periods of downtime due to issues that arise. Production Efficiency and Operational Availability must be maintained to stay profitable.
The good news is that with today’s newest technologies and advancements, Manufacturing 4.0 allows us to more readily and easily identify and address many systemic manufacturing pitfalls and complex causes of waste and downtime.
The heart of Manufacturing 4.0 lies in communication. Now there are many more individual concepts, techniques, and tools to utilize in conjunction with Manufacturing 4.0. However, the key to successfully adopting and deploying Manufacturing 4.0 in this era of new technologies is communication.
3 Simple but Proven Benefits of Manufacturing 4.0
Let's look at three simple but proven ways that Manufacturing 4.0 can reshape and drive significant improvements in manufacturing.
- Communication tied to Action
At the heart of manufacturing 4.0 is communication.
This communication can be Machine to Machine or Machine to Operator or vice versa, and can impact communications and connectivity in all facets of manufacturing. The key to unlocking the power of Manufacturing 4.0 is to create and improve in an environment of continuous and constant connectivity and communication. Utilizing modern manufacturing techniques easily allows for seamless Machine to Machine communications. With the introduction of IoT, the options are virtually endless. Machines are now capable of collecting many process attributes and variables with the capabilities to send data to the Cloud.
Having machines and processes connected allows for many advantages to further enhance communication. Such as the ability to self-report problems: provide critical data and insight regarding potential downtime, quality, safety, and efficiency information.
Machine to machine communication brings huge advantages to manufacturing. As powerful as this communication can be, some of the most significant communications and connectivity will always lie in human interactions and communications. Utilizing today's advancements and technologies in a Cloud based LES (Lean Execution System) software solution like Leading2lean can provide a proven platform to bridge the gap and close the loop on many common communication failures and missed data acquisition points opportunities.
A Cloud Based LES platform such as L2L can also provide a solution to compute the deluge of data and analyze the mass quantities and proliferation of that acquired data. Computing this communication and information passed from machine to machine or from human interactions enables all users to extract, analyze, review, and store this critical information.
Communication without driving associated Actions limits the potential overall value. Don't underestimate the additional value derived from touting your victories along the way as well.
- Smart Automation
Automation today is not only simply adding a Robot to a process or adding a vibrating bowl to feed components into a process. Although the implementation of Robotics is a critical element of continuous improvement and waste reduction, these applications are better utilized in situations or environments that are better suited for Robotics vs Human interactions.
Today's Smart Automation utilizes information, communications, and events from both the Robot and Human Interactions. Combined processes of Robotic and Human interactions allows the ability to cohabitate and share information. Automating the information sharing process between machines, humans, robotics, and connected processes can single-handedly be the most effective and significant Smart Automation improvement.
With today’s automation capabilities and Robotics, the ability to acquire the deluge of information is endless. Automated processes have a tremendous capacity to gather and capture critical information. Once you have connected these processes and automated information sharing, how do you analyze, extract, and review these critical communications and information sharing? Utilizing a new era software platform like L2L's LES can accelerate the rate of growth and success as a solution to Analyze, Extract and Review these critical data and information shared in a live real-time dashboard /report view.
Information and communication are vital to manufacturing success. Time destroys evidence and manufacturing sites cannot afford complacency. Information and communications gathered from the connected process must be used in real-time, accurate, objective reporting results with autonomous escalations.
- Cloud Solutions
With the introduction of Manufacturing 4.0 come many concepts and tools,like IIoT, the “Industrial Internet of Things”, that can radically improve the seamless connectivity and instrumentation of machines and processes on the manufacturing floor. IIoT has become a remarkably simple and inexpensive method to provide live real-time information and equipment data.
The applications of IIoT are used to identify and enhance Safety, Quality, and OA, or even reduce downtime by predicting and preventing downtime events. With all this capability comes significant amounts of data and information. This data and information can be a game-changer if utilized effectively. The ability to capture extremely large amounts of data brings new challenges to the execution and utilization of IoT and Manufacturing 4.0. We then need to answer questions such as:
- What do I do with this data?
- Where do I securely save this data?
- How do I retrieve data?
- Where is the data?
- Is the data computed?
Over the years, I have found that many manufacturing sites have become extremely effective at capturing data. The amount of data and information captured is remarkably large in many instances. However, over and over it seems as if the common failure mode is due to manufacturing sites not utilizing the data, or not having repeatable methods to extract and analyze the data.
It's remarkable how many Problem Solving Events I have personally been a team member of over the years that are ultimately solved and eliminated by simply drilling deep into the data. More times than not, after drilling into the data, the root cause or recreation steps and criteria are identified by digging into and analyzing the data. As embarrassing as it may personally sound, in many instances in the past, the data was available to potentially prevent or eliminate root causes of waste and or quality issues. I suspect many sites are in similar situations where they do not have timely access to data and or not sure how to retrieve, compute, and or analyze the data they have.
Some more good news is that today's era of Cloud LES Solutions like Leading2Lean have revolutionized the amount and type of data that is available to teams and users. This enables teams to extract and analyze vast quantities of information and data immediately, enable additional functionality, such as mobile and overall connectedness, that can be accessed anywhere instantly.
This is truly good news in the rapidly changing landscape of modern manufacturing. Make sure you are part of this revolution! If you're not already using Leading2Lean to leverage all you can with Manufacturing 4.0, the time to act is now. Call us today! We love to help you put it all together!
Or check out this guide: You're Here, Industry 4.0 Is There
Revisions
Original version: 16 December 2020
Written by: Jon Richardson
Reviewed by: Daan Assen
Please read our editorial process for more information
Related Posts
Subscribe to Our Blog
We won't spam you, we promise. Only informative stuff about manufacturing, that's all.