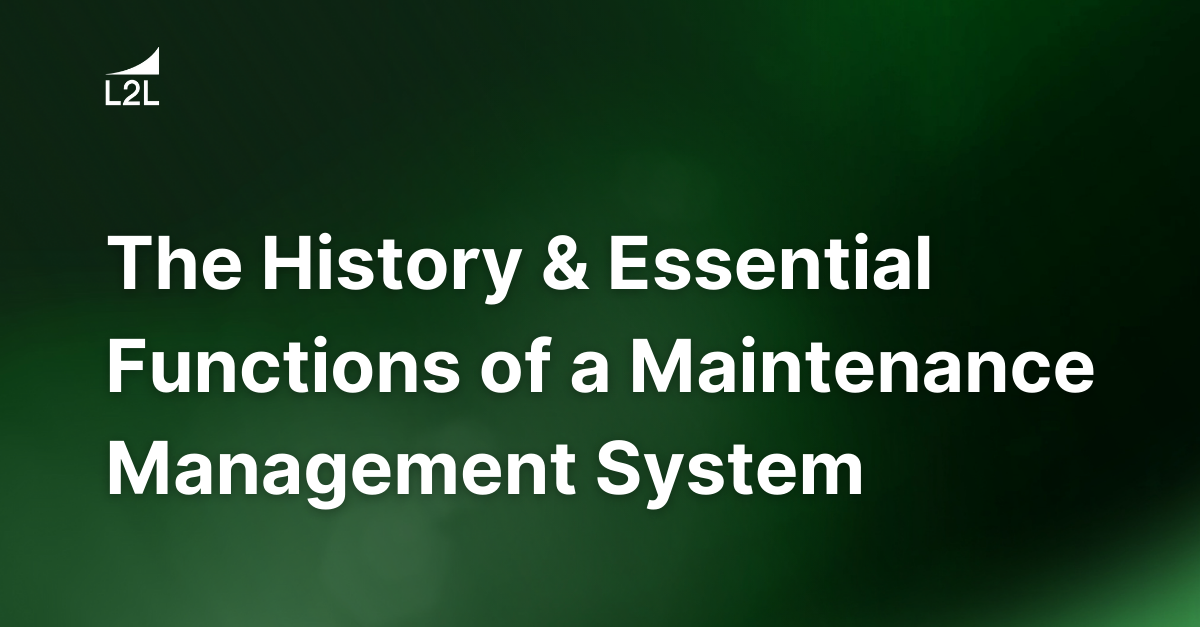
A Brief History of Maintenance Management Systems
Back when the computerized maintenance management system was first conceptualized, that computer could not run a single app you now have on your phone. But even with these early limitations, software engineers of the day had hopes of developing a computerized maintenance management system that would simplify the maintenance activities within manufacturing.
Unfortunately, it has taken some 40-50 years of technology and software evolution to arrive at a point in time when these concepts could be fully put to work on the factory floor.
- Early versions were nothing more than a vehicle to input static data with little or no chance of that data ever being pulled for analysis.
- Later versions allowed the user to enter data in multiple fields allowing for greater access to this data. But this data was still only available through Superusers that were specifically trained to retrieve the information through detailed query and specialized screens.
- Finally, newer versions of these traditional CMMS software programs allowed for control and categorization of information even down to the job, Work Order and scheduled PM events, but they still lack the user experience that makes it easy for everyday mechanics and technicians to use comfortably.
Essential Functions of a Maintenance Management System
As the manufacturing sector becomes more and more globalized, the need for a robust maintenance management system has never been more critical. At the core, a maintenance management system is a strategic process that allows you to manage the reliability of a manufacturing facility. This includes the following critical elements:
- Skilled Labor Management
- Asset Management
- Predictive and Preventative Maintenance
- Spare Part Management
- Abnormality Management
The Goal of a Maintenance Management System
A company's ability to manage these key elements through modern software systems has revolutionized plants' ability to operate more efficiently than ever with fewer resources.
The digital or computerized maintenance management system (CMMS) is not a new solution.
It has been around for decades, but often small or growing companies fail to implement a system early in their growth journey. This leads them to over-invest in capital and labor to meet their growth needs. Those that are able to implement even traditional CMMS systems have seen huge benefits in their ability to plan maintenance more effectively and manage critical information about assets and spares.
However, in today’s environment, traditional maintenance management systems have many limitations that prevent a plant from operating at the next level.
Shortcomings of the Computerized Maintenance Management System
As computerized maintenance management system technology progressed, gaps still existed in what software companies were (and in some cases still are) delivering to users. These still-existing gaps are easy to identify when assessing maintenance organizations that use older, outdated maintenance management systems.
- Indicators that these gaps are present include:
- Excessive manual input of data
- Minimal/limited available seat licenses
- Excessive cost to upgrade to the latest version
- Small percentage (if any) reactive maintenance captured
- Confusion on how the data is used
- Difficult and clunky user interface
Historically, traditional CMMS software has only been available to large corporations with the budgets to handle the high cost of purchase, upgrades, and resources needed to support the implementation.
In some cases, these systems are add-ons to existing accounting platforms that are not designed primarily with the end-user in mind (the maintenance technician and/or manager). These add-ons can cost millions of dollars and take years to implement, only to end up not delivering on features and user experiences as advertised.
The upgrade process is another source of frustration brought on by traditional systems. Due to an unwillingness to budget for upgrades and a real fear that new upgrades will cause disruption to the process, these upgrades are postponed for years, causing the company to lag in user skill and understanding of modern features.
Our COO at L2L said it best when he said:
“In my experience, 90% of factories are operating with systems and methods that are outdated. Antiquated, actually. These are systems that do not support continuous improvement and are in fact wasteful and don’t add value.”
So, considering the fact that these traditional systems are not being upgraded in a timely manner and are sub-standard in features set and user experience, homegrown and black market systems begin to emerge that help technicians manage the real day-to-day operations of the maintenance department.
- Key indicators that these systems are finding their way in operations are:
- The hoarding of spare parts in tool boxes
- Multiple spreadsheets with old data
- Grease boards with outdated information
- Stacks of printed PM’s and Work Orders
- Technicians planning activities on the fly
5 Essential Functions of a Next Generation Maintenance Management System
In today’s digital and increasingly remote-work environment, it’s more important than ever to ensure you’re utilizing the tools that are built to solve the problems of today, not just the problems of more than a decade ago.
There are 5 essential functions of a next generation Maintenance Management System:
- It should provide real-time visibility
- It should bring value to the end user
- It should make your life easier (not harder)
- It should provide a simple tie-in with Production
- It should foster greater employee engagement
A Maintenance Management System Should Provide Real-Time Visibility
One of the biggest limitations of traditional maintenance management systems is a lack of real-time visibility.
We live in a smartphone world. The power to do more than we ever imagined is in the palm of our hands. I am always amazed at how archaically many manufacturing companies still operate in this highly technical and competitive world we live in.
How can a plant thrive if it's tracking their operations on whiteboards and spreadsheets?
Imagine watching a game with no scoreboard. How would you know if you are winning or losing? Real-time visibility is as critical to manufacturing as it is to any sport or game. By implementing a system that is real-time, companies are seeing significant improvements in:
- Employee Accountability
- Decision Making at Lower Levels
- Reduced Downtime
- Engaged and Empowered Workforce
- Increased Output and Profits
A key reason for these successes is access to tools and systems that help people do their job more efficiently vs. creating a burden on them.
Traditional CMMS software is more like a "black hole", as often the preventative, predictive, and reactive data entered by the technicians is all entered after events have actually occurred. This dilutes accuracy.
Furthermore, they often aren't able to recall the information later for troubleshooting or training purposes. This doesn't engage the users: it actually pushes them away. As equipment and technicians become more and more connected through API integrations, the days of printing paper work orders are rapidly disappearing.
A Maintenance Management System Should Bring Value To The End User
"I'm not sure our people are ready for this."
I hear this often when working with new customers (from managers, in particular). They underestimate their workforce's eagerness to learn new solutions and be more engaged in the business.
A maintenance management system should be a tool, not a task.
Time and time again I see companies—usually corporate—forcing maintenance management systems onto the plants without realizing the massive shortcomings of the systems they're trying to implement.
Traditional maintenance management systems often require highly skilled administrators to access data and are very cumbersome to input and access at the shop floor level. Workers tend to resist technology if it doesn't bring immediate value to them.
On the other hand, if you give an employee a tool and it makes their job easier, you usually cannot pry it out of their hands. That's the sign of real value; they see it as their own and not something that they are forced to use.
I am continually amazed to see how quickly users of all levels of tech-savviness can learn and leverage maintenance management systems to improve their jobs and deliver business results at all levels. When you make it as easy to use as any other social media app or site, it's no wonder the adoption rate is so rapid.
A Maintenance Management System Should Make Your Life Easier (Not Harder)
I worked as a maintenance manager for five years in a major consumer electronics company and was faced with the challenges of a traditional CMMS. It took me way too much time to get data out of the system and I often had to rely on others to do so.
I always had a note taped to my desk with all of the special system codes. Had I ever lost that sheet, pulling reports or querying data would have been nearly impossible. After implementing L2L, I felt like I owned the data. I could pull reliability data in seconds compared to hours or even days. Since I was looking at the data so much more, the quality and quantity also increased exponentially.
The old adage is true: What gets measured gets worked on, and I felt like I finally had a system I could use and leverage to manage the maintenance team more effectively for not only their benefit but for the business too.
- Other benefits of a cutting-edge maintenance management system include:
- Reduction in administrative time
- Increased Productivity/Time for Hourly and Salary
- Easier Budget Planning Tools
- Simple Reporting and Trending
- Real Time Cost Tracking
It Should Provide A Simple Tie-in With Production
The real coupe with a next gen maintenance management system is the tie-in with production data through IoT technology.
Using PLCs and wireless connected sensors, you can easily collect data around:
- Downtime data
- Production numbers
- Scrap data
- Run rates
These are combined to create a single source of data, useful for calculating machine OEE and other critical metrics. This also eliminates tension between maintenance and production personnel. Instead of having two separate sets of data, both teams feed data into the same software to create one system that acts as a single source of truth.
It Should Foster Greater Employee Engagement
For decades, organizations have striven to unlock the true potential of engagement from employees. A next-gen computerized maintenance management system combines mobility, ease of UI, and real-time visibility in order provide a platform where employees can quickly:
- Log abnormalities
- Suggest improvements
- Record improvement processes in the constraint areas of the facility
As you see, computerized maintenance management software technology has come a long way since its inception over four decades ago. Advancements in hardware and coding techniques have given the software industry greater tools to create a seamless user experience.
But the one constant through all of it has been that the most powerful machine on the factory floor is still the human brain and its ability to problem solve.
As we provide plant floor workers a tool to have the right information at the right times, then we can count on their abilities to analyze and solve problems that impact the bottom line.
Hopefully, you can see how the maintenance management system in your facility can be more than just a cost center. Cloud-based tools and systems like L2L’s Next-Gen CMMS are changing the way maintenance is done all over the world, revolutionizing plant floors, and ultimately adding value to the bottom line more than ever before.
Interested in a maintenance management system that does it all? Request a demo with L2L to see how we can help you achieve operational excellence.
Revisions
Original version: 26 July 2019
Written by: Mark Hungerford
Reviewed by: Daan Assen
Please read our editorial process for more information
Related Posts
Subscribe to Our Blog
We won't spam you, we promise. Only informative stuff about manufacturing, that's all.