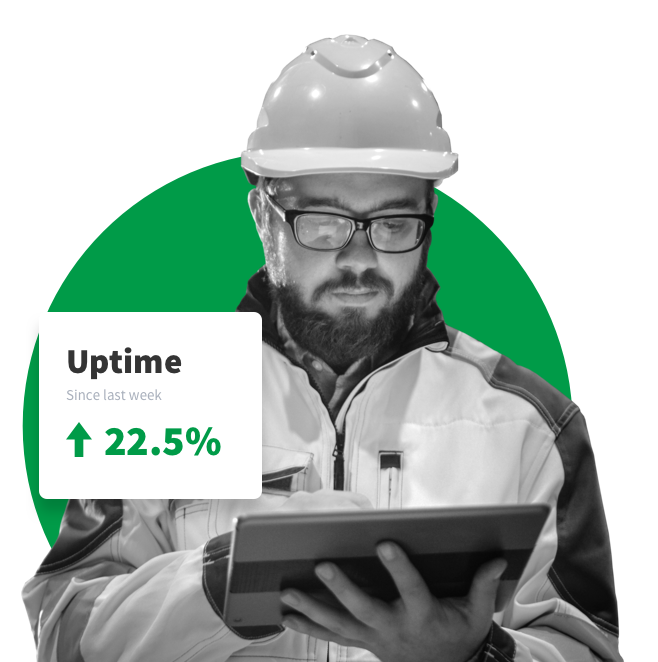
Free Guide
What Is CMMS Software?
Uses, Prices, & Benefits
All manufacturing plants need CMMS software. Machines break. CMMS software helps managers both prevent breakdowns from happening and respond to them when they do happen. It does this by creating a central hub for all data about machines on the manufacturing plant floor.
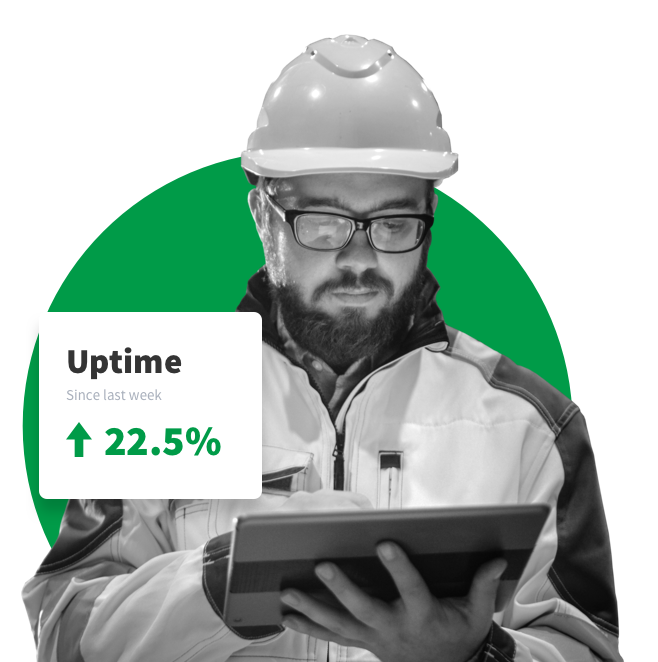
Ready to Get Started? Request a Free Consultation.
A computerized maintenance management system, or CMMS, is a digital database used to manage operational assets in a manufacturing plant. CMMS software mostly relates to a factory's production equipment and the maintenance tasks required to care for that equipment. It's designed to prevent machines from breaking down and help plant personnel address breakdowns with speed and efficiency.
CMMS software tracks preventative maintenance, which is like getting the oil in your car changed; it's scheduled based on intervals of time.
The purpose of CMMS software is to reduce machine downtime. When a machine breaks down, it affects production, which ultimately affects a manufacturing plant's bottom line. CMMS maintenance software provides maintenance teams with the information they need to plan effectively and make better decisions on the plant floor.
If you own just one car, it’s easy enough to keep a mental maintenance schedule. You know when to get your oil changed, your brake fluid checked, or your tires swapped out. If you have more than one car, it’s more difficult to keep track of each preventive maintenance task. You might keep the information in a spreadsheet.
But what if you have one hundred cars? You’re going to need more than a spreadsheet.
That same idea applies to asset maintenance in a manufacturing plant. Keeping data in a spreadsheet (or on paper) isn’t an effective way of keeping machines up and running.
CMMS software creates a central hub for all data — a united maintenance operation. This allows managers to plan effectively and make better decisions on the plant floor.
Most traditional CMMS software is designed to perform a baseline set of operations that includes:
-
Controlling the company’s list of maintainable assets through an asset register
-
Controlling accounting of assets, purchase price, depreciation rates, etc.
-
Controlling preventative maintenance procedures and documentation
-
Controlling the issue and documentation of planned and unplanned maintenance activity
-
Organizing the maintenance personnel database, including work orders and shift schedules
-
Scheduling calibration for gauges and instruments
-
Controlling portable appliance testing.
-
Assisting in maintenance project management
-
Providing maintenance budgeting and costing statistics
-
Controlling maintenance inventory
-
Processing condition monitoring inputs
-
Providing analysis tools for maintenance performance
Without a computerized system, it’s difficult to visualize all of these intricately connected operations. That’s why manufacturing businesses with manual systems generally don’t have the data they need for optimal facility management, asset tracking, work request supervision, and more.
CMMS software helps a plant with equipment maintenance, spare parts, regulatory compliance, and costs related to day-to-day maintenance activity. It can also ensure technicians complete each work order in a timely manner.
Other CMMS software benefits should include:
Minimizing Machine Downtime
CMMS software provides a way to manage preventive maintenance and keep work orders organized for optimum efficiency. A more efficient asset management team has a direct impact on minimizing machine downtime, which helps improve productivity.
Improving Production Quality
Failing equipment inevitably leads to product quality issues, costing you time and money to resolve. Costly product rework may be required after a dip in production quality, impacting overall output.
Simplifying Spare Parts Management
Effective spare parts management helps solve problems before they become problems at all. Without a solid approach to spare parts, component failure could leave you without an immediate solution, leading to extensive productivity loss and effects felt across the supply chain.
Increasing Worker Productivity
Good CMMS software should make asset breakdown history available to everyone, from the maintenance manager to the technician — an essential step in the efficient resolution of equipment issues. Having the right information available to technicians when they need it (and in a digital format) is critical to achieving optimal productivity.
Supporting Spare Parts and Inventory Management
Having spare parts available when a technician needs them can be the difference between a quick return to service and seemingly infinite downtime. Even better, knowing what spare parts are needed during an effective preventative maintenance process will reduce the need for large quantities of spares on hand.
Improving Compliance
Auditors look at maintenance activities, work orders, training compliance, and adherence to standards. A CMMS system should provide a digital record of these activities and allow the auditor to verify compliance much more easily than pouring through file cabinets full of paper records.
Providing Insight into Facility Management
A CMMS should also provide insight into facility asset reliability, maintenance, and repair. Seeing this history at a glance improves processes for spares and resource costs, work order status, resource utilization, and KPIs such as MTTR and MTBF.
Boosting ROI
With maintenance management system software, plant managers and decision-makers can expect a consistent and measurable ROI in six to nine months. With traditional CMMS software, it may take a couple of years. This is in part because of how long traditional systems take to deploy.
Pricing for CMMS will range depending on the target market:
-
Small shops: If you’re just looking to move from paper or Excel to a digital system, basic capabilities might be sufficient. These CMMS systems typically start around $30 - $80 per user, per month, and they often require a setup charge of $750 - $2,500.
-
Medium to large enterprises: Bigger operations should look at more robust software, generally priced based on the number of users across the enterprise. The cost can range from tens of thousands to millions per year.
Although this per-user approach is a somewhat standard pricing model, there’s one major issue: It fails to engage the entire maintenance team and the workforce across the entire plant.
When a CMMS’s pricing is based on a per-user model, manufacturers often try to keep the number of users at a minimum to reduce costs. To achieve the quickest ROI and the greatest success, you want more than just a few people accessing the system.
These are the top three signs that you may need CMMS software:
Your equipment breaks down regularly.
If you use outdated asset management methods, chances are that most of your maintenance work will be reactive as opposed to proactive.
If your maintenance team only fixes things after they’ve broken, the result is higher machine downtime and lower overall production. Introducing CMMS software can significantly improve the maintenance process. Just ask our client Lakeview Farms. (Spoiler alert: They experienced a 34% reduction in downtime.)
Repairs can't be completed on time.
When spare parts and inventory management are all over the place, your whole plant suffers. Maintenance teams must wait for parts to arrive, which means the downtime lasts longer than is necessary. You might even lose a greater chunk of your budget when ordering the parts you need in an emergency.
CMMS software can track spare parts and triggers a reorder alert when inventory is low. This also minimizes the need for manual inventory checking.
There is no visibility.
If managers struggle to communicate effectively with their teams, processes flounder, and work order stacks keep growing. Luckily, CMMS empowers plants to monitor progress on a task and get the whole team on the same page.
Here’s the thing: Traditional CMMS software is a task, not a tool.
Even though a digital system is better than manual methods of tracking maintenance activities, the unfortunate truth is that many CMMS software offerings don't add value for people on the plant floor. Sometimes, CMMS software can even be downright wasteful.
Here are just a few limitations of traditional maintenance management software:
Lack of User Friendliness
Technicians sometimes wait until the end of the day or week to enter data that’s crucial to maintenance and facility management. Worse yet, we find that it’s common for only 25% of this vital data to get recorded properly.
Why do teams wait so long and only capture a quarter of maintenance data? Simple: The system is a pain for them to use, and the data is difficult to access after it’s been inputted.
Lack of Agility
Traditional CMMS software tends to be slow and inefficient.
Even deploying CMMS is a laborious process. This is enough to deter some plants from trying to implement new software because they know what a hassle integrating CMMS with manufacturing equipment can be.
Additionally, CMMS software often comes with a limited number of licenses. That means not everyone has access to the system, and only some team maintenance members can input data, which creates a bottleneck.
Lack of Adaptability
Perhaps the biggest issue with traditional CMMS software is that it doesn't provide real-time data. Often, the data seen in a traditional CMMS solution is yesterday's news. Without up-to-date information, plant workers are left relying on guesswork and equally troublesome solutions to get their jobs done.
That's why real-time data is critical to success on the manufacturing plant floor: It's the best way to truly engage workers and streamline maintenance request processes. Plus, it may be the only way to see what’s really going on across your plant — which is the key to making decisions that support continuous improvement.
In the new Industry 4.0 environment we live and work in, old-school software systems just aren’t cutting it. We need to rethink whether the traditional CMMS definition covers what today’s connected environment really needs.
A modern CMMS platform should correct the issues posed by traditional CMMS by offering:
-
Quick deployment. How does one week sound?
-
IoT readiness. A maintenance system that is already part of digital manufacturing.
-
ROI (within a reasonable time frame). No one moves into your plant to take up residence.
-
Predictive maintenance. You run the plant. The plant doesn't run you.
-
Real-time data. Empower your associates with real-time, transparent data: no more finger-pointing. They know what to do. You just have to give them the tools.
-
Total accountability. No more assigning blame. Problems are clear. Time to go fix them.
-
An end to silos. Unite all departments behind a common cause: production and being productive.
-
System integration. The modern maintenance care solution should tie your existing systems together (ERP, MES, QMS, etc.)
Due to new mobile technology and new cloud-based applications like L2L Dispatch, mechanics, engineers, quality technicians, and others have the ability to input information into a real-time system. In fact, they can do it right from the shop floor by using mobile and wearable devices, keeping them connected to machines, how-to guides, vital metrics, and one another. This new advantage allows for a more free flow of accurate data as the work is performed.
Here’s what that looks like:
-
Machine history data is instantly available.
-
Spare parts usage is documented as consumed.
-
Costs are associated directly with the reactive or proactive event.
-
Employees feel motivated because they can see in real time that their input is making a difference.
We have a saying here at L2L that sums up the approach to making work easy: “Stop putting your processes through the Complexicator and start putting them through the Simplifier.” If you do this, you’ll be amazed at the quality and content of work that comes out the other end.
See how easy it will be to take your maintenance success to the next level with our best CMMS software. Book your personalized demo today!
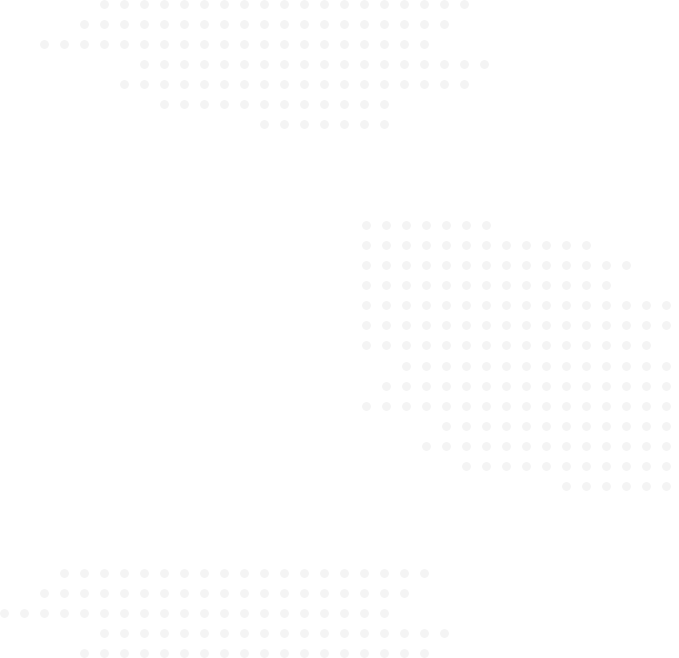
Empower Your Connected Workforce
"L2L is a valuable tool. Having everything at our fingertips creates continuity between maintenance, operators, and leadership."
.png)